Batch reactors and semi-batch reactors are both widely used in chemical and industrial processes, but they differ significantly in their operation, design, and applications. Batch reactors involve loading all reactants at once, allowing the reaction to proceed over a set period, and then removing the products. Semi-batch reactors, on the other hand, combine elements of batch and continuous reactors, where one reactant is loaded initially, and another is added gradually during the reaction. This difference in operation leads to variations in control, efficiency, and suitability for specific applications. Below, we explore the key differences between these two reactor types in detail.
Key Points Explained:
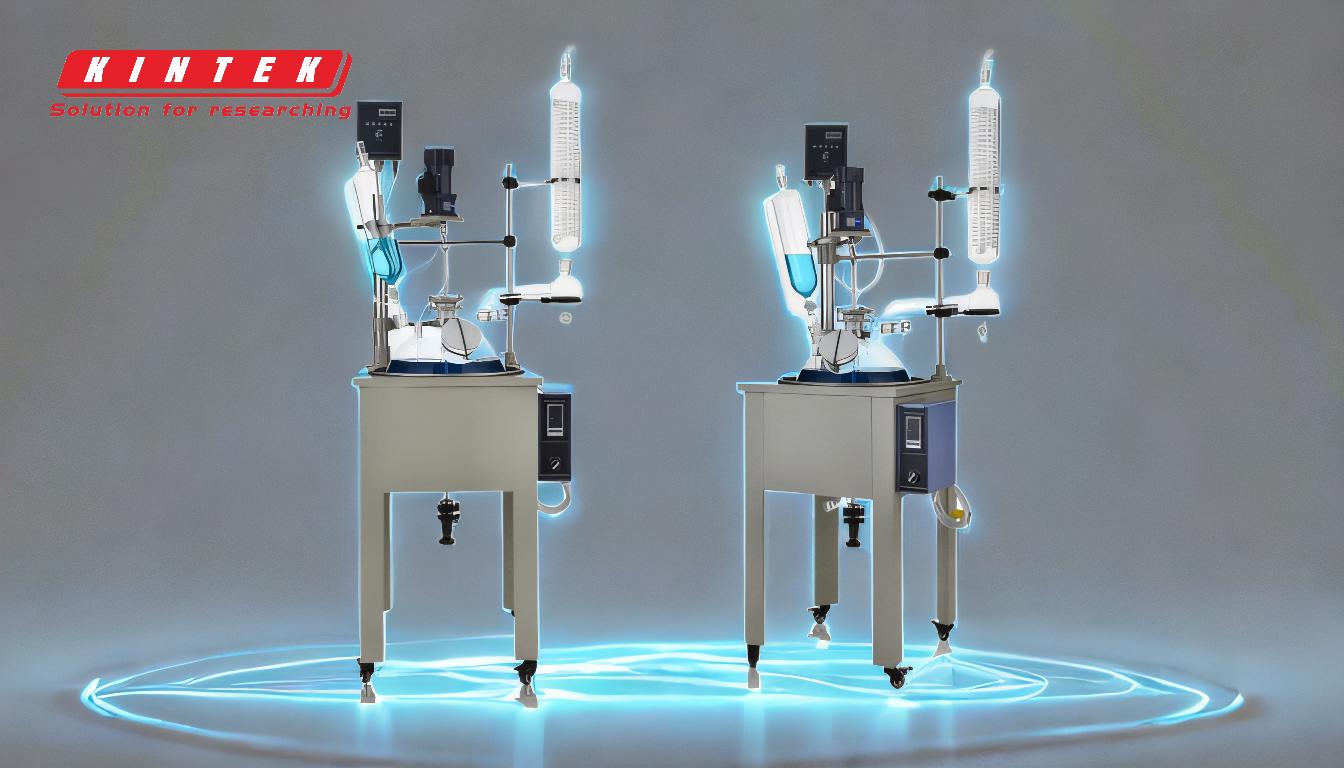
-
Operational Mechanism:
-
Batch Reactor: In a batch reactor, all reactants, catalysts, and necessary components are added to the reactor at the start. The reactor is then sealed, and the reaction proceeds over a predetermined time, often with heating or cooling. Once the reaction is complete, the products are removed, and the reactor is cleaned for the next batch.
