Introduction to Isostatic Pressing Technology
Basic Principles of Isostatic Pressing
Isostatic pressing technology fundamentally revolves around the placement of sample powder within a high-pressure container, where it is uniformly pressurized using the incompressible nature of a liquid medium. This process leverages the properties of fluids to distribute pressure equally across all surfaces of the sample, ensuring a consistent and dense formation.
The core of this technology lies in the use of a flexible mold, typically made of materials like polyurethane, which encapsulates the powder. This mold is then subjected to hydrostatic pressure, often facilitated by a pressurizing fluid such as soluble oil. This uniform application of pressure is key to forming a dense green body from the powder, a crucial step in the production of various materials, including high-temperature refractories, ceramics, and cemented carbides.
There are two primary techniques within the broader category of isostatic pressing: the wet-bag technique and the dry-bag technique. In the wet-bag technique, the flexible bag containing the powder is submerged into the pressure vessel filled with the pressurizing fluid. Conversely, the dry-bag technique involves fixing the flexible bag within the pressure vessel, allowing for the powder to be loaded without the need for the bag to leave the vessel. Both methods ensure that the powder is subjected to equal pressure from all directions, leading to the desired dense and uniform product.
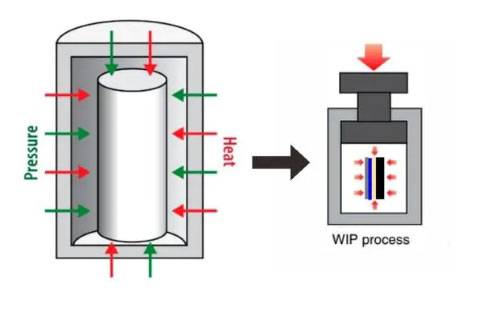
Types of Isostatic Pressing
Isostatic pressing is fundamentally categorized into two primary methods: cold isostatic pressing (CIP) and hot isostatic pressing (HIP).
Cold Isostatic Pressing (CIP): This technique involves the application of pressure to a powder at ambient temperatures. The process begins by placing the powder in a flexible container, which is then submerged in a liquid medium. A high-pressure pump is used to apply uniform pressure to the liquid, which in turn compresses the powder from all directions. This method is particularly advantageous for forming dense green bodies from powders, which can then be further processed or sintered.
Hot Isostatic Pressing (HIP): In contrast, HIP involves both high temperature and high pressure. The powder is subjected to isostatic molding and sintering simultaneously under elevated temperatures and pressures. This dual approach not only compacts the powder but also facilitates the sintering process, leading to materials with superior mechanical and physical properties. HIP is often used in the production of high-performance ceramics and advanced materials where the combination of temperature and pressure is crucial for achieving the desired microstructure and performance.
Both methods leverage the principles of fluid mechanics and the incompressible nature of the liquid medium to ensure uniform pressure distribution across the sample, thereby enhancing the density and structural integrity of the final product.
Applications and Advantages of Isostatic Pressing
Advantages of Cold Isostatic Pressing
Cold isostatic pressing (CIP) technology offers a multitude of benefits that significantly enhance product performance, quality, and economic efficiency. One of the standout features of CIP is its ability to impart high green strength to molded materials. This green strength allows for faster processing times, as the materials can be sintered or machined more rapidly compared to those produced by other methods. The high green strength also translates to a higher turnover rate, making CIP a preferred choice in industries where time is of the essence.
Another key advantage of CIP is its capability to produce materials with uniform density. This uniformity ensures consistent shrinkage during subsequent processes like sintering, leading to more predictable and reliable final products. The even distribution of pressure throughout the material, facilitated by the incompressible liquid medium, is the primary reason behind this uniform density. This characteristic is particularly beneficial in industries such as powder metallurgy, ceramics, and refractory materials, where dimensional accuracy and material integrity are critical.
CIP also contributes to uniform strength across the product, offering greater homogeneity and precision in finished product dimensions. This uniformity in strength allows for greater flexibility in the shape and size of the finished product, enabling the production of longer aspect ratios and intricate designs that would be challenging to achieve with uniaxial pressing. Furthermore, CIP improves the compaction of powder, resulting in enhanced densification and better overall material properties.
The versatility of CIP extends to its ability to process a wide range of materials with different characteristics and shapes, making it a highly adaptable technology. Additionally, CIP reduces cycle times and improves productivity, contributing to economic benefits and making it a cost-effective solution for various industrial applications.
Promising Method for High-Performance Ceramics
Cold isostatic pressing (CIP) has emerged as a pivotal technique in the production of high-performance ceramics. This method involves the use of high-pressure liquid media to uniformly pressurize ceramic powder, forming a dense green body. The process begins by encapsulating the powder in a flexible container, which is then placed within a pressurized chamber. As the pressure is applied, the liquid medium ensures that the force is evenly distributed across the entire surface of the powder, leading to a uniform compression.
