The Evolution and Applications of Isostatic Pressing
The inception and growth of isostatic pressing
Table of Contents
- The Evolution and Applications of Isostatic Pressing
- The Three Basic Types of Isostatic Pressing
- Comparison of Isostatic Pressing Methods
- Types of Cold Isostatic Pressing: Wet-Bag and Dry-Bag CIP
- Warm Isostatic Pressing (WIP)
- Hot Isostatic Pressing (HIP)
- Versatility of Isostatic Processing
- Conclusion
Isostatic pressing, a technique that applies hydrostatic pressure to a material to improve its density and mechanical strength, has seen significant growth and development over the years. Originally pioneered in the mid-1950s as a research curiosity, it has now become a viable production tool for many industries. Isostatic pressing is commonly used for the consolidation of powders and defect healing of castings, making it a versatile process for a range of materials including ceramics, metals, composites, plastics, and carbon.

Industries and materials that utilize isostatic pressing
Isostatic pressing finds applications in various industries, particularly those that require complex parts with specific geometries. Industries such as aerospace, automotive, and medical rely on isostatic pressing to produce parts with superior structural integrity. Isostatic pressing is also widely used in the manufacturing of advanced ceramics, which are utilized in the aerospace and automotive sectors. Isostatically pressed ceramics offer improved mechanical properties such as high hardness, wear resistance, and thermal stability, making them ideal for demanding applications.
The benefits of isostatic pressing for ceramic and refractory applications
Isostatic pressing offers unique benefits for ceramic and refractory applications. The process applies a uniform, equal force over the entire product, regardless of its shape or size. This ability to provide uniform pressure enables the formation of product shapes with precise tolerances, reducing the need for costly machining. Isostatically pressed ceramics exhibit higher density and improved mechanical properties compared to other manufacturing methods, making them highly desirable for industries that require high-performance materials.
Increase in Adoption of Additive Manufacturing
In recent years, additive manufacturing has gained significant traction in various industries. This has led to an increase in the demand for isostatic pressing as a post-processing technique. The combination of additive manufacturing and isostatic pressing provides a comprehensive solution for the production of complex and functional parts. Isostatic pressing helps achieve dimensional accuracy and stability for additive manufactured parts by subjecting them to uniform pressure. This process reduces or eliminates residual stresses and distortions, ensuring that the final part meets the required specifications.

The evolution and applications of isostatic pressing have revolutionized manufacturing processes in industries such as aerospace, automotive, and medical. The ability to produce high-density, high-performance materials with precise tolerances has driven the growth of the isostatic press market. As the demand for advanced materials continues to increase, the market is expected to expand further, creating opportunities for technological advancements and innovative solutions across various industries.
The Three Basic Types of Isostatic Pressing
Isostatic pressing is a powder processing technique that is used to compact materials by applying pressure evenly from all directions. This process helps to achieve uniform density and microstructure without the limitations of uniaxial pressing. There are three basic types of isostatic pressing: Cold isostatic pressing (CIP), Warm isostatic pressing (WIP), and Hot isostatic pressing (HIP).
Comparison of Isostatic Pressing Methods
Advantages, limitations, and cycle times of cold, warm, and hot isostatic pressing
Isostatic pressing is a powder processing technique that uses fluid pressure to compact a part. Metal powders are placed in a flexible container, which serves as the mold for the part. Fluid pressure is applied over the entire outside surface of the container, causing it to press and form the powder into the desired shape. Unlike other processes that exert forces on the powder through an axis, isostatic pressing uses all-around pressure.

