The operating pressure of a reactor depends on the specific application and type of reaction being conducted. Reactor pressures can range from a few torr (low vacuum) to several hundred torr (near atmospheric or higher), with base pressures as low as 10^-3 torr for certain processes. The choice of operating pressure is influenced by factors such as the reaction type (e.g., polymerization, hydrocracking), desired reaction kinetics, and the need to control competing reactions. Higher pressures can accelerate reactions by increasing reactant concentration and collision frequency, while also maintaining cleaner reaction profiles. The pressure range must be carefully selected to optimize reaction efficiency and safety.
Key Points Explained:
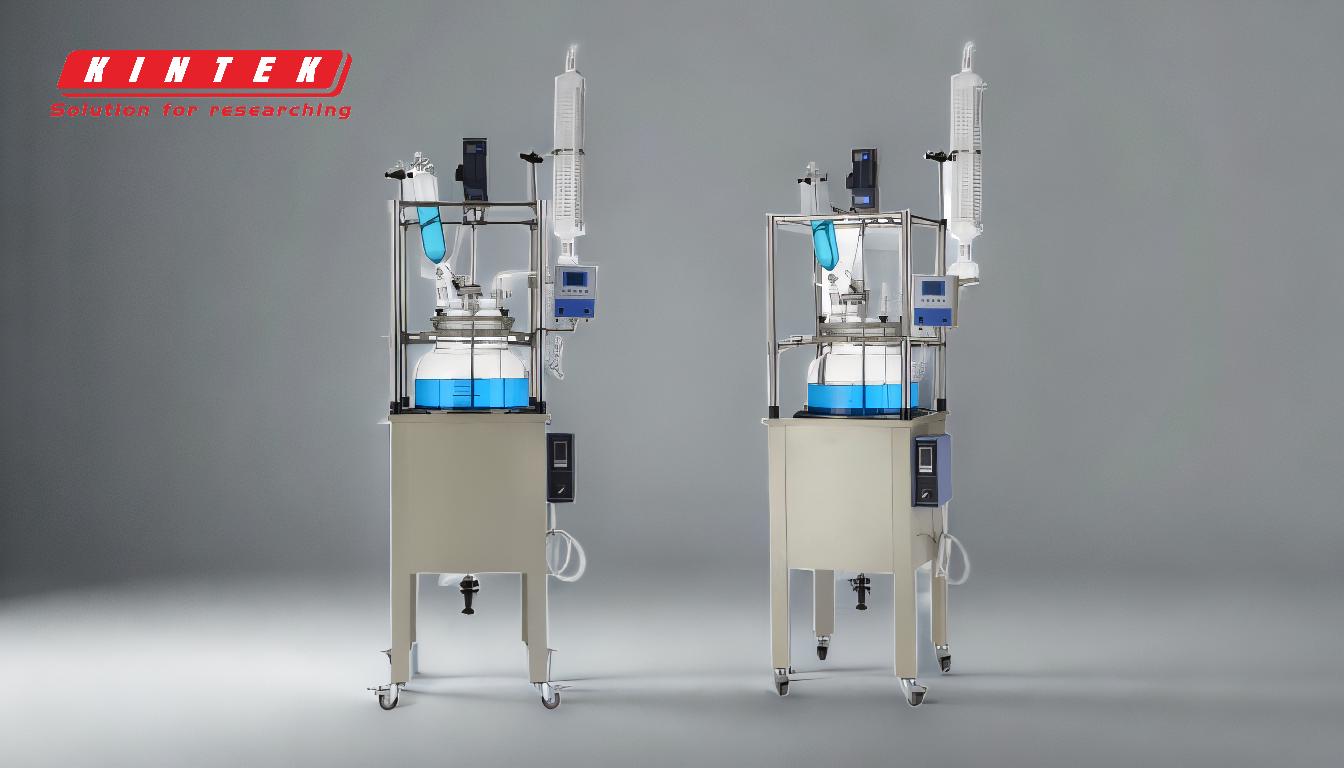
-
Range of Operating Pressures:
- Reactors can operate at a wide range of pressures, from a few torr (low vacuum) to several hundred torr (near atmospheric or higher).
- Base pressures in some reactors can be as low as 10^-3 torr, which is typical for high-vacuum applications.
-
Factors Influencing Pressure Selection:
- Reaction Type: Different reactions, such as polymerization or hydrocracking, require specific pressure conditions to proceed efficiently.
- Reaction Kinetics: Higher pressures can speed up reactions by reducing the reaction volume and increasing the concentration and collision frequency of reactants.
- Reaction Profile: Pressure helps maintain clean reaction profiles and reduces the likelihood of competing reactions, which is crucial for achieving desired product yields.
-
Impact of Pressure on Reactions:
- Acceleration of Reactions: Increased pressure enhances the reaction rate by forcing reactants into closer proximity, thereby increasing their interaction frequency.
- Decomposition and Gas Release: Pressure impacts decomposition reactions only if gas is released or if the reaction involves gaseous components.
- Control of Competing Reactions: Proper pressure management can minimize side reactions, ensuring a cleaner and more efficient process.
-
Design Considerations for Reactors:
- Temperature and Pressure Relationship: Reactors are often designed to handle specific temperature and pressure ranges, which are interdependent. Higher pressures may require robust materials and safety mechanisms.
- Flow Rate and Volume: The flow rate of reactants and the reactor volume must be optimized to maintain the desired pressure and reaction conditions.
-
Applications of Pressure in Reactors:
- Polymerization: High-pressure reactors are often used in polymerization processes to control molecular weight and polymer structure.
- Hydrocracking: This process typically operates at elevated pressures to break down complex hydrocarbons into simpler molecules.
- High-Pressure Glass Reactors: These reactors are used for reactions where visibility and pressure control are critical, such as in catalytic studies or material synthesis.
By understanding these key points, equipment and consumable purchasers can make informed decisions about the type of reactor and operating conditions needed for their specific applications. The selection of the appropriate pressure range is critical for achieving optimal reaction outcomes and ensuring the safety and efficiency of the process.
Summary Table:
Key Aspect | Details |
---|---|
Pressure Range | Few torr (low vacuum) to several hundred torr (near atmospheric or higher) |
Base Pressure | As low as 10^-3 torr for high-vacuum applications |
Influencing Factors | Reaction type, kinetics, and control of competing reactions |
Impact on Reactions | Accelerates reactions, controls decomposition, and minimizes side reactions |
Design Considerations | Temperature-pressure relationship, flow rate, and reactor volume |
Applications | Polymerization, hydrocracking, and high-pressure glass reactors |
Need help selecting the right reactor pressure for your application? Contact our experts today!