Rotary pumps, particularly oil-sealed rotary vane vacuum pumps, are widely used in laboratories and industrial settings due to their ability to achieve deep vacuums and their relatively low initial cost. However, they come with several disadvantages that can impact their efficiency, cost-effectiveness, and environmental footprint. These include the need for regular oil top-ups, high operational costs, frequent maintenance requirements, and the potential release of oil mist into the environment. Additionally, improper maintenance or mismatched applications can lead to premature failure, making them more expensive in the long run. Understanding these drawbacks is crucial for making informed decisions about their use.
Key Points Explained:
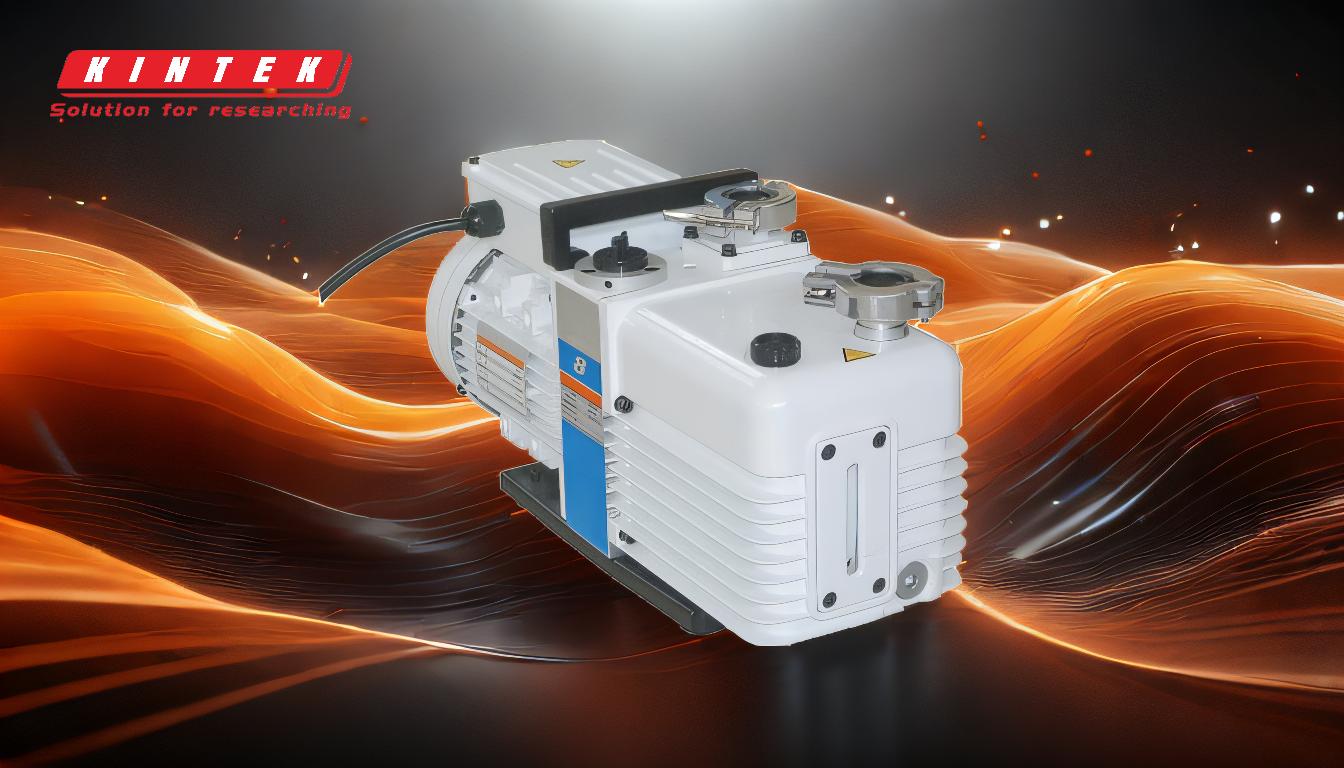
-
Regular Oil Top-Ups:
- Explanation: Oil-sealed rotary vane vacuum pumps require regular oil top-ups to maintain their performance. The oil acts as a sealant and lubricant, but it degrades over time and needs to be replenished.
