Multilayer coextrusion is a sophisticated manufacturing process used to create materials with multiple layers of different polymers, each contributing unique properties to the final product. This process involves extruding multiple polymer streams simultaneously and combining them into a single structure with distinct layers. The layers are bonded together either in a feedblock or directly in the die, ensuring a seamless and cohesive final product. This method is widely used in industries such as packaging, automotive, and electronics, where materials with specific barrier properties, strength, or aesthetic qualities are required.
Key Points Explained:
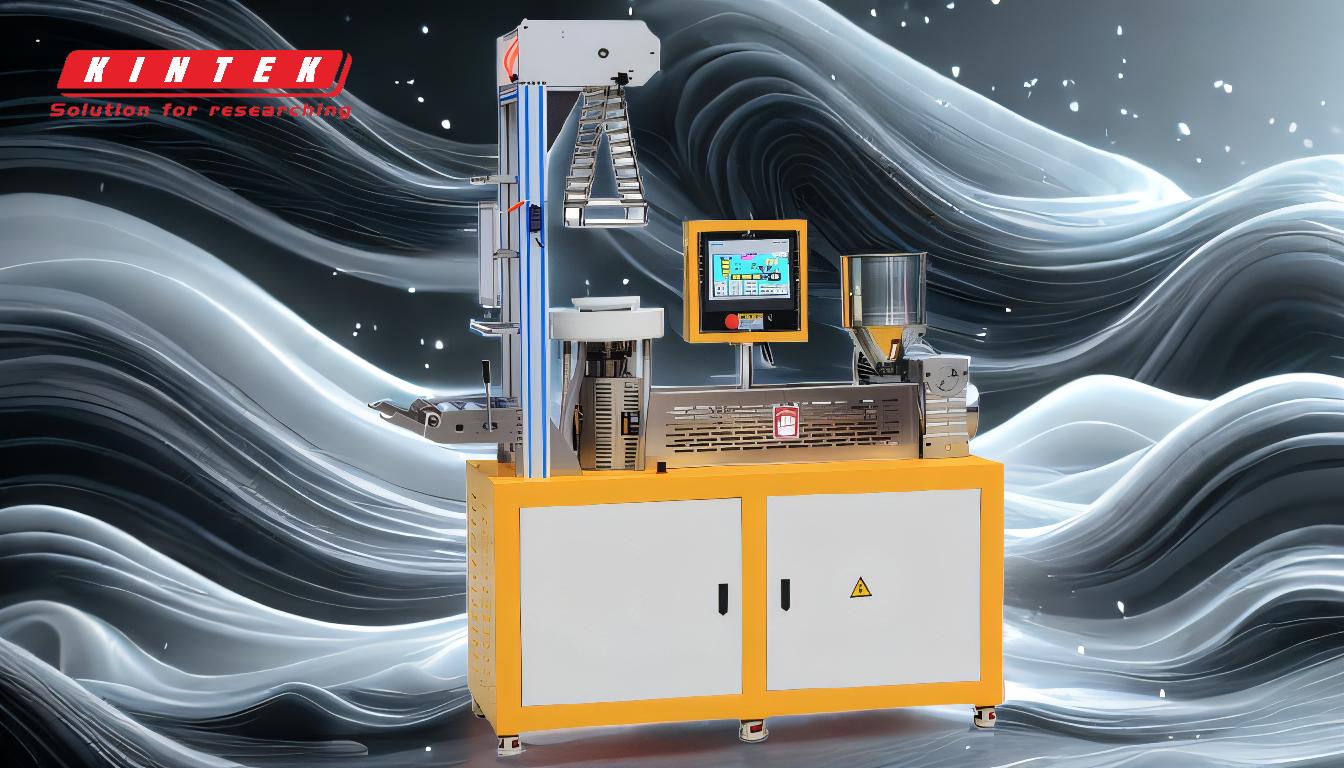
-
Definition and Purpose of Multilayer Coextrusion:
- Multilayer coextrusion is a process where multiple polymer layers are extruded simultaneously and combined into a single structure.
