Magnetron sputtering is a versatile and widely used thin-film deposition technique with applications spanning multiple industries and research fields. It is particularly valued for its ability to produce high-quality, uniform coatings with specific functional properties. Key applications include microelectronics, optics, machining, and decorative coatings, as well as advanced research areas like high-temperature superconductors, solar cells, and memory alloys. The technology is essential in semiconductor manufacturing, optical film production, and surface engineering, offering solutions for wear resistance, corrosion protection, and energy efficiency. Below, the key uses of magnetron sputtering are explained in detail.
Key Points Explained:
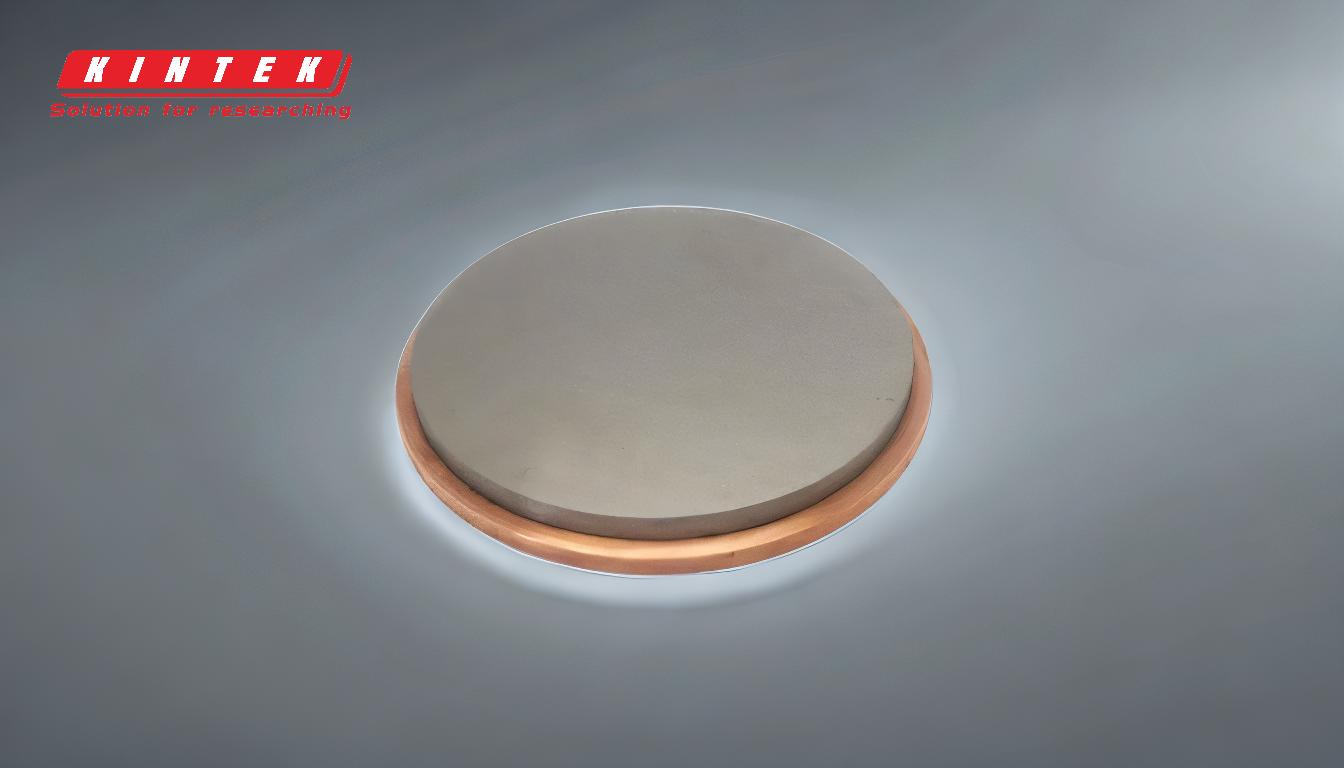
-
Microelectronics and Semiconductor Industry
- Magnetron sputtering is a cornerstone of the semiconductor industry, used for depositing thin films in integrated circuit (IC) fabrication.
- It enables the creation of conductive, insulating, and semiconducting layers essential for ICs, transistors, and memory devices.
- Historically, it played a pivotal role in the production of computer hard disks, where it was used to deposit magnetic layers.
-
Optical Applications
- Magnetron sputtering is widely used to produce optical films with specific properties such as absorption, transmission, reflection, refraction, and polarization.
- Applications include anti-reflective coatings for lenses, low-radiation glass, and transparent conductive coatings for touchscreens and displays.
- It is also used in energy-saving glass and solar control coatings for architectural glass, enhancing energy efficiency in buildings.
-
Surface Engineering and Machining
- In the machining industry, magnetron sputtering is used to deposit functional coatings such as super-hard films, wear-resistant films, and self-lubricating films.
- These coatings improve the durability and performance of tools, molds, and machine parts, reducing wear and extending service life.
- It is also applied to aircraft and automobile components to enhance wear resistance and reduce friction.
-
Decorative and Functional Coatings
- Magnetron sputtering is employed for high-grade decorative coatings, such as those used in mobile phone back panels and luxury items.
- It provides aesthetic finishes while also offering functional benefits like scratch resistance and durability.
-
Advanced Research and Emerging Technologies
- The technology is critical in research areas such as high-temperature superconducting thin films, ferroelectric thin films, and giant magnetoresistive thin films.
- It is used to develop thin-film light-emitting materials, memory alloys, and materials for solar cells, contributing to advancements in renewable energy and electronics.
-
Energy Applications
- Magnetron sputtering is integral to the production of thin-film solar cells, enabling the deposition of photovoltaic layers that convert sunlight into electricity.
- It is also used in thin-film batteries and barrier layers for organic light-emitting diodes (OLEDs) and solar cells, enhancing their performance and longevity.
-
Industrial and Large-Area Coatings
- The technique is applied in large-area coatings for architectural glass, providing functionalities such as solar control, thermal insulation, and glare reduction.
- It is also used in the textile industry for depositing functional coatings on fabrics, such as conductive or anti-static layers.
-
Wear and Corrosion Protection
- Magnetron sputtering is widely used to deposit hard coatings on tools and molds, improving their resistance to wear and extending their lifespan.
- It is also applied to machine and engine parts to reduce friction and enhance corrosion resistance, contributing to improved efficiency and reliability.
In summary, magnetron sputtering is a highly adaptable technology with applications ranging from industrial manufacturing to cutting-edge research. Its ability to deposit precise, high-performance coatings makes it indispensable in fields such as microelectronics, optics, energy, and surface engineering. By enabling the creation of functional films with tailored properties, magnetron sputtering continues to drive innovation and efficiency across multiple sectors.
Summary Table:
Application | Key Uses |
---|---|
Microelectronics | IC fabrication, conductive layers, memory devices |
Optical Applications | Anti-reflective coatings, touchscreens, energy-saving glass |
Surface Engineering | Wear-resistant films, self-lubricating films, tool and mold coatings |
Decorative Coatings | Mobile phone back panels, luxury items, scratch-resistant finishes |
Advanced Research | High-temperature superconductors, solar cells, memory alloys |
Energy Applications | Thin-film solar cells, OLED barrier layers, thin-film batteries |
Industrial Coatings | Architectural glass, solar control, conductive fabric coatings |
Wear and Corrosion Protection | Hard coatings for tools, engine parts, corrosion-resistant films |
Discover how magnetron sputtering can revolutionize your industry—contact our experts today!