- Impact: This requirement increases the operational burden and can lead to downtime, as the pump must be stopped for oil changes. It also adds to the ongoing costs of running the pump.
-
High Operational Costs:
- Explanation: These pumps are relatively expensive to run due to their energy consumption and the need for regular oil changes and maintenance.
- Impact: The cumulative cost of electricity, oil, and maintenance can make rotary vane pumps less economical over time compared to other types of pumps that may have higher upfront costs but lower ongoing expenses.
-
Frequent Maintenance:
- Explanation: Rotary vane pumps require frequent maintenance to ensure they operate efficiently. This includes regular oil changes, replacement of worn parts, and cleaning.
- Impact: The need for frequent maintenance can lead to increased downtime and labor costs. If maintenance is neglected, the pump's performance can degrade, leading to more significant issues and potential failure.
-
Release of Oil Mist:
- Explanation: Despite advancements in oil filter hardware, oil-sealed rotary vane pumps can still release some oil mist into the environment.
- Impact: This can be problematic in laboratory settings where contamination must be minimized. The release of oil mist can also pose health risks to operators and contribute to environmental pollution.
-
Potential for Premature Failure:
- Explanation: If a rotary vane pump is not maintained properly or is used in an application for which it is not suited, it may fail prematurely.
- Impact: Premature failure can lead to unexpected replacement costs and downtime, making the pump more expensive in the long run compared to other types of pumps that may have a longer lifespan with proper maintenance.
-
Environmental and Health Concerns:
- Explanation: The release of oil mist and the need for regular oil changes contribute to environmental pollution and potential health risks for operators.
- Impact: These concerns can lead to stricter regulations and the need for additional equipment to mitigate these effects, further increasing the operational costs and complexity of using rotary vane pumps.
-
Sample Loss in Rotary Evaporators:
- Explanation: When used in conjunction with rotary evaporators, rotary vane pumps can contribute to sample loss, especially with volatile substances like ethanol and water.
- Impact: This can be mitigated by adjusting the vacuum pump's strength or the heating pot's temperature, but it requires careful monitoring and can still result in some loss of valuable samples.
-
Taste and Aroma Issues:
- Explanation: In some cases, the use of rotary evaporators can lead to a final product that smells appealing but tastes unpleasant due to the concentration of certain aromatics.
- Impact: This can affect the quality of the final product, especially in applications where taste is a critical factor, such as in the food and beverage industry.
In summary, while rotary pumps, particularly oil-sealed rotary vane vacuum pumps, offer certain advantages such as the ability to achieve deep vacuums and lower initial costs, they come with significant disadvantages. These include high operational and maintenance costs, environmental and health concerns, and the potential for premature failure. Understanding these drawbacks is essential for making informed decisions about their use and for implementing strategies to mitigate their impact.
Summary Table:
Disadvantage | Explanation | Impact |
---|---|---|
Regular Oil Top-Ups | Oil degrades over time and must be replenished to maintain performance. | Increases operational burden, downtime, and ongoing costs. |
High Operational Costs | Energy consumption, oil changes, and maintenance make them expensive to run. | Cumulative costs can make them less economical over time. |
Frequent Maintenance | Requires regular oil changes, part replacements, and cleaning. | Leads to increased downtime, labor costs, and potential performance issues. |
Release of Oil Mist | Some oil mist may still be released into the environment. | Causes contamination, health risks, and environmental pollution. |
Potential for Premature Failure | Improper maintenance or mismatched applications can lead to early failure. | Unexpected replacement costs and downtime increase long-term expenses. |
Environmental and Health Concerns | Oil mist and frequent oil changes contribute to pollution and health risks. | Stricter regulations and higher operational costs may result. |
Sample Loss in Rotary Evaporators | Can cause loss of volatile substances like ethanol and water. | Requires careful monitoring and may lead to valuable sample loss. |
Taste and Aroma Issues | Final product may smell appealing but taste unpleasant due to concentrated aromatics. | Affects product quality, especially in food and beverage applications. |
Need help choosing the right vacuum pump for your lab? Contact our experts today to find the best solution for your needs!