- Example: A reaction might involve mixing reactants and heating them at 50°C for 5 hours before extracting the final product.
-
Semi-batch Reactor: A semi-batch reactor operates by loading one reactant initially and then gradually introducing a second reactant during the reaction. This allows for better control over reaction kinetics and heat generation, as the addition rate can be adjusted based on the reaction progress.
- Example: In a gas-liquid reaction, the liquid might be loaded first, and the gas is slowly bubbled into the reactor over time.
-
Batch Reactor: In a batch reactor, all reactants, catalysts, and necessary components are added to the reactor at the start. The reactor is then sealed, and the reaction proceeds over a predetermined time, often with heating or cooling. Once the reaction is complete, the products are removed, and the reactor is cleaned for the next batch.
-
Control and Flexibility:
- Batch Reactor: Batch reactors offer limited control once the reaction has started, as all reactants are present from the beginning. This can lead to challenges in managing exothermic reactions or reactions with complex kinetics.
- Semi-batch Reactor: Semi-batch reactors provide greater control over the reaction process. By gradually adding one reactant, operators can manage heat release, reaction rates, and product formation more effectively. This makes semi-batch reactors ideal for reactions that are highly exothermic or require precise control.
-
Applications:
- Batch Reactor: Batch reactors are versatile and widely used in industries such as pharmaceuticals, food processing, and specialty chemicals. They are suitable for small-scale production, research, and development, where flexibility and adaptability are more critical than high throughput.
- Semi-batch Reactor: Semi-batch reactors are particularly useful in laboratory settings and processes involving gas-liquid or liquid-liquid reactions. They are also employed in industries where controlled addition of reactants is necessary to achieve desired product quality or safety.
-
Efficiency and Scalability:
- Batch Reactor: Batch reactors are less efficient for large-scale production due to the downtime between batches for loading, reaction, and cleaning. However, they are easy to scale up or down for different production volumes.
- Semi-batch Reactor: Semi-batch reactors offer better efficiency for certain processes, as the controlled addition of reactants can reduce waste and improve yields. However, they may require more complex equipment and monitoring systems compared to batch reactors.
-
Design and Complexity:
- Batch Reactor: Batch reactors are relatively simple in design, requiring minimal modifications for different applications. They are often chosen for their ease of use and low initial cost.
- Semi-batch Reactor: Semi-batch reactors are more complex, as they require systems for controlled addition of reactants and monitoring of reaction parameters. This complexity can increase the initial investment but may be justified by improved process control and product quality.
-
Safety Considerations:
- Batch Reactor: In batch reactors, safety concerns arise from the simultaneous presence of all reactants, which can lead to rapid heat generation or pressure buildup in exothermic reactions.
- Semi-batch Reactor: Semi-batch reactors mitigate some safety risks by allowing gradual addition of reactants, which helps manage heat and pressure more effectively. This makes them safer for reactions with high energy release.
In summary, the choice between batch and semi-batch reactors depends on the specific requirements of the process, including the need for control, safety, efficiency, and scalability. Batch reactors are ideal for simple, versatile applications, while semi-batch reactors excel in processes requiring precise control and gradual reactant addition.
Summary Table:
Aspect | Batch Reactor | Semi-Batch Reactor |
---|---|---|
Operation | All reactants loaded at once; reaction proceeds over a set period. | One reactant loaded initially; second reactant added gradually during the reaction. |
Control | Limited control once reaction starts. | Greater control over reaction kinetics and heat release. |
Applications | Pharmaceuticals, food processing, specialty chemicals. | Gas-liquid reactions, laboratory settings, controlled addition processes. |
Efficiency | Less efficient for large-scale production due to downtime. | More efficient for certain processes with reduced waste and improved yields. |
Design Complexity | Simple design, low initial cost. | More complex, requires controlled addition and monitoring systems. |
Safety | Higher risk of rapid heat/pressure buildup in exothermic reactions. | Safer due to gradual reactant addition, better heat/pressure management. |
Need help choosing the right reactor for your process? Contact our experts today!