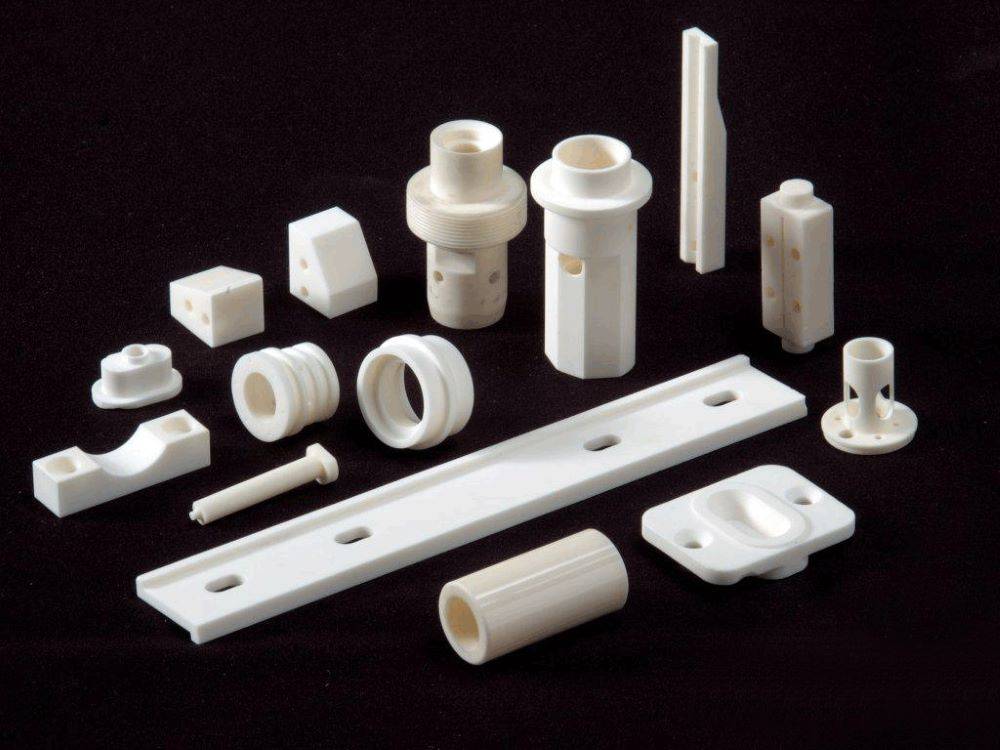
Once the powder is compressed into a rough blank, it undergoes further processing steps such as machining and sintering. These steps refine the blank into a final product with precise dimensions and enhanced mechanical properties. The use of CIP in this manner offers several advantages:
- Efficiency in Material Use: By reducing the need for additional binders and additives, CIP minimizes material waste and lowers production costs.
- Enhanced Product Quality: The uniform compression ensures that the final ceramic product has consistent density and strength, improving overall performance.
- Cost-Effectiveness: The streamlined process reduces the overall processing volume, leading to significant cost savings in both material and energy consumption.
The integration of CIP into the ceramic manufacturing process not only optimizes the production cycle but also paves the way for the development of advanced ceramic materials with superior properties.
Isostatic Pressing in Solid-State Battery Production
Application in Solid Electrolyte Production
Researchers leverage isostatic pressing technology to produce solid electrolytes for solid-state lithium batteries, a critical component in the quest for safer and more efficient energy storage solutions. The process begins with the meticulous selection and mixing of specific materials, which are then transformed into a homogeneous slurry. This slurry is subjected to isostatic pressing, a method that ensures uniform pressure distribution across the material, leading to the formation of ultra-thin, flexible composite solid electrolyte membranes.
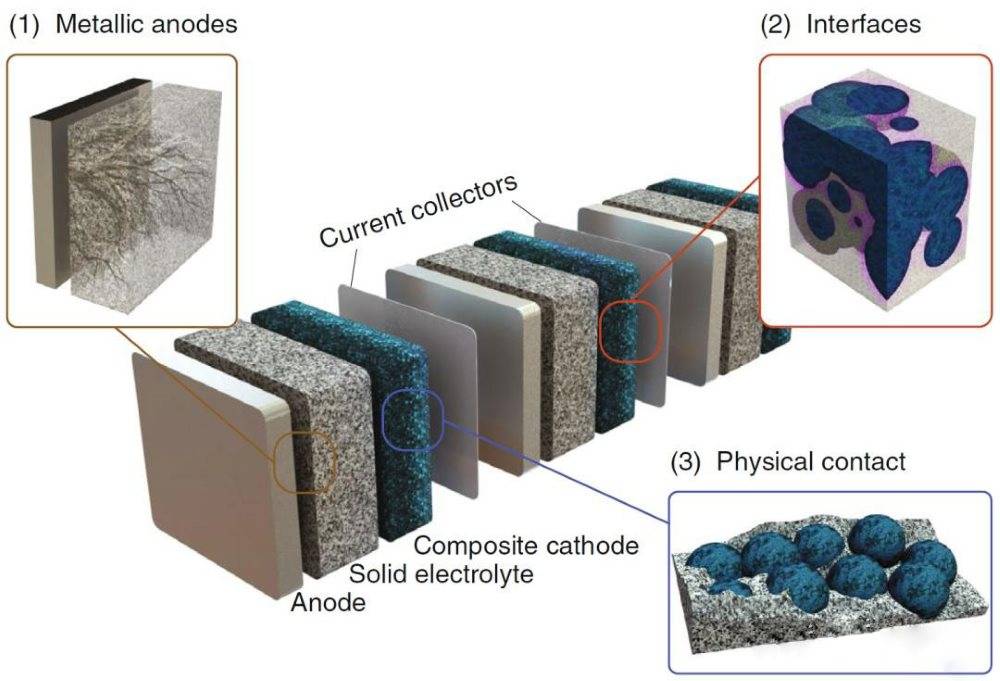
The use of isostatic pressing in this context offers several advantages. Firstly, it enables the creation of membranes with exceptional mechanical properties, including high flexibility and strength, which are essential for the operational reliability of solid-state batteries. Secondly, this technique facilitates the production of electrolytes with precise thickness and uniformity, crucial for maintaining consistent ion conductivity and overall battery performance.