Cold isostatic presses, warm isostatic presses, and hot isostatic presses are different types of equipment that utilize high-pressure gases to process materials. These presses heat or cool the gas to a specific temperature and then apply uniform pressure to the material through a closed vessel. This method improves the density, structure, and properties of various materials such as ceramics, metals, and composites.
The main difference between cold, warm, and hot isostatic presses lies in the temperature at which they operate during forming and consolidation. Cold isostatic presses are typically used in room temperature environments and are suitable for temperature-sensitive materials like ceramics and metal powders. Warm isostatic presses work at medium temperatures and are suitable for materials with specific temperature requirements, such as plastics and rubber. Hot isostatic presses, on the other hand, operate at high temperatures and are suitable for materials that require high-temperature processing, such as metals and alloys.
Here are some advantages and limitations of each isostatic pressing method:
-
Cold Isostatic Pressing (CIP):
- Advantages:
- Suitable for temperature-sensitive materials
- Can achieve high levels of material density and uniformity
- Can produce complex shapes with minimal defects
- Limitations:
- Longer cycle times compared to warm and hot isostatic pressing
- Limited to materials that can withstand the applied pressure and temperature
- Advantages:
-
Warm Isostatic Pressing (WIP):
- Advantages:
- Suitable for materials with specific temperature requirements
- Can improve material properties, such as strength and durability
- Can be used for both metal and non-metal materials
- Limitations:
- Requires careful control of temperature and pressure to avoid material degradation
- Limited to materials that can withstand the applied pressure and temperature
- Advantages:
-
Hot Isostatic Pressing (HIP):
- Advantages:
- Suitable for materials that require high-temperature processing
- Can achieve high levels of material density and uniformity
- Can eliminate defects and improve material properties, such as fatigue resistance
- Limitations:
- Expensive equipment and operating costs
- Limited to materials that can withstand the high temperatures and pressures involved
- Advantages:
In summary, each isostatic pressing method offers distinct advantages and limitations. The choice between cold, warm, and hot isostatic pressing depends on the specific goals of your project and the characteristics of the materials being processed. Consider factors such as temperature sensitivity, required material properties, and cost-effectiveness when selecting the appropriate method for your application.
Cold Isostatic Pressing is a viable option for temperature-sensitive materials and can achieve high material density and shape complexity.
Types of Cold Isostatic Pressing: Wet-Bag and Dry-Bag CIP
Description and benefits of wet-bag method
Wet bag isostatic pressing is a type of cold isostatic pressing that involves placing the powder into a forming mold, also known as the casing. The mold is then sealed and placed in a high-pressure cylinder for pressing. During the pressing process, the mold is completely immersed in a liquid, which serves as the pressure transmission medium.

The wet bag method offers several benefits. It has strong applicability and is particularly suitable for experimental research and small batch production. It allows for the simultaneous pressing of multiple different shapes of parts in a single high-pressure cylinder, making it ideal for producing large and complex parts. Additionally, the production process is relatively short and cost-effective.
Description and advantages of dry-bag method
The dry bag method is another type of cold isostatic pressing. In this process, the powder material is enclosed in a flexible mold bag, which is then submerged into a high-pressure liquid in a pressure vessel. Isostatic pressure is applied to the outer surfaces of the mold, compressing the powder into a desired shape.
The dry bag method offers advantages in terms of automation and high-volume production. It is suitable for producing relatively simple shapes in large quantities. The process is automated, allowing for efficient and consistent production. This method is especially beneficial when there is a need for high-volume production of relatively simple shapes.
Overall, both wet-bag and dry-bag methods of cold isostatic pressing have their own unique advantages and applications. The choice of method depends on factors such as the complexity of the parts, production volume, and cost considerations. By understanding these methods, manufacturers can make informed decisions when selecting the most suitable cold isostatic pressing technique for their specific needs.
Warm Isostatic Pressing (WIP)
The process and applications of WIP
Warm Isostatic Pressing (WIP) is a variant of cold isostatic pressing (CIP) that includes a heating element. It employs warm water or a similar medium to apply uniform pressure to powdered products from all directions. WIP is a cutting-edge technology that enables isostatic pressing at a temperature that does not exceed the boiling point of the liquid medium.
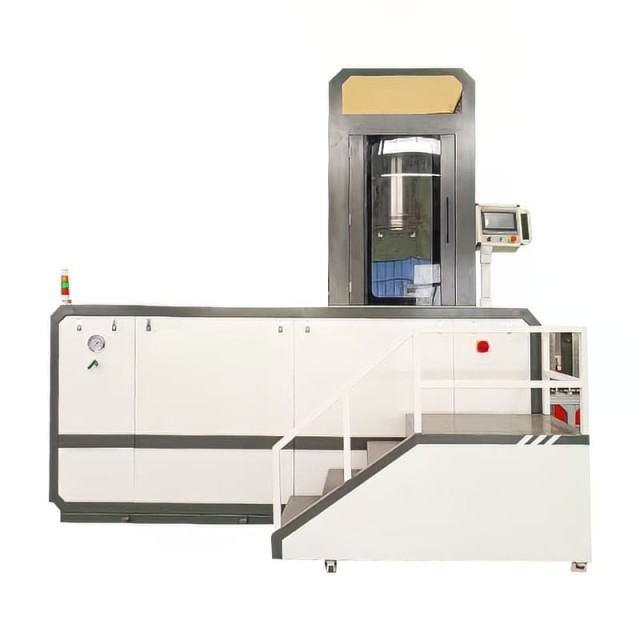
WIP utilizes flexible materials as a jacket mold and hydraulic pressure as a pressure medium to shape and press the powder material. The process involves heating the liquid medium first and then continuously injecting the heated liquid medium into a sealed pressing cylinder through a booster source. This ensures the accuracy of temperature control.
WIP is commonly used for plastics and laminated products. It is a versatile process that can be customized for different applications, making it suitable for a wide range of industries. The system can be gas or liquid pressurized and can operate at various pressures. Liquid WIP systems can reach temperatures up to 250°C, while gas WIP systems can go up to 500°C.
Comparison between WIP and heated platen press
Traditionally, a heated platen press has been applied in applications similar to WIP. However, the heated platen press has a drawback of uneven pressure distribution, which can result in dimensional variations from one side to the other. This lack of uniform pressure affects the quality and consistency of the final product.
WIP, on the other hand, offers a well-suited alternative by providing equal and uniform pressure on all surfaces. This ensures that the parts are pressed uniformly, leading to consistent dimensions and improved product quality.
The use of warm water or a similar medium in WIP allows for controlled and precise heating, further enhancing the effectiveness of the process. The combination of uniform pressure and controlled heating makes WIP a superior choice for applications that require high-quality and dimensionally accurate products.
In addition to its advantages in terms of pressure distribution and temperature control, WIP can also be customized to meet specific requirements. It offers features such as custom modes for special functions and a touch screen with computer-based graphical operation interface for ease of use.
Overall, WIP provides a more efficient and reliable solution compared to heated platen presses, making it a preferred choice for various industries.
Hot Isostatic Pressing (HIP)
Hot Isostatic Pressing (HIP) is a manufacturing process that applies high temperature and pressure to materials in order to improve their mechanical properties. The process involves heating the materials in a sealed chamber and applying isostatic pressure uniformly in all directions using an inert gas, typically argon. This pressure causes voids in the material to collapse, resulting in improved density and eliminating defects such as porosity. HIP is especially beneficial for materials that require enhanced structural integrity and higher mechanical properties.
The Two Methods Used in HIP: Direct HIP and Post-HIP
There are two main methods used in HIP: direct HIP and post-HIP.
Direct HIP involves subjecting the material to high pressure and high temperature simultaneously within a pressure vessel. This method is used to densify the material, eliminate defects, and enhance its properties through diffusion and consolidation. Direct HIP is ideal for creating high-performance materials with superior mechanical properties and structural integrity.
On the other hand, post-HIP involves using HIP as a post-processing step for materials that have already undergone other manufacturing processes, such as 3D printing. Post-HIP is used to reduce the porosity of the materials and increase their density. This process helps improve the material's mechanical properties and workability.

