Understanding Hot Pressing
Table of Contents
Definition and process of hot pressing
Hot pressing is a high-pressure, low-strain-rate powder metallurgy process used to form powder or powder compact at high temperatures to induce sintering and creep processes. It involves the simultaneous application of heat and pressure to fabricate hard and brittle materials.
Primary usage and application
Hot pressing is mainly used in the consolidation of diamond-metal composite cutting tools, technical ceramics, and other hard and brittle materials. It works through particle rearrangement and plastic flow at the particle contacts. The loose powder or pre-compacted part is filled into a graphite mould, allowing for induction or resistance heating up to temperatures of typically 2,400 °C (4,350 °F). Pressures of up to 50 MPa (7,300 psi) can be applied. Hot pressing is also used in the pressing of different types of polymers.
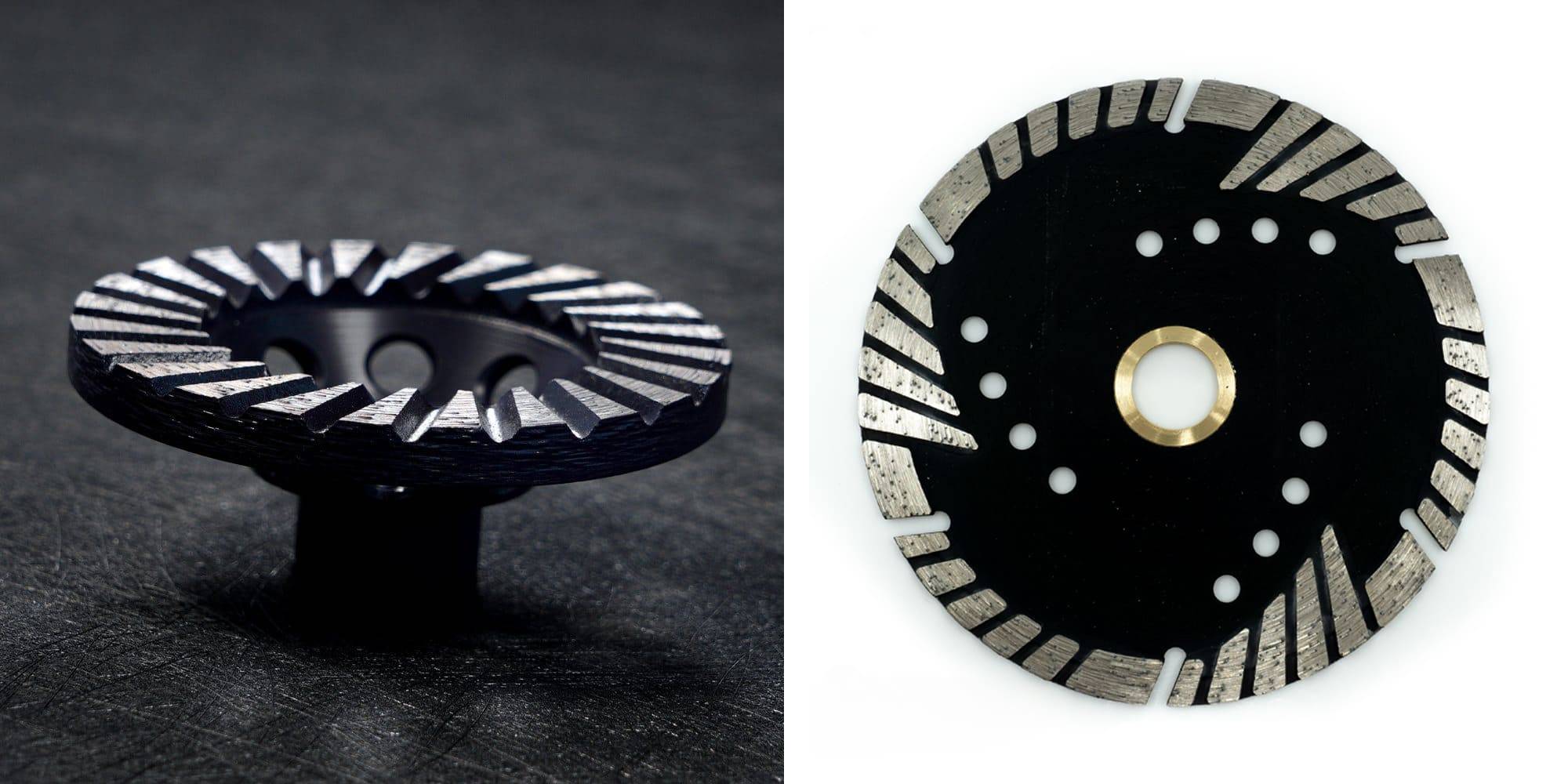
Hot pressed diamonds
Densification through particle rearrangement and plastic flow
The densification process in hot pressing occurs through particle rearrangement and plastic flow at the particle contacts. The external pressure applied during hot pressing causes the destruction of internal defects and pores, resulting in the internal surfaces coming into contact with each other. The material then undergoes high temperature creep, allowing for mutual penetration and diffusion bonding, completely eliminating defects and porosity.
