Stainless steel (SS) reactors are widely used in chemical processes due to their durability, corrosion resistance, and ability to withstand high pressures and temperatures. The design pressure of an SS reactor depends on several factors, including the grade of stainless steel, reactor design, intended application, and compliance with industry standards. While the provided references do not specify exact design pressure values, they emphasize the importance of material selection and integrity checks for safe operation. Below, the key points related to the design pressure of SS reactors are explained in detail.
Key Points Explained:
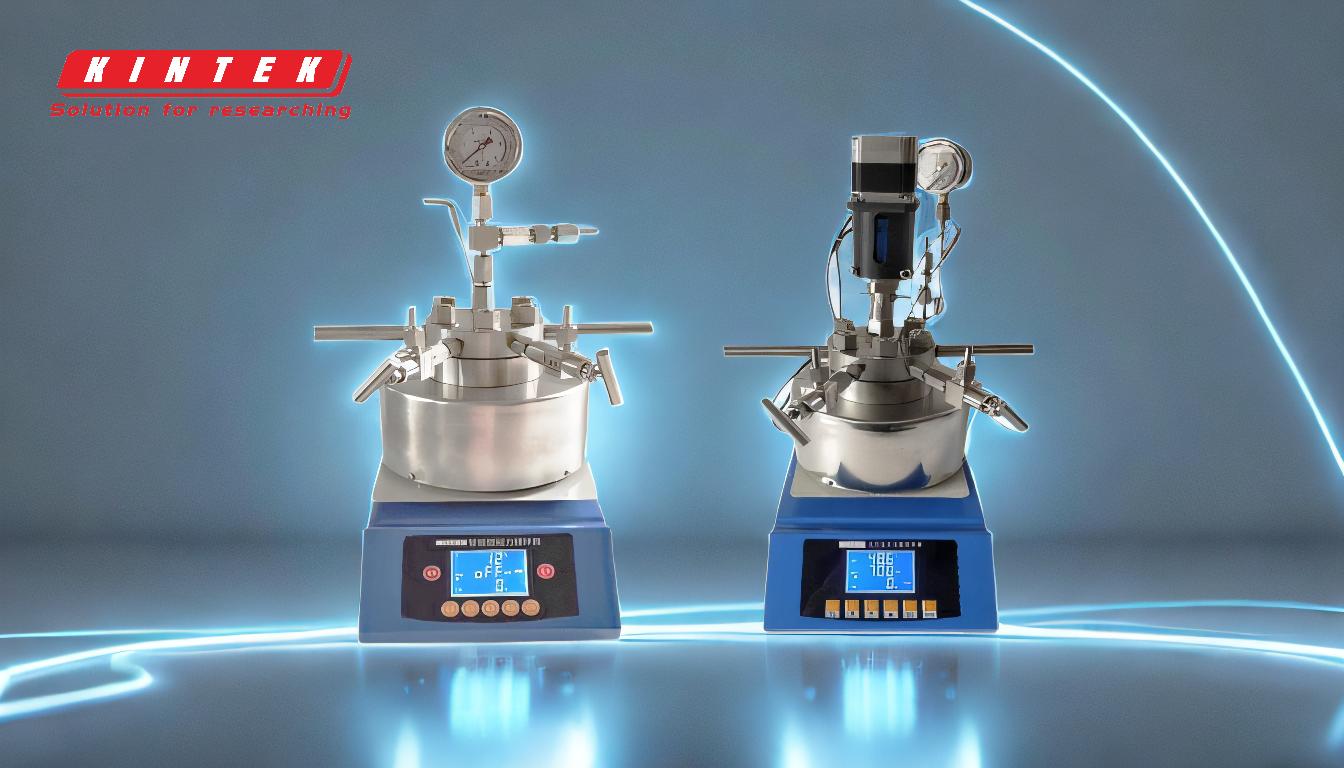
-
Material Grade and Chemical Resistance
- The design pressure of an SS reactor is influenced by the grade of stainless steel used. Common grades include 304, 316, and 316L, each with varying chemical resistance and mechanical properties.
- Higher-grade stainless steels (e.g., 316L) offer better corrosion resistance, which is critical for maintaining structural integrity under high-pressure conditions.
- Users must ensure the selected grade is chemically resistant to the reactants and products involved in the intended reactions.
-
Reactor Design and Construction
- The design pressure is determined by the reactor's structural design, including wall thickness, shape, and reinforcement.
- Reactors are typically cylindrical to evenly distribute pressure and minimize stress concentrations.
- The design must comply with engineering standards such as ASME (American Society of Mechanical Engineers) or PED (Pressure Equipment Directive) to ensure safety and reliability.
-
Temperature and Pressure Relationship
- The design pressure is closely tied to the operating temperature. Higher temperatures can reduce the material's strength, requiring a lower design pressure.
- SS reactors often include temperature control systems to maintain safe operating conditions.
-
Integrity of Seals and Joints
- O-rings, gaskets, and joints must be made of materials compatible with the reactor's operating conditions.
- Regular integrity checks are essential to prevent leaks or failures under high pressure.
-
Application-Specific Considerations
- The design pressure varies depending on the application, such as pharmaceutical synthesis, petrochemical processing, or laboratory-scale reactions.
- For example, laboratory reactors may have lower design pressures (e.g., 10-20 bar) compared to industrial reactors, which can withstand pressures exceeding 100 bar.
-
Compliance with Standards
- Design pressure is determined based on compliance with industry standards and safety regulations.
- Standards such as ASME Section VIII for pressure vessels provide guidelines for calculating maximum allowable working pressure (MAWP).
-
Manufacturer Specifications
- The design pressure is ultimately specified by the manufacturer based on the reactor's intended use and material properties.
- Users should consult the manufacturer's documentation for precise design pressure values.
In summary, the design pressure of an SS reactor is influenced by material grade, reactor design, operating conditions, and compliance with standards. Users must ensure proper material selection, integrity checks, and adherence to safety guidelines to operate the reactor safely and effectively.
Summary Table:
Factor | Description |
---|---|
Material Grade | Higher grades like 316L offer better corrosion resistance and strength. |
Reactor Design | Cylindrical shape, wall thickness, and reinforcement ensure even pressure distribution. |
Temperature Relationship | Higher temperatures reduce material strength, requiring lower design pressure. |
Seals and Joints | Must be compatible with operating conditions; regular integrity checks are vital. |
Application-Specific Needs | Lab reactors (10-20 bar) vs. industrial reactors (100+ bar). |
Compliance with Standards | Adherence to ASME Section VIII or PED ensures safety and reliability. |
Manufacturer Specifications | Manufacturer provides precise design pressure based on intended use. |
Need help selecting the right stainless steel reactor for your application? Contact our experts today!