Blown film and extruded film are two distinct manufacturing processes used to produce plastic films, each with unique characteristics and applications. Blown film involves extruding a thick layer of plastic through a circular die, followed by inflating it into a large bubble using air. The bubble's size, along with the original diameter and thickness of the extruded tube, determines the final thickness and properties of the film. Extruded film, on the other hand, typically refers to flat films produced by forcing molten plastic through a flat die, resulting in a more uniform thickness and surface. The choice between these methods depends on the desired film properties, such as thickness, strength, and flexibility, as well as the specific application requirements.
Key Points Explained:
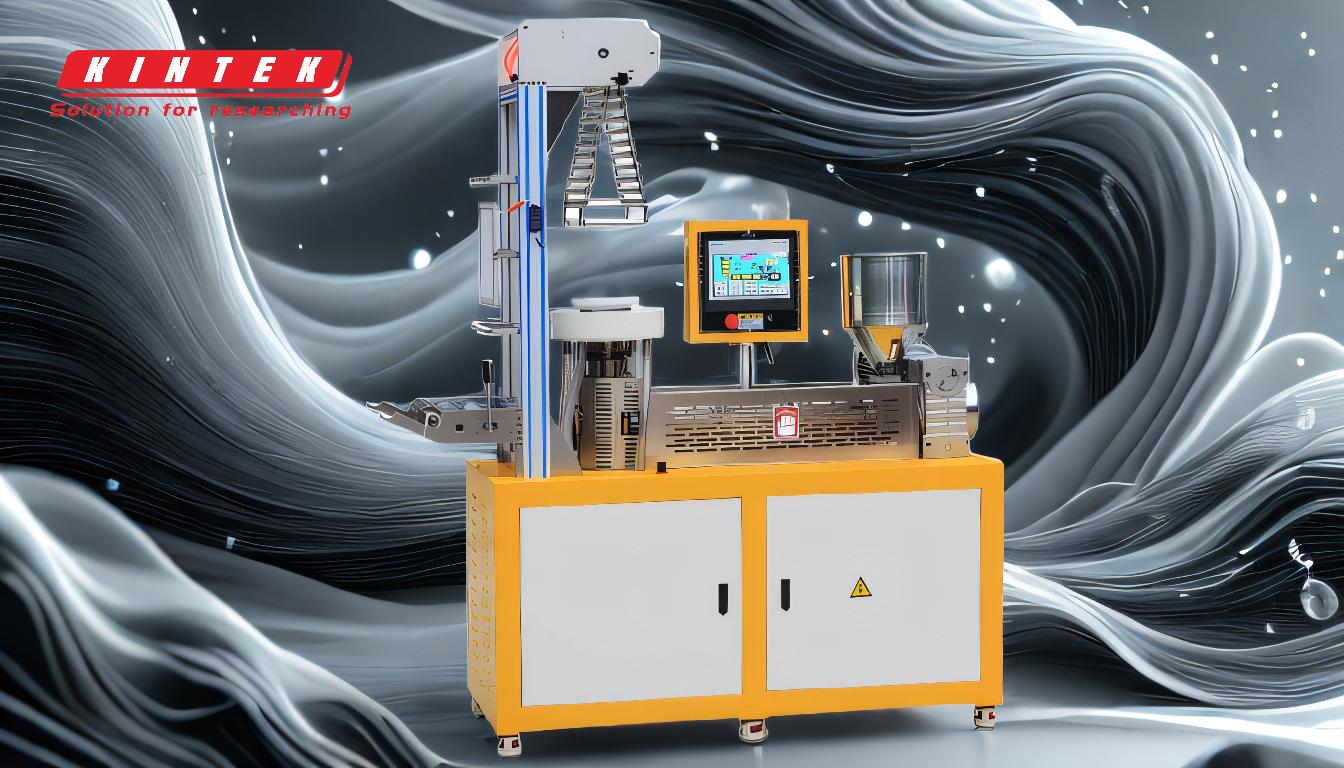
-
Manufacturing Process:
- Blown Film: This process involves extruding molten plastic through a circular die, followed by inflating it into a large bubble using air. The bubble is then cooled and collapsed to form a flat film. The process allows for the production of films with varying thicknesses and properties, depending on the size of the bubble and the extrusion parameters.
- Extruded Film: In this process, molten plastic is forced through a flat die, resulting in a flat film with a more uniform thickness. The film is then cooled and wound onto rolls. This method is typically used for producing films with consistent thickness and surface properties.
-
Film Properties:
- Blown Film: The blown film process allows for the production of films with a wide range of properties, including varying thicknesses, strengths, and flexibility. The film can be made thicker or thinner by adjusting the size of the bubble and the extrusion parameters. Additionally, blown films often have better mechanical properties, such as higher tear strength and puncture resistance, due to the orientation of the polymer chains during the blowing process.
- Extruded Film: Extruded films are known for their uniform thickness and surface properties. They are typically used in applications where consistency and precision are critical, such as in packaging or laminating. The flat die extrusion process also allows for the production of films with specific surface finishes, such as glossy or matte.
-
Applications:
- Blown Film: Blown films are commonly used in applications where flexibility and strength are important, such as in the production of plastic bags, shrink films, and agricultural films. The process is also suitable for producing films with specialized properties, such as barrier films for food packaging.
- Extruded Film: Extruded films are often used in applications where uniformity and precision are required, such as in the production of laminating films, industrial films, and packaging films. The flat die extrusion process is also used to produce films with specific surface properties, such as those used in printing or labeling.
-
Advantages and Disadvantages:
-
Blown Film:
- Advantages: The blown film process allows for the production of films with a wide range of properties, including varying thicknesses and strengths. It is also more cost-effective for producing large quantities of film.
- Disadvantages: The process can be more complex and require more precise control of the extrusion parameters. Additionally, the films produced may have more variability in thickness and properties compared to extruded films.
-
Extruded Film:
- Advantages: The flat die extrusion process produces films with a more uniform thickness and surface properties. It is also easier to control the extrusion parameters, resulting in more consistent film properties.
- Disadvantages: The process may be less flexible in terms of producing films with varying thicknesses and properties. Additionally, it may be more expensive for producing large quantities of film.
-
Blown Film:
-
Equipment and Consumables:
- Blown Film: The equipment required for blown film production includes a circular die, air ring, bubble collapsing frame, and cooling circulator. The consumables include the plastic resin and any additives used to modify the film properties.
- Extruded Film: The equipment required for extruded film production includes a flat die, cooling rolls, and winding system. The consumables include the plastic resin and any additives used to modify the film properties.
In summary, the choice between blown and extruded film depends on the specific requirements of the application, including the desired film properties, production volume, and cost considerations. Both processes have their advantages and disadvantages, and the decision should be based on a thorough evaluation of these factors.
Summary Table:
Aspect | Blown Film | Extruded Film |
---|---|---|
Manufacturing | Extruded through a circular die, inflated into a bubble, then collapsed. | Forced through a flat die, cooled, and wound into rolls. |
Film Properties | Varying thickness, high strength, flexibility, and better mechanical properties. | Uniform thickness, consistent surface finishes (glossy/matte). |
Applications | Plastic bags, shrink films, agricultural films, barrier films. | Laminating films, industrial films, packaging films, printing films. |
Advantages | Wide range of properties, cost-effective for large volumes. | Uniform thickness, precise control, consistent properties. |
Disadvantages | Complex process, variability in thickness and properties. | Less flexibility, potentially higher costs for large volumes. |
Need help choosing the right film production method? Contact our experts today for tailored solutions!