Understanding Tube Furnaces: An Overview
Tube furnaces are versatile laboratory equipment used in various industries, including materials research, chemistry, and nanotechnology. They consist of a cylindrical chamber surrounded by heating elements, allowing for rapid heating, recovery, and cooling.
Applications of Tube Furnaces:
Vertical Tube Furnaces:
- Thermal decomposition
- Pyrolysis
- Chemical vapor deposition (CVD)
- Annealing of materials
Horizontal Tube Furnaces:
- Heat treatment
- Sintering
- Annealing
- Thermal analysis
Advantages of Tube Furnaces:
Vertical Tube Furnaces:
- Convenient loading and unloading of samples
- Excellent temperature uniformity along the tube length
- Compact footprint
Horizontal Tube Furnaces:
- Larger working volume for processing larger samples
- Flexibility in sample loading and unloading
- Uniform heat distribution along the sample
Tube furnaces are essential for precise temperature control and uniform heating of samples. Their versatility makes them suitable for a wide range of applications in various industries, including:
- Materials science
- Metallurgy
- Ceramics
- Chemical synthesis
- Curing ceramics
- Materials science engineering
- Food science
- Geological research
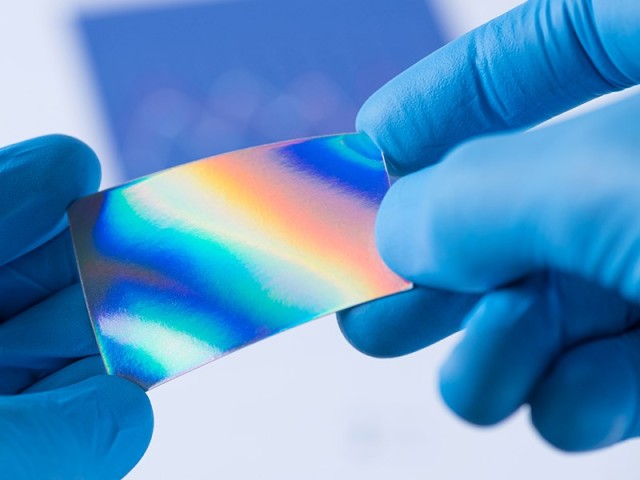
Types of Tube Furnaces
Tube furnaces are versatile laboratory equipment used for various thermal processes, including inorganic and organic purification, accelerated aging, annealing, coating, drying, and more. They come in various configurations to suit specific application requirements. Here are the main types of tube furnaces:
Single-Zone, Dual-Zone, and Multiple-Zone Furnaces
Tube furnaces can have different temperature control zones, allowing for precise temperature profiles along the tube. Single-zone furnaces have a single heating zone, while dual-zone furnaces have two independently controlled zones. Multiple-zone furnaces offer even more control, with three or more independently controlled zones. The number of zones required depends on the application and the desired temperature gradient.
Horizontal and Vertical Mounting Options
Tube furnaces can be mounted horizontally or vertically. Horizontal furnaces are typically used for long samples or processes that require a specific orientation. Vertical furnaces are more compact and are often used for smaller samples or processes that do not require a specific orientation.
Temperature Ranges and Capabilities
Tube furnaces have different temperature ranges and capabilities depending on the application. Some furnaces can reach temperatures up to 1800°C, while others are limited to lower temperatures. The temperature range of a furnace is determined by the heating elements and the construction materials used.
Specific Types of Tube Furnaces
In addition to the general categories mentioned above, there are also specific types of tube furnaces designed for particular applications. These include:
- Split Tube Furnaces: Split tube furnaces have a hinged body that opens in half for easy access to the inner chamber. They are ideal for applications where frequent sample changes or maintenance is required.
- Solid Tube Furnaces: Solid tube furnaces have a stationary heated cylinder with a process tube passing through it. They are suitable for applications where repetitive samples are processed in bulk.
- Rotary Tube Furnaces: Rotary tube furnaces rotate the process tube during heating, ensuring uniform temperature distribution and preventing sample agglomeration.
- Vertical and Cylindrical Tubular Furnaces: These furnaces have a vertical cylindrical chamber and are used for a variety of applications, including heat treatment, annealing, and sintering.
The choice of the most suitable tube furnace depends on the specific application requirements, including the desired temperature range, sample size and shape, mounting orientation, and process requirements.
Specific Models and Their Applications
Rotary Tube Furnace for Continuous Processes
Rotary tube furnaces are specifically designed for continuous material processing. These furnaces employ multiple thermal control zones to heat the sample as it progresses through the rotating tube. The heat is effectively transferred from the heat source to the rotating tube containing the material being processed.
