Sputtering targets are materials used in thin film deposition processes, such as in semiconductor manufacturing or coating applications. Arcing in sputtering targets refers to the formation of electrical discharges or sparks between the target material and the substrate during the sputtering process. This phenomenon can negatively impact the quality of the deposited film, cause damage to the target, and reduce the efficiency of the process. The issue of arcing was addressed in the 1970s by proposing the use of a low-frequency AC power supply instead of a standard DC unit. This solution helped mitigate arcing by adjusting the frequency based on the dielectric properties of the insulating film being deposited.
Key Points Explained:
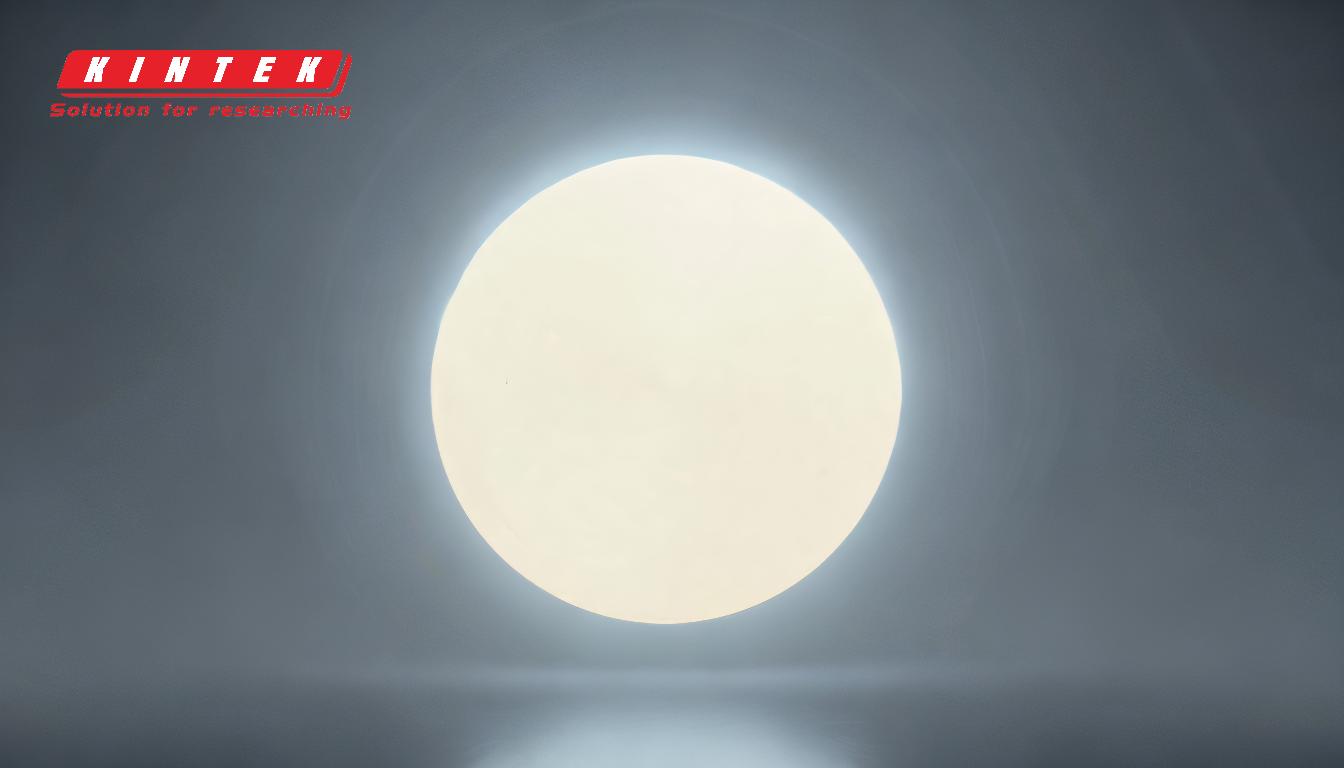
-
Definition of Arcing in Sputtering Targets:
- Arcing occurs when an electrical discharge or spark forms between the sputtering target and the substrate during the deposition process.
- This discharge is caused by the buildup of charge on insulating layers or contaminants on the target surface, leading to localized breakdowns in the electric field.
-
Impact of Arcing:
- Film Quality: Arcing can create defects in the deposited film, such as pinholes, uneven thickness, or contamination.
- Target Damage: Repeated arcing can erode the target surface, reducing its lifespan and increasing operational costs.
- Process Efficiency: Arcing disrupts the uniformity of the sputtering process, leading to inefficiencies and inconsistent results.
-
Historical Solution: Low-Frequency AC Power Supply:
- In the 1970s, researchers proposed using a low-frequency AC power supply to address arcing issues.
- The AC supply alternates the polarity of the voltage applied to the target, preventing the buildup of charge on insulating layers.
- The frequency of the AC supply (ranging from 400 to 60,000 Hz) is tailored to the dielectric constant of the insulating film being deposited.
-
How AC Power Mitigates Arcing:
- Charge Neutralization: Alternating the polarity ensures that charges do not accumulate on the target surface, reducing the likelihood of arcing.
- Improved Film Uniformity: By minimizing arcing, the AC power supply helps achieve a more uniform and defect-free film.
- Enhanced Target Longevity: Reduced arcing minimizes damage to the target, extending its usable life.
-
Considerations for Equipment and Consumable Purchasers:
- Power Supply Compatibility: When purchasing sputtering equipment, ensure the power supply supports AC operation with adjustable frequency settings.
- Target Material Selection: Choose targets with low contamination levels and high purity to further reduce the risk of arcing.
- Process Optimization: Work with suppliers to determine the optimal frequency range for specific dielectric films to maximize performance and minimize arcing.
By understanding the causes and solutions for arcing in sputtering targets, equipment and consumable purchasers can make informed decisions to improve process efficiency, film quality, and overall equipment longevity.
Summary Table:
Aspect | Details |
---|---|
Definition of Arcing | Electrical discharge between target and substrate during sputtering. |
Impact on Film Quality | Causes defects like pinholes, uneven thickness, and contamination. |
Impact on Target | Erodes target surface, reducing lifespan and increasing costs. |
Impact on Efficiency | Disrupts process uniformity, leading to inefficiencies. |
Solution | Low-frequency AC power supply (400–60,000 Hz) neutralizes charge buildup. |
Key Considerations | Power supply compatibility, target material purity, and process optimization. |
Ready to optimize your sputtering process? Contact us today for expert guidance and solutions!