Introduction
Table of Contents
- Introduction
- KinTek's WIP Design and Applications
- Designing and building Warm Isostatic Presses
- Gas or liquid pressurized systems
- Use for plastics and laminated products
- Custom-built WIP systems for various pressure levels
- Temperature ranges for liquid and gas WIP systems
- Collaboration with companies for molding and technology development
- Availability of testing for interested parties
- Features of WIP Equipment
- Benefits of WIP Equipment over General Press Machine
- Conclusion
Welcome to our blog post on Warm Isostatic Press Equipment (WIP). If you're in the manufacturing industry, specifically dealing with plastics and laminated products, then you're in the right place. WIP is a game-changer when it comes to applying artificial pressure for various applications. In this article, we'll dive into the design, features, and benefits of WIP equipment. Whether you're looking for superior temperature uniformity performance or high densification with low density variation, WIP has got you covered. So, let's explore this innovative technology and how it can revolutionize your production processes.
KinTek's WIP Design and Applications
Designing and building Warm Isostatic Presses
KinTek specializes in designing and building Warm Isostatic Presses (WIP) for various applications. These systems can be either gas or liquid pressurized and are commonly used for plastics and laminated products. WIPs are custom-built to accommodate different pressure levels, ranging from low pressure to extreme pressures.
Gas or liquid pressurized systems
WIP systems can be pressurized using either gas or liquid. Liquid WIP systems have a temperature range of up to 250°C, while gas WIP systems can reach temperatures up to 500°C. Both cold and hot wall versions of WIP systems are available.
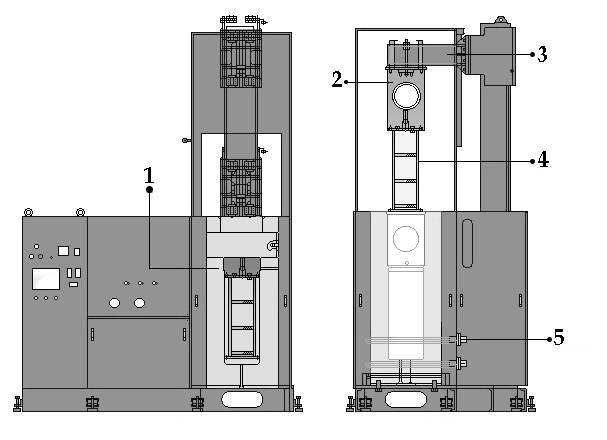
Use for plastics and laminated products
The main applications of WIP systems include the production of plastics and laminated products. WIP can be used for hybrid chips, MLCC lamination, Bluetooth components, fuel cells, medical electronics, multilayer PZTs, LTCCs (Low Temperature Cofired Ceramics), varistors, and other laminated electronic components.
Custom-built WIP systems for various pressure levels
KinTek offers custom-built WIP systems to meet the specific pressure requirements of different applications. These systems can be tailored to accommodate different pressure levels, ensuring optimal performance and efficiency.
Temperature ranges for liquid and gas WIP systems
Liquid WIP systems have a temperature range of up to 250°C, while gas WIP systems can reach temperatures up to 500°C. This wide temperature range allows for the processing of various materials and applications.
Collaboration with companies for molding and technology development
KinTek has collaborated with many companies to develop the molding and technologies required to make the WIP process cost-effective and efficient. This collaboration ensures that KinTek's WIP systems meet the specific needs and requirements of different industries.
Availability of testing for interested parties
KinTek offers testing services to interested parties. This allows potential customers to evaluate the performance and capabilities of the WIP systems before making a purchase. The testing services provided by KinTek ensure that customers can make informed decisions based on accurate and reliable data.
In conclusion, KinTek's WIP systems are designed and built for various applications, including plastics and laminated products. These custom-built systems can be pressurized using either gas or liquid and offer a wide temperature range. With collaboration opportunities and testing services available, KinTek ensures that its WIP systems meet the specific needs and requirements of different industries.
Features of WIP Equipment
Suitability for applications requiring artificial pressure
WIP equipment is designed for various applications that require artificial pressure. It can be customized to meet specific needs and functions. This makes it versatile and adaptable for different industries and processes.
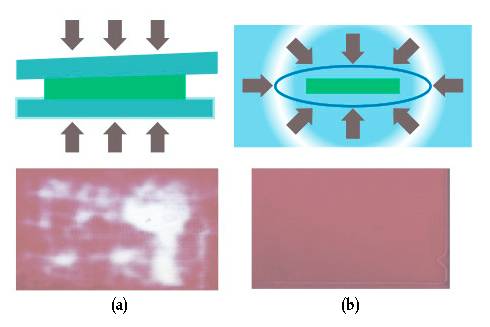
Custom mode for special functions
With a custom mode feature, WIP equipment can be tailored to perform special functions as required by specific applications. This allows for flexibility and optimization of the equipment's capabilities.
Use of water or oil thermal fluid in production
WIP systems for production purposes utilize either water or oil thermal fluid. These fluids are heated using an external circulation heater, ensuring efficient and controlled heating for the desired process.
Heating through external circulation heater
The heating process in WIP equipment is facilitated by an external circulation heater. This allows for precise temperature control and uniform heating throughout the equipment, ensuring optimal results in the production process.