Graphite mould usage and heating temperatures
In hot pressing, a graphite mould is commonly used to contain the loose powder or pre-compacted part. The graphite mould allows for efficient heating through induction or resistance heating. The temperatures used in hot pressing can reach up to 2,400 °C (4,350 °F), ensuring the sintering and creep processes necessary for densification.
Pressures involved in the process
Hot pressing involves the application of high pressures to achieve densification. Pressures of up to 50 MPa (7,300 psi) can be applied during the hot pressing process. The high pressure aids in particle rearrangement and plastic flow, resulting in a compact and dense final product.
Hot pressing in the polymer industry
Hot pressing is also widely used in the polymer industry. By using the hot pressing technique, manufacturers can eliminate the need for binders in their manufacturing process and instead use the combination of force and temperature to bond their parts completely. This allows for the production of high-quality polymer products with improved mechanical properties and dimensional accuracy.
In summary, hot pressing is a powder metallurgy process used to fabricate hard and brittle materials. It involves the application of heat and pressure to induce sintering and creep processes, resulting in densification. Hot pressing is widely used in various industries, including aerospace, ceramics, and polymer manufacturing. The process utilizes a graphite mould and can reach high temperatures and pressures to achieve the desired results.
Types of Heating in Hot Pressing
Introduction to three types of heating: induction heating, indirect resistance heating, and field-assisted sintering technique (FAST) / direct hot pressing
Hot pressing is a widely used technique in the manufacturing industry for creating durable and tight bonds between materials. It involves the combination of added force during the sintering of high-temperature materials, either in a vacuum or under a positive pressure of inert gas. This pressure aids in the increased densification of the material, resulting in a billet of material with densities close to theoretical.
There are two main types of hot press furnaces: those that use hot and cold rods for applying pressure and those that use graphite punches and dies or pressing platens to exert the force during diffusion bonding. These furnaces eliminate the need for binders in the manufacturing process, making them highly efficient.
Within hot pressing technology, there are three distinct types of heating methods used: induction heating, indirect resistance heating, and field-assisted sintering technique (FAST) / direct hot pressing.
Inductive Heating
Inductive heating is a commonly used method for the sintering of metal, ceramic, and some refractory metal intermetallic compound powder. It involves the use of electromagnetic induction to generate heat within the material.
In this process, an alternating current is passed through a coil, creating a magnetic field. This magnetic field induces eddy currents within the material, which in turn generate heat. The heat is then used to sinter the material and create the desired bond.
Inductive heating is known for its efficiency and precision. It allows for fast heating rates and precise control over temperature distribution, resulting in high-quality bonds. It is particularly suitable for materials that have high electrical conductivity.
Indirect Resistance Heating
Indirect resistance heating is another method commonly used in hot pressing. It involves the use of electrical resistance to generate heat within the material.
In this process, an electrical current is passed through the material, causing resistance and generating heat. The heat is then used to sinter the material and create the desired bond.
Indirect resistance heating is known for its simplicity and versatility. It can be used with a wide range of materials and is particularly suitable for materials that have low electrical conductivity. It allows for precise control over temperature and can achieve high heating rates.
