Introduction to Solid-State Batteries and Isostatic Pressing
Commercialization of Solid-State Batteries
Battery researchers at Oak Ridge National Laboratory (ORNL) emphasize the critical role of isostatic pressing technology in advancing the commercialization of next-generation batteries. This technology, which leverages the principles of Pascal's law to apply uniform pressure through liquids and gases, ensures the production of highly consistent battery components. The method's ability to facilitate smooth ion movement and adapt to various battery compositions at different temperatures and pressures makes it a cornerstone for the development of solid-state batteries.
Solid-state batteries, known for their potential to charge faster, last longer, and operate more safely than traditional lithium-ion batteries, are poised to revolutionize industries such as electric vehicles and aviation. The versatility of isostatic pressing, which can be applied from room temperature to extreme heat, broadens its applicability across a spectrum of materials, including polymers and oxides. This flexibility not only enhances the performance of solid-state batteries but also paves the way for their integration into high-demand sectors.
Several leading automotive companies have already outlined plans to incorporate solid-state batteries into their electric vehicle fleets, recognizing the transformative impact they could have on range, safety, and charging times. Isostatic pressing technology stands as a pivotal enabler in this transition, offering the means to assemble intricate battery layers without the impracticalities often associated with conventional methods. As the push towards commercialization intensifies, the synergy between solid-state batteries and isostatic pressing technology is set to redefine the future of energy storage and application.
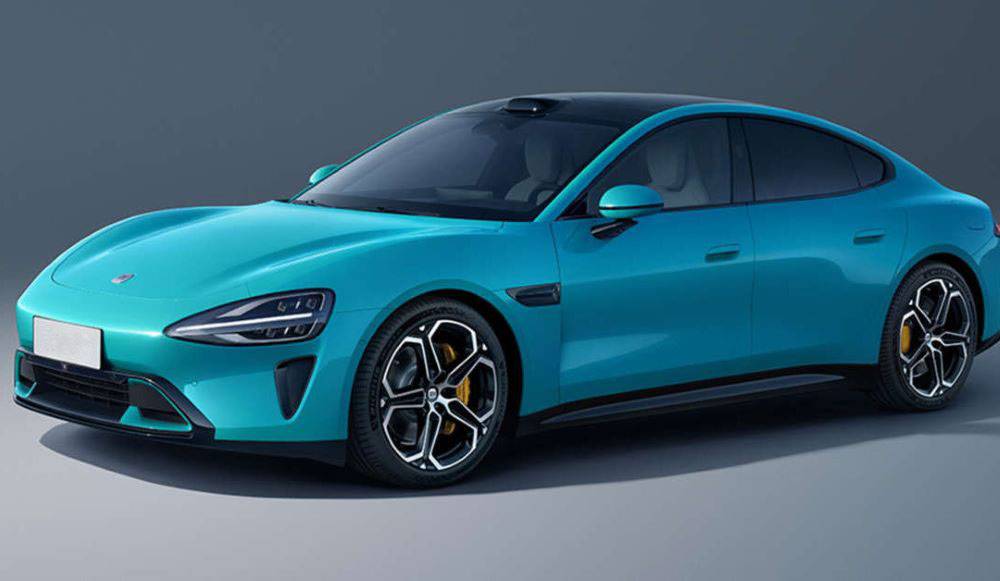
Benefits of Solid-State Batteries
Solid-state batteries offer a significant leap forward in battery technology, promising to revolutionize the energy storage landscape. Unlike traditional lithium-ion batteries, solid-state batteries utilize a solid electrolyte instead of a liquid one, which not only enhances their safety profile but also significantly improves their performance metrics.
One of the most compelling advantages of solid-state batteries is their ability to charge at unprecedented speeds. This rapid charging capability is particularly beneficial for applications where time is of the essence, such as electric vehicles (EVs). With solid-state batteries, drivers could potentially recharge their vehicles in a fraction of the time currently required, alleviating range anxiety and making EVs a more practical and appealing option for daily use.
