Centrifugal separators are widely used in various industries for separating components of different densities, such as liquids from solids or immiscible liquids. While they offer numerous advantages, including high efficiency and the ability to handle large volumes, they also come with several disadvantages. These include high initial and operational costs, sensitivity to feed variations, maintenance challenges, and limitations in handling certain types of materials. Understanding these drawbacks is crucial for making informed decisions when selecting separation equipment.
Key Points Explained:
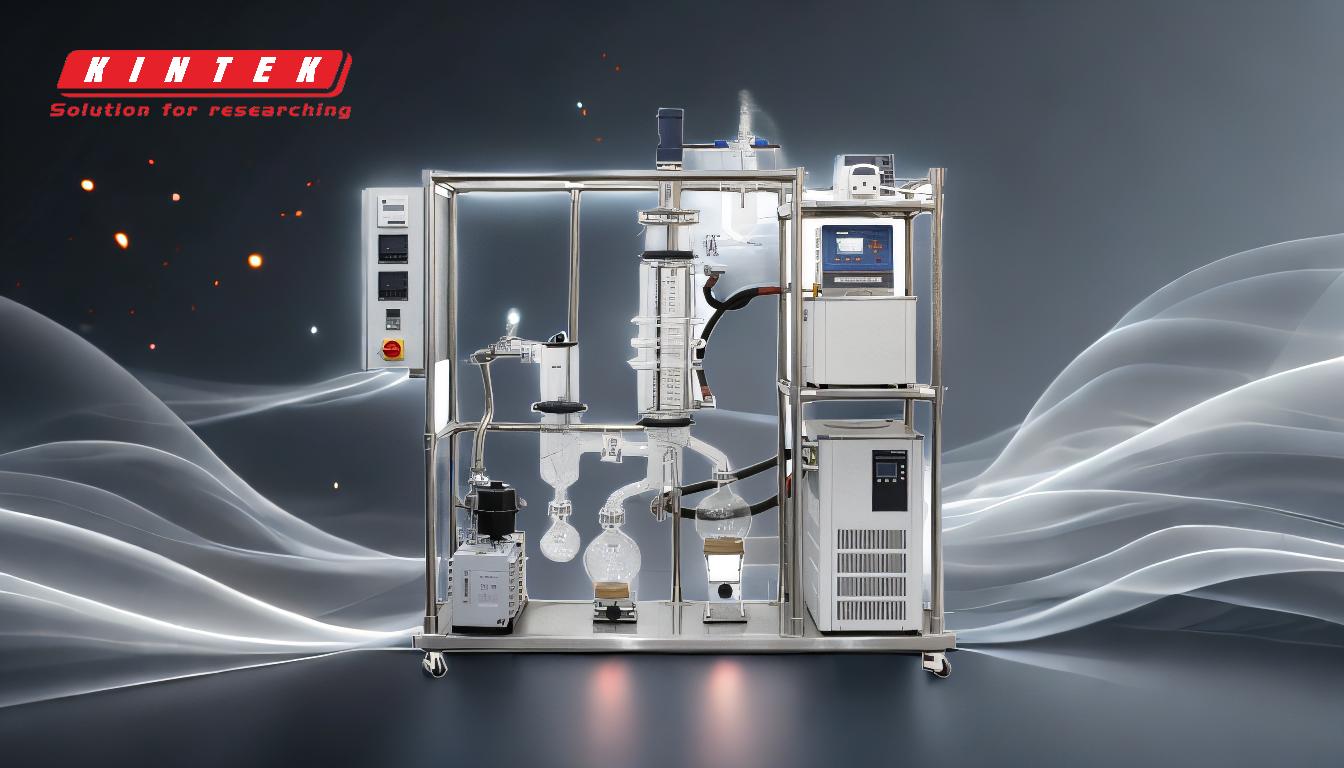
-
High Initial and Operational Costs:
- Capital Investment: Centrifugal separators require significant upfront investment due to their complex design and high-quality materials needed to withstand the forces involved.
- Operational Expenses: The energy consumption of centrifugal separators is high, especially for units operating at high speeds. This results in elevated operational costs over time.
- Maintenance Costs: Regular maintenance is essential to keep the equipment running efficiently, adding to the overall cost of ownership.
-
Sensitivity to Feed Variations:
- Consistency of Feed: Centrifugal separators perform best with a consistent feed in terms of flow rate, density, and particle size. Variations in these parameters can lead to reduced separation efficiency and potential damage to the equipment.
- Pre-Treatment Requirements: To mitigate sensitivity, pre-treatment of the feed may be necessary, such as filtering or homogenizing, which adds complexity and cost to the process.
-
Maintenance Challenges:
- Wear and Tear: The high rotational speeds and mechanical forces involved in centrifugal separation lead to significant wear and tear on components, necessitating frequent maintenance and part replacements.
- Complexity of Maintenance: The intricate design of centrifugal separators makes maintenance tasks complex and time-consuming, often requiring specialized skills and tools.
-
Limitations in Handling Certain Materials:
- Viscous Fluids: Centrifugal separators are less effective with highly viscous fluids, as the separation efficiency decreases with increasing viscosity.
- Abrasives and Corrosives: Materials that are abrasive or corrosive can cause rapid degradation of the separator's components, leading to frequent failures and increased maintenance needs.
- Temperature Sensitivity: Some materials may degrade or change properties at the high temperatures generated during operation, limiting the applicability of centrifugal separators in certain processes.
-
Space and Installation Requirements:
- Footprint: Centrifugal separators, especially larger models, require significant space for installation, which can be a constraint in facilities with limited space.
- Installation Complexity: Proper installation is critical for optimal performance, often requiring precise alignment and foundation work, adding to the initial setup time and cost.
-
Noise and Vibration:
- Operational Noise: The high-speed operation of centrifugal separators generates considerable noise, which can be a concern in environments where noise levels need to be controlled.
- Vibration Issues: Vibrations from the equipment can affect nearby machinery and structures, potentially leading to additional maintenance and operational challenges.
-
Limited Scalability:
- Batch vs. Continuous Operation: Some centrifugal separators are designed for batch operation, which may not be suitable for processes requiring continuous separation.
- Scalability Constraints: Scaling up centrifugal separation processes can be challenging, as larger units may not proportionally increase efficiency and can introduce new operational complexities.
In conclusion, while centrifugal separators offer significant advantages in terms of separation efficiency and capacity, their disadvantages, such as high costs, sensitivity to feed variations, maintenance challenges, and material handling limitations, must be carefully considered. Evaluating these factors in the context of specific application requirements is essential for selecting the most appropriate separation technology.
Summary Table:
Disadvantage | Key Details |
---|---|
High Initial and Operational Costs | Significant capital investment, high energy consumption, and maintenance costs. |
Sensitivity to Feed Variations | Requires consistent feed; pre-treatment may be needed. |
Maintenance Challenges | Frequent wear and tear; complex and time-consuming maintenance. |
Material Handling Limitations | Less effective with viscous, abrasive, or corrosive materials. |
Space and Installation Needs | Requires significant space and precise installation. |
Noise and Vibration | Generates operational noise and vibrations. |
Limited Scalability | Challenges in scaling up and continuous operation. |
Need help selecting the right separation equipment? Contact our experts today for tailored solutions!