Field-Assisted Sintering Technique (FAST) / Direct Hot Pressing
The field-assisted sintering technique (FAST), also known as direct hot pressing, is a relatively new method used in hot pressing. It involves the use of an electric field to aid in the sintering process.
In this process, an electric current is passed through the material, creating an electric field. This electric field enhances the mobility of the atoms within the material, allowing for accelerated sintering and densification.
FAST / direct hot pressing is known for its ability to produce highly dense and uniform materials. It allows for fast sintering rates and can achieve high densities close to theoretical. It is particularly suitable for materials that have low diffusivity and high electrical conductivity.
In conclusion, hot pressing is a valuable technique in the manufacturing industry for creating durable and tight bonds between materials. Within hot pressing technology, three types of heating methods are commonly used: induction heating, indirect resistance heating, and field-assisted sintering technique (FAST) / direct hot pressing. Each method has its own advantages and is suitable for different materials and applications.
Inductive Heating
Process and functioning of inductive heating
Inductive heating is the process of heating electrically conductive materials, such as metals or semi-conductors, using electromagnetic induction. This is achieved by passing a high-frequency alternating current through an electromagnet, creating a rapidly alternating magnetic field. This magnetic field induces eddy currents within the material, which flow through its resistance and generate heat by Joule heating. In ferromagnetic and ferrimagnetic materials, heat is also generated by magnetic hysteresis losses. The frequency of the electric current used depends on factors such as the size and material of the object, coupling between the work coil and the object, and the penetration depth.
This heating method is commonly used for melting metals and making alloys. Vacuum induction melting, which combines controlled atmosphere and precise control of the melting process, is a popular application of inductive heating. Induction furnaces can reach temperatures of 1800ºC or higher, and typically consist of a chiller, power unit, and vacuum unit.
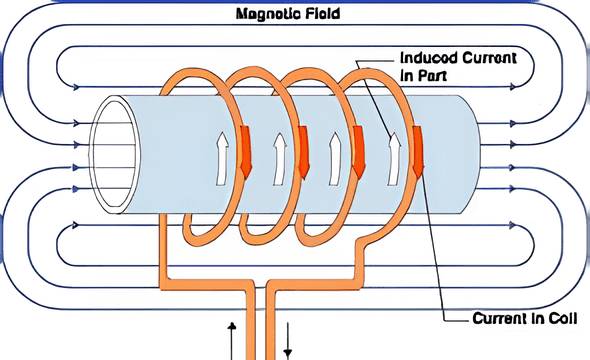
Advantages and disadvantages of inductive heating
Inductive heating offers several advantages over other heating methods. It is a faster process compared to electric or gas heating, thanks to its induction principle. Induction furnaces also have a quick startup time, as they do not require a warm-up or cooling down cycle. The induction power supply creates a strong stirring action, resulting in homogeneous mixtures of liquid metal. Additionally, induction furnaces require less refractory materials compared to fuel-fired units. They are more energy-efficient and capable of reducing power consumption for melting metals. Induction furnaces are also compact in size, allowing for easier installation, and enable higher production rates due to shorter melting times.
However, there are also some disadvantages to consider. The rated power of induction furnaces may not always reflect their actual working power, leading to reduced melting efficiency. It is important to ensure that the supplier has self-developed induction power board technology and can provide flexible customized solutions. Additionally, induction heating may pose challenges in heat distribution and heating rate, requiring careful consideration of the specific application and material being heated.
Issues with heat distribution and heating rate
Induction heating can produce high-power densities, allowing for short interaction times to reach the required temperature. This results in tight control of the heating pattern, closely following the applied magnetic field. This precise control helps reduce thermal distortion and damage to the material being heated.
However, heat distribution and heating rate can be potential issues in induction heating. Uneven heat distribution may occur if the induction coil does not have proper contact with the material or if the material has irregular shape or composition. It is important to ensure a proper coupling between the work coil and the object to be heated to achieve uniform heating.
The heating rate can also be influenced by factors such as the size and material of the object, as well as the penetration depth of the electromagnetic field. Understanding these factors and their impact on the heating process is crucial for achieving the desired results in induction heating applications.
