Introduction to Isostatic Pressing
Isostatic pressing is a manufacturing process that is used to eliminate defects in materials. It involves subjecting a material to high pressure from all directions, which helps to evenly distribute the pressure and eliminate any voids or defects. In this process, the material is placed inside a sealed container and subjected to high pressure using a pressurized fluid such as water or gas. Isostatic pressing can be performed at room temperature (cold isostatic pressing) or at high temperature (hot isostatic pressing). This process is widely used in the aerospace, medical, and automotive industries to produce high-quality components with superior strength and durability.
Table of Contents
- Introduction to Isostatic Pressing
- Cold vs. Hot Isostatic Pressing
- Hot Isostatic Pressing Process
- Benefits of Hot Isostatic Pressing
- Cold Isostatic Pressing Process
- Benefits of Cold Isostatic Pressing
- Isostatic Pressing for Additive Manufacturing
- Importance of Material Characterization
- Types of Isostatic Pressing
- Applications of Isostatic Pressing
- Conclusion
Cold vs. Hot Isostatic Pressing
Isostatic pressing is a process that applies equal pressure in all directions on a powder compact to achieve optimal density and microstructure uniformity. The process has two variations: cold and hot isostatic pressing.
Cold Isostatic Pressing
Cold isostatic pressing is typically used for materials such as ceramics, metals, and polymers that are not heat-resistant. During this process, the materials are placed in a high-pressure vessel filled with a liquid, such as water, and the pressure is applied uniformly to the material from all directions. This helps to eliminate any voids, cracks, or other defects that may be present in the material.
Compared to cold pressing, isostatic compaction applies pressure uniformly over the entire surface of the mold. Die-wall friction, which exerts a major influence on the density distribution of cold-pressed parts, is absent, so much more uniform densities are obtained. The elimination of die-wall lubricants also permits higher pressed densities and eliminates problems associated with lubricant removal prior to or during final sintering.
Hot Isostatic Pressing
Hot isostatic pressing, on the other hand, is used for materials that are heat-resistant and can withstand high temperatures. During this process, the materials are heated to a high temperature and then placed in a high-pressure vessel filled with a gas, typically argon. The pressure is applied uniformly to the material from all directions, which helps to eliminate any defects that may be present in the material.
Hot isostatic pressing is performed to fully consolidate parts at elevated temperatures by solid-state diffusion. It can also be used to eliminate residual porosity from a sintered PM part. The working temperature of hot isostatic press is high temperature, suitable for materials with high-temperature requirements, such as metals, alloys, etc.
Comparison
The main difference between cold and hot isostatic pressing is their high and low temperatures during forming and consolidation. Cold isostatic presses are generally used in room temperature environments and are suitable for temperature-sensitive materials such as ceramics, metal powders, etc. Warm isostatic presses work at medium temperature and are suitable for materials with certain temperature requirements, such as plastics, rubber, etc.
In summary, the choice of whether to use cold or hot isostatic pressing depends on the type of material, temperature resistance, and the desired outcome. Cold isostatic pressing is best suited for materials that are not heat-resistant, while hot isostatic pressing is used for materials that can withstand high temperatures. Both methods help to eliminate defects in materials and create high-quality products with improved density, structure, and properties.
Hot Isostatic Pressing Process
Hot Isostatic Pressing (HIP) is a process that simultaneously applies high temperature and pressure to materials to improve their mechanical properties. The process involves placing materials inside a high-temperature furnace and enclosing the furnace in a pressure vessel. The pressure and temperature are precisely controlled to achieve the desired material properties.
Stage 1: Internal Defects Removal
The first stage of the hot isostatic pressing process involves destroying internal defects and pores in the material by subjecting it to external pressure greater than the material's high-temperature strength of the conditions of plastic deformation. This process helps to remove porosity, inclusions, or other defects in the materials.
Stage 2: Surface Contact and Diffusion Bonding
In the second stage, the external pressure is reduced to a level lower than the material's high-temperature strength, and the material undergoes high-temperature creep. The materials' surface contacts with each other, mutual penetration, and diffusion bonding, completely eliminate defects and porosity.
Argon Gas and Other Gases
In the hot isostatic pressing process, parts are heated in an inert gas, generally argon, which applies "isostatic" pressure uniformly in all directions. Other gases such as nitrogen and helium are sometimes used, while hydrogen and carbon dioxide are rarely used. Sometimes combinations of different gases are also used.
