The vacuum pump in an evaporator serves multiple critical purposes, primarily centered around creating a controlled low-pressure environment. This environment lowers the boiling point of solvents, enabling faster and more efficient evaporation at reduced temperatures. By doing so, it minimizes the risk of degrading heat-sensitive compounds, improves safety, and enhances the purity of the extracted materials. Additionally, the vacuum pump helps maintain a continuous feed system, ensures process integrity by preventing contamination, and allows for precise control over evaporation parameters. These functions collectively optimize the evaporation process for both efficiency and quality.
Key Points Explained:
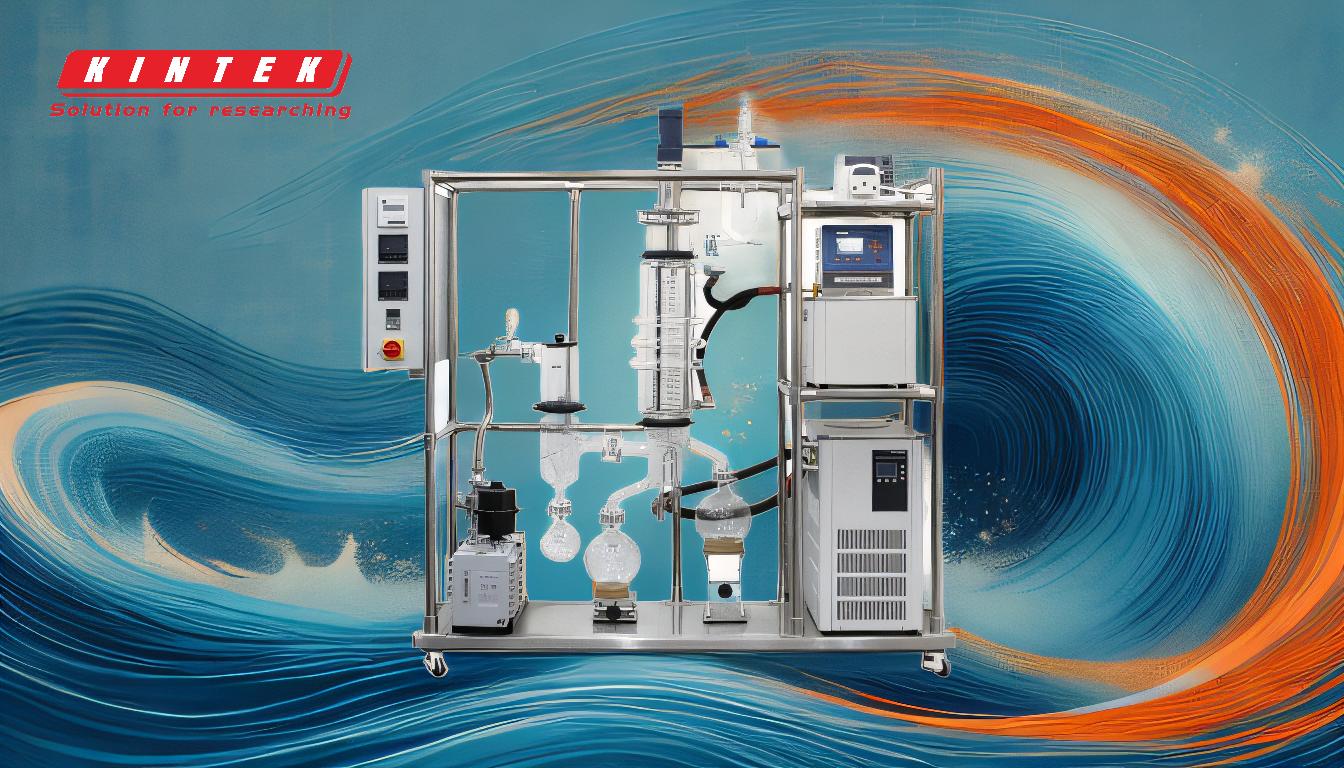
-
Lowering Boiling Points for Efficient Evaporation
- The vacuum pump reduces the pressure within the evaporation system, which directly lowers the boiling point of the solvent.
- This enables solvents to evaporate at much lower temperatures than they would under normal atmospheric pressure.
- For example, water, which typically boils at 100°C, can evaporate at room temperature under a strong vacuum.
- This feature is particularly beneficial for heat-sensitive compounds that might degrade or react at higher temperatures.
-
Faster Evaporation Rates
- By lowering the boiling point, the vacuum pump accelerates the evaporation process.
- This is especially useful in applications where time efficiency is critical, such as in laboratories or industrial settings.
- Faster evaporation also reduces the energy required to heat the system, contributing to cost savings and improved sustainability.
-
Gentler Processing of Heat-Sensitive Materials
- Many compounds, such as pharmaceuticals, biological samples, or delicate chemicals, are sensitive to high temperatures.
- The vacuum pump allows these materials to be processed at lower temperatures, preserving their integrity and preventing unwanted reactions.
- This gentler approach ensures higher yields and better-quality end products.
-
Maintaining Purity and Preventing Contamination
- The vacuum pump removes unwanted gases and vapors from the system, ensuring that only the desired solvent is evaporated.
- This prevents contamination from background gases, which could otherwise interfere with the process or compromise the purity of the extracted material.
- For example, in thin-film deposition processes, a vacuum ensures that evaporated particles reach the substrate without interacting with contaminants.
-
Precise Control Over Process Parameters
- Modern vacuum pumps are often paired with vacuum controllers, allowing users to set and maintain specific pressure levels.
- This precision enables fine-tuning of the evaporation process, making it adaptable to different solvents and materials.
- Adjustable vacuum levels also provide a quick way to influence the speed of evaporation, offering flexibility in process optimization.
-
Energy Efficiency and Safety
- By enabling evaporation at lower temperatures, the vacuum pump reduces the energy required to heat the system.
- This not only lowers operational costs but also minimizes the risk of overheating or thermal runaway, enhancing overall safety.
- Additionally, working at lower temperatures reduces the likelihood of hazardous reactions, making the process safer for operators.
-
Enabling Continuous Feed Systems
- In industrial applications, vacuum pumps help maintain a continuous feed system by ensuring a steady flow of solvents through the evaporator.
- This is essential for large-scale operations where uninterrupted processing is necessary to meet production targets.
-
Facilitating Controlled Deposition Processes
- In processes like thin-film deposition, the vacuum pump ensures that evaporated particles travel directly to the target substrate without interference.
- This control is crucial for achieving uniform thickness and high-quality coatings, which are vital in industries like electronics and optics.
In summary, the vacuum pump is a cornerstone of modern evaporation systems, providing critical functions that enhance efficiency, safety, and product quality. Its ability to lower boiling points, accelerate evaporation, and maintain a controlled environment makes it indispensable in both laboratory and industrial settings.
Summary Table:
Function | Benefits |
---|---|
Lower Boiling Points | Enables evaporation at reduced temperatures, ideal for heat-sensitive materials. |
Faster Evaporation Rates | Accelerates the process, saving time and energy. |
Gentle Processing | Preserves integrity of sensitive compounds, ensuring higher yields. |
Purity and Contamination Prevention | Removes unwanted gases, maintaining material purity. |
Precise Control | Allows fine-tuning of pressure levels for optimized evaporation. |
Energy Efficiency and Safety | Reduces energy costs and minimizes risks of overheating or hazardous reactions. |
Continuous Feed Systems | Ensures steady solvent flow for large-scale operations. |
Controlled Deposition Processes | Achieves uniform coatings in applications like thin-film deposition. |
Ready to optimize your evaporation process? Contact our experts today to learn more!