Overall, inductive heating is a versatile and efficient method for heating electrically conductive materials. Its advantages in terms of speed, energy efficiency, and controllability make it a popular choice in various industries, including metallurgy, semiconductor manufacturing, and gold casting. By considering the specific requirements and challenges of each application, businesses can make informed decisions when utilizing inductive heating technology.
Indirect Resistance Heating
Indirect resistance heating is a technology used in electric furnaces that involves heating a mold or load using graphite heating elements. The heat is generated by passing an electric current through these elements, which then transfer the heat to the mold through convection. This process is known as indirect resistance heating.
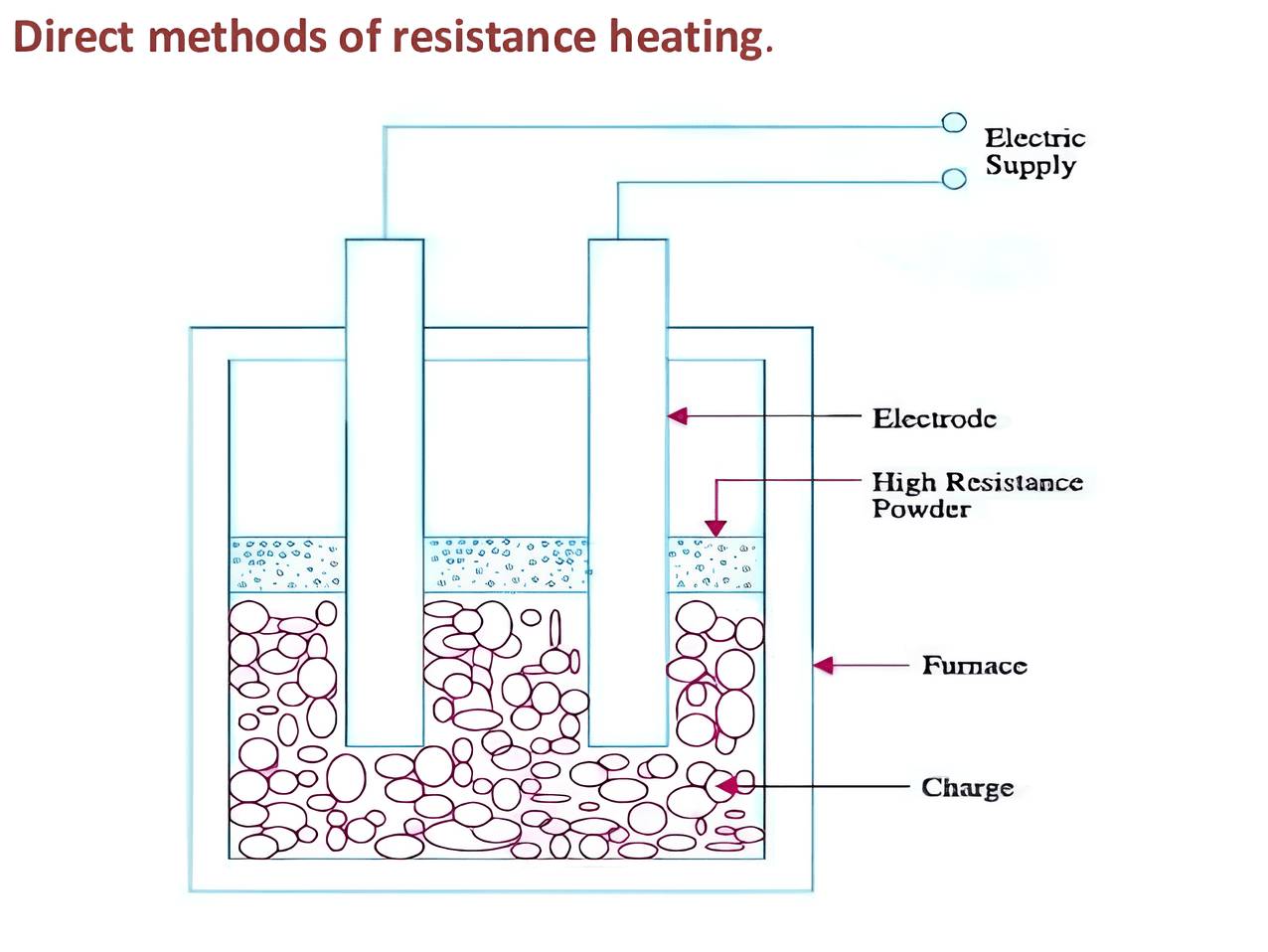
Process and Functioning of Indirect Resistance Heating
In indirect resistance heating, the mold is placed in a heating chamber where graphite heating elements are located. These elements are heated by the electric current passing through them. The heat generated by the heating elements is then transferred to the mold through convection, resulting in the heating of the mold.