The Role of Various Barriers in Direct HIP
In direct HIP, various barriers play a crucial role in the process. These barriers include the material's melting point, the pressure vessel's strength, and the inert gas used. The material's melting point determines the maximum temperature that can be applied during the HIP process. The pressure vessel's strength ensures that it can withstand the high pressure required for HIP. The inert gas, usually argon, helps apply the isostatic pressure uniformly to the material.
The Process and Benefits of Post-HIP
Post-HIP is a process that involves subjecting materials to high pressure and temperature after they have undergone other manufacturing processes. The materials are loaded into a pressure vessel inside a high-temperature furnace and held at a specified temperature and pressure for a certain amount of time. This process helps reduce the porosity of the materials and improve their density, resulting in enhanced mechanical properties. The benefits of post-HIP include increased strength, improved fatigue resistance, and enhanced overall performance of the materials.
The Factors Affecting HIP Cycle Time and the Role of Advanced Furnaces
Several factors can affect the cycle time of the HIP process. These factors include the material's composition, the desired properties, and the size and complexity of the part. Materials with a higher melting point may require longer cycle times to achieve the desired results. Additionally, larger and more complex parts may require longer cycle times due to the need for uniform pressure distribution.
Advanced furnaces play a crucial role in the HIP process by providing precise temperature and pressure control. These furnaces are equipped with advanced technology that allows for accurate heating and cooling rates, as well as precise pressure control. This helps optimize the HIP process and reduce cycle times, resulting in more efficient production.
In summary, Hot Isostatic Pressing (HIP) is a manufacturing process that applies high temperature and pressure to materials to improve their mechanical properties. The process can be carried out through direct HIP or post-HIP methods, depending on the specific requirements of the materials. HIP offers numerous benefits, including increased density, improved structural integrity, and enhanced mechanical properties. Advanced furnaces and precise control of temperature and pressure are essential for optimizing the HIP process and reducing cycle times.
Versatility of Isostatic Processing
The wide range of applications of isostatic processing
Isostatic processing is a versatile process that has found wide use for many different materials in a variety of applications. It offers unique benefits for ceramic and refractory applications due to its ability to apply a uniform, equal force over the entire product, regardless of shape or size. This process is used in industries such as aerospace, automotive, energy, medical, and electronics.
One of the main applications of isostatic processing is cold isostatic pressing (CIP), which is a powder consolidation process. CIP uses inexpensive molds as barriers to compact powders into simple to complex shapes at densities ranging from 60% to 80%. The choice between a "wet bag" or "dry bag" method depends on factors such as the type, mix, and production lots of parts produced.
Warm isostatic pressing (WIP) is another variant of isostatic processing that has found a niche in certain industries. WIP involves applying combined pressure and low temperatures, typically up to 100°C, to specific materials in industries where these parameters are specified.
The use of hot isostatic pressing (HIP) is gaining momentum in the engineered ceramics field. HIP is used to obtain near-net-shape and fully dense ceramics for high-performance applications. It can also be used to eliminate residual porosity from sintered powder metallurgy parts. The choice between direct HIP or post-HIP depends on the material or process specified.
The role of CIP in consolidating powders
Cold isostatic pressing (CIP) is a process used for consolidating metal powders into solid parts. It has applications in various industries, including medical implants and stainless steel filter cartridges. The quality of the CIPed parts depends on the powder materials and properties. Powder metallurgy is a viable manufacturing route for producing specific materials, especially for high-performance applications, as it reduces material waste and produces parts that are close to the final shape.

