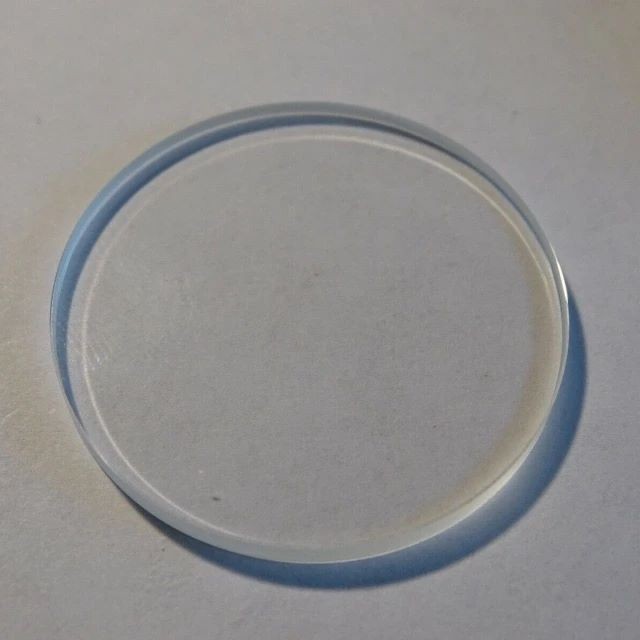
Optical Materials
400-700nm Wavelength Anti Reflective AR Coating Glass
Item Number : KTOM-ARG
Price varies based on specs and customizations
- lass material
- Clear glass/ Ultra clear glass
- Light transparent
- >98% (400-700nm)
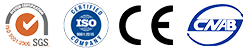
Shipping:
Contact us to get shipping details Enjoy On-time Dispatch Guarantee.
Why Choose Us
Reliable PartnerEasy ordering process, quality products, and dedicated support for your business success.
Anti reflective / AR coating glass
An anti-reflection coating (AR coating) is a thin film or multiple layers of materials that are applied to optical surfaces, such as lenses or windows, to reduce reflection. The primary purpose of an AR coating is to minimize the amount of light that is reflected off the surface, thereby increasing the amount of light that can pass through the material.
AR coatings work by altering the refractive index of the surface they are applied to. By carefully designing and depositing these coatings, the thickness and composition of the layers can be optimized to create destructive interference for the reflected light waves. This interference effect reduces the intensity of the reflected light, resulting in a significant reduction in glare and unwanted reflections.
Detail & Parts
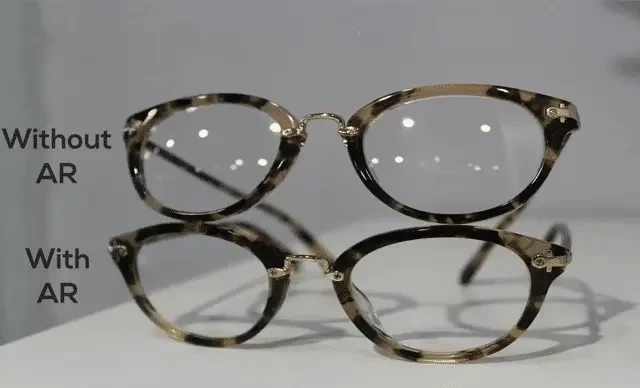
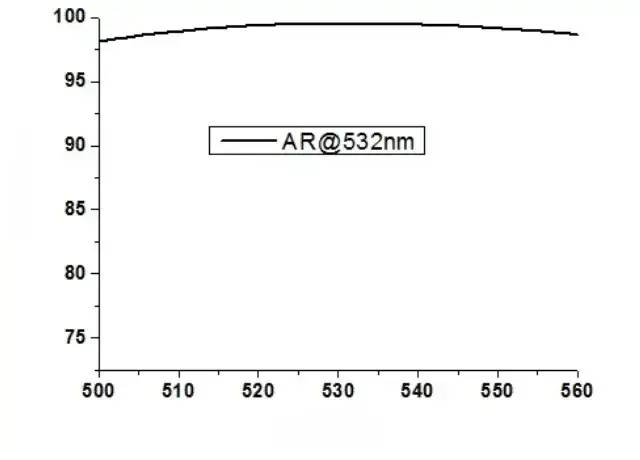
Applications of Anti reflective / AR coating glass
- Eyeglasses and Sunglasses: AR coatings on prescription eyeglasses and sunglasses reduce glare, improve visual clarity, and enhance the overall optical quality of the lenses. They allow more light to pass through the lenses, reducing reflections that can interfere with vision.
