Mold fitting is a critical step in the mold manufacturing process, performed before mold trial to ensure the material seal-off performance during production. This process aims to prevent defects such as part flash, short shots, or redundant material. Traditionally, mold fitting was done manually by skilled craftsmen, but this method has several limitations, including inefficiency, inconsistency, and reliance on human expertise. Modern advancements are addressing these issues by introducing automated or semi-automated solutions to improve precision and repeatability.
Key Points Explained:
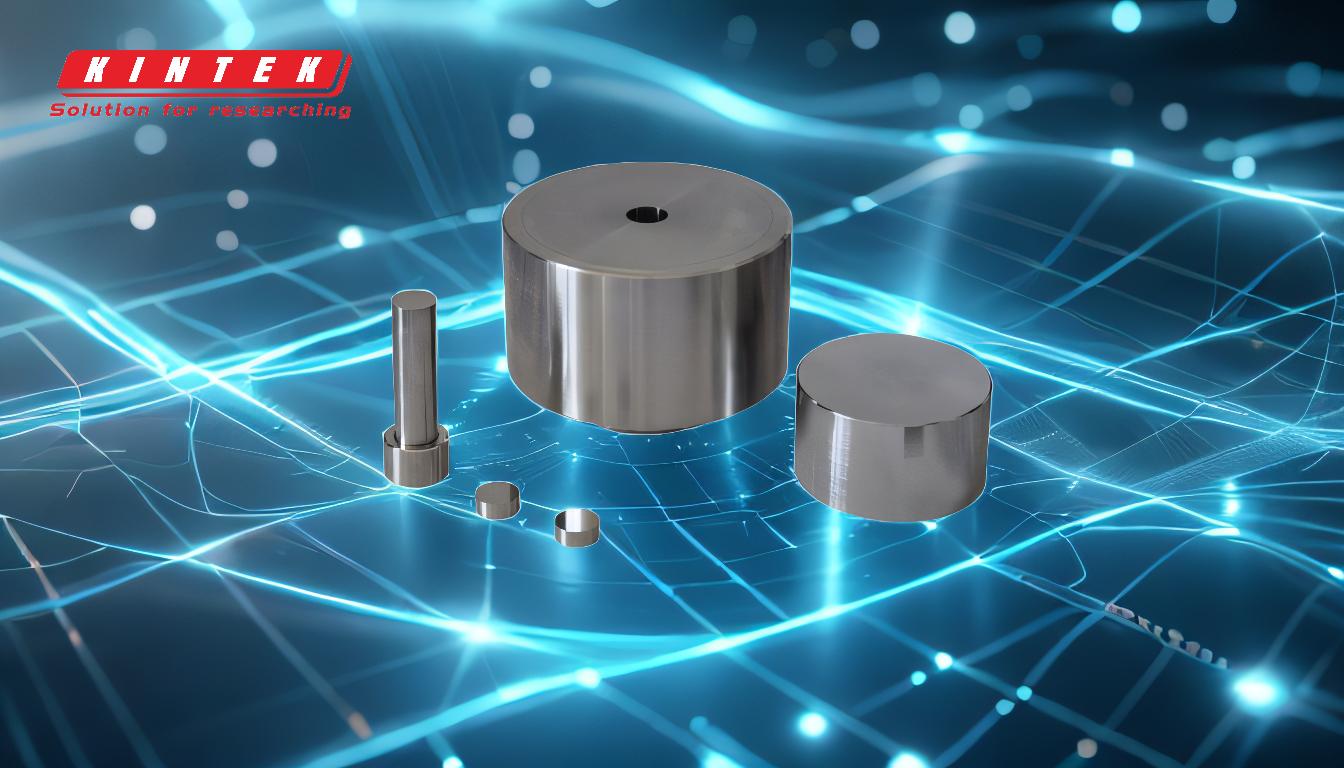
-
Definition and Purpose of Mold Fitting
- Mold fitting is the process of ensuring that the mold components fit together perfectly to create a sealed environment for material injection.
- Its primary purpose is to prevent defects like part flash (excess material leaking out of the mold), short shots (incomplete filling of the mold), or redundant material (unwanted material buildup).
- This step is crucial for achieving high-quality production and minimizing waste.
-
Importance in the Mold Trial Process
- Mold fitting is performed before the mold trial, which is the initial test run of the mold to identify and correct any issues.
- Proper mold fitting ensures that the mold operates as intended during production, reducing the risk of defects and downtime.
- It directly impacts the efficiency and cost-effectiveness of the manufacturing process.
-
Traditional Mold Fitting Methods
- Historically, mold fitting was done manually by skilled craftsmen using hand tools and techniques.
- This method relies heavily on the expertise and experience of the craftsman, making it time-consuming and prone to human error.
- The manual process can lead to inconsistencies in mold performance, affecting the quality of the final product.
-
Challenges with Traditional Methods
- Inefficiency: Manual mold fitting is labor-intensive and can delay the production timeline.
- Inconsistency: Human error can result in variations in mold performance, leading to defects.
- Skill Dependency: The process requires highly skilled workers, which can be a limitation in regions with a shortage of experienced craftsmen.
- Cost: The labor-intensive nature of manual mold fitting increases production costs.
-
Modern Advancements in Mold Fitting
- Automation and technology are transforming mold fitting processes.
- Computer-aided design (CAD) and computer-aided manufacturing (CAM) systems enable precise mold fitting with minimal human intervention.
- Advanced machinery, such as CNC (Computer Numerical Control) machines, ensures consistent and accurate mold fitting.
- These advancements improve efficiency, reduce costs, and enhance the overall quality of the final product.
-
Benefits of Modern Mold Fitting Techniques
- Precision: Automated systems ensure that mold components fit together perfectly, reducing the risk of defects.
- Consistency: Technology-driven processes eliminate human error, resulting in uniform mold performance.
- Efficiency: Automation speeds up the mold fitting process, reducing production time.
- Cost-Effectiveness: While initial investment in technology may be high, the long-term savings in labor and material costs are significant.
-
Applications in Various Industries
- Mold fitting is essential in industries that rely on injection molding, such as automotive, electronics, consumer goods, and medical devices.
- Each industry has specific requirements for mold performance, making precise mold fitting critical for meeting quality standards.
By understanding the importance of mold fitting and the advantages of modern techniques, manufacturers can optimize their production processes, reduce defects, and improve overall product quality.
Summary Table:
Aspect | Details |
---|---|
Definition | Ensures mold components fit perfectly for a sealed material injection environment. |
Purpose | Prevents defects like part flash, short shots, and redundant material. |
Traditional Methods | Manual process by skilled craftsmen; prone to inefficiency and inconsistency. |
Modern Techniques | Automated solutions using CAD, CAM, and CNC for precision and repeatability. |
Benefits | Improved precision, consistency, efficiency, and cost-effectiveness. |
Applications | Automotive, electronics, consumer goods, and medical devices. |
Optimize your mold fitting process with advanced solutions—contact us today for expert guidance!