Designing a reactor for laboratory or industrial use involves a comprehensive understanding of the parameters that ensure optimal performance, safety, and efficiency. The key parameters for reactor design include evaporation reaction, heating reaction, speed, cooling effect, material strength, heat and mass transfer optimization, and compliance with industry standards such as GMP. These parameters must align with the specific functions and goals of the reactor, whether for pharmaceutical, chemical, or other applications. Below, we explore these parameters in detail to provide a clear understanding of what to consider when designing or selecting a reactor.
Key Points Explained:
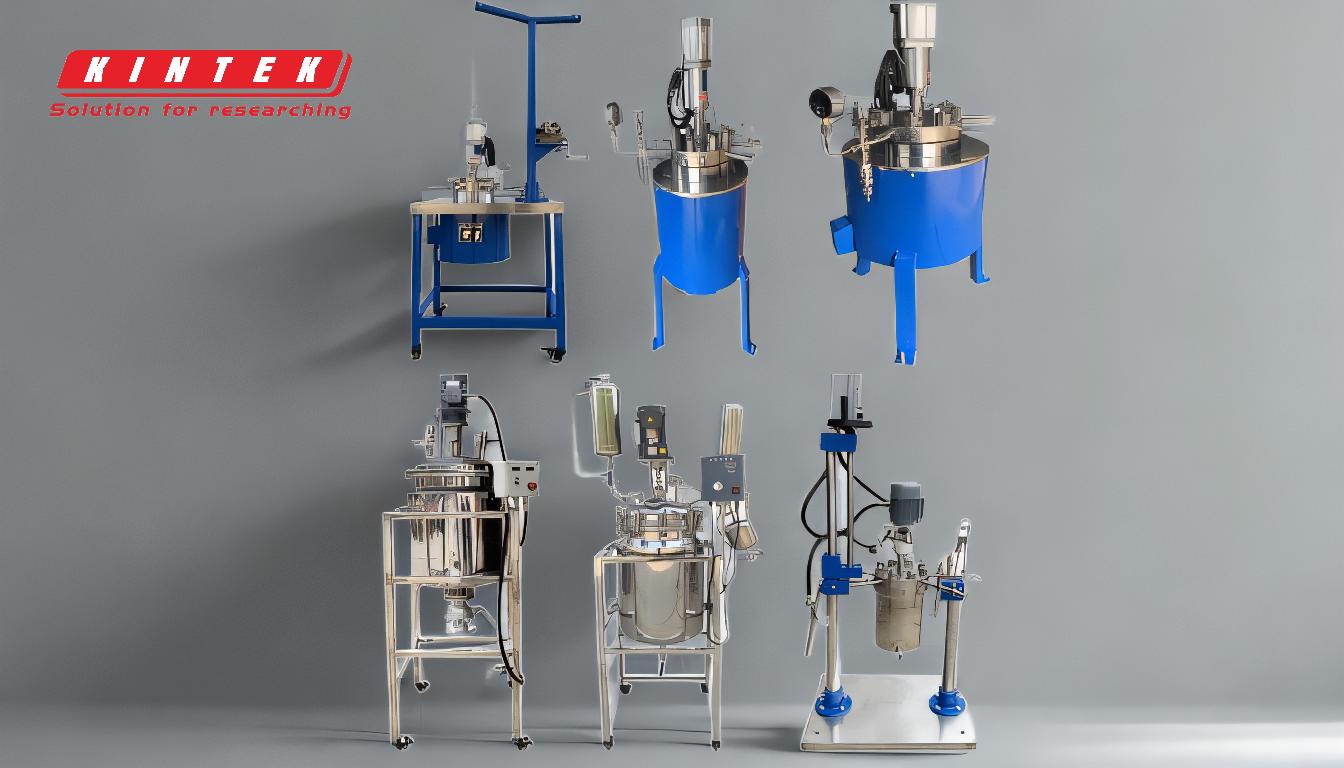
-
Evaporation Reaction Parameters:
- Purpose: Evaporation reactions require precise control over temperature and pressure to ensure efficient separation of components.
-
Design Considerations:
- The reactor should have a robust heating system to maintain consistent temperatures.
- A vacuum system may be necessary to lower the boiling point of solvents, enhancing evaporation efficiency.
- The design should include features to prevent loss of volatile components during the process.
