Introduction to Heated Lab Presses: Unveiling a Versatile Tool
In the realm of scientific research and industrial processes, heated lab presses emerge as versatile tools that play a pivotal role in shaping materials and transforming substances. These remarkable machines employ heat and pressure to mold, compact, and analyze samples, paving the way for groundbreaking discoveries and advancements in diverse fields. From sample preparation and material testing to polymer film production and pill manufacturing, heated lab presses leave an indelible mark on the world of science and industry. Delve into this comprehensive guide to unravel the intricacies of heated lab presses, uncovering their applications, advantages, and essential considerations for selecting the ideal press for your specific requirements.
Exploring Applications of Heated Lab Presses: A Journey Through Diverse Fields
Heated lab presses have become indispensable tools in a wide spectrum of industries and research domains, offering precise temperature control and uniform pressure distribution for various applications. Their versatility extends across fields such as infrared spectroscopy, XRF spectroscopy, polymer film preparation, pill making, and laminating.
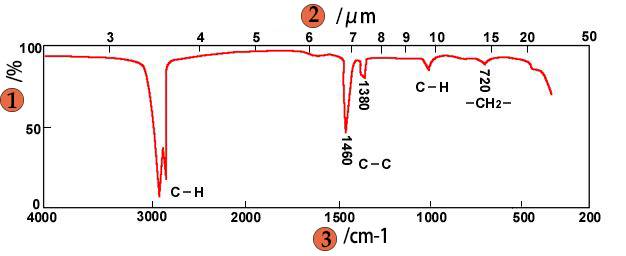
- Infrared Spectroscopy:
- Heated lab presses play a crucial role in preparing samples for infrared (IR) spectroscopy, a technique used to analyze the molecular structure of compounds.
- By applying pressure and heat, the press consolidates powdered samples into thin, transparent films or pellets, enabling the transmission of infrared radiation through the sample.
- This process, known as pellet pressing, enhances the signal-to-noise ratio and improves the accuracy of IR spectra, facilitating the identification and characterization of functional groups and molecular bonds.
- XRF Spectroscopy:
- Heated lab presses are employed in X-ray fluorescence (XRF) spectroscopy, a non-destructive analytical technique used to determine the elemental composition of materials.
- In XRF analysis, samples are often pressed into pellets or briquettes to ensure a uniform and consistent surface for X-ray irradiation.
- The application of heat and pressure during pellet preparation promotes better sample homogeneity, reduces particle scattering, and enhances the accuracy and sensitivity of XRF measurements.
- Polymer Film Preparation:
- Heated lab presses are essential in the preparation of thin polymer films for various applications, including transmission IR spectroscopy, mechanical testing, and packaging.
- By applying controlled heat and pressure, the press consolidates polymer materials into thin, uniform films with desired properties, such as thickness, density, and crystallinity.
- This process enables the study of polymer structure, properties, and behavior under different conditions.
- Pill Making:
- Heated lab presses are widely used in the pharmaceutical industry for the production of tablets and pills.
- The press compresses powdered drug substances and excipients into solid dosage forms, ensuring uniform drug distribution, accurate dosage, and consistent release properties.
- The application of heat and pressure during tableting improves the compaction and bonding of particles, resulting in tablets with high mechanical strength and stability.
- Laminating:
- Heated lab presses are employed in laminating processes, where multiple layers of materials, such as paper, plastic, or metal, are bonded together under heat and pressure.
- This process creates composite materials with enhanced properties, such as increased strength, durability, and resistance to moisture and chemicals.
- Laminating is widely used in various industries, including packaging, printing, and construction.
With their ability to precisely control temperature and pressure, heated lab presses have become indispensable tools in diverse fields, enabling researchers and industries to perform a wide range of applications with accuracy, efficiency, and reliability.
Benefits of Utilizing Heated Lab Presses: Uncovering the Advantages
Heated lab presses have become indispensable tools in various industries, including pharmaceutical, laminating, rubber and plastic molding, and R&D work. Their unique capabilities and advantages make them ideal for testing, short runs, limited production, cell manufacturing, and lean manufacturing.
Enhanced Heating Efficiency:
Heated lab presses employ specifically designed flat heating elements to ensure uniform temperature distribution over the platen surface. This precise heating mechanism allows for efficient and consistent heating of the workpiece, resulting in optimized processing times and improved product quality.
Improved Workpiece Quality:
The uniform temperature distribution achieved by heated lab presses ensures consistent thickness and closure force of the sample, leading to enhanced workpiece quality. The precise control of temperature and pressure enables the production of high-quality products with repeatable characteristics.
Reduced Heat Generation:
Heated lab presses minimize heat generation during the pressing process, reducing energy consumption and promoting a safer working environment. This energy efficiency also contributes to cost savings and a more sustainable laboratory operation.
Environmental Friendliness:
Heated lab presses adhere to strict environmental standards, minimizing emissions and ensuring hygiene and safety. Their eco-friendly design aligns with the growing emphasis on environmental protection and sustainability in modern manufacturing practices.