Advantages and Disadvantages of Indirect Resistance Heating
One of the advantages of indirect resistance heating is the ability to achieve high temperatures. The temperature achieved is independent of the conductivity of the mold and is not affected by heat and pressure. However, a main disadvantage of indirect resistance heating is the time it takes to heat up the mold. The heat transfer from the furnace atmosphere to the mold surface and throughout the cross-section of the mold is relatively slow.
History and Current Interest in Resistance Heating
Resistance heating has been used for many years in various applications. It is commonly used in household appliances such as electric ranges and toasters. In recent years, there has been a growing interest in resistance heating for industrial applications, such as hot pressing technology. Induction heating and field assisted sintering technique (FAST) / direct hot pressing are other heating methods used in conjunction with resistance heating.
Resistance heating elements, such as resistance wires or ribbons, are commonly used in various heating devices and industrial furnaces. These elements convert electrical energy into heat through Joule heating. The resistance encountered by the electric current passing through the element results in the heating of the element.
In conclusion, indirect resistance heating is a technology that utilizes graphite heating elements to heat a mold or load through convection. It offers advantages such as high achievable temperatures, independent of mold conductivity and heat/pressure. However, it has the drawback of relatively slow heat transfer. Resistance heating elements, such as resistance wires, are commonly used in various heating devices and industrial furnaces.
Field Assisted Sintering Technique (FAST) / Direct Hot Pressing
Concept and execution of FAST
Field Assisted Sintering Technology/Spark Plasma Sintering (FAST/SPS) utilizes a DC electric current to directly heat the mold and/or sample through Joule heating. This direct heating allows for high heating rates and low processing cycle times to be achieved. It also enables the consolidation of a wide range of metallic, ceramic, and functional materials. FAST/SPS offers new possibilities for manufacturing materials with potentially extraordinary characteristics. It can also process multi-material composites, functionally grade, and diffusion bond materials.
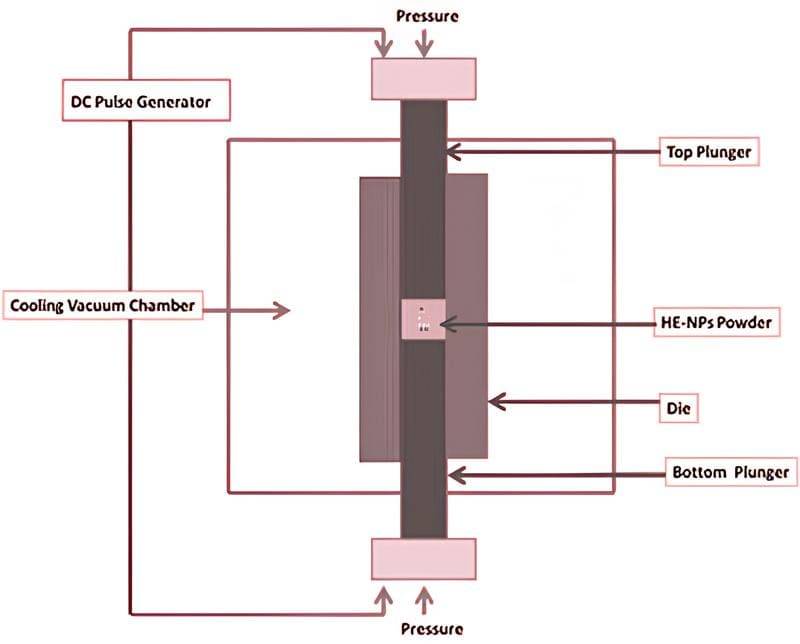
Reasons for shortening cycle time
The compelling reason for shortening the cycle time in direct hot pressing is to avoid grain growth and save energy. In direct hot pressing, the mold is directly connected to electrical power, generating heat in the mold through the resistivity of the mold and the powder part. This results in very high heating rates and significantly increases the sintering activity of fine metal powder aggregates. Short cycle times of a few minutes become possible, and the process lowers the threshold sintering temperature and pressure compared to conventional sintering techniques. Direct resistance heating ensures that the heat is generated where it is needed.