Advantages of Hot Isostatic Pressing Technology
The main advantages of hot isostatic pressing technology are: increased product density, improved mechanical properties, increased productivity, reduced scrap and losses. Castings treated by hot isostatic pressing have internal porosity defects repaired, lighter designs, products with better ductility and toughness, reduced property fluctuations, longer service life, and the ability to form metallurgical bonds between different materials.
Applications
Hot isostatic pressing technology is currently used not only in the treatment of castings, powder metallurgy, and the ceramics industry, but also in porous materials, near-net forming, material bonding, plasma spraying, and the manufacture of high-end graphite. The process is particularly useful for manufacturing materials used in critical applications, such as aerospace parts, medical implants, and high-performance alloys.
In conclusion, hot isostatic pressing is an essential technique for eliminating defects in materials and improving the quality of materials used in critical applications. The process helps to improve the mechanical properties of materials, such as strength and fatigue resistance, and it can be carried out with precision and accuracy, ensuring that the final product is of high quality and meets the required standards.
Benefits of Hot Isostatic Pressing
Hot isostatic pressing (HIP) is a specific type of isostatic pressing that involves heating the material to a high temperature before applying pressure. This process has several benefits over other manufacturing methods. Below are some of the benefits of hot isostatic pressing:
1. Improved strength and ductility
HIP can improve the mechanical properties of materials, such as impact resistance, ductility, and fatigue strength, by removing internal porosity. This is achieved by applying pressure and temperature uniformly throughout the material, resulting in a fine-grain structure and homogeneous microstructures. This, in turn, leads to improved strength and ductility.
2. Increased resistance to corrosion and fatigue
HIP can also enhance the resistance of materials to corrosion and fatigue. By controlling the grain size and shape and producing homogeneous microstructures, HIP can improve the wear and corrosion resistance of materials. This is achieved through cladding, extended alloying possibilities, and producing homogeneous microstructures.
3. Enhanced overall performance
The improved mechanical properties, wear and corrosion resistance, and ductility resulting from HIP lead to enhanced overall performance of materials. This is particularly important in high-performance applications, such as in the aerospace, automotive, and medical industries, where materials must meet stringent standards.
4. Uniform density
HIP can produce materials with uniform density, which is particularly important in ceramic and refractory applications. The ability to form product shapes to precise tolerances (reducing costly machining) has been a major driving force for its commercial development. This is achieved by applying equal pressure in all directions, regardless of shape or size, resulting in a more uniform final component density.
5. Reduction in welds
HIP enables diffusion bonding of similar and dissimilar materials, either in powder or solid form. This means that components can be designed and fabricated with a reduction, or complete elimination, in the number of welds and related inspections.
In conclusion, hot isostatic pressing (HIP) is an important manufacturing process that can improve the mechanical properties, wear and corrosion resistance, and ductility of materials. By eliminating defects in the material, HIP helps manufacturers produce superior products that are reliable and long-lasting.
Cold Isostatic Pressing Process
Cold isostatic pressing (CIP) is a widely used method for compacting powdered materials into a solid homogeneous mass before machining or sintering. It is used for parts that are too large to be pressed in uniaxial presses and that do not require high precision in the sintered state. In this process, the powder is subjected to equal pressure from all directions, followed by machining.
How does it work?
In the cold isostatic pressing process, a mould or vacuumed sample is placed into a chamber that is filled with a working fluid, usually water with a corrosion inhibitor, which is pressurized by an external pump. The pressure chamber of the CIP machine is designed to withstand the severe cyclic loading imposed by rapid production rates and has taken into account fatigue failure.
Advantages over traditional methods
Compared with manual CIP, the electrical CIP can deliver better pressure control. Isostatic compaction applies pressure uniformly over the entire surface of the mould. Die-wall friction, which exerts a major influence on the density distribution of cold-pressed parts, is absent. Therefore, much more uniform densities are obtained. The elimination of die-wall lubricants also permits higher pressed densities and eliminates problems associated with lubricant removal prior to or during final sintering. Furthermore, if necessary, air can be evacuated from the loose powder before compaction.
Applications
Cold isostatic pressing is useful in the production of ceramic and metallic components that require high strength and reliability. The technique is also useful in the production of semiconductor materials, where a high level of purity is necessary. In addition to its defect-eliminating capabilities, cold isostatic pressing can be used to create complex shapes and geometries that are difficult to achieve using traditional manufacturing methods.