In addition to faster charging times, solid-state batteries boast extended lifespans. They are designed to withstand more charge-discharge cycles without degradation, which translates to longer battery life and reduced maintenance costs. This durability is especially critical for industries that rely heavily on battery-powered equipment, such as aerospace and telecommunications.
Safety is another cornerstone of solid-state batteries' appeal. The elimination of flammable liquid electrolytes significantly reduces the risk of thermal runaway, a phenomenon that can lead to catastrophic battery failures in lithium-ion batteries. This enhanced safety feature makes solid-state batteries an ideal choice for applications where reliability and safety are paramount, including medical devices and aerospace systems.
Furthermore, the versatility of solid-state batteries extends beyond their performance and safety benefits. Their compact design and high energy density make them suitable for a wide array of applications, from portable electronics to grid-scale energy storage. This adaptability positions solid-state batteries as a transformative technology that could reshape the future of energy storage and distribution.
In summary, solid-state batteries stand out for their ability to charge faster, last longer, and operate safer than their lithium-ion counterparts. These attributes make them a highly attractive option for a diverse range of industries, promising to drive innovation and efficiency across the board.
How Isostatic Pressing Technology Works
Principle of Isostatic Pressing
Isostatic pressing operates under the fundamental principle of Pascal's law, which asserts that pressure applied to a confined fluid is transmitted uniformly in all directions. This method involves the use of liquids or gases to exert consistent and uniform pressure on battery components, leading to the creation of highly uniform materials. The process begins with the placement of a powder, typically a battery component, within a flexible mold, such as polyurethane. This mold is then sealed and subjected to a uniform hydrostatic pressure, ensuring that the pressure is evenly distributed across all surfaces of the powder.
There are two primary techniques employed in isostatic pressing: the wet-bag technique and the dry-bag technique. In the wet-bag technique, the flexible bag containing the powder is submerged into a pressure vessel filled with a pressurizing fluid, such as soluble oil. This method allows for the direct application of pressure to the bag, ensuring that the powder within is uniformly compacted. On the other hand, the dry-bag technique involves fixing the flexible bag within the pressure vessel, allowing for the loading of powder without the need for the bag to leave the vessel. This technique offers greater convenience and efficiency, especially in large-scale manufacturing processes.
The isostatic pressing process is particularly advantageous for battery manufacturing due to its ability to achieve high densities and uniform shapes under high pressure. This method is widely utilized in the formation of various materials, including high-temperature refractories, ceramics, cemented carbides, lanthanon permanent magnets, carbon materials, and rare metal powders. By applying equal pressure to each surface of the product, isostatic pressing ensures that the resulting materials are not only uniform but also optimized for performance in solid-state batteries.
Advantages of Isostatic Pressing
Isostatic pressing offers several key advantages that make it a superior method for compacting battery materials. The process ensures uniform compaction by applying equal pressure in all directions, eliminating the need for lubricants and thereby achieving high and consistent density. This uniformity is crucial for battery performance, as it facilitates smooth ion movement, which is essential for efficient charge and discharge cycles.
Moreover, isostatic pressing is highly versatile, applicable to a wide array of battery compositions and operating conditions. It can be conducted at various temperatures and pressures, accommodating materials that are traditionally difficult to compact, such as superalloys, titanium, tool steels, stainless steel, and beryllium. This flexibility not only enhances material utilization but also broadens the scope of battery designs that can be effectively manufactured.
The process also alleviates many of the geometric constraints associated with unidirectional compaction in rigid dies. This freedom in design allows for the creation of complex battery shapes and structures, which can be tailored to meet specific performance requirements in applications ranging from pharmaceuticals to nuclear fuel.
In summary, isostatic pressing stands out for its ability to produce high-quality, uniform battery materials that are adaptable to a variety of conditions and material types, making it a pivotal technology in the advancement of solid-state batteries.
Versatility and Future Applications
Versatility in Materials
Isostatic pressing technology stands out for its remarkable adaptability across a broad spectrum of materials. This process can operate effectively from room temperature all the way up to thousands of degrees Fahrenheit, making it a versatile tool in the manufacturing of solid-state batteries. The ability to handle such a wide temperature range allows for the utilization of diverse materials, including polymers and oxides, which are critical components in battery construction.