Moreover, the process of forming these electrolytes through isostatic pressing involves a series of controlled steps, each contributing to the final product's quality. These steps include the precise mixing of raw materials, the formation of a slurry with optimal viscosity, and the application of isostatic pressure to consolidate the material into a dense, yet flexible, membrane. This methodical approach ensures that the resulting solid electrolytes meet the stringent requirements for use in next-generation solid-state lithium batteries.
In summary, isostatic pressing plays a pivotal role in the production of solid electrolytes, enabling the creation of high-performance, ultra-thin membranes that are integral to the advancement of solid-state battery technology.
Preparation of Garnet-Type Solid Electrolyte
The synthesis of Garnet-type solid electrolytes, such as those based on Al-LLZTO (Aluminum-doped Lithium Lanthanum Zirconate Titanate), involves a meticulous multi-step process designed to achieve high purity and structural integrity. The procedure begins with calcining, a thermal treatment that removes volatile components and stabilizes the precursor material. Following calcination, the material undergoes ball milling, a technique that grinds the particles into a fine powder, enhancing the homogeneity and reactivity of the mixture.
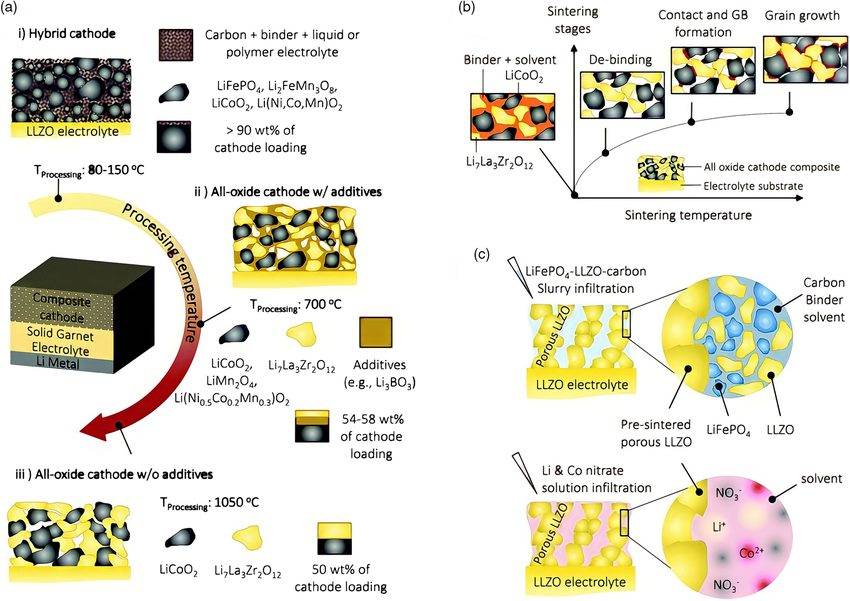
Cite:Al-Salih, Hilal & Houache, Mohamed & Baranova, Elena & Abu-Lebdeh, Yaser. (2022). Composite Cathodes for Solid‐State Lithium Batteries: “Catholytes” the Underrated Giants. Advanced Energy and Sustainability Research. 3. 10.1002/aesr.202200032.
After milling, the powder is subjected to drying to remove any residual moisture, ensuring that subsequent steps are not compromised by water content. The dried powder then advances to sintering, a high-temperature process that induces densification and grain growth, forming a dense ceramic body. Finally, the sintered material is subjected to cold isostatic pressing (CIP), a method that applies uniform pressure through a liquid medium, further consolidating the structure and enhancing mechanical properties. This comprehensive approach ensures the production of a Garnet-type solid electrolyte with superior performance characteristics, suitable for advanced solid-state battery applications.
CONTACT US FOR A FREE CONSULTATION
KINTEK LAB SOLUTION's products and services have been recognized by customers around the world. Our staff will be happy to assist with any inquiry you might have. Contact us for a free consultation and talk to a product specialist to find the most suitable solution for your application needs!