Rotary pumps and centrifugal pumps are both widely used in various industries, but they have distinct advantages and limitations. Rotary pumps, such as gear, vane, or lobe pumps, are known for their ability to provide a steady, low-pulsation flow, making them ideal for applications requiring precise fluid delivery. In contrast, centrifugal pumps are better suited for high-flow, low-pressure applications but may struggle with viscous fluids or situations requiring consistent flow rates. The primary advantage of rotary pumps over centrifugal pumps lies in their ability to handle viscous fluids, provide consistent flow, and maintain efficiency in low-flow, high-pressure scenarios. Below, we explore these advantages in detail.
Key Points Explained:
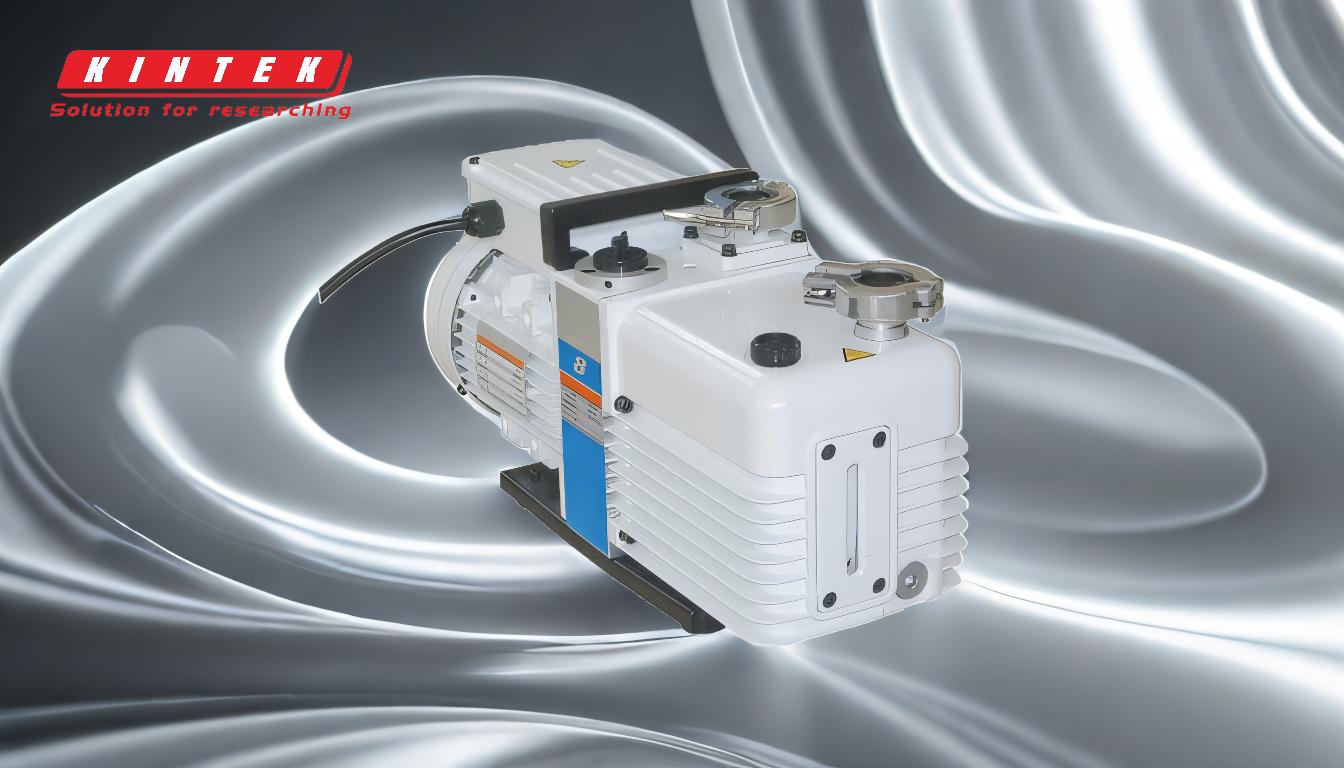
-
Steady, Low-Pulsation Flow:
- Rotary pumps, such as gear or vane pumps, deliver fluids with minimal pulsation, ensuring a smooth and continuous flow. This is particularly beneficial in applications like chemical dosing, lubrication systems, or hydraulic systems, where inconsistent flow can lead to inefficiencies or equipment damage.