Touch screen with computer-based graphical operation
WIP equipment is equipped with a touch screen interface that provides a user-friendly experience. The touch screen allows for easy operation and control of the equipment, with a graphical display of all technological parameters of the heat treatment processes.
Standard interface
WIP equipment is designed with a standard interface that allows for easy integration with other systems and databases. This ensures seamless communication and compatibility with external systems for data analysis and further processing.
The features of WIP equipment make it a reliable and efficient tool for various applications that require artificial pressure. Its suitability for different functions, use of thermal fluids, precise heating capabilities, user-friendly touch screen interface, and standard interface for integration make it a valuable asset in industries such as semiconductor, electronic components, pharmaceuticals, and more.
Benefits of WIP Equipment over General Press Machine
Superior temperature uniformity performance
WIP equipment offers excellent temperature uniformity performance compared to general press machines. This means that the equipment can maintain a consistent and uniform temperature throughout the pressing process. This is crucial for achieving precise and consistent results in the final product. With superior temperature uniformity performance, WIP equipment ensures that every part is pressed at the desired temperature, resulting in high-quality and reliable outcomes.
Processing in dry state
One of the key advantages of WIP equipment is the ability to process materials in a dry state. Unlike general press machines that may require the use of water, lubricants, or binders, WIP equipment allows for dry isostatic pressing. This not only eliminates the need for additional materials but also offers greater flexibility in processing different types of materials. Dry processing in WIP equipment is particularly beneficial for difficult-to-press materials and offers increased possibilities for machining the compact in its green state.
High strength and accuracy
WIP equipment excels in terms of strength and accuracy. The equipment is designed to provide excellent compaction of the powder, leading to improved densification of the final product. This results in higher strength and accuracy of the pressed parts. With WIP equipment, manufacturers can achieve precise dimensions and greater homogeneity in the finished products. The high strength and accuracy of WIP equipment make it an ideal choice for industries that require reliable and high-quality components.
High densification, low density variation, and uniformity
WIP equipment offers high densification of the pressed parts, resulting in improved density and uniformity. The equipment ensures that the powder is compacted efficiently, leading to a more uniform and consistent density throughout the product. This is crucial for industries that require products with predictable compression during subsequent processes like sintering. WIP equipment also allows for the production of parts with low density variation, ensuring consistent quality across all components.
In conclusion, WIP equipment provides several advantages over general press machines. Its superior temperature uniformity performance, ability to process materials in a dry state, high strength and accuracy, and high densification with low density variation and uniformity make it a preferred choice for industries that require reliable and high-quality components. Additionally, WIP equipment offers increased flexibility in shape and size of the finished products, longer aspect ratios, and improved productivity. With these benefits, WIP equipment is a valuable investment for companies looking to achieve consistent and precise results in their manufacturing processes.
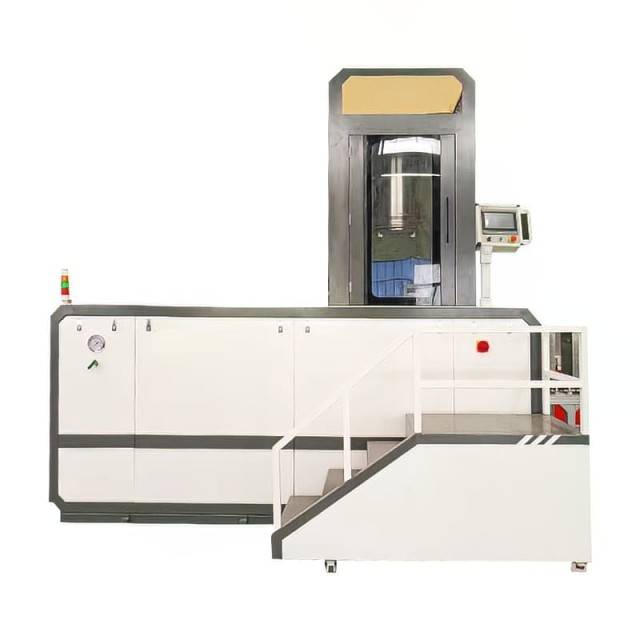
Conclusion
In conclusion, the Warm Isostatic Press (WIP) equipment offered by KinTek provides a range of benefits and features that make it a superior choice over general press machines. With its superior temperature uniformity performance, WIP ensures consistent and high-quality results. The ability to process in a dry state eliminates the need for additional drying processes, saving time and resources. The high strength and accuracy of WIP equipment ensure precise and reliable manufacturing. Additionally, the high densification, low density variation, and uniformity achieved with WIP equipment contribute to the production of high-quality products. Overall, investing in WIP equipment can greatly enhance productivity and efficiency in various industries.
If you are interested in our products, please visit our company website: https://kindle-tech.com/product-categories/isostatic-press, where innovation has always been a priority. Our R&D team consists of experienced engineers and scientists who closely follow industry trends and are constantly pushing the boundaries of what is possible. Our laboratory equipment incorporates the latest technology to ensure that you can obtain accurate and repeatable results during your experiments. From high-precision instruments to intelligent control systems, our products will provide you with unlimited possibilities for your experimental work.
CONTACT US FOR A FREE CONSULTATION
KINTEK LAB SOLUTION's products and services have been recognized by customers around the world. Our staff will be happy to assist with any inquiry you might have. Contact us for a free consultation and talk to a product specialist to find the most suitable solution for your application needs!