Applications of Rotary Tube Furnaces:
Rotary tube furnaces find applications in a diverse range of industries, including materials research, chemistry, and nanotechnology. They are commonly used for:
- Production of various materials, such as alumina, vermiculite, iron ore pellets, and cement clinker
- Oxidation processes, involving the addition of oxygen and loss of electrons in the sample
- Roasting processes, used to induce phase transitions
Split Tube Furnace for Accessibility and Versatility
Split tube furnaces offer exceptional accessibility and versatility for various laboratory applications. The split design allows for easy sample insertion and removal, making them ideal for batch processing. These furnaces typically have a capacity ranging from 620 to 2320 ml, depending on the model.
Vertical & Cylindrical Tubular Furnace for Specialized Applications
Vertical tube furnaces are widely employed in industries such as materials research, chemistry, and nanotechnology. These furnaces excel in processes such as thermal decomposition, pyrolysis, chemical vapor deposition (CVD), and annealing of materials. They offer precise temperature control and uniform heating of long or vertically aligned samples.
Advantages of Vertical Tube Furnaces:
- Convenient sample loading and unloading due to their vertical design
- Consistent and reliable outcomes due to excellent temperature uniformity along the tube's length
- Compact footprint, making them suitable for laboratories with limited space
Industrial Applications of Tube Furnaces
Tube furnaces are widely employed in various industries, including materials research, chemistry, and nanotechnology. They are particularly suitable for processes requiring precise temperature control and uniform heating of long or vertically aligned samples.
Annealing, Brazing, Calcining, and Other Industrial Processes
In industrial settings, tube furnaces are utilized for a diverse range of processes, including:
-
Annealing: This process involves heating and cooling materials to alter their physical properties, such as hardness, strength, and ductility. Tube furnaces are ideal for annealing long or vertically oriented samples, such as wires, rods, and tubes.
-
Brazing: This technique joins metal components using a filler metal that melts at a lower temperature than the base metals. Tube furnaces provide the precise temperature control necessary for successful brazing.
-
Calcining: This process involves heating materials to drive off volatile components, such as water or carbon dioxide. Tube furnaces are commonly used for calcining powders, minerals, and other materials.
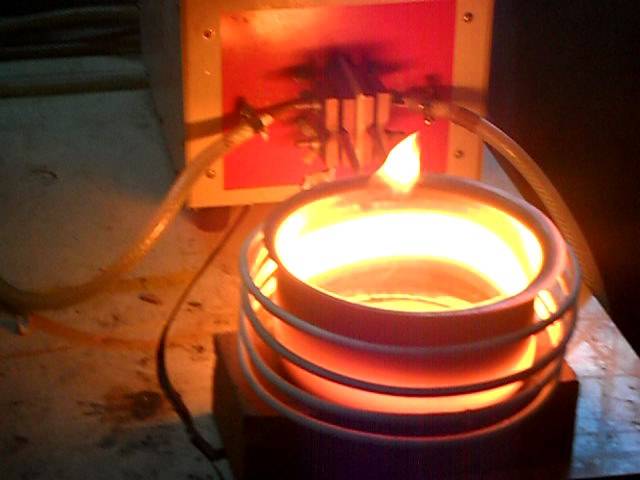
Advantages of Tube Furnaces in Various Industries
Tube furnaces offer several advantages that make them well-suited for industrial applications:
-
Precise Temperature Control: Tube furnaces provide accurate and consistent temperature control, which is crucial for many industrial processes.
-
Uniform Heating: The vertical design of tube furnaces ensures uniform heating along the length of the sample, resulting in consistent and reliable outcomes.
-
Compact Footprint: Tube furnaces have a compact footprint, making them suitable for laboratories with limited space.
-
Vertical Design: The vertical design simplifies sample loading and unloading, making batch processing convenient.
-
High Temperature Capability: Tube furnaces can operate at high temperatures, up to 1800°C, making them suitable for a wide range of industrial processes.
-
Shorter Melting Time: Tube furnaces offer rapid heating and cooling rates, reducing the processing time for various applications.
-
Low Volume of Flue Gases: Tube furnaces produce a low volume of flue gases, minimizing environmental impact and ensuring a clean working environment.
In summary, tube furnaces are versatile and efficient heating devices that find applications in a wide range of industries. Their precise temperature control, uniform heating, compact footprint, and high-temperature capability make them an essential tool for various industrial processes.
