Sputtering is a physical process in which atoms are ejected from a solid target material due to bombardment of the target by energetic particles, typically ions. This technique is widely used in materials science and thin-film deposition, where it allows for the precise coating of surfaces with thin layers of material. Sputtering is a key process in the manufacturing of semiconductors, optical coatings, and various nanotechnology applications. It is a non-thermal process, meaning it does not rely on heat to achieve material transfer, making it suitable for temperature-sensitive substrates.
Key Points Explained:
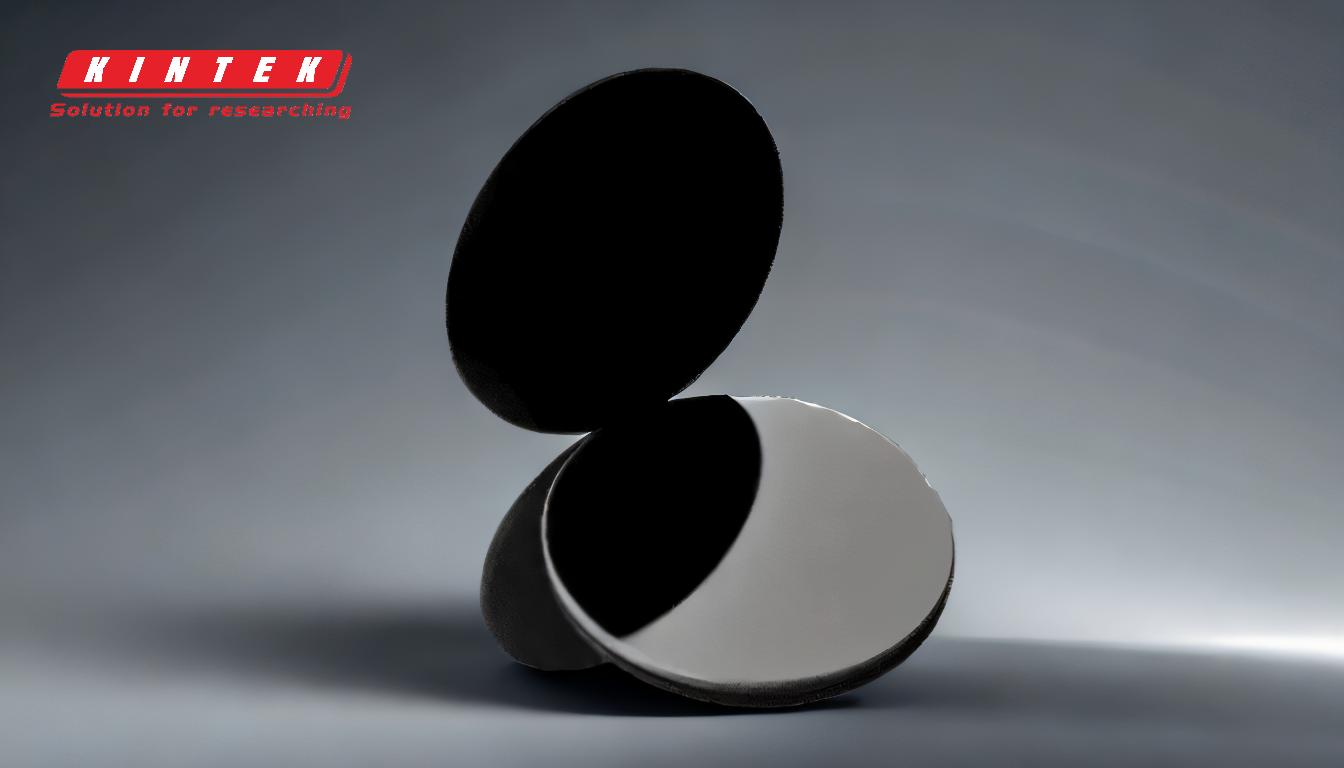
-
Definition of Sputtering:
- Sputtering refers to the ejection of atoms from a solid target material when it is bombarded by high-energy particles, usually ions. This process occurs in a vacuum environment to ensure that the ejected atoms can travel unimpeded and deposit onto a substrate.
-
Mechanism of Sputtering:
- The process begins with the acceleration of ions (often argon ions) towards the target material. When these ions collide with the target, they transfer their energy to the target atoms. If the energy transfer is sufficient, the target atoms are dislodged from their positions and ejected into the surrounding space.
-
Types of Sputtering:
- DC Sputtering: Uses a direct current (DC) power source to create a plasma that bombards the target material. Commonly used for conductive materials.
- RF Sputtering: Utilizes radio frequency (RF) power to generate plasma, making it suitable for both conductive and non-conductive materials.
- Magnetron Sputtering: Incorporates magnetic fields to enhance the efficiency of the sputtering process by confining electrons near the target surface, increasing the ionization rate of the sputtering gas.
-
Applications of Sputtering:
- Semiconductor Manufacturing: Sputtering is used to deposit thin films of metals and dielectrics onto silicon wafers, essential for creating integrated circuits.
- Optical Coatings: Thin films deposited via sputtering are used to create anti-reflective coatings, mirrors, and filters for optical devices.
- Nanotechnology: Sputtering enables the precise deposition of materials at the nanoscale, crucial for the development of advanced nanomaterials and devices.
-
Advantages of Sputtering:
- Precision: Sputtering allows for the deposition of very thin and uniform layers of material, often just a few nanometers thick.
- Versatility: It can be used with a wide range of materials, including metals, alloys, and ceramics.
- Low Temperature: Since sputtering is a non-thermal process, it is suitable for temperature-sensitive substrates, such as plastics or certain biological materials.
-
Challenges and Considerations:
- Cost: Sputtering equipment and the required vacuum environment can be expensive to set up and maintain.
- Complexity: The process requires careful control of parameters such as pressure, power, and target-substrate distance to achieve desired film properties.
- Material Limitations: Some materials may not sputter efficiently, or the process may introduce impurities if not carefully managed.
In summary, sputtering is a versatile and precise method for depositing thin films of material onto a substrate. Its applications span across various industries, from electronics to optics, and it offers several advantages, including precision and the ability to work with temperature-sensitive materials. However, it also presents challenges such as cost and complexity, which must be carefully managed to achieve optimal results.
Summary Table:
Aspect | Details |
---|---|
Definition | Ejection of atoms from a solid target due to ion bombardment. |
Mechanism | High-energy ions collide with target, dislodging atoms for deposition. |
Types | DC Sputtering, RF Sputtering, Magnetron Sputtering. |
Applications | Semiconductor manufacturing, optical coatings, nanotechnology. |
Advantages | Precision, versatility, low-temperature processing. |
Challenges | High cost, process complexity, material limitations. |
Discover how sputtering can revolutionize your thin-film processes—contact our experts today!