Introduction
Table of Contents
Isostatic pressing is a versatile manufacturing process that is widely used in various industries. It involves subjecting a material to equal pressure from all directions to achieve uniform density and shape. Isostatic pressing offers numerous advantages, such as the ability to produce complex shapes, uniformity in material properties, and high precision. This comprehensive guide will delve into the different types of isostatic pressing, including cold, warm, and hot pressing. We will explore the processes, features, and applications of each type, providing you with a thorough understanding of this essential manufacturing technique. So let's dive in!
Understanding Isostatic Pressing
Definition of Isostatic Pressing
Isostatic pressing is a powder processing technique that involves applying equal pressure to each surface of a product in a closed container filled with liquid. This process increases the density of the product under high pressure, allowing it to take on the required shape. Isostatic pressing is commonly used in the forming of high-temperature refractory, ceramics, cemented carbide, lanthanum permanent magnet, carbon material, and rare metal powder.
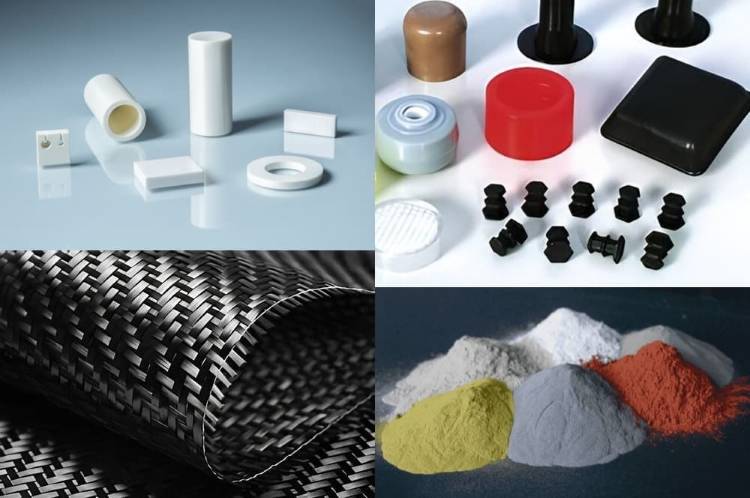
Features of Isostatic Pressing
Isostatic pressing is a unique powder processing technique that utilizes fluid pressure to compact the part. In this process, metal powders are placed in a flexible container, which serves as the mold for the part. Unlike other processes that exert forces on the powder through an axis, isostatic pressing applies pressure evenly over the entire outside surface of the container. This all-around pressure allows for uniform compaction and shaping of the powder into the desired geometry.
Principle of Fluid Mechanics in Isostatic Pressing
Isostatic pressing works by reducing the porosity of a powder mixture to produce various types of materials. The powder mixture is compacted and encapsulated using isostatic pressure, which involves applying pressure equally from all directions. This is achieved by confining the metal powder within a flexible membrane or hermetic container. The pressure barrier created by the membrane or container ensures that the pressure is uniformly transferred to the powder from all directions. This principle of fluid mechanics enables the powder to be uniformly pressurized and shaped in all directions. Isostatic pressing can be further categorized into three types based on the molding temperature: hot isostatic pressing (HIP), warm isostatic pressing (WIP), and cold isostatic pressing (CIP).
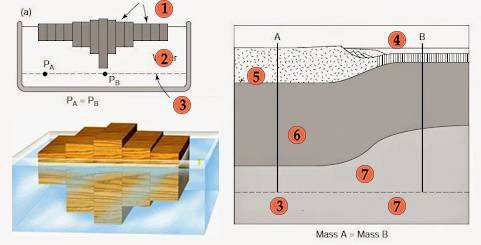
Isostatic pressing offers several advantages over conventional metallurgical techniques. The all-around pressure exerted by the fluid during the process ensures uniform compaction of the powder and consistent density within the compacted part. This eliminates density variations that may occur with conventional processing methods. Isostatic pressing is particularly useful for producing larger parts, parts with high thickness to diameter ratios, and parts with superior material properties. However, it is important to note that isostatic pressing tends to have longer cycle times and is best suited for short production runs.
In conclusion, isostatic pressing is a powerful manufacturing process that applies equal pressure in all directions to achieve maximum uniformity of density and microstructure in powder compacts. This process is used in various industries and offers unique advantages over traditional processing methods.