- Camera Lenses: AR coatings on camera lenses help minimize lens flare, ghosting, and unwanted reflections, resulting in clearer and sharper images. They also increase light transmission, allowing photographers to capture more detail and improve overall image quality.
- Display Screens: AR coatings on display screens, such as computer monitors, televisions, smartphones, and tablets, reduce reflections and improve visibility by minimizing glare. This enhances the viewing experience, particularly in bright environments, and provides better image clarity and color accuracy.
- Optical Instruments: AR coatings are used on various optical instruments like microscopes, telescopes, binoculars, and camera lens filters. They reduce reflections and increase light transmission, allowing users to observe objects with greater clarity and detail.
Properties of Anti-Reflective Coating Glasses
- Minimize surface reflection and glare.
- Maximize visible wavelength capacity.
- Prevent visual distortions and ambiguous images.
- Absorb minimal light, benefiting the eye.
- Offer high abrasion resistance and strong coating adhesion.
Precautions
- Using a dry cloth on a dry lens can cause scratches and damage the lens coating. Anti-reflective coatings reduce reflections that can hide lens defects, but scratches are more visible on AR-coated lenses.
- Handle and clean lenses with AR coatings carefully to avoid scratches and maintain clarity.
Provide customized services
Through the implementation of innovative and state-of-the-art melting processes, we have acquired extensive expertise in the development and manufacture of quality glass products, offering a wide range of optical glass products for a variety of commercial, industrial and scientific applications. The company provides various specifications of optical glass such as raw glass, cut parts and finished components, and cooperates closely with customers to customize products according to customer needs. With an unwavering commitment to quality, we ensure our customers receive the perfect solution tailored to their requirements.
For further quotations, please contact us.
FAQ
How Thick Is A Typical AR Coating?
Is AR Coating On Inside Or Outside?
How Long Does Anti-reflective Coating Last?
4.8
out of
5
The AR coating glass is a game-changer for my lab. It has significantly reduced glare and reflections, resulting in clearer images and more accurate results.
4.7
out of
5
The quality of this AR coating glass is exceptional. It's durable and has held up well in our lab's demanding environment.
4.9
out of
5
The speedy delivery of the AR coating glass was a lifesaver. It arrived just in time for a crucial experiment, and the results were outstanding.
4.6
out of
5
I'm thoroughly impressed with the value for money I got with this AR coating glass. It's a cost-effective solution that has greatly improved the efficiency of our optical experiments.
4.8
out of
5
The technological advancement of this AR coating glass is remarkable. It has opened up new possibilities for our research and has pushed the boundaries of what we can achieve in the lab.
4.7
out of
5
The durability of the AR coating glass is exceptional. It has withstood rigorous use in our lab and continues to perform flawlessly, delivering consistent and reliable results.
4.9
out of
5
The clarity and sharpness of images obtained using this AR coating glass are truly impressive. It has revolutionized the way we conduct experiments and has led to groundbreaking discoveries.
4.6
out of
5
The versatility of this AR coating glass is commendable. It has proven to be adaptable to various applications in our lab, enhancing the performance of different optical instruments.
4.8
out of
5
The AR coating glass has exceeded our expectations. It has minimized reflections and improved the overall quality of our optical data, leading to more accurate and reliable results.
4.7
out of
5
The customer service provided by the company was exceptional. They were responsive, knowledgeable, and went above and beyond to ensure a smooth and hassle-free experience.
Products
400-700nm Wavelength Anti Reflective AR Coating Glass
REQUEST A QUOTE
Our professional team will reply to you within one business day. Please feel free to contact us!
Related Products
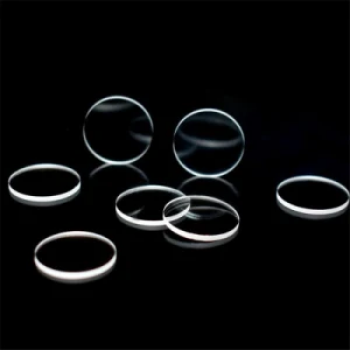
High Temperature Resistant Optical Quartz Glass Sheet
Discover the power of optical glass sheets for precise light manipulation in telecommunications, astronomy, and beyond. Unlock advancements in optical technology with exceptional clarity and tailored refractive properties.