- Centrifugal pumps, on the other hand, rely on impeller rotation to move fluid, which can result in pulsating flow, especially at lower speeds or when handling viscous fluids.
-
Efficiency with Viscous Fluids:
- Rotary pumps excel at handling viscous fluids, such as oils, syrups, or adhesives, because their design allows for efficient displacement of thick liquids without significant energy loss.
- Centrifugal pumps struggle with viscous fluids because the impeller's ability to transfer energy to the fluid diminishes as viscosity increases, leading to reduced efficiency and flow rates.
-
Self-Priming Capability:
- Many rotary pumps are self-priming, meaning they can create a vacuum to draw fluid into the pump without external assistance. This makes them ideal for applications where the pump is located above the fluid source.
- Centrifugal pumps typically require the pump casing and suction line to be filled with fluid before operation, limiting their use in self-priming scenarios.
-
High-Pressure Capability:
- Rotary pumps can generate high pressures even at low flow rates, making them suitable for hydraulic systems, fuel injection, or other high-pressure applications.
- Centrifugal pumps are better suited for high-flow, low-pressure applications and may require multiple stages to achieve high pressures, increasing complexity and cost.
-
Compact Design and Versatility:
- Rotary pumps are often more compact and can be designed to handle a wide range of fluids, including those with varying viscosities or containing particulates (within limits).
- Centrifugal pumps are generally larger and less versatile when it comes to handling fluids with varying characteristics.
-
Lower Maintenance in Certain Applications:
- Rotary pumps, particularly those with fewer moving parts (e.g., gear pumps), tend to have lower maintenance requirements in applications where abrasive contaminants are not present.
- Centrifugal pumps may require more frequent maintenance due to wear on impellers and seals, especially when handling abrasive or corrosive fluids.
-
Limitations of Rotary Pumps:
- While rotary pumps offer many advantages, they are not suitable for handling abrasive fluids, as the small clearances between the rotor and housing can erode over time. Centrifugal pumps, with their more robust impeller design, may perform better in such scenarios.
- Rotary pumps are also generally more expensive than centrifugal pumps, which can be a consideration for cost-sensitive applications.
In summary, rotary pumps provide significant advantages over centrifugal pumps in applications requiring steady flow, high-pressure capabilities, and efficient handling of viscous fluids. However, their limitations in handling abrasive media and higher initial cost should be carefully considered when selecting the appropriate pump for a specific application.
Summary Table:
Feature | Rotary Pumps | Centrifugal Pumps |
---|---|---|
Flow Characteristics | Steady, low-pulsation flow ideal for precise delivery | Pulsating flow, especially with viscous fluids |
Viscous Fluid Handling | Efficient displacement of thick fluids (e.g., oils, syrups) | Struggles with viscous fluids, reduced efficiency |
Self-Priming | Capable of self-priming, suitable for above-fluid-source applications | Requires pre-filled casing and suction line |
Pressure Capability | High-pressure generation at low flow rates | Suited for high-flow, low-pressure; multi-stage needed for high pressure |
Design and Versatility | Compact, versatile for varying viscosities and particulates | Larger, less versatile for diverse fluid characteristics |
Maintenance | Lower maintenance in non-abrasive applications | Higher maintenance due to wear on impellers and seals |
Cost | Higher initial cost | Generally more cost-effective |
Limitations | Not suitable for abrasive fluids; higher cost | Better for abrasive fluids; less efficient with viscous fluids |
Need help choosing the right pump for your application? Contact our experts today to find the best solution!