Mixers are versatile kitchen appliances designed to automate and simplify various food preparation tasks. Their primary purpose is to handle repetitive tasks such as stirring, whisking, beating, and kneading, which can be time-consuming and labor-intensive when done manually. Mixers come in different forms, including handheld eggbeaters, motorized handheld beaters, and larger stand mixers. They are essential tools for both home cooks and professional chefs, as they ensure consistency, save time, and reduce physical effort. By using attachments like dough hooks, mixers can also knead dough, making them indispensable for baking. Overall, mixers enhance efficiency and precision in the kitchen.
Key Points Explained:
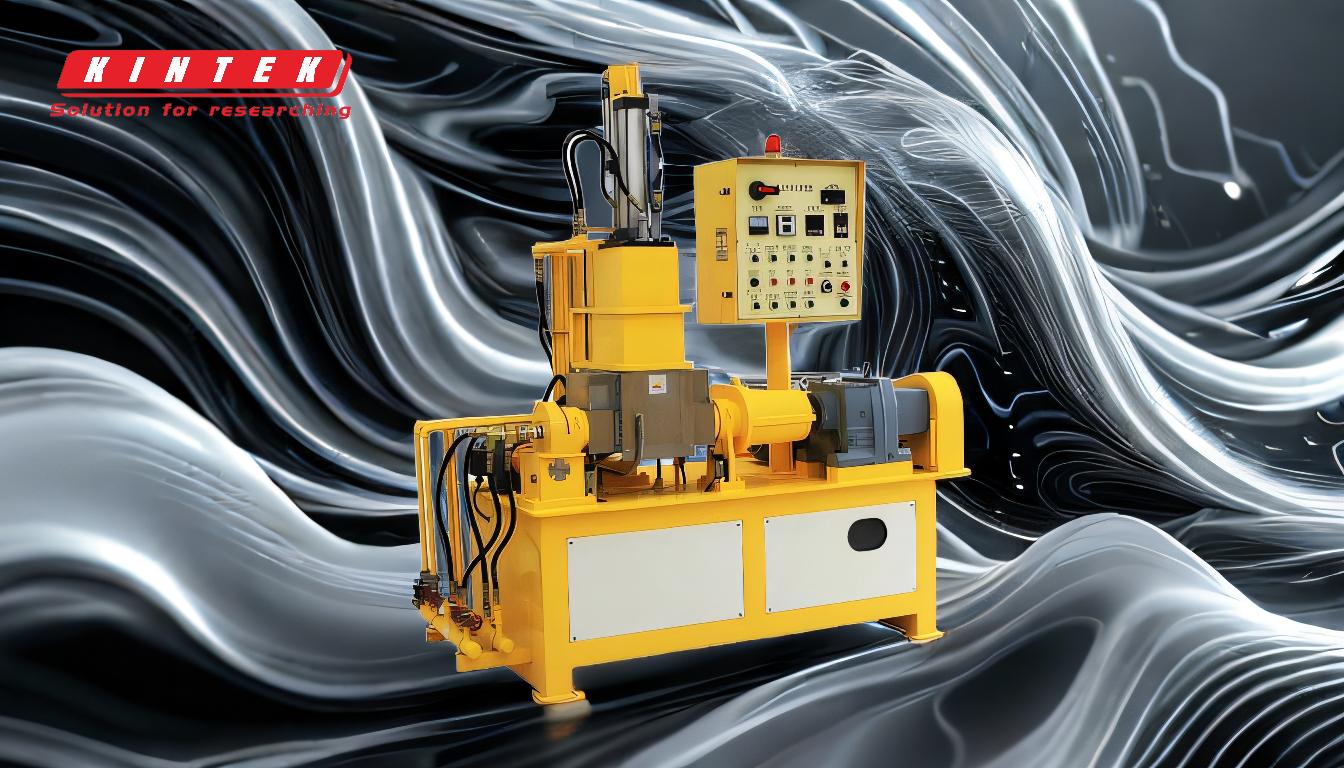
-
Automation of Repetitive Tasks:
- Mixers are designed to automate tasks such as stirring, whisking, and beating, which are often repetitive and tedious when done by hand.
- This automation not only saves time but also ensures consistent results, which is crucial for recipes requiring precise mixing.
-
Versatility in Functions:
- Mixers can perform a variety of functions depending on the attachment used. For example:
- Beaters: Ideal for whisking eggs, beating batter, or mixing light ingredients.
- Dough Hooks: Used for kneading dough, which is essential for baking bread, pizza, and other dough-based products.
- This versatility makes mixers suitable for a wide range of culinary tasks, from baking to preparing sauces.
- Mixers can perform a variety of functions depending on the attachment used. For example:
-
Types of Mixers:
- Handheld Eggbeaters: Simple, manual tools for light mixing tasks.
- Handheld Motorized Beaters: Provide more power and ease of use compared to manual eggbeaters, suitable for heavier tasks.
- Stand Mixers: Larger, more powerful mixers that can handle heavy-duty tasks and are often used in professional kitchens or by avid home bakers.
- Drill Mixers: Typically used for mixing construction materials like paint or cement, but can also be adapted for certain kitchen tasks.
-
Efficiency and Consistency:
- Mixers ensure that ingredients are evenly mixed, which is critical for the texture and quality of the final product.
- They reduce the physical effort required, making it easier to handle large quantities or heavy mixtures.
-
Time-Saving:
- By automating mixing tasks, mixers significantly reduce the time spent in the kitchen, allowing cooks to focus on other aspects of meal preparation.
-
Enhanced Baking Capabilities:
- The ability to knead dough with a dough hook attachment makes mixers particularly valuable for baking. Kneading by hand can be labor-intensive and inconsistent, whereas a mixer ensures even kneading, leading to better dough structure and texture.
-
Suitability for Different Users:
- Home Cooks: Benefit from the convenience and ease of use, especially when preparing everyday meals or baking.
- Professional Chefs: Rely on mixers for consistent results and the ability to handle large volumes of ingredients.
In summary, mixers are essential kitchen tools that automate repetitive tasks, enhance efficiency, and ensure consistency in food preparation. Their versatility and ability to handle a wide range of tasks make them invaluable for both home cooks and professional chefs.
Summary Table:
Feature | Description |
---|---|
Automation | Handles repetitive tasks like stirring, whisking, and kneading effortlessly. |
Versatility | Supports multiple functions with attachments like beaters and dough hooks. |
Types of Mixers | Includes handheld eggbeaters, motorized beaters, stand mixers, and drill mixers. |
Efficiency | Ensures even mixing, reducing physical effort and improving consistency. |
Time-Saving | Speeds up meal prep, allowing focus on other kitchen tasks. |
Baking Capabilities | Kneads dough evenly, essential for baking bread and pastries. |
User Suitability | Ideal for both home cooks and professional chefs. |
Ready to upgrade your kitchen efficiency? Contact us today to find the perfect mixer for your needs!