CIP has been successfully used to consolidate most common metals, but there is increasing interest in exploiting the technology for metal powder processing in a wider range of applications. Factors such as powder properties, tooling types, process parameters, post-processing, and mechanical properties play a crucial role in determining the quality of the CIPed parts.
The role of WIP in specific industries
Warm isostatic pressing (WIP) is a cutting-edge technology that enables isostatic pressing at a temperature that does not exceed the boiling point of the liquid medium. It is used in industries where combined pressure and low temperatures are specified. WIP employs warm water or a similar medium to apply uniform pressure to powdered products from all directions.
The WIP process typically involves heating the liquid medium first and then continuously injecting the heated liquid medium into a sealed pressing cylinder through a booster source. This process uses flexible materials as a jacket mold and hydraulic pressure as a pressure medium to shape and press the powder material. WIP ensures accurate temperature control by equipping the pressing cylinder with a heating element.
The increasing use of HIP in engineered ceramics field
Hot isostatic pressing (HIP) is gaining popularity in the engineered ceramics field for obtaining near-net-shape and fully dense ceramics for high-performance applications. HIP is used to reduce porosity in metals and increase the density of ceramic materials. Advanced HIP machines are capable of applying higher pressures, often exceeding 145,000 PSI, resulting in enhanced material density and reduced absorbency.
The combination of additive manufacturing and isostatic pressing has gained traction in various industries. Isostatic pressing is used as a post-processing technique for additive manufactured parts to achieve dimensional accuracy and stability. It subjects the manufactured components to uniform pressure, reducing or eliminating residual stresses or distortions and ensuring that the parts meet the required specifications.
Isostatic pressing technology has advanced over the years, with the development of high-pressure isostatic press (HIP) systems. These advancements have significantly improved the efficiency and effectiveness of the process, allowing for higher pressures and enhanced material density.

Isostatic pressing has proven to be a valuable manufacturing solution across industries. Its versatility and adaptability enable industries to seek advanced manufacturing solutions, driving the demand for isostatic pressing in the near future. The market for isostatic presses is expected to continue growing as the demand for advanced materials increases, creating opportunities for technological advancements and innovative solutions. Isostatic pressing offers a comprehensive solution for the production of complex and functional parts in industries such as aerospace, automotive, energy, medical, and electronics.
Conclusion
In conclusion, the isostatic pressing process offers numerous benefits and applications in various industries. Cold isostatic pressing (CIP), warm isostatic pressing (WIP), and hot isostatic pressing (HIP) are the three main types of isostatic pressing. CIP is known for its ability to produce complex shapes and uniform density, while WIP provides excellent material properties and is often used in aerospace and automotive industries. HIP, on the other hand, is widely utilized in the engineered ceramics field for its ability to enhance material properties and eliminate defects. With its versatility and effectiveness, isostatic pressing continues to play a crucial role in consolidating powders and producing high-quality components.
If you are interested in this product you can browse our company website:https://kindle-tech.com/product-categories/isostatic-press, we always insist on the principle of quality first. During the production process, we strictly control every step of the process, using high quality materials and advanced production technology to ensure the stability and durability of our products. to ensure that their performance meets the highest standards. We believe that only by providing customers with excellent quality can we win their trust and long-term cooperation.
CONTACT US FOR A FREE CONSULTATION
KINTEK LAB SOLUTION's products and services have been recognized by customers around the world. Our staff will be happy to assist with any inquiry you might have. Contact us for a free consultation and talk to a product specialist to find the most suitable solution for your application needs!