Sputtering is a sophisticated thin film deposition technique widely used in industries such as semiconductors, optical devices, and solar panels. It involves the ejection of atoms from a target material onto a substrate through bombardment by high-energy ions, typically in a vacuum environment. The process is highly controlled and efficient, making it ideal for applications requiring precise thin film coatings. Key steps include ion generation, target atom ejection, transport of sputtered atoms, and condensation on the substrate. Magnetron sputtering, a popular variant, enhances deposition rates and control, making it particularly useful for microelectronics and semiconductor manufacturing.
Key Points Explained:
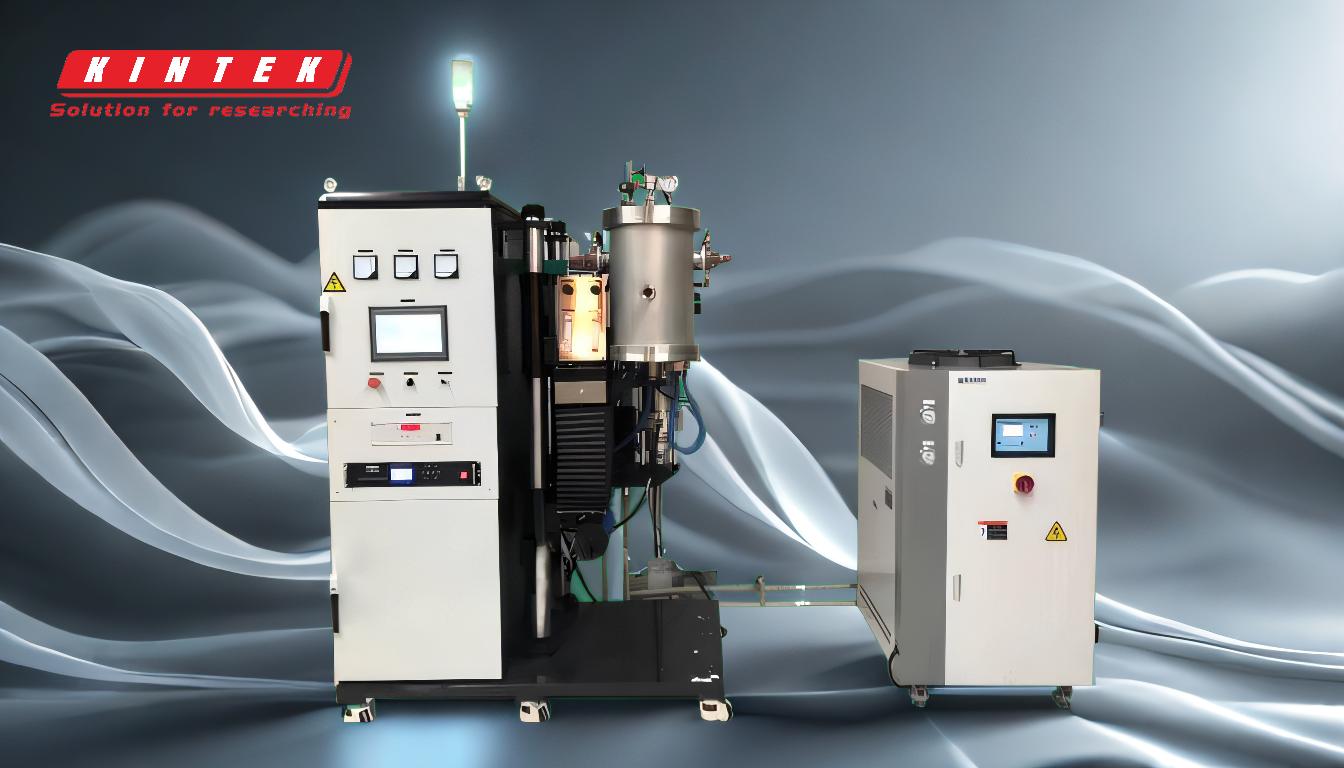
-
Ion Generation and Bombardment:
- The sputtering process begins with the generation of ions, usually from an inert gas like argon, in a vacuum chamber. These ions are accelerated towards a target material by an electrical field.
- When the ions collide with the target, they transfer their kinetic energy, causing atoms from the target to be ejected. This is the fundamental mechanism of sputtering.
-
Ejection of Target Atoms:
- The high-energy ions bombard the target material, dislodging atoms or molecules from its surface. This process is highly efficient and allows for precise control over the deposition of materials.
- The ejected atoms form a vapor stream, which is directed towards the substrate.
-
Transport of Sputtered Atoms:
- The sputtered atoms travel through the vacuum chamber towards the substrate. The vacuum environment ensures minimal interference and contamination, allowing for a clean and uniform deposition.
- This step is crucial for maintaining the integrity and quality of the thin film.
-
Condensation on the Substrate:
- Upon reaching the substrate, the sputtered atoms condense and form a thin film. The substrate can be a silicon wafer, solar panel, or any other material requiring a thin film coating.
- The thickness and uniformity of the film can be precisely controlled by adjusting parameters such as ion energy, target material, and deposition time.
-
Magnetron Sputtering:
- Magnetron sputtering is an advanced variant of the sputtering process. It uses magnetic fields to confine the plasma near the target, increasing the efficiency of ion bombardment and deposition rates.
- This method is particularly useful for depositing dielectric and nitride films in microelectronics and semiconductor applications.
-
Applications and Advantages:
- Sputtering is widely used in the production of semiconductors, optical devices, and solar panels. Its ability to deposit thin films with high precision and uniformity makes it indispensable in these industries.
- The process is versatile, efficient, and continues to evolve with ongoing research, offering improved deposition techniques and materials.
-
Process Control and Optimization:
- The sputtering process can be fine-tuned by adjusting various parameters such as gas pressure, ion energy, and target material. This allows for the optimization of film properties such as thickness, adhesion, and uniformity.
- Advanced techniques like magnetron sputtering further enhance process control, enabling the deposition of complex materials and multilayered structures.
In summary, sputtering is a highly controlled and efficient method for depositing thin films, essential for various high-tech industries. Its ability to precisely control film properties and its versatility make it a cornerstone of modern manufacturing processes.
Summary Table:
Step | Description |
---|---|
Ion Generation and Bombardment | Ions (e.g., argon) are generated and accelerated toward a target material. |
Ejection of Target Atoms | High-energy ions dislodge atoms from the target, creating a vapor stream. |
Transport of Sputtered Atoms | Atoms travel through a vacuum chamber to the substrate, ensuring minimal contamination. |
Condensation on the Substrate | Atoms condense on the substrate, forming a thin film with precise control. |
Magnetron Sputtering | Uses magnetic fields to enhance deposition rates and control for microelectronics. |
Applications | Used in semiconductors, optical devices, and solar panels for precise coatings. |
Process Control | Parameters like gas pressure and ion energy are adjusted to optimize film properties. |
Discover how sputtering can revolutionize your manufacturing process—contact our experts today!