Conclusion
Cold isostatic pressing is an effective technique for compacting powdered materials into a solid homogeneous mass before machining or sintering. It offers several advantages over traditional methods, such as uniform density distribution, the elimination of die-wall lubricants, and the ability to evacuate air from the loose powder. This technique finds its applications in the production of ceramic and metallic components, semiconductor materials, and in creating complex shapes and geometries.
Benefits of Cold Isostatic Pressing
Cold isostatic pressing (CIP) is a process that has several benefits in the manufacturing of various materials. The process involves the application of uniform pressure from all sides of a material, resulting in a uniform density and improved structural integrity. Here are some of the benefits of cold isostatic pressing:
Uniform Strength
Since the pressure used in CIP is equal in all directions, the material produced has uniform strength. Materials with uniform strength are usually more efficient than those without uniform strength.
Versatility
CIP can be used to produce difficult shapes that cannot be produced by other methods. In addition, it can be used to produce large-sized materials. The only limitation to the size of materials produced by this method is the size of the pressure vessel.
Corrosion Resistance
Cold isostatic pressing improves the corrosion resistance of a material. Thus materials that undergo this process have a longer lifespan than most other materials.
Mechanical Properties
The mechanical properties of cold isostatic pressed materials are improved. Some of the properties improved include ductility and strength.
Green Strength
Materials produced via cold isostatic pressing have high green strength. This means that such materials have a higher turnover as they can be sintered or machined faster than other materials.
Uniform Density
Cold isostatic pressing ensures that materials have a uniform density. This means that there will be uniform shrinkage when the material is going through other processes such as sintering. The uniform density can be attributed to the fact that the pressure used in CIP reaches every part of the material with equal magnitude.
Powder Metallurgy
CIP is used in powder metallurgy. It is used for the compacting step of powder metallurgy that comes just before the sintering step. In powder metallurgy, CIP is often used to produce complex shapes and dimensions.
Refractory Metals
CIP is used to produce refractory metals such as tungsten, molybdenum, and tantalum. Tungsten, for example, is used to manufacture wires for filaments in the lamp industry. Generally, refractory metals have a high melting point and are resistant to wear and tear.
Sputtering Targets
Cold isostatic pressing (CIP) can press indium tin oxide (ITO) powder into large ceramic preforms, which are then sintered under certain conditions. This method can theoretically produce ceramic targets with a density of 95%.
Automobiles
Cold isostatic pressing is used in manufacturing automobile components such as bearings and oil pump gears.
In conclusion, cold isostatic pressing has revolutionized the manufacturing industry, allowing for the production of stronger, more durable materials that can be used in a wide range of applications. From improved green strength to uniform density, cold isostatic pressing has several advantages over other similar processes.
Isostatic Pressing for Additive Manufacturing
Additive manufacturing, commonly known as 3D printing, has revolutionized the manufacturing industry. However, 3D-printed parts often suffer from defects such as porosity and uneven density. These defects can affect the quality and reliability of the part, especially in critical applications such as aerospace and medical industries. Isostatic pressing has emerged as a solution to eliminate these defects and improve the overall quality of 3D-printed parts.
What is Isostatic Pressing for Additive Manufacturing?
Isostatic pressing is a process that involves applying uniform pressure to a material from all sides, which helps to eliminate defects and improve its overall quality. In the field of additive manufacturing, isostatic pressing is used to produce high-quality parts and eliminate the porosity and defects commonly associated with 3D printing. The process involves placing a 3D-printed part in a container filled with a liquid or gas and applying pressure to the container to equalize the pressure on all sides of the part. This process helps to remove any remaining air pockets or voids in the part, resulting in a more uniform and dense material.
How Does Isostatic Pressing Work?
Isostatic pressing involves placing the powder specimen to be pressed in a high-pressure container, using the incompressible nature of the liquid or gas medium, and the nature of uniform transfer of pressure from all directions to uniformly pressurize the specimen. In additive manufacturing, the 3D-printed part is placed in a container filled with a liquid or gas, and pressure is applied to the container to equalize the pressure on all sides of the part. This process helps to remove any remaining air pockets or voids in the part, resulting in a more uniform and dense material.