Factors to Consider When Purchasing a Lab Press: A Buyer's Guide
Selecting the right laboratory press is crucial for delivering accurate and reliable results in various applications. Several key factors must be carefully considered to ensure you make an informed purchasing decision.
1. Pressure Requirements
The pressure capacity of a lab press is a primary consideration. Different applications demand different pressure levels to effectively mold or compress materials. Presses typically generate pressure ranging from 15 tons to over 100 tons. Evaluate the specific pressure requirements of your intended experiments or processes to choose a press that meets or exceeds those needs.
2. Temperature Range
The temperature range of a lab press is another critical factor to consider. The desired temperature range depends on the materials being processed and the specific application. Presses typically offer temperature ranges from 600°F to 1200°F. Ensure the press you select can achieve and maintain the desired temperature accurately.
3. Platen Size
Platen size is another important consideration. The platens are the heated surfaces that apply pressure to the material being processed. The size of the platens determines the maximum sample size that can be accommodated. Consider the dimensions of your samples and choose a press with platens large enough to handle them comfortably.
4. Computer Control Options
Computer control options can greatly enhance the functionality and ease of use of a lab press. Advanced presses may offer computer control features that allow for precise temperature and pressure programming, data logging, and automated operation. If these features are desirable for your application, ensure the press you select has the desired level of computer control capabilities.
5. Temperature Hold Time
The temperature hold time refers to the duration for which the press can maintain a specific temperature. This factor is crucial for processes that require precise temperature control over an extended period. Determine the required temperature hold time for your application and choose a press that can maintain the desired temperature accurately for the necessary duration.
6. Temperature Control Precision
Temperature control precision is another important consideration. The precision of the temperature control system determines how accurately the press can maintain the desired temperature. Higher precision is essential for applications that demand tight temperature tolerances. Evaluate the temperature control precision specifications of the press to ensure it meets your requirements.
7. Benchtop vs. Floor Press Suitability
Lab presses are available in two primary configurations: benchtop and floor models. Benchtop presses are compact and designed to be placed on a laboratory bench or countertop. Floor presses are larger and more powerful units that are typically installed on the floor. Consider the available space in your laboratory and the size and weight of the samples you will be processing to determine whether a benchtop or floor press is more suitable for your needs.
Maintenance Tips for Heated Lab Presses: Ensuring Optimal Performance
Heated lab presses are essential equipment in various scientific and industrial applications, offering precise and consistent results for testing and compacting materials. To maintain optimal performance and longevity of these presses, regular maintenance is crucial. Here are some key maintenance tips to follow:
1. Regular Inspection:
- Conduct thorough inspections of the press before each use to identify any potential issues.
- Check for leaks in hoses, seals, and fittings to prevent fluid loss and contamination.
- Inspect the heating plates for cracks, damage, or warping that could affect temperature uniformity.
- Monitor the hydraulic system for leaks, ensuring proper fluid levels and pressure.
- Listen for unusual noises or excessive vibration during operation, which may indicate mechanical problems.
2. Cleaning and Maintenance of Working Parts:
- Keep the working parts of the press clean and free from dirt, dust, and debris to prevent wear and tear.
- Regularly clean the heating plates using appropriate cleaning agents to remove any residue or contamination.
- Inspect and clean the pressure gauges, valves, and other components to ensure accurate readings and proper functioning.
- Lubricate moving parts, such as bearings and guides, according to the manufacturer's recommendations to minimize friction and extend their lifespan.
3. Proper Lubrication:
- Ensure proper lubrication of the press's mechanical components to reduce wear and tear and prevent premature failure.
- Use the recommended lubricants specified by the manufacturer to ensure compatibility and optimal performance.
- Regularly check the lubrication levels and replenish as needed to maintain adequate lubrication.
- Avoid over-lubrication, as excess lubricant can attract dirt and contaminants, potentially causing more harm than good.
4. Hydraulic Fluid Maintenance:
- Over time, the hydraulic fluid in the press may degrade due to heat, contamination, or extended use.
- Regularly check the condition of the hydraulic fluid, monitoring its color, viscosity, and cleanliness.
- Replace the hydraulic fluid as recommended by the manufacturer or when it shows signs of deterioration.
- Use the appropriate type and grade of hydraulic fluid specified by the manufacturer to ensure optimal performance and longevity.
5. Electrical System Maintenance:
- Inspect the electrical components of the press, including wiring, connections, and controls, for any signs of damage or wear.
- Ensure proper grounding of the press to prevent electrical hazards.
- Regularly clean electrical contacts and terminals to maintain good conductivity and prevent corrosion.
- Have a qualified electrician perform periodic inspections and maintenance of the electrical system to ensure its safety and reliability.
By following these maintenance tips, you can keep your heated lab press in optimal working condition, ensuring accurate and reliable results, extending its lifespan, and minimizing downtime. Regular maintenance also helps prevent costly repairs and ensures the safety of users and the surrounding environment.
