A rotary vane pump is a type of positive displacement pump that uses rotating vanes to create a vacuum or move fluids. Its primary purpose is to generate strong and consistent vacuum pressures, typically below 10⁻³ mbar, making it suitable for applications requiring precise vacuum control. These pumps are oil-sealed, which ensures tight sealing and lubrication of internal components. Common applications include hydraulic brake systems, freeze dryers, and mass spectrometry. While they offer reliable performance, they also come with challenges, such as managing toxic oil waste and sourcing replacement parts. Overall, rotary vane pumps are versatile and widely used in industries requiring efficient vacuum generation.
Key Points Explained:
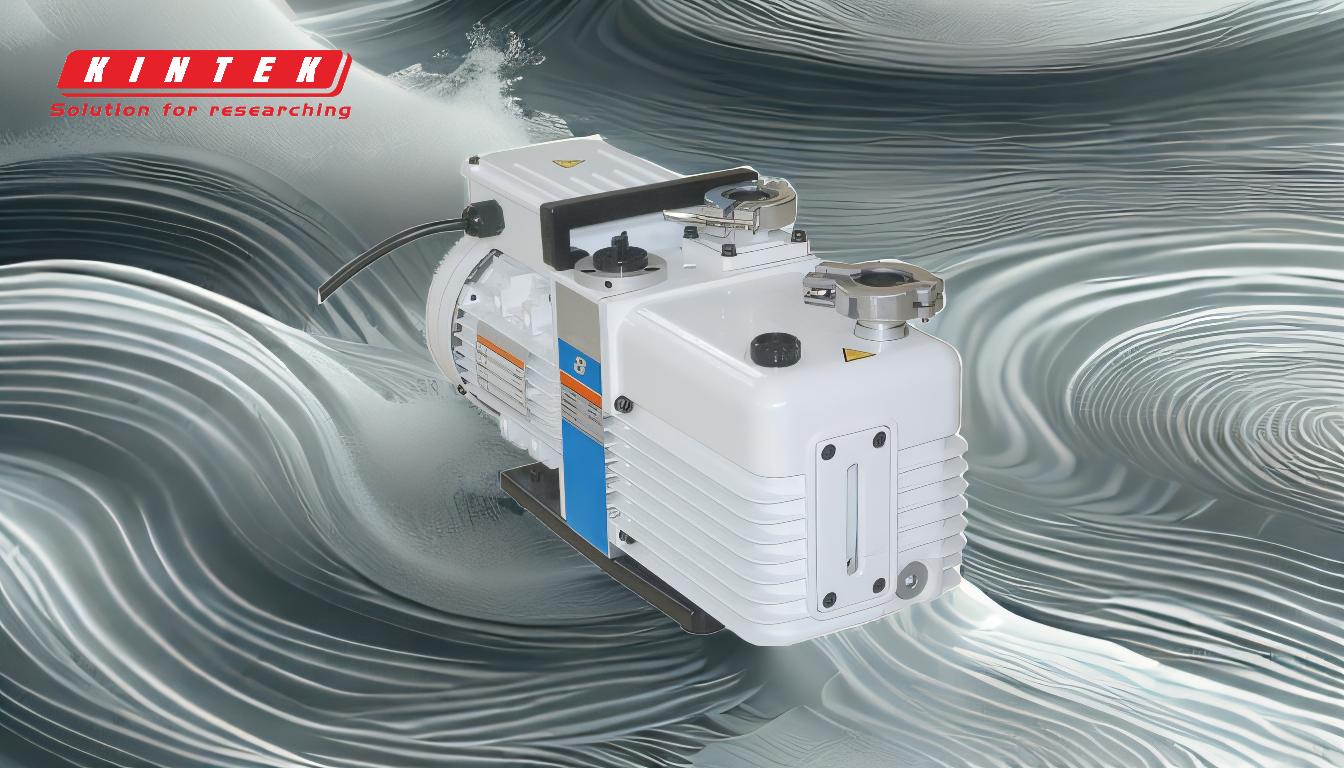
-
Primary Function of Rotary Vane Pumps:
- Rotary vane pumps are designed to create a vacuum or move fluids by using rotating vanes mounted on an off-center rotor. As the rotor turns, the vanes form chambers that expand and contract, drawing in and expelling fluid or gas.