Benefits of Isostatic Pressing for Additive Manufacturing
Isostatic pressing eliminates defects and porosity in 3D-printed parts, resulting in a more uniform and dense material. This process is particularly useful in the production of parts for critical applications, such as aerospace and medical industries, where the quality and reliability of the part are of utmost importance. The ability of isostatic pressing to eliminate defects in materials has made it an essential tool in many industries, ensuring the quality and performance of materials used in critical applications.
Conclusion
In conclusion, isostatic pressing has emerged as a solution to eliminate the defects and porosity commonly associated with 3D printing. The process involves applying uniform pressure to a material from all sides, which helps to eliminate defects and improve its overall quality. Isostatic pressing is particularly useful in the production of parts for critical applications, such as aerospace and medical industries, where the quality and reliability of the part are of utmost importance. The ability of isostatic pressing to eliminate defects in materials has made it an essential tool in many industries, ensuring the quality and performance of materials used in critical applications.
Importance of Material Characterization
Material characterization is a critical step in the isostatic pressing process to ensure that the correct material is selected for the application and that it can withstand the high pressure and temperature conditions involved in the CIP process. It involves analyzing the physical and chemical properties of the material to determine its suitability for specific applications.
Analyzing Material Composition
The composition of the material plays a crucial role in determining its properties. Analyzing the composition of a material can help manufacturers select the right materials for their products and optimize their manufacturing processes to produce high-quality, defect-free materials. In addition, analyzing the composition of a material can help identify any potential defects or weaknesses that may affect the material's performance.
Determining Microstructure
Microstructure analysis is another critical aspect of material characterization. It involves examining the internal structure of a material at the microscopic level to determine its properties. By understanding the microstructure of a material, manufacturers can identify any potential defects or weaknesses that may affect the material's performance. Microstructure analysis can also help optimize the manufacturing process to produce high-quality, defect-free materials.
Thermal and Mechanical Properties
Another essential aspect of material characterization is analyzing the thermal and mechanical properties of the material. Thermal properties determine how materials respond to changes in temperature, while mechanical properties determine how materials respond to external forces. By understanding the thermal and mechanical properties of a material, manufacturers can select the right materials for their products and optimize their manufacturing processes to produce high-quality, defect-free materials.
Importance of Defect Analysis
Defect analysis is a crucial part of material characterization. It involves identifying and analyzing any defects or weaknesses in a material that may affect its performance. Defect analysis can help manufacturers select the right materials for their products and optimize their manufacturing processes to produce high-quality, defect-free materials.
In conclusion, material characterization is an essential step in the isostatic pressing process to ensure that the correct material is selected for the application and that it can withstand the high pressure and temperature conditions involved in the CIP process. Analyzing the composition, microstructure, thermal, and mechanical properties of a material, as well as defect analysis, can help manufacturers select the right materials for their products and optimize their manufacturing processes to produce high-quality, defect-free materials.
Types of Isostatic Pressing
Isostatic pressing is a valuable manufacturing process that helps eliminate defects and produce high-quality materials used in a variety of industries. Isostatic pressing involves applying uniform pressure on a material using a fluid or gas, which results in the elimination of any defects such as porosity or cracks. There are two types of isostatic pressing: cold isostatic pressing (CIP) and hot isostatic pressing (HIP).
Cold Isostatic Pressing (CIP)
Cold isostatic pressing (CIP) involves applying pressure at room temperature. In CIP, a uniform hydrostatic pressure is applied to the powder closed in a flexible rubber or plastic mold. The powder is filled in a shaped and flexible mold, sealed, and immersed in liquid in a high-pressure vessel. The liquid is pressurized, and the pressure is transmitted through the flexible wall of the mold to the powder, which results in compaction. Wet-bag isopressing coupled with 3D green machining is used to fabricate complex ceramic parts at very high quality. The benefits of CIP include higher packing uniformity than in uniaxial pressing. Pressures of up to 1000 GPa can be used, although the most common production units operate up to 200-300 MPa.
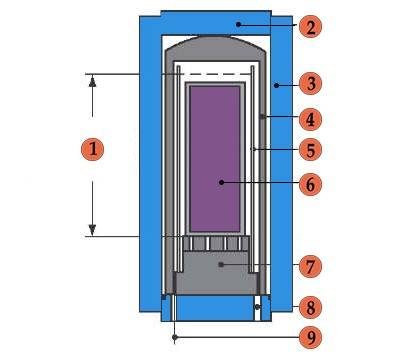
Hot Isostatic Pressing (HIP)
Hot isostatic pressing (HIP) involves applying pressure at high temperature, which allows for the elimination of not only defects but also any residual stresses in the material. HIP is a similar process carried out at high temperature. In HIP, the materials are heated to a high temperature and subjected to high pressure from all directions. This process is used to eliminate defects, such as cracks and porosity, that may have occurred during the manufacturing process. HIP can produce microstructure homogeneous, fine-grained, and completely dense materials at lower sintering temperatures and can produce products with complex shapes.
