Sputtering is a physical vapor deposition (PVD) technique used to deposit thin films of materials onto substrates. It involves bombarding a target material with high-energy ions in a vacuum environment, causing atoms to be ejected from the target and deposited onto a substrate. The process is highly precise and is widely used in industries such as semiconductors, optics, and coatings. Sputtering relies on the creation of a plasma, the ionization of a sputtering gas (typically argon), and the acceleration of ions toward the target. The ejected atoms form a thin film on the substrate, with properties such as reflectivity, conductivity, and density being controllable. The process is versatile, allowing for the deposition of metals, oxides, and other materials onto various substrates, including heat-sensitive ones like plastics.
Key Points Explained:
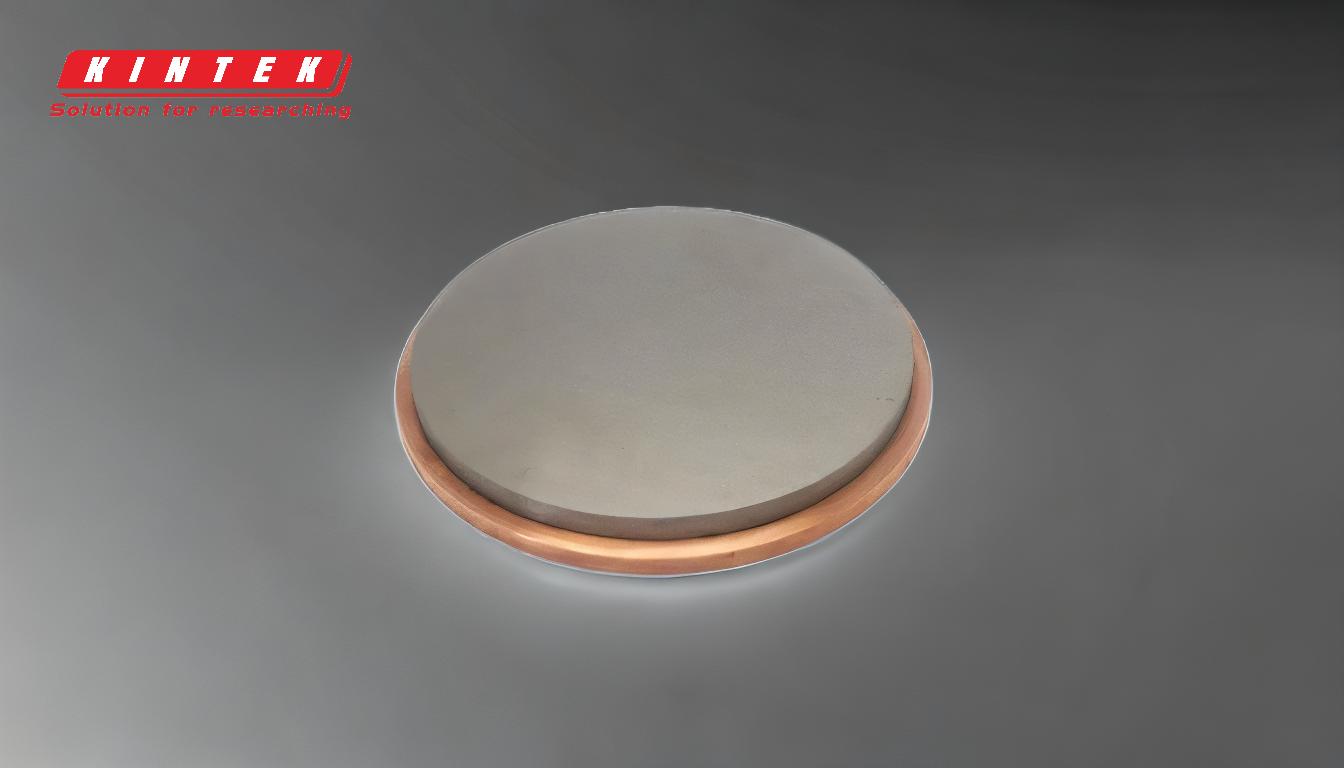
-
Basic Principle of Sputtering:
- Sputtering is a physical vapor deposition process where atoms are ejected from a solid target material due to bombardment by high-energy ions.
- The ejected atoms form a vapor stream that deposits onto a substrate, creating a thin film.
-
Role of Plasma and Ionization:
- A plasma is created by ionizing a sputtering gas (usually argon) in a vacuum chamber.
- Gas atoms lose electrons to become positively charged ions, which are then accelerated toward the target material by an electric field.
-
Target and Substrate Configuration:
- The target (source material) and substrate (destination) are placed in a vacuum chamber.
- The target acts as the cathode, while the substrate acts as the anode when a voltage is applied.
-
Energy Transfer and Ejection of Atoms:
- The accelerated ions collide with the target material, transferring kinetic energy.
- This energy transfer causes atoms or molecules to be ejected from the target surface in a process known as sputtering.
-
Deposition of Thin Films:
- The ejected atoms travel through the chamber and deposit onto the substrate.
- The atoms nucleate and form a thin film with specific properties, such as reflectivity, electrical resistivity, or ionic resistivity.
-
Control Over Film Properties:
- Sputtering allows precise control over film morphology, grain orientation, grain size, and density.
- This makes it suitable for applications requiring high precision, such as semiconductor manufacturing and optical coatings.
-
Versatility of the Process:
- Sputtering can be used to deposit a wide range of materials, including metals, oxides, and nitrides.
- It is compatible with various substrates, including heat-sensitive materials like plastics.
-
Vacuum Environment:
- The process occurs in a vacuum chamber to prevent contamination from air or other gases.
- The vacuum ensures that the sputtered particles maintain high kinetic energy and purity.
-
Applications of Sputtering:
- Sputtering is used in industries such as electronics (semiconductors, displays), optics (anti-reflective coatings), and decorative coatings.
- It is also employed in research for creating thin films with tailored properties.
-
Advantages of Sputtering:
- High precision and control over film properties.
- Ability to deposit ultra-high purity materials.
- Compatibility with a wide range of substrates and materials.
By understanding these fundamentals, one can appreciate the versatility and precision of the sputtering process, making it a cornerstone technology in modern manufacturing and research.
Summary Table:
Key Aspect | Description |
---|---|
Basic Principle | Atoms ejected from a target material by high-energy ions form a thin film. |
Role of Plasma | Ionized gas (argon) creates plasma, accelerating ions toward the target. |
Target & Substrate | Target (cathode) and substrate (anode) are placed in a vacuum chamber. |
Energy Transfer | Ions collide with the target, transferring kinetic energy to eject atoms. |
Thin Film Deposition | Ejected atoms deposit onto the substrate, forming films with controlled properties. |
Film Property Control | Precise control over morphology, grain size, and density for high-precision applications. |
Versatility | Deposits metals, oxides, nitrides, and more on various substrates, including plastics. |
Vacuum Environment | Ensures high kinetic energy and purity of sputtered particles. |
Applications | Used in semiconductors, optics, coatings, and research for tailored thin films. |
Advantages | High precision, ultra-high purity, and compatibility with diverse materials. |
Discover how sputtering can enhance your manufacturing or research—contact our experts today!