- The purpose is to create materials with enhanced properties by combining the strengths of different polymers in a single product.
-
Components Involved in the Process:
- Extruders: Multiple extruders are used to melt and pump different polymers. Each extruder handles a specific polymer material.
- Feedblock: A feedblock is often used to combine the polymer streams before they enter the die. It ensures that the layers are properly aligned and distributed.
- Die: The die shapes the combined polymer streams into the desired final form, such as a film, sheet, or tube.
-
Steps in the Multilayer Coextrusion Process:
- Polymer Preparation: Different polymers are prepared and fed into their respective extruders.
- Melting and Extrusion: Each polymer is melted and extruded through its extruder. The molten polymers are then combined in the feedblock or die.
- Layer Combination: The polymers are layered together in the feedblock or die. The number of layers and their arrangement depend on the desired properties of the final product.
- Shaping and Cooling: The combined polymer layers are shaped into the final product by the die and then cooled to solidify the structure.
-
Types of Multilayer Structures:
- Symmetrical Structures: Layers are arranged symmetrically around a central core. This is often used for products requiring balanced properties.
- Asymmetrical Structures: Layers are arranged in a non-symmetrical manner, which is useful for products requiring specific properties on one side, such as barrier layers in packaging.
-
Applications of Multilayer Coextrusion:
- Packaging: Used to create films and sheets with barrier properties to protect food, pharmaceuticals, and other sensitive products.
- Automotive: Produces parts with specific mechanical properties, such as dashboards or fuel tanks.
- Electronics: Used in the production of insulating films and flexible circuits.
-
Advantages of Multilayer Coextrusion:
- Enhanced Properties: By combining different polymers, the final product can have improved strength, barrier properties, and aesthetic qualities.
- Cost Efficiency: Allows for the use of expensive polymers only where needed, reducing overall material costs.
- Customization: The process can be tailored to produce materials with specific properties for various applications.
-
Challenges and Considerations:
- Material Compatibility: The polymers used must be compatible in terms of melting temperatures and adhesion properties to ensure proper bonding.
- Process Control: Precise control of extrusion parameters (temperature, pressure, flow rate) is essential to maintain layer uniformity and product quality.
- Equipment Complexity: The process requires specialized equipment, including multiple extruders and a feedblock or die, which can be costly and complex to operate.
-
Future Trends in Multilayer Coextrusion:
- Sustainable Materials: Increasing use of biodegradable and recyclable polymers to meet environmental regulations and consumer demand.
- Advanced Barrier Technologies: Development of new polymers and layer structures to improve barrier properties for sensitive applications.
- Automation and AI: Integration of automation and artificial intelligence to enhance process control and product consistency.
In summary, multilayer coextrusion is a versatile and advanced manufacturing process that allows for the creation of complex, multi-layered materials with tailored properties. By combining different polymers, manufacturers can produce products that meet specific performance requirements across a wide range of industries. However, the process requires careful consideration of material compatibility, precise process control, and specialized equipment to ensure high-quality results.
Summary Table:
Aspect | Details |
---|---|
Definition | Combines multiple polymer layers into a single structure for enhanced properties. |
Key Components | Extruders, feedblock, die. |
Process Steps | Polymer preparation, melting, layer combination, shaping, and cooling. |
Structure Types | Symmetrical (balanced) or asymmetrical (specific properties on one side). |
Applications | Packaging (barrier films), automotive (dashboards), electronics (insulating films). |
Advantages | Enhanced properties, cost efficiency, customization. |
Challenges | Material compatibility, process control, equipment complexity. |
Future Trends | Sustainable materials, advanced barrier tech, automation, and AI integration. |
Discover how multilayer coextrusion can revolutionize your materials—contact our experts today!