Comparison of CIP and HIP
Both types of isostatic pressing require specialized equipment, such as a high-pressure vessel and a pressure generator, to create the necessary pressure. While CIP is used for low-volume production of specialty parts, prototyping, and for research and development, HIP is used for high-volume production. CIP is limited by its flexible mold, which is not able to provide green bodies with the accurate dimensions that uniaxial pressing does. In contrast, HIP is able to produce parts with accurate dimensions and complex shapes. Both CIP and HIP have advantages and disadvantages, and the choice of which process to use depends on the specific application and production requirements.
In summary, isostatic pressing is a valuable manufacturing process that helps eliminate defects and produce high-quality materials used in a variety of industries. Cold isostatic pressing (CIP) involves applying pressure at room temperature, while hot isostatic pressing (HIP) involves applying pressure at high temperature. Both types of isostatic pressing require specialized equipment and have advantages and disadvantages. The choice of which process to use depends on the specific application and production requirements.
Applications of Isostatic Pressing
Isostatic pressing is a versatile process that can be used to produce a wide range of materials with varying properties. It offers several advantages over other manufacturing processes, including the ability to produce complex shapes, high precision, and the ability to produce components with a high degree of uniformity. Here are some common applications of isostatic pressing:
Ceramics
Isostatic pressing is widely used in the production of ceramics. It is used to produce high-density components that are used in a variety of applications, such as cutting tools, biomedical implants, and electronic components. The process helps to eliminate defects in the material, such as air pockets or voids, which can weaken the material and reduce its performance.
Metals
The process is also used in the production of metals, where it is used to produce components that are used in aerospace, automotive, and medical applications. Isostatic pressing helps to ensure that the material is compressed uniformly, which helps to eliminate defects and improve the performance of the final product.
Composites
Isostatic pressing is also used in the production of composite materials. It is used to ensure that the fibers are uniformly distributed throughout the material, which helps to improve the strength and performance of the final product. This process is commonly used to produce composites used in aerospace, automotive, and sporting goods applications.
Powder Metallurgy
Isostatic pressing is used in the production of powder metallurgy components. The process is used to produce high-density components with a high degree of uniformity. It is commonly used to produce components used in automotive and aerospace applications, such as gears, bearings, and turbine blades.
Medical Implants
Isostatic pressing is used in the manufacture of medical implants. The process is used to produce high-density components with a high degree of uniformity. Medical implants made using isostatic pressing are commonly used in orthopedic and dental applications.
Nuclear Industry
Isostatic pressing is used in the nuclear industry to produce components used in nuclear reactors. The process is used to produce high-density components with a high degree of uniformity. These components must be able to withstand extreme temperatures and radiation levels, making isostatic pressing an ideal manufacturing process.
In conclusion, isostatic pressing is a versatile manufacturing process that is used in a wide range of industries. It offers several advantages over other manufacturing processes, including the ability to produce complex shapes, high precision, and the ability to produce components with a high degree of uniformity. The applications of isostatic pressing are varied, from ceramics and metals to composites, powder metallurgy, medical implants, and the nuclear industry.
Conclusion
Isostatic pressing has proven to be an effective method for eliminating defects in materials. By subjecting materials to high pressure, isostatic presses can help to compact and consolidate powders, remove porosity and improve material density. The process can be carried out using either hot or cold isostatic pressing, depending on the material and desired outcome. Isostatic pressing is widely used in a range of industries, including aerospace, automotive, medical, and energy. Material characterization is an important aspect of the process, as it allows for the selection of the appropriate isostatic pressing method. With its many benefits, isostatic pressing is a valuable tool for producing high-quality materials with few defects.
CONTACT US FOR A FREE CONSULTATION
KINTEK LAB SOLUTION's products and services have been recognized by customers around the world. Our staff will be happy to assist with any inquiry you might have. Contact us for a free consultation and talk to a product specialist to find the most suitable solution for your application needs!