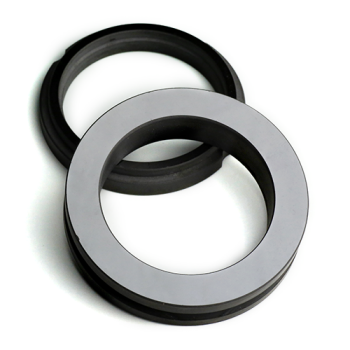
Custom CVD Diamond Coating for Lab Applications
CVD Diamond Coating: Superior Thermal Conductivity, Crystal Quality, and Adhesion for Cutting Tools, Friction, and Acoustic Applications
Related Articles
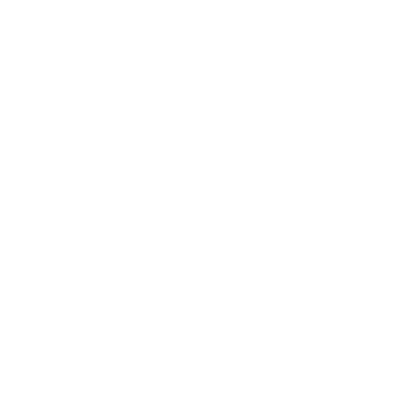
Unlocking the Power of Optical Quartz Plates: Applications and Benefits
Delve into the world of optical quartz plates, exploring their exceptional properties, diverse applications in industries like optics, electronics, and more. Discover their advantages, including low thermal expansion, high temperature resistance, and precise optical clarity.
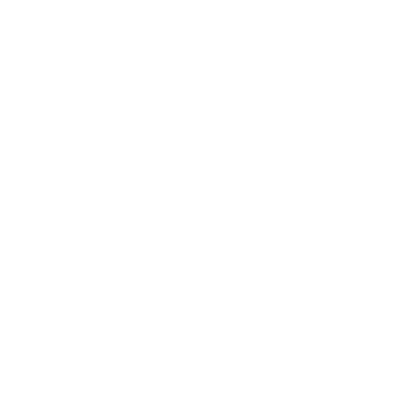
Unveiling the Exceptional Properties and Applications of Optical Quartz Plates
Discover the remarkable characteristics and diverse applications of optical quartz plates, including their superior ultraviolet transmission, thermal stability, and use in lenses, lighting devices, and semiconductor manufacturing.
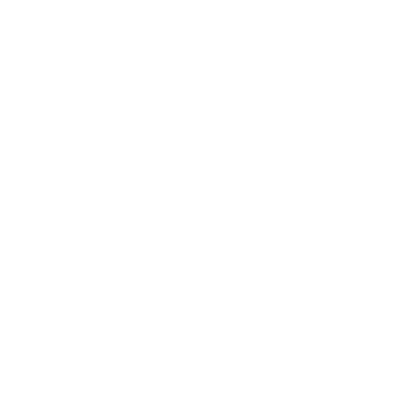
Safety Equipment In A Lab - Eye Protection
Safety glasses or chemical goggles must be donned before entering any wet bench lab, including cell culture labs. This applies to lab visitors, GT maintenance and custodial workers as well as staff and students.
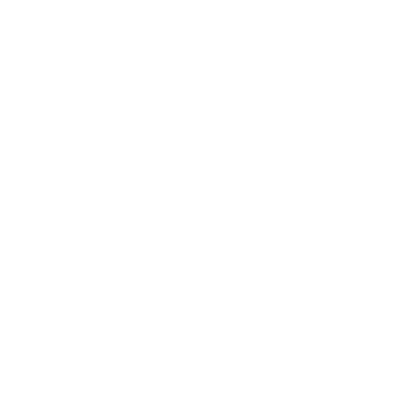
Comprehensive Guide to Optical Windows: Material Properties and Surface Specifications
This article delves into the properties and specifications of optical windows, focusing on material properties, surface quality, and anti-reflection coatings.
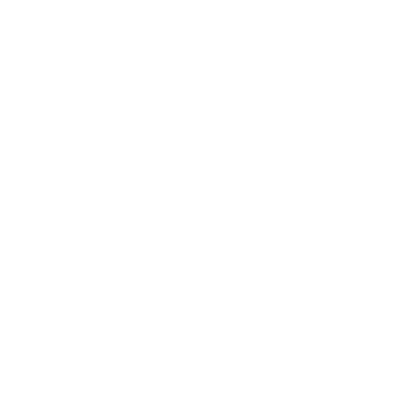
Application of Vacuum Coating on Architectural Glass
An in-depth look at the methods and benefits of vacuum coating on architectural glass, focusing on energy efficiency, aesthetics, and durability.
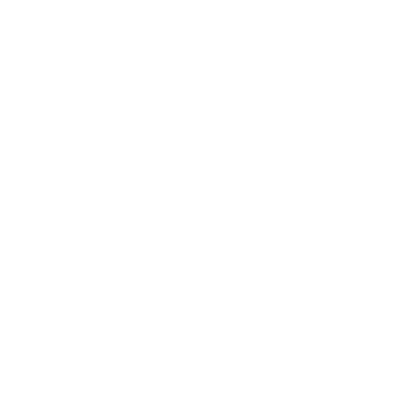
Factors in Selecting Large Optical Windows
Considerations for choosing large optical windows, including material, polishing, and coating.