Types of Isostatic Pressing
Isostatic pressing is a powder metallurgy procedure that evenly presses a powder compact in all directions to provide uniform density and microstructure. There are three main types of isostatic pressing:
1. Isostatic Cold Pressing
Isostatic cold pressing involves compacting a powder in an elastomeric container submerged in a fluid at a pressure of 20 to 400 MPa. This process allows for the production of small or large powder compacts with a uniform green density, even for parts with large height/diameter ratios. However, it sacrifices pressing speed and dimensional control, requiring subsequent machining in the green compact. Cold isostatic pressing is commonly used for powders that are difficult to press, such as hard metals.
2. Isostatic Warm Pressing
Isostatic warm pressing (WIP) is a variant of cold isostatic pressing (CIP) that includes a heating element. It uses warm water or a similar medium to apply uniform pressure to powdered products from all directions. WIP enables isostatic pressing at a temperature that does not exceed the boiling point of the liquid medium. This process involves utilizing flexible materials as a jacket mold and hydraulic pressure as a pressure medium to shape and press the powder material. The pressing cylinder is equipped with a heating element to ensure temperature control.
3. Isostatic Hot Pressing
Hot isostatic pressing (HIP) is a process of compressing materials under high temperatures and pressure. It improves the mechanical properties of castings by eliminating internal microporosity. HIP is offered as systems and services that include wet bag pressing and dry bag pressing. The capacities involved range from small-sized HIP to medium-sized HIP and large-sized HIP. This process finds applications in various industries such as manufacturing, automotive, electronics and semiconductor, medical, aerospace and defense, energy and power, research and development, and others.
Isostatic pressing, whether it is cold, warm, or hot, offers significant advantages in achieving uniform density and microstructure in powder compacts. These processes are widely used in industries that require high-quality components with optimal mechanical properties.
Isostatic Cold Pressing
Process of Isostatic Cold Pressing
Isostatic cold pressing, also known as cold isostatic pressing (CIP), is a manufacturing process performed at room temperature. In this process, a mold made from an elastomer material such as urethane, rubber, or polyvinyl chloride is used. The powder material is compacted to a uniform density by applying isostatic pressure to the outer surfaces of the mold. The green compact is then conventionally sintered to produce the desired part.
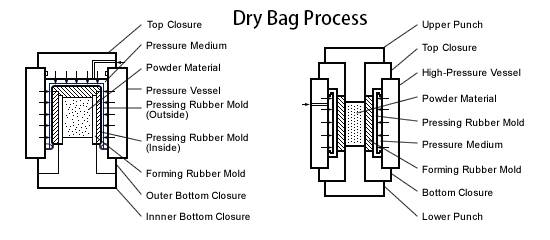
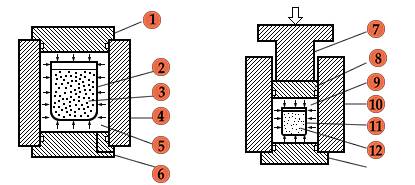
Differentiation between Dry Bag and Wet Bag Isostatic Pressing
Isostatic cold pressing can be categorized into two methods: dry bag isostatic pressing and wet bag isostatic pressing.
In dry bag isostatic pressing, the powder is directly pressed into the fixed forming die (sleeve) in the high-pressure cylinder. This method is suitable for mass production of simple shapes and parts and offers convenience for automation.
On the other hand, wet bag isostatic pressing involves putting the powder into a forming mold (casing) first, which is then sealed and submerged in a high-pressure cylinder. The mold is in direct contact with the pressure transmission medium, usually a high-pressure liquid. Wet bag isostatic pressing has strong applicability and is especially suitable for experimental research and small batch production. It allows for the simultaneous pressing of multiple different shapes of parts in one high-pressure cylinder and can produce large and complex parts.
Advantages of Dry Bag Isostatic Pressing
Dry bag isostatic pressing offers several advantages. Firstly, it allows for mass production of simple shapes and parts, making it ideal for industries requiring high-volume production. Additionally, the fixed forming die in the high-pressure cylinder enables automation, increasing productivity and efficiency.
Advantages of Wet Bag Isostatic Pressing
Wet bag isostatic pressing also has its advantages. It offers strong applicability and is suitable for experimental research and small batch production. The ability to simultaneously press multiple different shapes of parts in one high-pressure cylinder makes it convenient and cost-effective. Furthermore, wet bag isostatic pressing is capable of producing large and complex parts, expanding its range of applications.
In conclusion, isostatic cold pressing, whether through dry bag or wet bag methods, is a versatile manufacturing process that allows for the production of complex parts with high compact densities. Each method has its own advantages and is suitable for different production requirements.
