Sputtering gas is a critical component in the sputtering process, a widely used technique in thin-film deposition. It involves the use of a noble gas, typically argon, to create a plasma that bombards a target material, causing atoms to be ejected and deposited onto a substrate. This process is essential in industries such as semiconductor manufacturing, optics, and coatings. The choice of sputtering gas, along with the type of sputtering process and power source, significantly influences the efficiency and quality of the deposition. Understanding the role of sputtering gas and its interaction with the target material and substrate is key to optimizing thin-film production.
Key Points Explained:
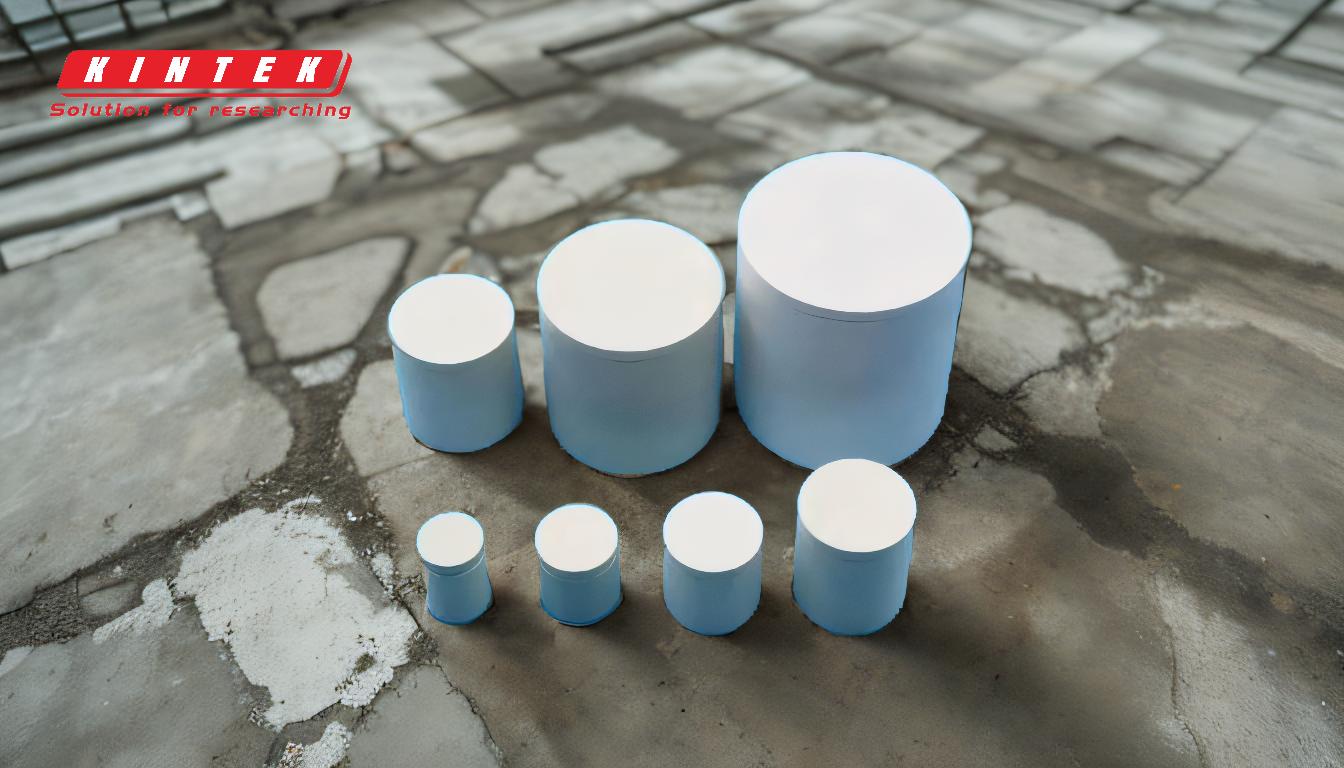
-
Definition of Sputtering Gas:
- Sputtering gas is typically a noble gas, such as argon, used in the sputtering process to create a plasma. This plasma is directed at a target material, causing atoms to be ejected and deposited onto a substrate. The inert nature of noble gases ensures minimal chemical interaction with the target material, making them ideal for this purpose.
-
Types of Sputtering Processes:
- Several sputtering processes exist, including ion beam sputtering, diode sputtering, and magnetron sputtering. Each method has its unique advantages and is chosen based on the specific requirements of the thin-film deposition. For instance, magnetron sputtering is known for its high deposition rates and is commonly used in industrial applications.
-
Role of Sputtering Gas in the Process:
- The sputtering gas is ionized to form a plasma, which is then directed at the target material. The impact of the plasma ions on the target causes atoms to be ejected in a process known as sputtering. These ejected atoms travel through the vacuum chamber and deposit onto the substrate, forming a thin film.
-
Power Sources in Sputtering:
- Various power sources can be used in sputtering, including DC (Direct Current), RF (Radio Frequency), Pulsed DC, MF (Medium Frequency), AC (Alternating Current), and HIPIMS (High-Power Impulse Magnetron Sputtering). The choice of power source affects the energy and efficiency of the sputtering process. For example, DC sputtering is cost-effective and suitable for conductive materials, while RF sputtering is used for insulating materials.
-
Precursor Gas Method:
- In some sputtering processes, a precursor gas method is employed. This involves providing a metal-containing precursor to an activation zone, where it is activated to form an activated precursor gas. This gas is then moved to a reaction chamber, where it undergoes a cyclical deposition process, alternately adsorbing with a reducing gas onto the substrate to form a film.
-
Deposition Mechanism:
- Deposition occurs when the ejected atoms from the target material travel through the vacuum chamber and adhere to the substrate. The process is controlled by opening a shutter to expose the sample to the free atoms. The collision cascade triggered by the plasma ensures that the entire substrate surface is coated uniformly.
-
Applications of Sputtering Gas:
- Sputtering gas is used in various applications, including the production of thin films for semiconductors, optical coatings, and decorative finishes. The ability to precisely control the deposition process makes sputtering an essential technique in modern manufacturing.
Understanding the role of sputtering gas and its interaction with the target material and substrate is crucial for optimizing the sputtering process. By selecting the appropriate sputtering gas, power source, and deposition method, manufacturers can achieve high-quality thin films with desired properties.
Summary Table:
Key Aspect | Details |
---|---|
Definition | Noble gas (e.g., argon) used to create plasma for thin-film deposition. |
Types of Sputtering | Ion beam, diode, magnetron sputtering, each with unique advantages. |
Role in Process | Ionized gas forms plasma, ejects target atoms, and deposits them on a substrate. |
Power Sources | DC, RF, Pulsed DC, MF, AC, HIPIMS—each suited for specific materials. |
Applications | Semiconductors, optical coatings, decorative finishes, and more. |
Optimize your thin-film deposition process with the right sputtering gas—contact our experts today!