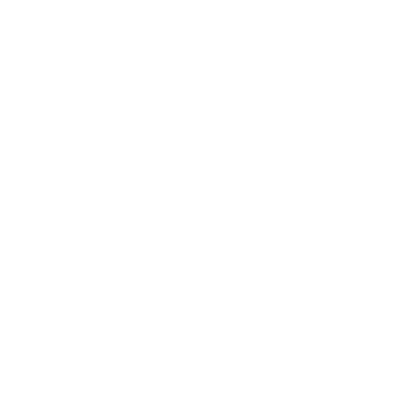
Electron Beam Evaporation: Advanced Thin Film Creation
Explores the technology and applications of electron beam evaporation in thin film production.
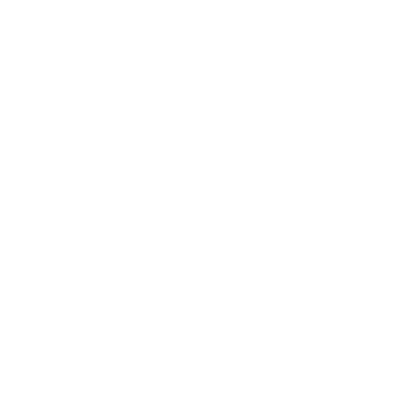
Thin Film System Design: Principles, Considerations, and Practical Applications
An in-depth exploration of thin film system design principles, technological considerations, and practical applications in various fields.
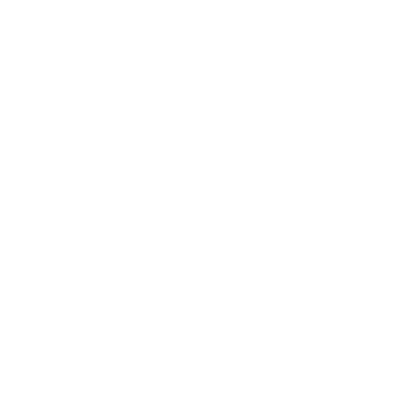
Optical Window Sheet Selection Guide
A comprehensive guide on selecting optical window sheets based on substrate material, optical and mechanical precision, and coating options.
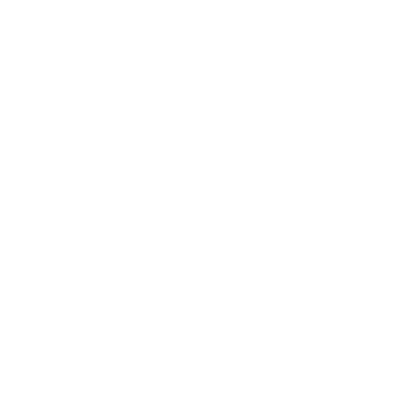
Common Rework Causes and Solutions for Tubular PECVD Coatings
This article discusses common rework causes in PECVD coating for crystalline silicon solar cells and provides feasible solutions to improve quality and reduce costs.
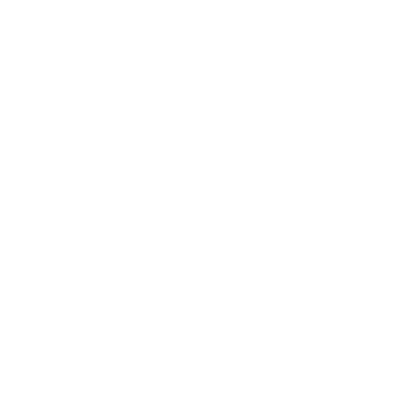
Applications of PECVD Nano-Coating Technology in Electronic Devices
PECVD nano-coating technology enhances durability and reliability in various electronic devices.
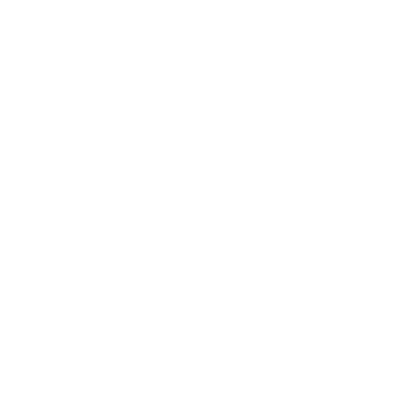
Optical Components: Window Sheets and Their Applications
An overview of various types of optical window sheets, their materials, precision, and coating options.