Advantages of Hot Pressing: Unveiling the Edge
Hot pressing, a versatile manufacturing technique, offers a plethora of advantages that set it apart from other fabrication methods. Its unique attributes make it a preferred choice for producing high-quality materials and components across diverse industries. Let's delve into the key benefits of hot pressing:
1. Low Equipment Investment:
Hot pressing stands out with its cost-effectiveness. The initial investment required for hot pressing equipment is significantly lower compared to other pressing techniques, such as isostatic pressing. This economic advantage makes it an attractive option for manufacturers seeking to optimize their capital expenditures.
2. Improved Temperature Field Uniformity:
Hot pressing excels in achieving superior temperature field uniformity within the workpiece. The pressure-bearing material used in hot pressing can be refined to minimize longitudinal heat flow, resulting in a more evenly distributed temperature throughout the material. This uniformity is crucial for ensuring consistent material properties and reducing the risk of defects.
3. Reduced Energy Consumption:
Hot pressing offers substantial energy savings compared to alternative pressing methods. By limiting the longitudinal heat flow, hot pressing reduces the energy required to achieve the desired temperature and pressure conditions. This energy efficiency translates into lower operating costs and a reduced environmental footprint.
4. Ability to Prepare Large Diameter Materials:
Hot pressing is capable of processing large diameter materials, making it suitable for applications that require substantial material dimensions. This versatility expands the range of materials and components that can be manufactured using hot pressing technology.
5. IT Control for Effective Process and Quality Management:
Hot pressing machines can be integrated with IT technology, enabling precise control over the densification process and quality of the materials. This level of automation ensures consistent and repeatable results, minimizing the risk of defects and enhancing overall production efficiency.
In summary, hot pressing offers a compelling combination of advantages, including low equipment investment, improved temperature field uniformity, reduced energy consumption, the ability to prepare large diameter materials, and IT control for effective process and quality management. These benefits make hot pressing a highly attractive technique for a wide range of manufacturing applications.
Guide to Purchasing Presses: A Comprehensive Overview
Laboratory presses are versatile and powerful tools used in various industries and research institutions for sample preparation, testing, and manufacturing. Understanding the specific requirements of your application is crucial when selecting a laboratory press. This guide provides a comprehensive overview of the key factors to consider when purchasing a press, ensuring you make an informed decision that meets your needs.
1. Applications and Materials:
Laboratory presses are commonly employed in a wide range of industries and materials, including rubbers, polymers, composites, ceramics, wood, thermoplastic resins, textiles, laminating, and pharmaceutical applications. They are also suitable for short production runs and lean manufacturing, as well as educational and research purposes.
2. Pressure and Temperature Capabilities:
The pressure and temperature capabilities of a laboratory press are critical considerations. Presses come with varying pressure capacities, typically ranging from a few tons to hundreds of tons, and temperature capabilities that can reach up to several hundred degrees Celsius. Ensure that the press you choose meets or exceeds the pressure and temperature requirements of your intended applications.
3. Platen Size Options:
Laboratory presses feature different platen sizes to accommodate various sample dimensions. Platen sizes are typically measured in inches or millimeters, and the choice depends on the size of the samples you will be working with. Larger platens provide more flexibility for accommodating larger samples, while smaller platens are suitable for smaller samples or applications where space is limited.
4. Control Features:
Modern laboratory presses incorporate advanced control features that enable precise and accurate operation. These features may include programmable controls, digital displays, temperature controllers, pressure gauges, and data logging capabilities. The level of control required depends on the specific application and the desired level of precision and accuracy.
5. Maintenance and Safety Considerations:
Laboratory presses require regular maintenance to ensure optimal performance and safety. Regularly inspect the press for leaking hoses, seals, cracks, and excessive vibration. Keep the working parts clean and properly lubricated. Over time, the hydraulic fluids may need replacement. Ensure that the proper hydraulic oil is used when replacing.
By carefully considering these factors, you can select a laboratory press that meets your specific requirements and ensures efficient and reliable operation.
Conclusion: Embracing the Power of Heated Lab Presses
Heated lab presses have revolutionized various scientific and industrial processes with their ability to apply controlled pressure and temperature to materials. From sample preparation and material testing to polymer film production and pill making, these versatile tools have become indispensable in numerous fields. Their advantages, such as enhanced heating efficiency, improved workpiece quality, and reduced heat generation, make them a preferred choice for researchers and manufacturers alike. When selecting a heated lab press, factors like pressure requirements, temperature range, platen size, and control options should be carefully considered to ensure optimal performance. With proper maintenance and adherence to safety guidelines, heated lab presses can deliver accurate and reliable results for years to come. Embracing the power of heated lab presses empowers researchers and manufacturers to explore new possibilities and achieve remarkable outcomes in their respective domains.
CONTACT US FOR A FREE CONSULTATION
KINTEK LAB SOLUTION's products and services have been recognized by customers around the world. Our staff will be happy to assist with any inquiry you might have. Contact us for a free consultation and talk to a product specialist to find the most suitable solution for your application needs!