Benefits of direct hot pressing
Direct hot pressing offers several benefits compared to conventional powder metallurgy sintering techniques. It allows for the production of unique properties by utilizing lower processing temperatures and/or shorter processing times. It enables hot pressing sintering of metal and ceramic powders, the preparation of ceramic/metal composites and intermetallic compounds, and the research and development of diffusion welding processes. It also facilitates the densification hot press sintering of oxygen/nitrogen/boron/carbon compounds and their mixtures.
Differences between sintering with pulsed or unpulsed current
Latest research suggests that there is no basic difference between sintering with pulsed or unpulsed current (SPS or FAST). In principle, all direct hot pressing techniques can achieve improved sintering results compared to conventional hot pressing if the improvement is only due to the in-situ heating of the powder. However, if additional physical effects associated with the electrical current density itself are present, a pulsed current frequently has additional beneficial effects. This is because during each pulse, the electrical current density peaks to a significantly higher value than a DC current with comparable heating power.
In summary, Field Assisted Sintering Technique (FAST) or direct hot pressing using a direct electric current offers numerous advantages in terms of shorter processing cycle times, lower temperatures and pressures, and the ability to produce unique properties in a wide range of materials. Whether using pulsed or unpulsed current, the direct hot pressing technique can achieve improved sintering results compared to conventional methods.
Applications of Hot Pressing
Manufacture of critical items like sputtering targets and high-performance ceramic components
Hot pressing technology has been successfully used in the manufacture of critical items such as sputtering targets and high-performance ceramic components. Materials like boron carbide, titanium diboride, and sialon have been achieved using this process. By using metal powder, the conductivity of the mold allows for fast heating of the workpiece. This method is especially suitable for applications that require high heating rates, making it ideal for materials that can only be held at high temperatures briefly or for processes requiring rapid heating rates for high productivity.
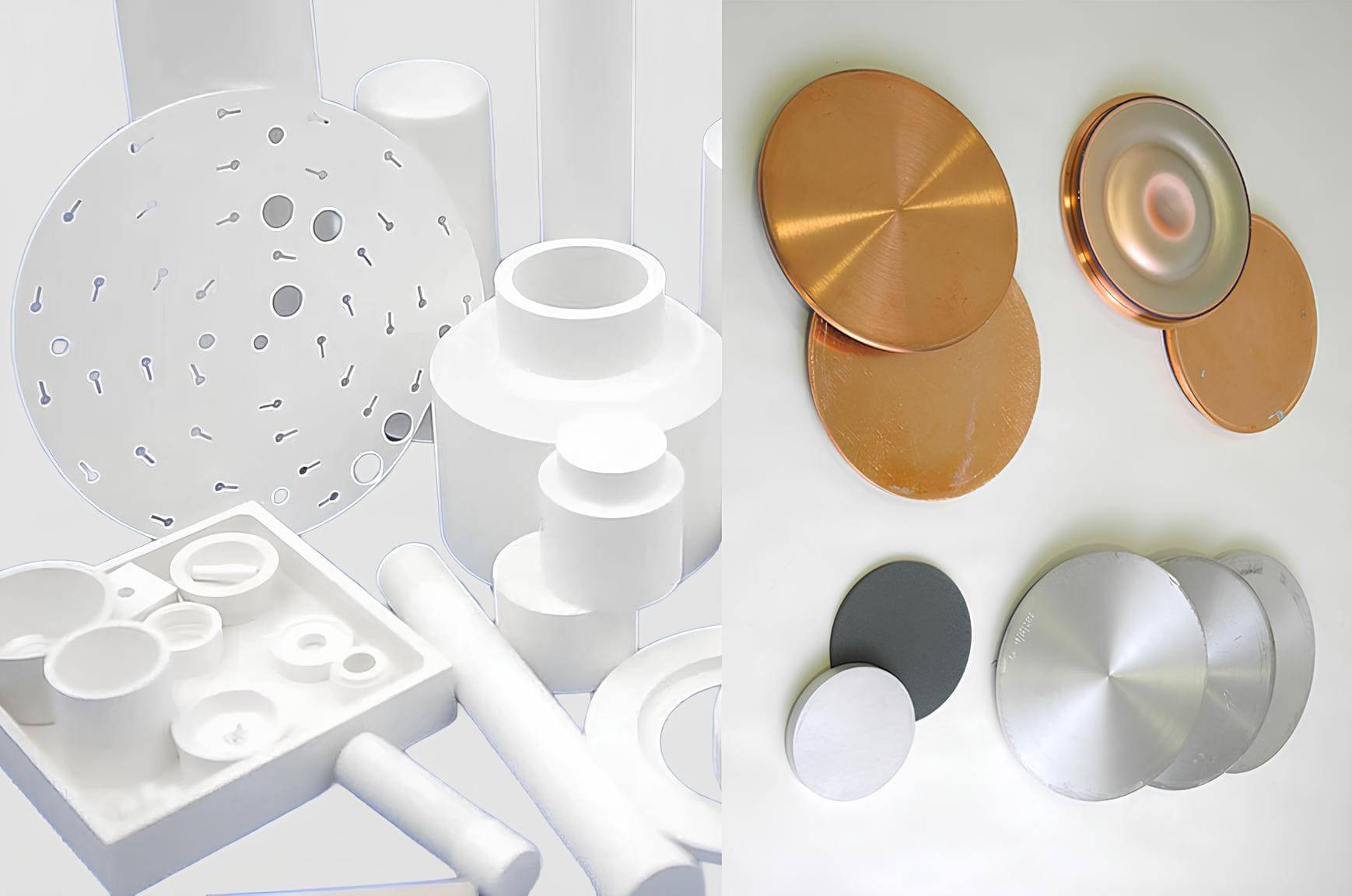
Benefits of using metal powder
