The process of thin film dip coating involves four main stages: immersion, dwelling, withdrawal, and drying. This method is used to apply a thin film coating onto a substrate by dipping it into a solution and then withdrawing it at a controlled speed. The process is widely used to modify surface properties, such as conductivity, wear resistance, corrosion resistance, and optical properties, depending on the application needs. Thin film deposition, in general, involves creating and depositing thin coatings onto substrates using various techniques, including chemical and physical deposition methods. The dip coating process is a simple yet effective way to achieve uniform thin films with controlled thickness and properties.
Key Points Explained:
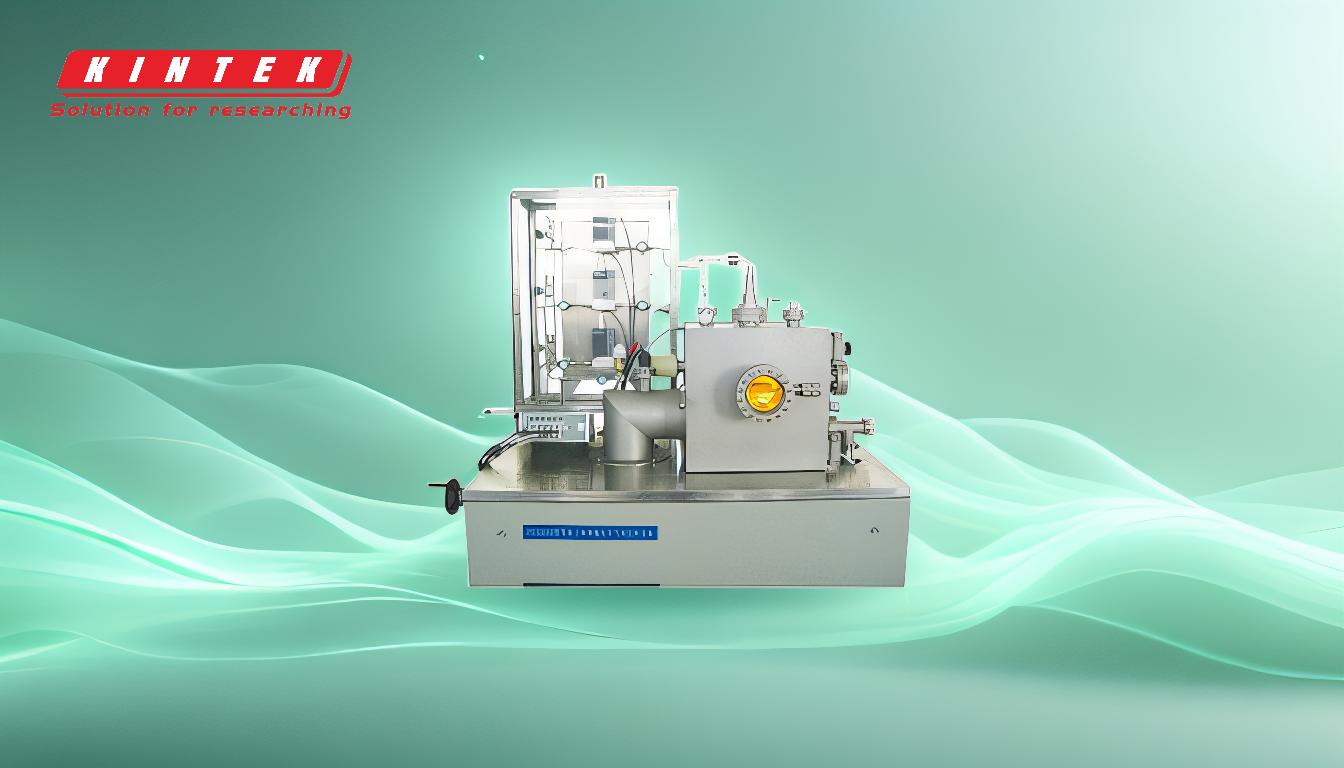
-
Stages of Thin Film Dip Coating:
- Immersion: The substrate is immersed into the coating solution at a controlled speed. This ensures uniform contact between the substrate and the solution.
- Dwelling: After immersion, the substrate is held in the solution for a specific period to allow the coating material to adhere properly.
- Withdrawal: The substrate is then withdrawn from the solution at a controlled speed. The withdrawal speed determines the thickness of the coating; slower speeds result in thicker films.
- Drying: The coated substrate is dried, often under controlled environmental conditions, to solidify the film and ensure adhesion.
-
Purpose of Thin Film Deposition:
- Thin film deposition is used to modify the surface properties of substrates, such as improving conductivity, wear resistance, corrosion resistance, or optical properties.
- It is widely used in industries like electronics, optics, and materials engineering to enhance the performance of components.
-
Types of Thin Film Deposition:
- Chemical Deposition: Involves a chemical reaction at the substrate surface, resulting in the formation of a solid layer. Examples include chemical vapor deposition (CVD).
- Physical Deposition: Uses mechanical, electromechanical, or thermodynamic means to deposit thin films. Examples include sputtering, thermal evaporation, and ion beam deposition.
-
Key Factors Influencing Dip Coating:
- Withdrawal Speed: Determines the thickness of the coating. Slower speeds result in thicker films due to increased solution retention on the substrate.
- Solution Viscosity: Higher viscosity solutions tend to produce thicker coatings.
- Drying Conditions: Controlled temperature and humidity during drying are critical to prevent defects like cracking or uneven drying.
-
Applications of Thin Film Dip Coating:
- Optical Coatings: Used to create anti-reflective or reflective coatings on glass or lenses.
- Protective Coatings: Applied to metals or other materials to enhance corrosion or wear resistance.
- Electronic Components: Used to deposit conductive or insulating layers in semiconductor devices.
-
Advantages of Dip Coating:
- Simplicity and cost-effectiveness compared to other deposition methods.
- Ability to coat complex shapes and large surfaces uniformly.
- Control over film thickness by adjusting withdrawal speed and solution properties.
-
Challenges and Considerations:
- Achieving uniform thickness on irregularly shaped substrates can be challenging.
- The process may require precise control of environmental conditions (e.g., temperature, humidity) to avoid defects.
- Limited to specific materials and solutions that can form stable coatings.
By understanding the stages and factors involved in thin film dip coating, manufacturers can optimize the process to achieve desired film properties for various applications. This method is particularly valuable for its simplicity, versatility, and ability to produce high-quality coatings on a wide range of substrates.
Summary Table:
Aspect | Details |
---|---|
Stages | Immersion, Dwelling, Withdrawal, Drying |
Purpose | Modify surface properties (conductivity, wear resistance, optical, etc.) |
Types of Deposition | Chemical (e.g., CVD), Physical (e.g., sputtering, thermal evaporation) |
Key Factors | Withdrawal speed, solution viscosity, drying conditions |
Applications | Optical coatings, protective coatings, electronic components |
Advantages | Cost-effective, uniform coatings, control over film thickness |
Challenges | Uniformity on irregular shapes, precise environmental control required |
Optimize your thin film dip coating process—contact our experts today for tailored solutions!