A stirred reactor is primarily designed to facilitate uniform mixing of reactants and ensure homogeneous temperature distribution within the reactor. This is achieved through the use of stirring mechanisms like magnetic stirrers or impellers, which help maintain consistent conditions throughout the reaction process. By promoting efficient mixing and heat transfer, stirred reactors enhance reaction efficiency, improve product quality, and enable precise control over reaction parameters, making them essential in various chemical, pharmaceutical, and industrial processes.
Key Points Explained:
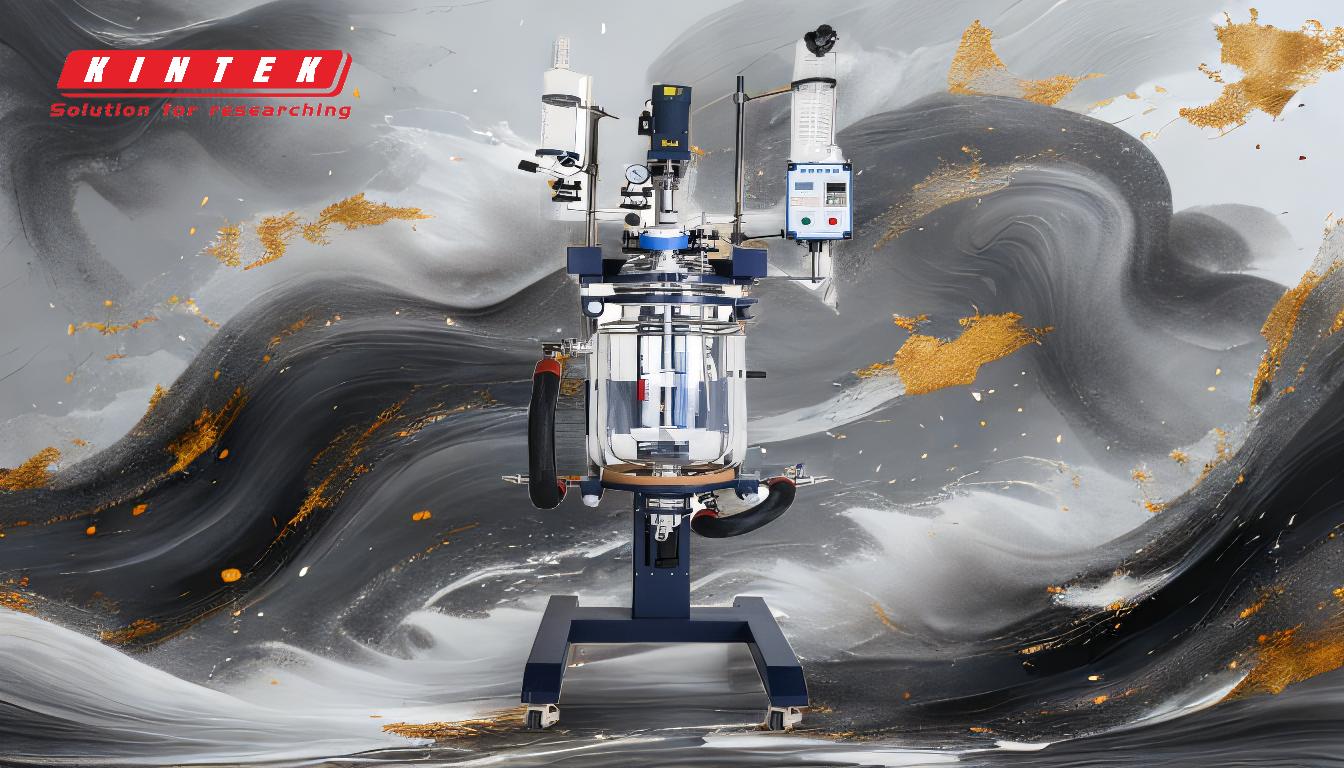
-
Uniform Mixing of Reactants:
- Stirred reactors are equipped with mechanisms such as magnetic stirrers or impellers to ensure that reactants are thoroughly mixed.
- Uniform mixing is critical for achieving consistent reaction rates and preventing localized concentration gradients, which can lead to incomplete reactions or undesirable by-products.
- This feature is particularly important in processes where reactants have different densities or viscosities, ensuring that all components interact effectively.
-
Homogeneous Temperature Distribution:
- The stirring mechanism helps maintain a consistent temperature throughout the reactor by distributing heat evenly.
- Temperature uniformity is crucial for controlling reaction kinetics and avoiding hotspots or cold zones, which can compromise product quality or safety.
- This is especially vital in exothermic or endothermic reactions, where uneven temperature distribution can lead to runaway reactions or incomplete conversions.
-
Enhanced Reaction Efficiency:
- By ensuring uniform mixing and temperature, stirred reactors optimize reaction conditions, leading to faster and more efficient chemical processes.
- This efficiency reduces reaction times and minimizes energy consumption, making the process more cost-effective and sustainable.
-
Improved Product Quality:
- Consistent mixing and temperature control result in higher-quality products with fewer impurities or defects.
- This is particularly important in industries like pharmaceuticals, where product purity and consistency are critical for compliance and efficacy.
-
Versatility in Applications:
- Stirred reactors are widely used in industries such as chemical manufacturing, pharmaceuticals, food processing, and biotechnology.
- Their ability to handle a wide range of reactions, from small-scale laboratory experiments to large-scale industrial production, makes them versatile and indispensable tools.
-
Precision and Control:
- Stirred reactors allow for precise control over reaction parameters, such as mixing speed, temperature, and pressure.
- This level of control is essential for conducting complex reactions, optimizing processes, and scaling up production while maintaining reproducibility.
In summary, the primary purpose of a stirred reactor is to provide a controlled environment where reactants can be uniformly mixed and maintained at a consistent temperature, ensuring efficient, high-quality, and scalable chemical processes.
Summary Table:
Key Feature | Description |
---|---|
Uniform Mixing of Reactants | Ensures thorough mixing, preventing concentration gradients and incomplete reactions. |
Homogeneous Temperature Distribution | Maintains consistent temperature, avoiding hotspots or cold zones. |
Enhanced Reaction Efficiency | Optimizes reaction conditions, reducing time and energy consumption. |
Improved Product Quality | Produces high-quality, consistent products with fewer impurities. |
Versatility in Applications | Suitable for chemical, pharmaceutical, food processing, and biotechnology industries. |
Precision and Control | Enables precise control over mixing speed, temperature, and pressure. |
Ready to optimize your chemical processes? Contact us today to learn more about stirred reactors!