One of the key advantages of isostatic pressing is its compatibility with various material types. For instance, polymers, known for their flexibility and insulating properties, can be processed to form robust battery casings. On the other hand, oxides, which are essential for the battery's cathode and anode, can be uniformly pressed to ensure optimal performance and longevity. This flexibility in material usage not only broadens the range of potential applications but also enhances the overall efficiency and reliability of solid-state batteries.
Moreover, the ability to press materials at different temperatures and pressures ensures that each component of the battery is tailored to its specific function. This precision engineering is crucial for the development of next-generation batteries that promise faster charging times, longer lifespans, and enhanced safety features. As a result, isostatic pressing emerges as a pivotal technology in the quest for more advanced and versatile solid-state batteries, paving the way for their widespread adoption in various industries.
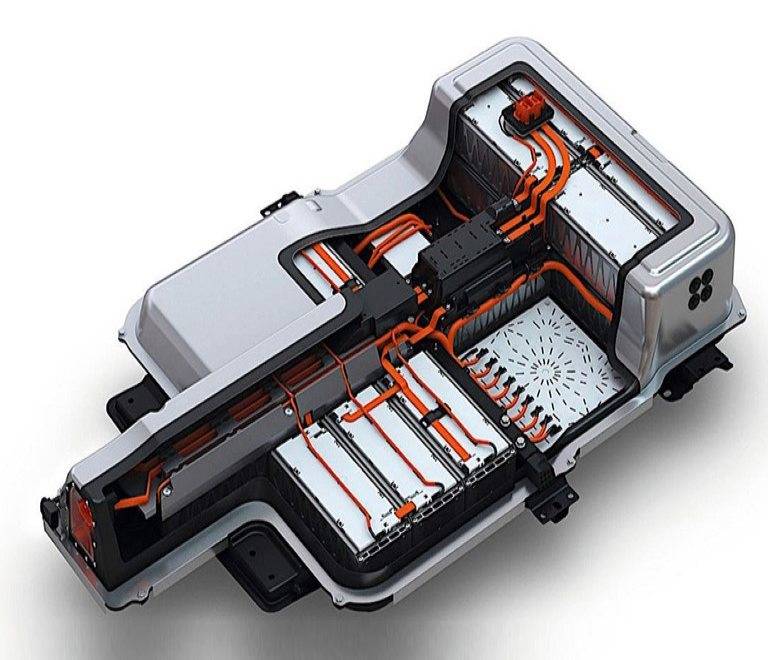
Potential for Automotive and Aviation Applications
The integration of solid-state batteries into electric vehicles (EVs) is a strategic move by several leading automotive companies, driven by the need for enhanced performance and safety. Isostatic pressing technology stands as a pivotal enabler in this transition, offering a streamlined method for assembling battery layers without the inherent complexities and inefficiencies of traditional processes.
In the automotive sector, the adoption of solid-state batteries promises to revolutionize EV capabilities, offering faster charging times, extended lifespans, and superior safety compared to conventional lithium-ion batteries. Isostatic pressing's ability to apply uniform pressure across battery components ensures the production of highly consistent and reliable battery layers, which are critical for achieving these performance benchmarks.
Moreover, the aviation industry is also eyeing solid-state batteries for its fleet, recognizing the potential for significant weight reduction and increased energy density. Isostatic pressing's adaptability to various materials and temperature ranges makes it a versatile solution for producing batteries that meet the stringent requirements of aviation applications. This technology not only simplifies the manufacturing process but also paves the way for more innovative and efficient energy storage solutions in both automotive and aviation sectors.
CONTACT US FOR A FREE CONSULTATION
KINTEK LAB SOLUTION's products and services have been recognized by customers around the world. Our staff will be happy to assist with any inquiry you might have. Contact us for a free consultation and talk to a product specialist to find the most suitable solution for your application needs!