Sintering is a critical process in powder metallurgy that significantly impacts the properties of a powder compact produced by pressing. During sintering, the compact is heated to temperatures below its melting point, leading to various physical and chemical changes such as particle bonding, grain growth, and pore elimination. These changes enhance the mechanical properties of the material, including strength, hardness, and wear resistance. However, sintering can also introduce defects like shrinkage and coarse grains, which may weaken the material. The process involves diffusion mechanisms that form necks at particle contact points, leading to densification and improved structural integrity. Overall, sintering transforms a loosely bonded green compact into a dense, cohesive component with enhanced performance characteristics.
Key Points Explained:
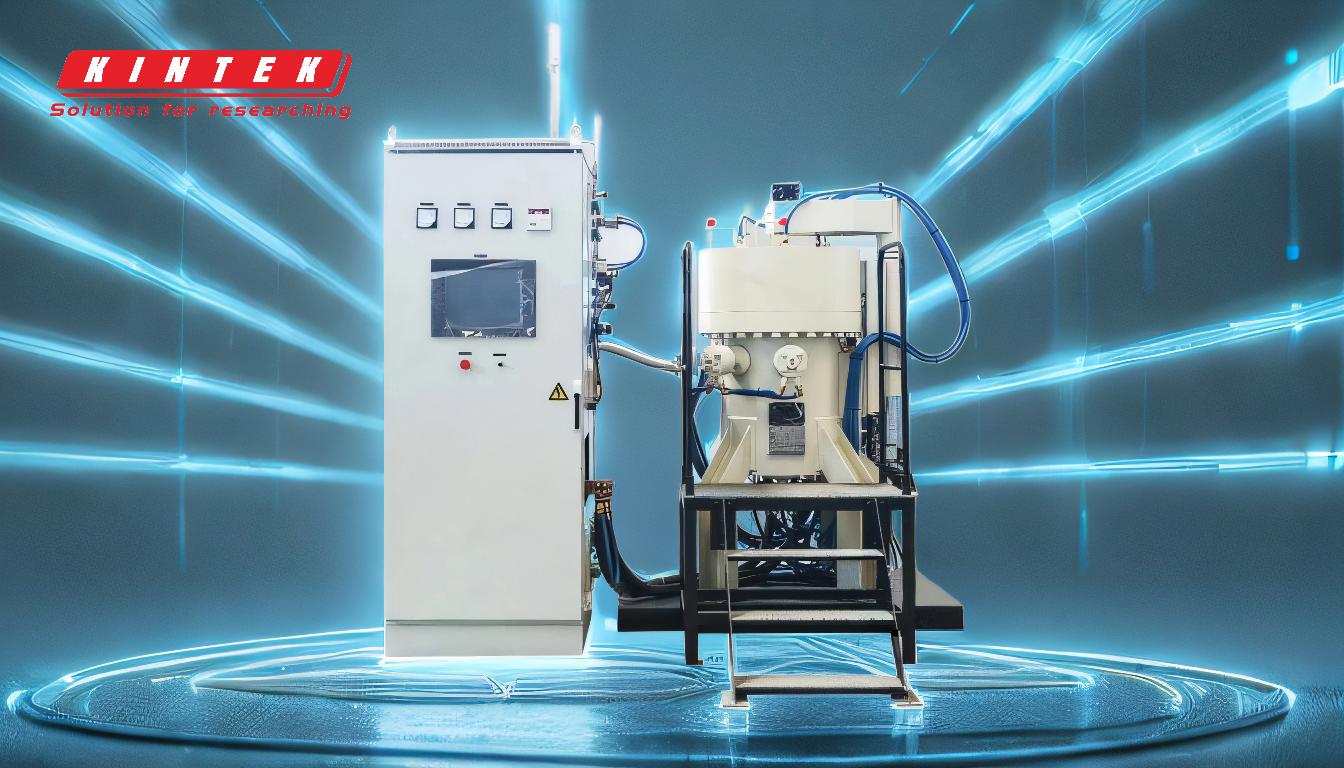
-
Metallurgical Bonding and Defects:
- Sintering creates strong metallurgical bonds between metal powders and the substrate through high temperatures or pressure.
- This bonding can lead to defects such as sorting, shrinkage, and coarse grains, which may weaken the mechanical properties of the material.
- Implications for Purchasers: Understanding these potential defects is crucial for selecting materials and sintering conditions that minimize adverse effects while maximizing bonding strength.
-
Temperature and Particle Rearrangement:
- Sintering occurs at temperatures below the melting point of the material, making it suitable for high-melting-point materials.
- At high temperatures, fine ceramic powders undergo grain growth and particle rearrangement, leading to the elimination of pores.
- Implications for Purchasers: The choice of sintering temperature is critical for achieving the desired density and microstructure, which directly affect the material's performance.
-
Cold Welds and Green Strength:
- After compaction, powder particles are held together by cold welds, providing the compact with sufficient green strength for handling.
- During sintering, diffusion processes cause necks to form and grow at these contact points, enhancing the material's structural integrity.
- Implications for Purchasers: Ensuring proper compaction and initial green strength is essential for successful sintering and the final product's quality.
-
Enhanced Mechanical Properties:
- Sintering improves the mechanical properties of materials, resulting in components with superior strength, hardness, and wear resistance.
- The controlled heating and diffusion mechanisms contribute to the development of a dense and cohesive structure.
- Implications for Purchasers: Sintered components are ideal for applications requiring high mechanical performance, making them a valuable choice for demanding environments.
-
Microstructural Changes:
- Sintering affects grain size, pore size, and grain boundary shape and distribution in the material's microstructure.
- These changes influence properties such as strength and durability.
- Implications for Purchasers: Understanding the microstructural changes helps in selecting materials and processes that optimize the desired properties for specific applications.
-
Physical and Chemical Changes:
- During sintering, several changes occur, including the evaporation of water or organic matter, removal of adsorbed gases, stress relief, reduction of surface oxides, material migration, recrystallization, and grain growth.
- Implications for Purchasers: These changes must be carefully controlled to achieve the desired material properties and avoid defects.
-
Powder Compacting:
- Powder compacting involves mechanical densification through cold or hot mold pressing to create a green part.
- This process allows for efficient production of components with tight tolerances due to low drying shrinkage.
- Implications for Purchasers: Proper compaction techniques are essential for achieving the desired shape and density before sintering, ensuring the final product meets specifications.
By considering these key points, purchasers can make informed decisions about the materials and processes used in sintering, ensuring the production of high-quality components with the desired mechanical properties and performance characteristics.
Summary Table:
Aspect | Key Details |
---|---|
Metallurgical Bonding | Creates strong bonds but may introduce defects like shrinkage and coarse grains. |
Temperature Effects | Occurs below melting point; critical for density and microstructure control. |
Cold Welds & Green Strength | Ensures structural integrity through diffusion and neck formation. |
Mechanical Properties | Improves strength, hardness, and wear resistance for demanding applications. |
Microstructural Changes | Affects grain size, pore size, and grain boundary distribution. |
Physical & Chemical Changes | Includes evaporation, stress relief, recrystallization, and grain growth. |
Powder Compacting | Enables efficient production of components with tight tolerances. |
Discover how sintering can enhance your material's performance—contact our experts today for tailored solutions!