Sputtering is a critical process in thin film deposition, widely used in industries such as electronics, semiconductors, and optics. It involves bombarding a target material with high-energy ions, typically argon, to dislodge atoms that then deposit onto a substrate, forming a thin film. The significance of sputtering lies in its ability to produce high-quality, uniform coatings with precise control over film properties. This process is essential for manufacturing advanced devices, including semiconductors, solar panels, and optical coatings. The controlled environment, including gas pressure and energy levels, ensures efficient and consistent deposition, making sputtering a cornerstone of modern industrial applications.
Key Points Explained:
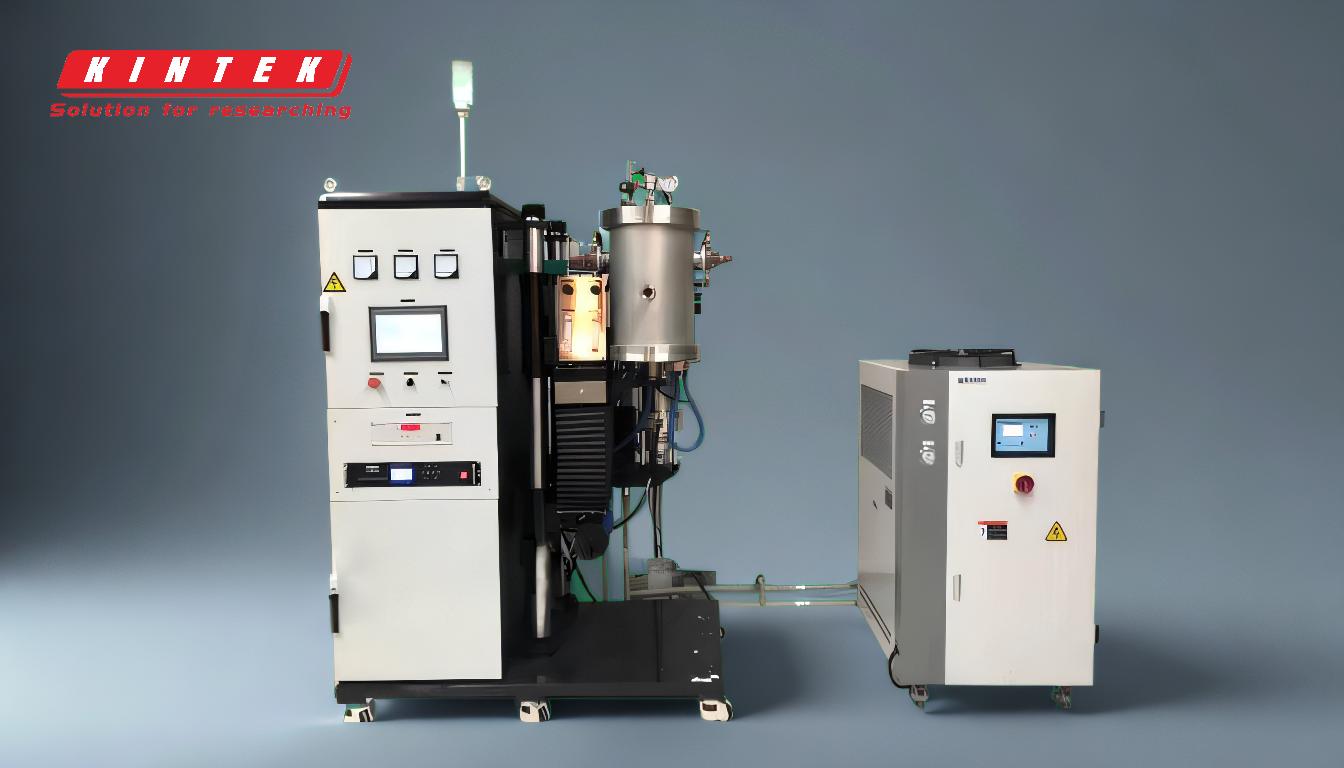
-
Mechanism of Sputtering:
- Sputtering involves bombarding a target material with high-energy ions, usually argon, to dislodge its atoms.
- These dislodged atoms travel through the chamber and deposit onto a substrate, forming a thin film.
- This process is highly controlled, ensuring uniform deposition and consistent film thickness.
-
Importance of Gas Pressure:
- The pressure of the sputtering gas, typically argon, must be carefully regulated.
- Proper gas pressure ensures the ions have the correct energy level to effectively bombard the target material.
- This control directly impacts the efficiency and quality of the thin film deposition.
-
Applications in Modern Industry:
- Sputtering, particularly RF magnetron sputtering, has been pivotal since its introduction in the 1970s.
- It is extensively used in the electronics and semiconductor industries for depositing thin films.
- The process enables precise control over film properties, facilitating advancements in various industrial applications.
-
Types of Sputtering:
- DC Sputtering: Involves direct current to generate ions, suitable for conductive materials. It results in highly uniform thin films due to low pressure and material characteristics.
- RF Sputtering: Uses radio frequency to generate ions, effective for both conductive and non-conductive materials. It offers enhanced control over film properties and is widely used in advanced applications.
-
Advantages of Sputtering:
- Produces high-quality, uniform coatings with precise thickness control.
- Suitable for a wide range of materials, including metals, alloys, and ceramics.
- Enables the deposition of complex multi-layer structures, essential for advanced technological applications.
-
Impact on Technological Advancements:
- Sputtering has been instrumental in the development of semiconductors, solar panels, and optical coatings.
- Its ability to produce consistent and high-performance thin films has driven innovations in electronics and renewable energy sectors.
- The process supports the miniaturization and performance enhancement of electronic devices.
In summary, sputtering is a foundational technology in thin film deposition, offering unparalleled precision and control. Its significance spans across various industries, enabling the production of advanced materials and devices that are integral to modern technology.
Summary Table:
Aspect | Description |
---|---|
Mechanism | Bombarding target material with high-energy ions to dislodge atoms for deposition. |
Key Control Factors | Gas pressure and energy levels ensure efficient and consistent thin film quality. |
Applications | Semiconductors, solar panels, optical coatings, and advanced electronics. |
Types of Sputtering | DC Sputtering (conductive materials) and RF Sputtering (conductive/non-conductive). |
Advantages | Uniform coatings, precise thickness control, and multi-layer deposition. |
Unlock the potential of sputtering for your industry—contact us today to learn more!