Isostatic Warm Pressing
Introduction to Isostatic Warm Pressing
Isostatic warm pressing is a technique used to achieve isostatic pressing at a temperature no higher than the standard boiling point of the liquid medium. It involves using a flexible material as the envelope die and hydraulic pressure as the pressure medium to shape and press powder materials.
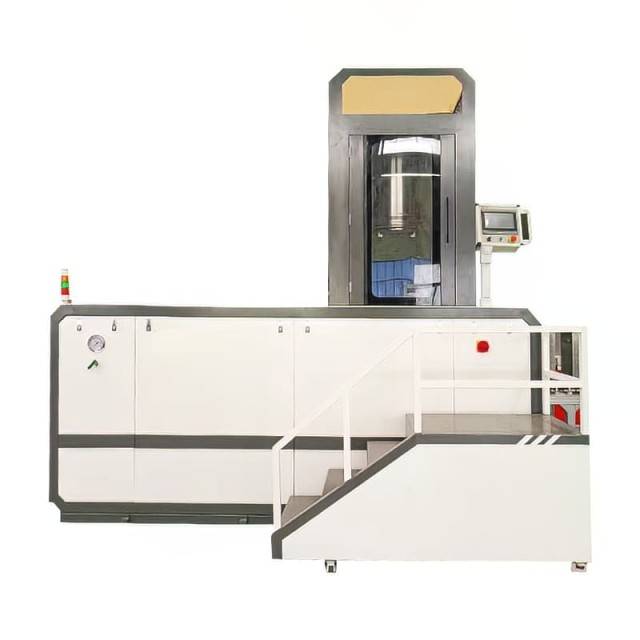
The warm isostatic press is heated with the liquid medium, which is then continuously injected into the sealed pressing cylinder. A heat generator is used in the pressing cylinder to ensure precise temperature control.
Warm isostatic pressing is commonly used for powders, binders, and other materials that have special temperature requirements or cannot be molded at room temperature. This technology has revolutionized the manufacturing industry, allowing for the production of complex parts and components with precision and efficiency.
Role of Binder in Isostatic Warm Pressing
Warm isostatic pressing (WIP) is a variant of cold isostatic pressing (CIP) that includes a heating element. It utilizes warm water or a similar medium to apply uniform pressure to powdered products from all directions.
The binder plays a crucial role in isostatic warm pressing. It helps to hold the powder particles together during the pressing process, ensuring that the final product has the desired shape and strength. The binder also aids in the removal of the part from the mold after pressing.
The selection of the binder depends on the specific requirements of the application. Different binders can be used for different materials and temperature ranges. It is important to choose a binder that can withstand the operating temperature of the warm isostatic press and provide the necessary strength and stability to the pressed part.
Characteristic Operating Temperature of Isostatic Warm Pressing
The operating temperature of the warm isostatic press includes the working temperature and the ambient temperature. The working temperature can be set within the range of 0-240°C, while the ambient temperature is typically between 10-35°C. The working static pressure can be set within the range of 0-240MPa.
The selection of the operating temperature depends on the characteristics of the powder material and the desired molding effect. If the temperature is too low, the powder material may not be fully densified. On the other hand, if the temperature is too high, the powder material may be sintered or deformed. It is important to determine the operating temperature based on the specific requirements to ensure high-quality molding and efficient production.
In conclusion, isostatic warm pressing is a versatile technique that allows for the shaping and pressing of powder materials at controlled temperatures. With the use of a flexible envelope die and hydraulic pressure, complex parts and components can be manufactured with precision and efficiency. The binder plays a crucial role in holding the powder particles together, while the operating temperature must be carefully selected to achieve the desired molding effect.
Isostatic Hot Pressing
Overview of Isostatic Hot Pressing
In the isostatic pressing process, products are put in a closed container filled with liquid and equal pressure is applied to each surface to increase their density under high pressure, thus achieving the required shapes. Isostatic presses are widely used in the forming of high-temperature refractory, ceramics, cemented carbide, lanthanon permanent magnet, carbon material, and rare metal powder.
The warm isostatic press is a technique used to achieve isostatic pressing at a temperature no higher than the standard boiling point of the liquid medium. It involves using a flexible material as the envelope die and hydraulic pressure as the pressure medium to form and press the powder material. Warm isostatic pressing is typically used for materials with special temperature requirements or materials that cannot be formed at room temperature.
