A filter tester is a specialized device used to evaluate the efficiency and performance of various types of filters, such as air filters, respiratory filters, cartridges, and protective garments. These testers are designed to measure how effectively a filter can capture particles or contaminants, ensuring that the filter meets specific performance standards. Filter testers, like those from TSI, are known for their simplicity and reliability in operation, making them essential tools for industries that require high-efficiency filtration, such as healthcare, manufacturing, and environmental monitoring. They help ensure that filters perform as expected, protecting equipment, environments, and individuals from harmful particles.
Key Points Explained:
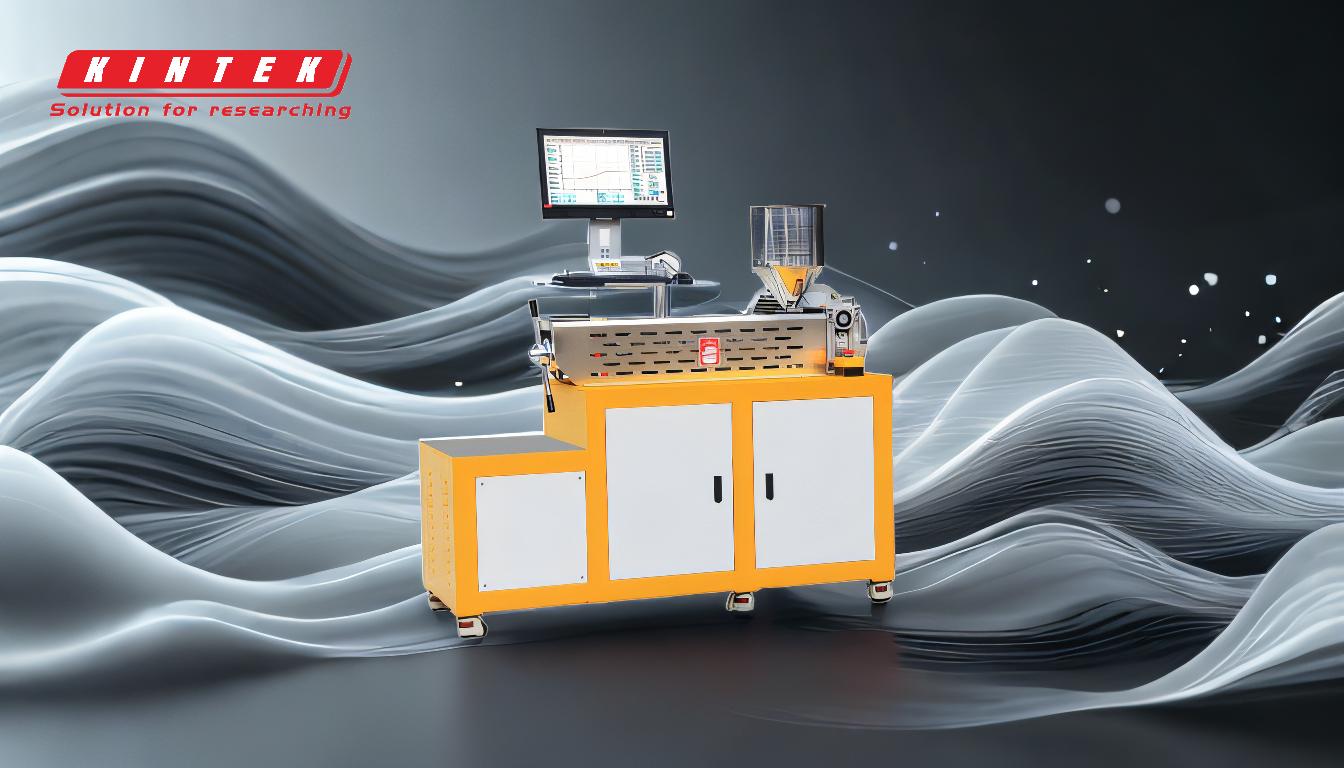
-
Definition and Purpose of a Filter Tester:
- A filter tester is a device used to assess the efficiency of filter media and various types of filters, including high-efficiency air filters, respiratory filters, and protective garments.
- Its primary purpose is to measure how well a filter can capture and retain particles or contaminants, ensuring it meets required performance standards.
-
Types of Filters Tested:
- High and Very High-Efficiency Filters: These are often used in environments requiring stringent air quality control, such as cleanrooms, hospitals, and laboratories.
- Respiratory Filters and Cartridges: These are critical for personal protective equipment (PPE), ensuring they provide adequate protection against harmful airborne particles.
- Protective Garments: These are tested to ensure they offer sufficient filtration for wearers in hazardous environments.
-
Key Features of Filter Testers:
- Simple Operation: Filter testers are designed to be user-friendly, allowing operators to conduct tests efficiently without extensive training.
- Reliability: They provide consistent and accurate results, which are crucial for maintaining quality control in filtration systems.
- Versatility: They can test a wide range of filter types, making them suitable for various industries and applications.
-
Applications of Filter Testers:
- Healthcare: Ensuring that air filters in hospitals and laboratories meet stringent standards to protect patients and staff.
- Manufacturing: Verifying the performance of filters used in industrial processes to protect equipment and maintain product quality.
- Environmental Monitoring: Testing filters used in air quality monitoring systems to ensure accurate detection of pollutants.
-
Importance of Filter Testing:
- Quality Assurance: Regular testing ensures that filters perform as expected, preventing contamination and protecting sensitive environments.
- Regulatory Compliance: Many industries are required to adhere to strict filtration standards, and filter testers help ensure compliance with these regulations.
- Safety: In applications involving respiratory protection, filter testing is critical to safeguarding the health and safety of individuals.
-
Examples of Filter Testers:
- TSI Filter Testers: Known for their simplicity and reliability, TSI filter testers are widely used in various industries to test the efficiency of high-efficiency filters, respiratory filters, and protective garments.
By understanding these key points, equipment and consumable purchasers can make informed decisions about the types of filter testers needed for their specific applications, ensuring optimal performance and compliance with industry standards.
Summary Table:
Aspect | Details |
---|---|
Purpose | Evaluates filter efficiency and ensures compliance with performance standards. |
Types of Filters | High-efficiency, respiratory, protective garments, and more. |
Key Features | Simple operation, reliability, and versatility. |
Applications | Healthcare, manufacturing, environmental monitoring. |
Importance | Ensures quality assurance, regulatory compliance, and safety. |
Example | TSI filter testers for high-efficiency and respiratory filters. |
Ensure your filters meet the highest standards—contact us today for expert guidance!