Rotary pumps, particularly rotary vane vacuum pumps, are widely used due to their cost-effectiveness and ability to handle continuous suction and dry gas extraction. However, they come with several limitations, including the need for regular oil top-ups, high operational costs, frequent maintenance requirements, and the potential release of oil mist into the environment despite advancements in oil filter technology. These factors can make them less suitable for certain laboratory environments or applications where cleanliness and low maintenance are critical.
Key Points Explained:
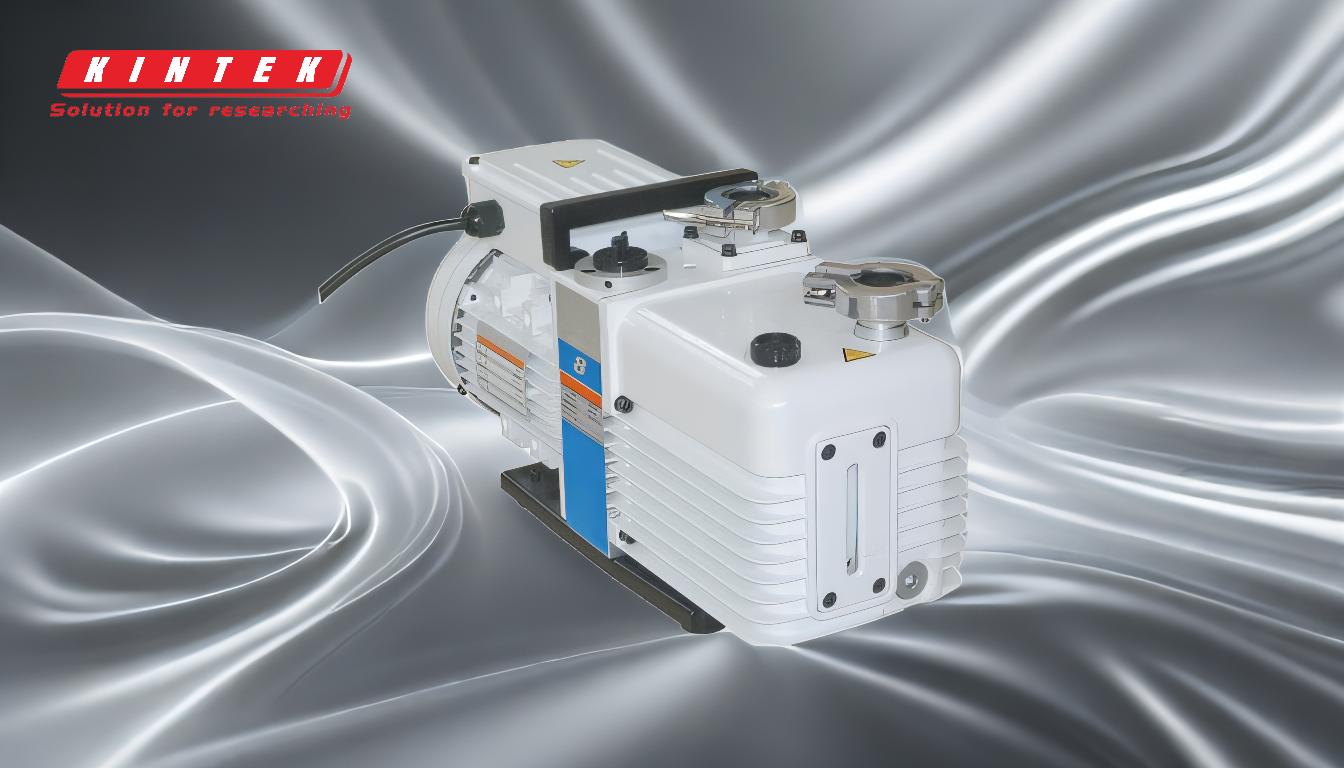
-
Regular Oil Top-Ups:
- Explanation: Rotary vane vacuum pumps require regular oil top-ups to maintain optimal performance. The oil serves as a sealant and lubricant for the moving parts within the pump. Over time, the oil degrades or gets consumed, necessitating frequent replenishment.
- Impact: This requirement can be inconvenient and time-consuming, especially in environments where continuous operation is essential. It also adds to the operational costs due to the need for purchasing and managing oil supplies.
-
High Operational Costs:
- Explanation: Despite being cost-effective in terms of initial purchase, rotary vane vacuum pumps can be relatively expensive to run. The costs include not only the oil but also electricity consumption and potential downtime for maintenance.
- Impact: The cumulative operational costs can be significant, making these pumps less economical in the long run compared to other types of vacuum pumps that may have lower running costs.
-
Frequent Maintenance:
- Explanation: These pumps require frequent maintenance to ensure they operate efficiently. Maintenance tasks include oil changes, filter replacements, and general wear and tear repairs.
- Impact: The need for regular maintenance can lead to increased downtime and labor costs. It also requires a certain level of expertise to perform the maintenance correctly, which may necessitate additional training or hiring specialized personnel.
-
Oil Mist Release:
- Explanation: Even with updated oil filter hardware, rotary vane vacuum pumps can still release oil mist into the laboratory environment. This mist can contaminate the workspace and potentially affect sensitive experiments or processes.
- Impact: The release of oil mist can be a significant drawback in environments that require high levels of cleanliness, such as cleanrooms or laboratories conducting sensitive analytical work. It may also pose health risks to personnel and require additional measures to mitigate contamination.
-
Limited Suitability for Certain Applications:
- Explanation: While rotary vane vacuum pumps are effective for continuous suction and dry gas extraction, they may not be suitable for applications involving corrosive gases, high moisture levels, or other challenging conditions.
- Impact: This limitation restricts their use in certain industrial or laboratory settings, necessitating the use of alternative pump types that can handle more demanding conditions.
-
Noise and Vibration:
- Explanation: Rotary vane vacuum pumps can generate significant noise and vibration during operation, which can be disruptive in quiet laboratory environments.
- Impact: The noise and vibration can affect the comfort of personnel and may interfere with sensitive measurements or experiments that require a stable and quiet environment.
In summary, while rotary vane vacuum pumps are widely used and cost-effective for many applications, they come with several limitations that can affect their suitability for certain environments and tasks. These include the need for regular oil top-ups, high operational costs, frequent maintenance, potential oil mist release, limited suitability for challenging conditions, and noise and vibration issues. Understanding these limitations is crucial for making informed decisions when selecting a vacuum pump for specific applications.
Summary Table:
Limitation | Explanation | Impact |
---|---|---|
Regular Oil Top-Ups | Oil degrades or gets consumed, requiring frequent replenishment. | Inconvenient, time-consuming, and increases operational costs. |
High Operational Costs | Includes oil, electricity, and maintenance downtime. | Cumulative costs make them less economical in the long run. |
Frequent Maintenance | Oil changes, filter replacements, and wear repairs are required. | Increases downtime, labor costs, and may require specialized expertise. |
Oil Mist Release | Oil mist can contaminate the environment despite advanced filters. | Unsuitable for cleanrooms or sensitive experiments; poses health risks. |
Limited Suitability | Not ideal for corrosive gases, high moisture, or challenging conditions. | Restricts use in certain applications, necessitating alternative pumps. |
Noise and Vibration | Generates significant noise and vibration during operation. | Disruptive in quiet environments and may interfere with sensitive measurements. |
Need help choosing the right vacuum pump for your application? Contact our experts today for personalized advice!