-
Heating Reaction Parameters:
- Purpose: Heating reactions depend on accurate temperature control to drive chemical reactions effectively.
-
Design Considerations:
- The reactor should have a reliable heating mechanism, such as a jacket or coil, to distribute heat evenly.
- Temperature sensors and controllers are essential to maintain the desired reaction conditions.
- Materials used in the reactor must withstand high temperatures without degrading.
-
Speed and Mixing Parameters:
- Purpose: Proper mixing ensures uniform reaction conditions and prevents localized overheating or incomplete reactions.
-
Design Considerations:
- The reactor should include an efficient agitator or stirrer to maintain consistent mixing speeds.
- Variable speed controls allow for adjustments based on the reaction requirements.
- The design should minimize dead zones where mixing may be insufficient.
-
Cooling Effect Parameters:
- Purpose: Cooling is critical to control exothermic reactions and prevent overheating.
-
Design Considerations:
- The reactor should have an integrated cooling system, such as a cooling jacket or coil.
- The cooling system must be capable of rapidly reducing temperatures when needed.
- Materials should be chosen to handle thermal shocks during cooling.
-
Material Strength and Durability:
- Purpose: The reactor must withstand the physical and chemical stresses of the reaction process.
-
Design Considerations:
- High-quality borosilicate glass (e.g., 3.3 or 3009 glass) is often used for its strength and resistance to thermal and chemical shocks.
- Steel reactors with glass lining or PTFE coatings provide additional durability and chemical resistance.
- The reactor cover should be robust and securely sealed to prevent leaks or contamination.
-
Heat and Mass Transfer Optimization:
- Purpose: Efficient heat and mass transfer are essential for consistent reaction outcomes.
-
Design Considerations:
- The reactor design should maximize surface area for heat exchange.
- Internal components, such as baffles or coils, can enhance mixing and heat transfer.
- The reactor should be compatible with various heating and cooling mediums.
-
Compliance with GMP Standards:
- Purpose: In pharmaceutical applications, reactors must meet Good Manufacturing Practice (GMP) requirements to ensure product safety and quality.
-
Design Considerations:
- The reactor should be easy to clean and sterilize to prevent cross-contamination.
- Materials must be non-reactive and suitable for use in sterile environments.
- The design should facilitate documentation and validation processes required by GMP.
-
Compact Layout and Modular Construction:
- Purpose: A compact and modular design allows for flexibility and scalability in laboratory or industrial settings.
-
Design Considerations:
- The reactor should have a small footprint to save space.
- Modular components enable easy upgrades or modifications for special functions.
- The design should allow for integration with other equipment, such as distillation units or filtration systems.
-
Special Functions and Expansion Capabilities:
- Purpose: Reactors should be adaptable to accommodate unique reaction requirements or future needs.
-
Design Considerations:
- The reactor should support additional features, such as reflux condensers or sampling ports.
- Expansion capabilities, such as adding extra modules or accessories, should be considered during the design phase.
- The reactor should be compatible with automation systems for advanced process control.
By carefully considering these parameters, you can design or select a reactor that meets your specific needs, whether for laboratory research or industrial production. Each parameter plays a critical role in ensuring the reactor's performance, safety, and compliance with industry standards.
Summary Table:
Parameter | Purpose | Design Considerations |
---|---|---|
Evaporation Reaction | Efficient separation of components | Robust heating, vacuum system, prevent volatile loss |
Heating Reaction | Accurate temperature control for reactions | Reliable heating mechanism, temperature sensors, high-temperature materials |
Speed and Mixing | Uniform reaction conditions | Efficient agitator, variable speed controls, minimize dead zones |
Cooling Effect | Control exothermic reactions | Integrated cooling system, rapid temperature reduction, thermal shock-resistant materials |
Material Strength | Withstand physical and chemical stresses | Borosilicate glass, steel with glass lining or PTFE coatings, secure sealing |
Heat and Mass Transfer | Consistent reaction outcomes | Maximize surface area, internal baffles/coils, compatible heating/cooling mediums |
GMP Compliance | Ensure product safety and quality | Easy cleaning/sterilization, non-reactive materials, facilitate documentation |
Compact Layout | Flexibility and scalability | Small footprint, modular components, integration with other equipment |
Special Functions | Adapt to unique requirements | Reflux condensers, sampling ports, automation compatibility |
Need help designing a reactor tailored to your needs? Contact our experts today for personalized solutions!