Monolayer and multilayer films differ primarily in their structure, functionality, and application suitability. Monolayer films are single-layer materials that offer cost-effective solutions for basic needs like puncture resistance and printability. They are simpler to produce and are ideal for applications where advanced barrier properties or mechanical strength are not required. Multilayer films, on the other hand, consist of multiple layers, each contributing specific properties such as superior barrier performance, enhanced mechanical strength, and specialized functionalities. These films are more complex to manufacture but are essential for applications demanding higher performance, such as food packaging, medical supplies, and industrial uses.
Key Points Explained:
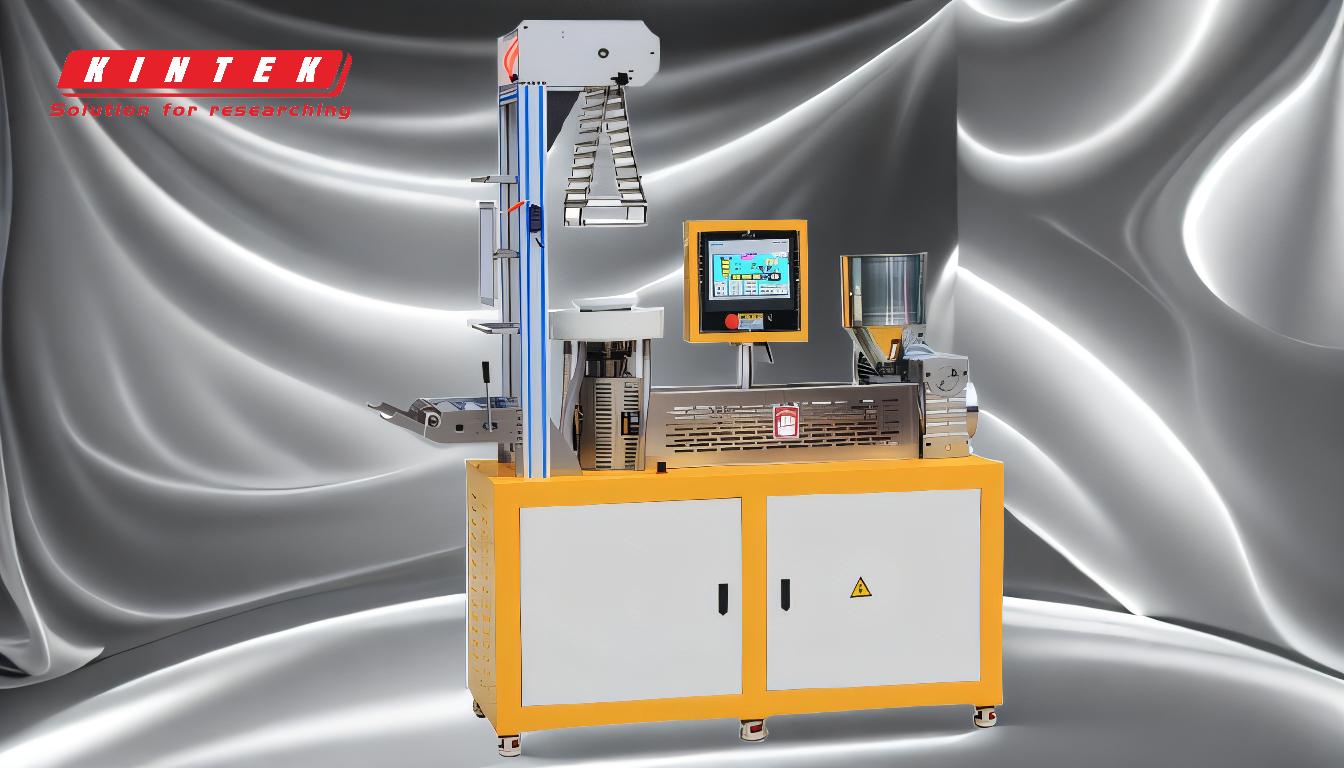
-
Structure and Composition:
- Monolayer Films: Consist of a single layer of material, typically made from one type of polymer. This simplicity makes them easier and cheaper to produce.
- Multilayer Films: Composed of multiple layers, often combining different polymers or materials to achieve specific properties. Each layer can be engineered to provide distinct functionalities, such as barrier properties, strength, or printability.
-
Functionality and Performance:
- Monolayer Films: Suitable for basic applications where high performance is not critical. They provide fundamental properties like puncture resistance and printability, making them ideal for simple packaging needs.
- Multilayer Films: Designed for advanced applications requiring superior performance. They offer enhanced barrier properties (e.g., against moisture, oxygen, or UV light), improved mechanical strength, and additional functionalities like heat resistance or chemical resistance.
-
Cost and Production Complexity:
- Monolayer Films: Generally more cost-effective due to simpler manufacturing processes and the use of a single material. They are easier to produce and require less sophisticated equipment.
- Multilayer Films: More expensive to produce due to the complexity of combining multiple materials and the need for specialized co-extrusion or lamination processes. The additional layers and materials increase production costs but provide higher performance.
-
Applications:
- Monolayer Films: Commonly used in applications where basic protection and printability are sufficient, such as lightweight packaging, simple bags, and non-critical industrial uses.
- Multilayer Films: Preferred for applications demanding high performance, such as food packaging (to extend shelf life), medical packaging (to maintain sterility), and industrial applications (where durability and barrier properties are crucial).
-
Advantages and Limitations:
-
Monolayer Films:
- Advantages: Cost-effective, easy to produce, suitable for basic needs.
- Limitations: Limited functionality, not suitable for high-performance applications.
-
Multilayer Films:
- Advantages: Superior performance, enhanced barrier properties, tailored functionalities.
- Limitations: Higher cost, more complex production process.
-
Monolayer Films:
-
Material Selection:
- Monolayer Films: Typically made from a single polymer like polyethylene (PE) or polypropylene (PP), chosen for its balance of properties and cost.
- Multilayer Films: Combine different materials such as ethylene vinyl alcohol (EVOH) for barrier properties, nylon for strength, and polyethylene for sealing. The selection of materials is tailored to meet specific application requirements.
-
Environmental Considerations:
- Monolayer Films: Easier to recycle due to the single material composition, making them more environmentally friendly in terms of end-of-life disposal.
- Multilayer Films: More challenging to recycle because of the combination of different materials, which can complicate the recycling process. However, advancements in recycling technologies are addressing these challenges.
In summary, the choice between monolayer and multilayer films depends on the specific requirements of the application. Monolayer films are suitable for basic, cost-sensitive applications, while multilayer films are necessary for high-performance applications requiring advanced properties and functionalities.
Summary Table:
Aspect | Monolayer Films | Multilayer Films |
---|---|---|
Structure | Single layer of material (e.g., PE, PP) | Multiple layers of different materials (e.g., EVOH, nylon, PE) |
Functionality | Basic properties like puncture resistance and printability | Advanced properties like barrier performance, mechanical strength, and heat resistance |
Cost | Cost-effective, simpler production | Higher cost, complex production |
Applications | Lightweight packaging, simple bags | Food packaging, medical supplies, industrial uses |
Recyclability | Easier to recycle due to single material | Challenging to recycle due to multiple materials |
Need help choosing the right film for your application? Contact our experts today for tailored solutions!