One of the advantages of using metal powder in the hot pressing process is that it allows for fast heating of the workpiece. Molds with a large diameter and relatively small height can be heated quickly, resulting in increased efficiency and productivity. Additionally, using metal powder eliminates the need for binders in the manufacturing process, allowing for a complete bond of the parts using a combination of force and temperature.
Suitability of the process for high heating rates
The hot pressing process is particularly suitable for applications that require high heating rates. This is beneficial for materials that can only be held at high temperatures briefly or for processes that require rapid heating rates to achieve high productivity. The combination of force and temperature in hot pressing allows for quick and efficient bonding of the parts.
Role of direct hot pressing in friction material industry
Direct hot pressing technology plays a significant role in the friction material industry. It allows materials to be sintered to their final density, achieving a high level of near-net-shape precision. This precision often eliminates the need for mechanical reworking of materials that are difficult to process. Direct hot pressing is particularly useful for materials that require a high level of density and precision in their final form.
Applications of sintered brake pads and clutch discs
Hot pressing is commonly used in the production of sintered brake pads and clutch discs. The process allows for the creation of dense and high-performance materials that offer superior braking and clutch engagement capabilities. Sintered brake pads and clutch discs are known for their durability, heat resistance, and consistent performance, making them highly valued in the automotive industry.
In conclusion, hot pressing is a versatile and valuable process that finds applications in various industries. It is particularly useful in the manufacture of critical items like sputtering targets and high-performance ceramic components. The use of metal powder in hot pressing offers benefits such as fast heating and elimination of binders. The process is suitable for high heating rates and plays a significant role in the friction material industry. Additionally, hot pressing is widely used in the production of sintered brake pads and clutch discs, providing superior performance and durability in automotive applications.
CONTACT US FOR A FREE CONSULTATION
KINTEK LAB SOLUTION's products and services have been recognized by customers around the world. Our staff will be happy to assist with any inquiry you might have. Contact us for a free consultation and talk to a product specialist to find the most suitable solution for your application needs!