Target poisoning in sputtering, particularly in magnetron sputtering, is a phenomenon where the deposition rate of the thin film decreases due to the absorption or nitridation of reactive gases (like nitrogen) on the target surface. This occurs when the partial pressure of reactive gases increases, leading to the formation of compounds on the target surface, which reduces its sputtering efficiency. As a result, fewer target atoms are ejected, and the thin film growth rate on the substrate decreases. This issue is particularly prevalent in reactive sputtering processes, where reactive gases are intentionally introduced to form compound films. To mitigate target poisoning, modifications such as increasing ionization rates or optimizing gas flow are often employed.
Key Points Explained:
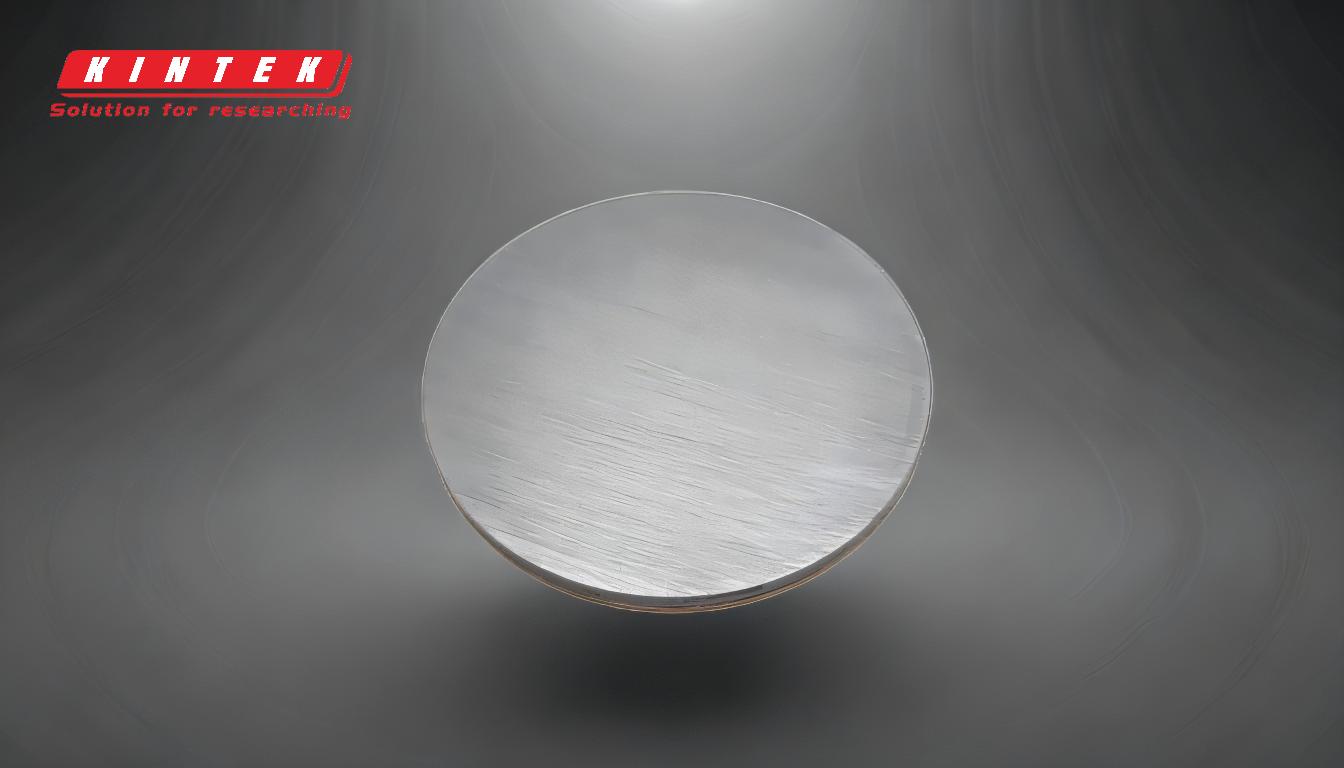
-
Definition of Target Poisoning:
- Target poisoning refers to the decrease in the deposition rate of thin films during sputtering due to the absorption or chemical reaction of reactive gases (e.g., nitrogen) on the target surface.
- This phenomenon is most commonly observed in reactive sputtering processes, where reactive gases are used to form compound films like nitrides or oxides.
-
Mechanism of Target Poisoning:
- When the partial pressure of a reactive gas (e.g., nitrogen) increases, the gas molecules are absorbed onto the target surface.
- This absorption leads to the formation of a compound layer (e.g., nitrides) on the target surface.
- The compound layer reduces the number of free target atoms available for sputtering, as the target material becomes less conductive or less reactive.
- As a result, fewer target atoms are ejected, and the deposition rate on the substrate decreases.
-
Impact on Sputtering Process:
- Reduced Deposition Rate: The primary consequence of target poisoning is a significant reduction in the thin film growth rate on the substrate.
- Increased Reactive Gas Availability: As the target surface becomes poisoned, more reactive gas is available to further poison the target, creating a feedback loop that exacerbates the problem.
- Changes in Film Composition: The chemical composition of the deposited film may also change, as the target surface becomes less effective at supplying the desired material.
-
Types of Sputtering Affected:
- Target poisoning is particularly relevant in reactive sputtering, where reactive gases are introduced to form compound films.
- It can also occur in magnetron sputtering, especially when nitrogen or oxygen is used as a reactive gas.
-
Mitigation Strategies:
- Increasing Ionization: By increasing the ionization of the reactive gas, the efficiency of the sputtering process can be improved, reducing the likelihood of target poisoning.
- Optimizing Gas Flow: Controlling the flow rate and partial pressure of the reactive gas can help maintain a balance between film formation and target poisoning.
- Pulsed Sputtering: Techniques like pulsed DC sputtering can help reduce target poisoning by periodically cleaning the target surface.
- Target Rotation: In some systems, rotating the target can help distribute the reactive gas more evenly, reducing localized poisoning.
-
Relevance to Equipment and Consumable Purchasers:
- For purchasers of sputtering equipment and consumables, understanding target poisoning is crucial for selecting the right system and materials.
- Systems with advanced ionization and gas flow control features may be more effective in mitigating target poisoning.
- Consumables like targets should be chosen based on their resistance to poisoning, especially for reactive sputtering applications.
-
Comparison with Other Sputtering Techniques:
- In DC diode sputtering, target poisoning is less common because reactive gases are not typically used.
- RF sputtering can be more resistant to target poisoning, as the alternating field can help clean the target surface.
- HiPIMS (High Power Impulse Magnetron Sputtering) is another technique that can reduce target poisoning by providing high-energy pulses that improve ionization and target cleaning.
-
Conclusion:
- Target poisoning is a significant challenge in reactive and magnetron sputtering, leading to reduced deposition rates and changes in film composition.
- By understanding the mechanisms and implementing mitigation strategies, equipment and consumable purchasers can optimize their sputtering processes for better performance and film quality.
Summary Table:
Aspect | Details |
---|---|
Definition | Decreased deposition rate due to reactive gas absorption on the target. |
Mechanism | Reactive gases form compounds on the target, reducing sputtering efficiency. |
Impact | Reduced deposition rate, changes in film composition. |
Affected Techniques | Reactive sputtering, magnetron sputtering. |
Mitigation Strategies | Increase ionization, optimize gas flow, pulsed sputtering, target rotation. |
Optimize your sputtering process and minimize target poisoning—contact our experts today for tailored solutions!