Factors to Consider When Using Tube Furnaces
Tube furnaces are laboratory equipment used for high-temperature processing of materials. They offer precise temperature control and uniformity, making them ideal for applications such as thermocouple calibration and material testing. When selecting and using tube furnaces, several key factors need to be considered:
Temperature Control and Uniformity:
Tube furnaces utilize cylindrical heaters that provide unrivaled thermal uniformity. Parts placed within the furnace chamber are consistently heated to temperatures exceeding 1000°C (1832°F) over the entire 360° axis. This uniform heat distribution ensures optimal processing results and minimizes thermal gradients.
Atmosphere Control and Gas Flow:
Tube furnaces allow for precise control of the atmosphere within the heating chamber. Inert gases, such as nitrogen or argon, can be introduced to create a non-oxidizing environment. Gas flow rates and compositions can be adjusted to meet specific process requirements. The ability to control the atmosphere is crucial for preventing oxidation and ensuring the purity of processed materials.
Safety Precautions and Maintenance:
Tube furnaces operate at high temperatures, posing potential safety hazards. Proper precautions must be taken to ensure safe operation. These include:
- Using appropriate protective gear, such as gloves and safety glasses
- Ensuring proper ventilation to remove potentially hazardous fumes
- Regularly inspecting and maintaining the furnace to identify and address any potential issues
- Following manufacturer's instructions for operation and maintenance
Additional Considerations:
- Tube Selection: The choice of tube material depends on the specific application and temperature requirements. Alloy tubing is suitable for larger diameters and lower temperatures, while ceramic tubing is preferred for high-temperature processing. Quartz tubing is impermeable but has limited temperature resistance.
- Process Parameters: Factors such as rotational speed, material quantity, tube diameter, hanging length, and tube thickness should be considered when configuring the furnace for a specific process.
- Environmental Conditions: Tube furnaces should be operated in controlled environments with low humidity and temperature to ensure optimal performance and longevity.
- Safety Measures: Routine maintenance and inspections are essential to maintain the furnace's safety and reliability. Proper handling and storage of materials are crucial to prevent accidents.
Advanced Features and Innovations
Amidst the advanced laboratory equipment landscape, innovative features and technologies play a vital role in enhancing efficiency, accuracy, and ease of operation. Our products are equipped with cutting-edge advancements that redefine the laboratory experience.
Intelligent One-Button Operation: Experience unparalleled ease of use with our intuitive one-button operation. The simplified interface allows you to initiate complex processes with a single touch, minimizing the learning curve and maximizing productivity.
Automated Temperature Profiling and Data Logging: Ensure precise temperature control and accurate data tracking with our automated temperature profiling and data logging capabilities. Monitor and record temperature parameters in real-time, enabling you to optimize heating cycles and achieve consistent results.
Integration with Other Lab Equipment: Seamlessly integrate our equipment with your existing laboratory setup. Advanced connectivity options allow for effortless communication with other devices, automating workflows and enhancing overall efficiency.
Additional Innovative Features:
- Multi-stage Temperature Rise Control: Precisely control temperature changes throughout the heating process, ensuring optimal conditions for various applications.
- Real-time Temperature Curve Display: Monitor temperature profiles in real-time, allowing for timely adjustments and enhanced process control.
- Silicone Belt Indexing Mechanism: Ensure accurate alignment and precise positioning of materials during processing.
- CCD Vision System: Utilize advanced CCD technology for precise alignment, reducing errors and improving overall efficiency.
- Large Capacity Program Pre-Storage: Store a wide range of programs for quick access, simplifying operation and minimizing downtime.
- Touch Operation Interface: Navigate through settings and control parameters effortlessly with our intuitive touch operation interface.
- Separate Temperature Control of Upper and Lower Templates: Maintain precise temperature distribution throughout the heating process, ensuring uniform results.
- Imported Intelligent Temperature Controller: Leverage advanced temperature control technology for accurate and consistent heating.
- Durable Components: Utilize high-quality components from renowned manufacturers, ensuring long-lasting performance and reliability.
- Simplified Oil Pressure Circuit: Minimize maintenance requirements and enhance operational efficiency with our simplified oil pressure circuit design.
- Safety Features: Prioritize safety with our comprehensive safety features, including two-hand start buttons, emergency rise switches, and safety hand gratings.
Conclusion
Tube furnaces offer a versatile and essential tool for a wide range of industries and laboratories. Their diverse types and applications make them invaluable for processes involving heat treatment, material synthesis, and research. Understanding the specific requirements and considerations for each application is crucial for optimal usage. By choosing the right tube furnace and adhering to proper operating procedures, users can effectively harness the power of these furnaces to achieve desired results.
CONTACT US FOR A FREE CONSULTATION
KINTEK LAB SOLUTION's products and services have been recognized by customers around the world. Our staff will be happy to assist with any inquiry you might have. Contact us for a free consultation and talk to a product specialist to find the most suitable solution for your application needs!