- They are particularly effective at generating strong and consistent vacuum pressures, often below 10⁻³ mbar, making them ideal for applications requiring precise vacuum control.
-
Oil-Sealed Design:
- These pumps use oil to create a tight seal between the vanes and the pump chamber, ensuring efficient operation and preventing gas or fluid leakage.
- The oil also serves as a lubricant, reducing friction and wear on moving parts, which enhances the pump's durability and performance.
-
Applications of Rotary Vane Pumps:
- Hydraulic Brake Systems: Rotary vane pumps are used to create the vacuum necessary for power braking systems in vehicles.
- Freeze Dryers: They are essential in freeze-drying processes, where a strong vacuum is required to remove moisture from materials.
- Mass Spectrometry: These pumps are used in mass spectrometry to maintain the high vacuum needed for accurate analysis of chemical compounds.
- General Lab Applications: Rotary vane pumps are widely used in laboratories for tasks requiring consistent vacuum pressures.
-
Types of Rotary Vane Pumps:
- Single-Stage Pumps: These pumps are capable of achieving a rough vacuum and are typically used in less demanding applications.
- Double-Stage Pumps: These pumps can achieve a deeper vacuum and are used in applications requiring higher vacuum levels. They operate at a rotating speed of approximately 1500 revolutions per minute.
-
Advantages of Rotary Vane Pumps:
- Strong and Consistent Vacuum: They provide reliable vacuum performance, making them suitable for critical applications.
- Versatility: Their ability to handle both gas and liquid makes them useful in a wide range of industries.
- Efficient Operation: The oil-sealed design ensures minimal leakage and efficient performance.
-
Disadvantages of Rotary Vane Pumps:
- Toxic Oil Waste: The use of oil in these pumps generates waste that can be toxic and requires proper disposal.
- Maintenance Challenges: Replacement parts, such as vanes and seals, can be difficult to source, and regular maintenance is required to ensure optimal performance.
- Oil Contamination: In some applications, oil contamination can be a concern, particularly in sensitive environments like laboratories.
-
How Rotary Vane Pumps Work:
- The pump consists of a rotor with vanes that slide in and out as the rotor turns. The off-center design of the rotor creates chambers of varying sizes.
- As the chambers expand, they draw in fluid or gas. When the chambers contract, the fluid or gas is expelled, creating a vacuum or moving the fluid through the system.
-
Considerations for Purchasers:
- Application Requirements: Buyers should consider the specific vacuum pressure and flow rate needed for their application.
- Maintenance and Operating Costs: The need for regular oil changes and potential difficulties in sourcing replacement parts should be factored into the decision.
- Environmental Impact: Proper disposal of oil waste and the potential for oil contamination should be considered, especially in sensitive environments.
In summary, rotary vane pumps are essential tools for creating vacuum pressures and moving fluids in various industries. Their oil-sealed design ensures efficient operation, but they also come with maintenance and environmental considerations. Understanding their purpose, advantages, and limitations is crucial for selecting the right pump for specific applications.
Summary Table:
Aspect | Details |
---|---|
Primary Function | Generates strong vacuum pressures (below 10⁻³ mbar) for precise control. |
Oil-Sealed Design | Ensures tight sealing, lubrication, and efficient operation. |
Applications | Hydraulic brakes, freeze dryers, mass spectrometry, and lab tasks. |
Types | Single-stage (rough vacuum) and double-stage (deeper vacuum). |
Advantages | Strong vacuum, versatility, and efficient operation. |
Disadvantages | Toxic oil waste, maintenance challenges, and oil contamination risks. |
Key Considerations | Application needs, maintenance costs, and environmental impact. |
Discover the perfect rotary vane pump for your needs—contact us today for expert advice!