Multilayer extrusion, also known as coextrusion, is a sophisticated manufacturing process used to create layered structures by combining two or more polymers into a single product. This process is widely used in industries such as packaging, automotive, and construction to produce materials with enhanced properties like barrier protection, strength, and flexibility. The process involves feeding different polymers into separate extruders, which then merge into a single structure through a feedblock or die. The layers are bonded together without mixing, ensuring each layer retains its unique properties. The final product can have anywhere from two to dozens of layers, depending on the application.
Key Points Explained:
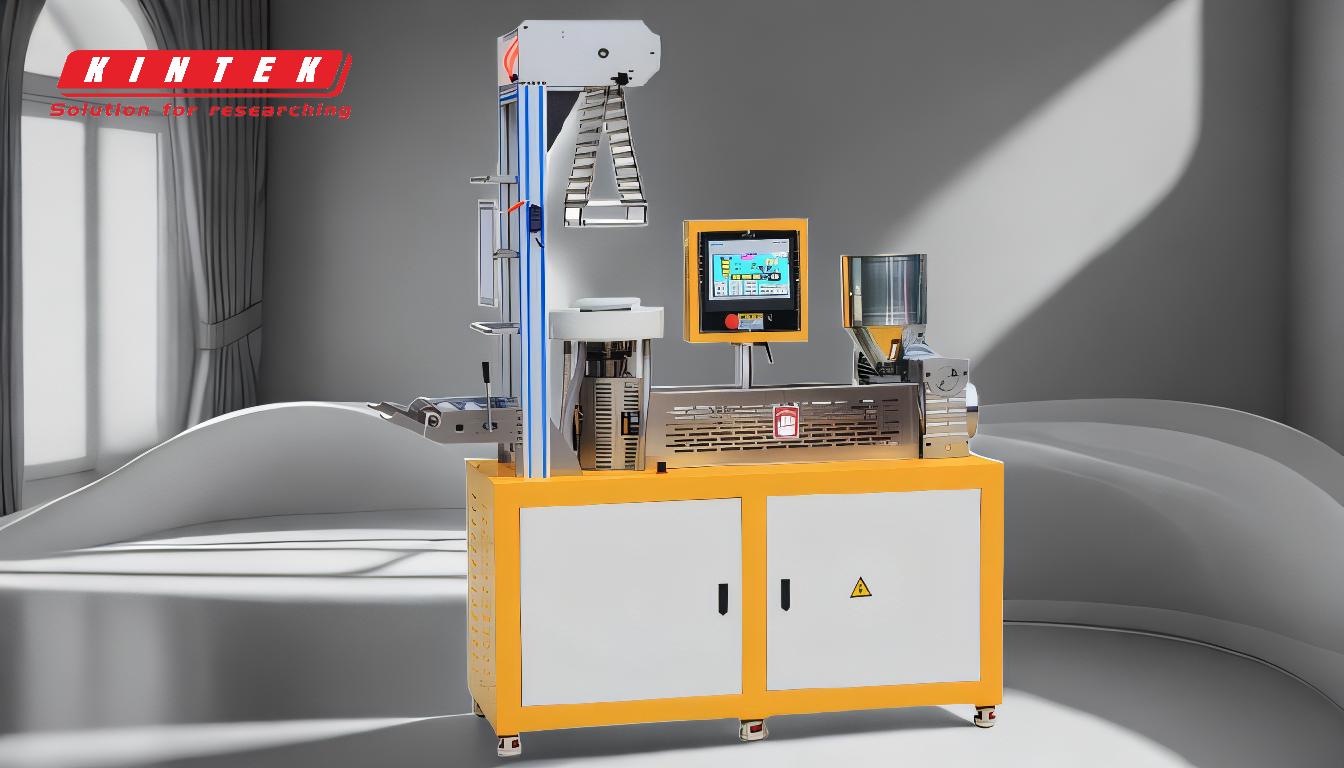
-
Definition of Multilayer Extrusion:
- Multilayer extrusion is a process where two or more polymers are extruded simultaneously and combined into a single structure with multiple layers.
- This technique allows for the creation of materials with tailored properties by combining the strengths of different polymers.
-
Components of the Process:
- Extruders: Each polymer is fed into a separate extruder, where it is melted and homogenized.
- Feedblock or Die: The molten polymers are then directed into a feedblock or die, where they are combined into a layered structure.
- Cooling and Shaping: The combined structure is then cooled and shaped into the final product, such as a film, sheet, or tube.
-
Types of Multilayer Structures:
- Symmetrical Structures: Layers are arranged symmetrically around a central core, often used for aesthetic or structural purposes.
- Asymmetrical Structures: Layers are arranged in a non-symmetrical manner, typically used to enhance specific properties like barrier resistance or adhesion.
-
Advantages of Multilayer Extrusion:
- Enhanced Properties: By combining different polymers, manufacturers can create materials with improved barrier properties, strength, flexibility, and thermal resistance.
- Cost Efficiency: Multilayer extrusion can reduce material costs by using thinner layers of expensive polymers combined with thicker layers of cheaper materials.
- Versatility: The process can be used to produce a wide range of products, from thin films to thick sheets, and can accommodate various polymers.
-
Applications of Multilayer Extrusion:
- Packaging: Multilayer films are commonly used in food packaging to provide barrier protection against moisture, oxygen, and other contaminants.
- Automotive: Multilayer tubes and sheets are used in automotive applications for fuel lines, air ducts, and interior trim.
- Construction: Multilayer pipes and sheets are used in construction for plumbing, insulation, and structural components.
-
Challenges and Considerations:
- Material Compatibility: The polymers used must be compatible in terms of melting temperature, viscosity, and adhesion to ensure proper bonding.
- Process Control: Precise control of temperature, pressure, and flow rates is essential to maintain the integrity of the layers and prevent defects.
- Equipment Complexity: Multilayer extrusion requires specialized equipment, including multiple extruders, feedblocks, and dies, which can increase capital and operational costs.
-
Future Trends:
- Sustainable Materials: There is a growing trend towards using biodegradable and recyclable polymers in multilayer extrusion to reduce environmental impact.
- Advanced Technologies: Innovations in extrusion technology, such as micro-layer coextrusion, are enabling the production of materials with even more layers and enhanced properties.
In summary, multilayer extrusion is a versatile and efficient process that allows manufacturers to create complex, multi-layered materials with tailored properties. By understanding the components, advantages, and challenges of this process, purchasers can make informed decisions about the equipment and materials needed for their specific applications.
Summary Table:
Aspect | Details |
---|---|
Definition | Combines two or more polymers into a single, multi-layered structure. |
Components | Extruders, feedblock/die, cooling/shaping systems. |
Types of Structures | Symmetrical (aesthetic/structural) and asymmetrical (barrier/adhesion). |
Advantages | Enhanced properties, cost efficiency, and versatility. |
Applications | Packaging, automotive, and construction industries. |
Challenges | Material compatibility, process control, and equipment complexity. |
Future Trends | Sustainable materials and advanced extrusion technologies. |
Ready to explore multilayer extrusion solutions for your industry? Contact us today to get started!