Hot isostatic pressing is a manufacturing process that utilizes elevated temperature and isostatic gas pressure to eliminate porosity and increase density in metals, ceramics, polymers, and composite materials. This process improves the material's mechanical properties and workability. Hot isostatic pressing is commonly used for the elimination of microshrinkage in castings, consolidation of powders, diffusion bonding, and the fabrication of metal matrix composites.
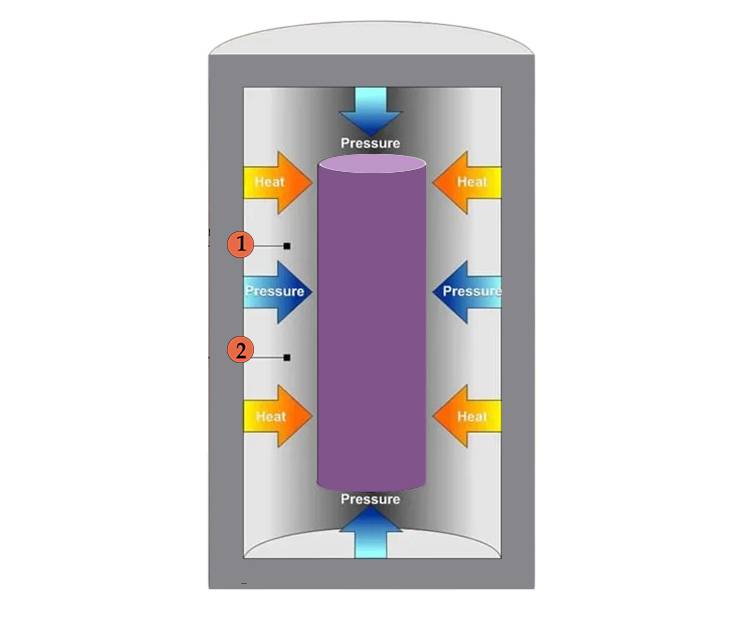
Applications of Isostatic Hot Pressing
Hot isostatic pressing technology is currently used in various industries such as castings, powder metallurgy, ceramics, porous materials, near-net forming, material bonding, plasma spraying, and the manufacture of high-end graphite. It is an effective method for achieving uniform density and microstructure in materials.
Working Medium in Isostatic Hot Pressing
In isostatic hot pressing, the working medium is a liquid or gas that is used to apply equal pressure to the powder compact. The pressure transmitted by the medium is equal in all directions, resulting in uniform compaction and density distribution in the product. The choice of working medium depends on the specific requirements of the material being processed.
Materials used for Sheathing in Isostatic Hot Pressing
In isostatic hot pressing, a sheathing material is used to enclose the powder compact and contain the working medium. The sheathing material should be able to withstand the high temperature and pressure during the pressing process without deforming or reacting with the material being processed. Common materials used for sheathing in isostatic hot pressing include elastomers, metals, and ceramics.
Overall, isostatic hot pressing is a versatile manufacturing process that offers unique benefits for achieving high-density and uniformity in materials. It finds applications in various industries and can be used with different working mediums and sheathing materials depending on the specific requirements of the process.
Conclusion
Isostatic pressing is an incredibly versatile and efficient manufacturing process that offers numerous benefits for a wide range of industries. Whether it's the cold, warm, or hot pressing method, isostatic pressing provides uniform and consistent pressure distribution, resulting in high-quality finished products. The use of dry or wet bags in cold pressing allows for different advantages depending on the specific application. Isostatic warm pressing with binders offers enhanced control over the shaping process, while isostatic hot pressing is ideal for applications requiring high temperatures and specialized materials. Overall, isostatic pressing is a valuable technique that can greatly improve manufacturing outcomes.
If you are interested in our products, please visit our company website: https://kindle-tech.com/product-categories/isostatic-press, where innovation has always been a priority. Our R&D team consists of experienced engineers and scientists who closely follow industry trends and are constantly pushing the boundaries of what is possible. Our laboratory equipment incorporates the latest technology to ensure that you can obtain accurate and repeatable results during your experiments. From high-precision instruments to intelligent control systems, our products will provide you with unlimited possibilities for your experimental work.
CONTACT US FOR A FREE CONSULTATION
KINTEK LAB SOLUTION's products and services have been recognized by customers around the world. Our staff will be happy to assist with any inquiry you might have. Contact us for a free consultation and talk to a product specialist to find the most suitable solution for your application needs!