The speed of a reactor agitator is a critical parameter that depends on the specific application, the type of reactor, the properties of the materials being mixed, and the desired outcome of the agitation process. It is typically measured in revolutions per minute (RPM) and can range from very low speeds (e.g., 10-50 RPM for gentle mixing) to high speeds (e.g., 500-3000 RPM for intense mixing or dispersion). The optimal speed is determined by factors such as viscosity, density, and the type of agitator used (e.g., propeller, turbine, or paddle). Proper selection ensures efficient mixing, heat transfer, and reaction rates.
Key Points Explained:
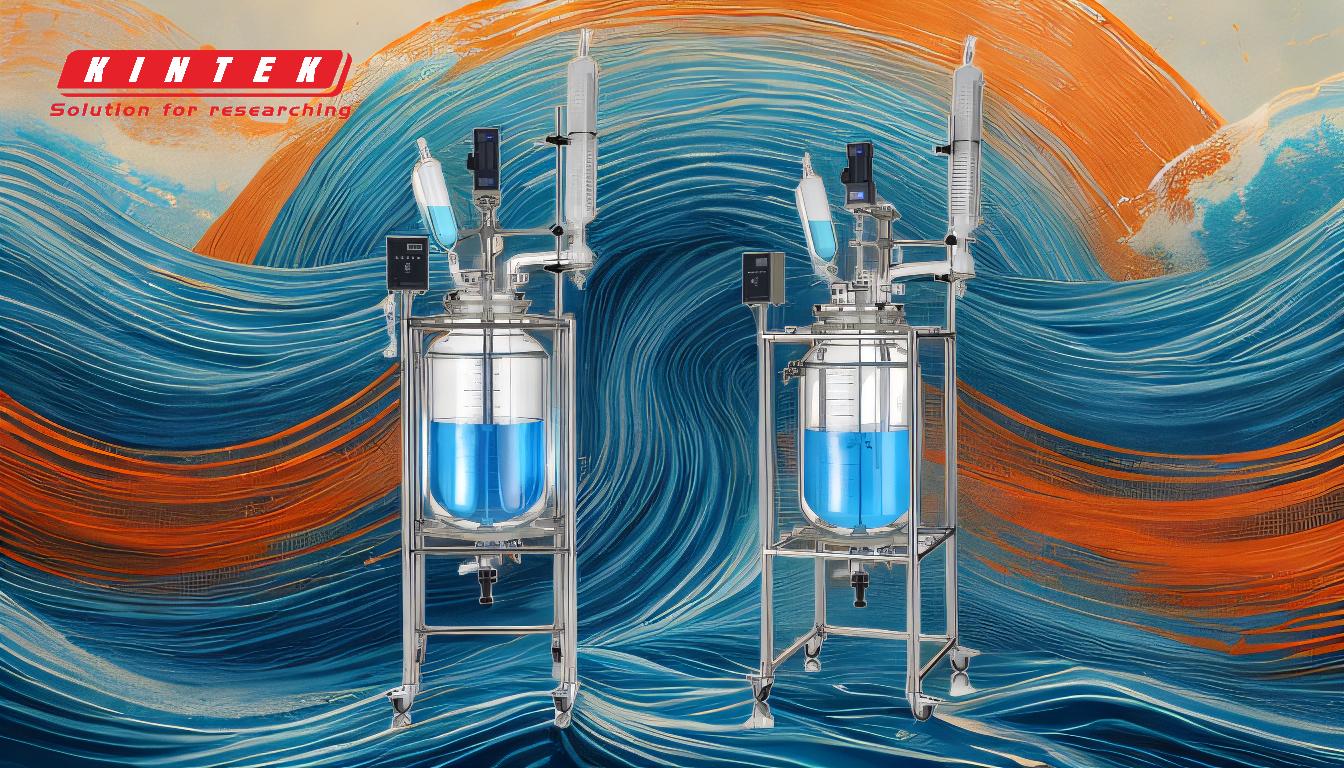
-
Definition and Importance of Reactor Agitator Speed
- The speed of a reactor agitator refers to how fast the agitator rotates, measured in RPM (revolutions per minute).
- It is a crucial parameter because it directly affects mixing efficiency, heat transfer, and the overall performance of the reactor.
- Improper speed selection can lead to inadequate mixing, poor reaction rates, or even damage to the equipment.
-
Factors Influencing Agitator Speed
-
Material Properties:
- Viscosity: High-viscosity fluids require slower speeds to avoid excessive power consumption and mechanical stress.
- Density: Denser materials may need higher speeds to achieve uniform mixing.
-
Reactor Design:
- The size and shape of the reactor influence the flow patterns and, consequently, the required speed.
-
Agitator Type:
- Different agitators (e.g., propellers, turbines, paddles) have varying speed requirements based on their design and application.
-
Process Requirements:
- The desired outcome (e.g., blending, dispersion, or suspension) dictates the speed range.
-
Material Properties:
-
Typical Speed Ranges for Different Applications
-
Low-Speed Mixing (10-50 RPM):
- Used for gentle mixing of high-viscosity fluids or shear-sensitive materials.
-
Medium-Speed Mixing (50-500 RPM):
- Suitable for general-purpose mixing in most chemical and pharmaceutical reactors.
-
High-Speed Mixing (500-3000 RPM):
- Employed for intense mixing, dispersion, or emulsification processes.
-
Low-Speed Mixing (10-50 RPM):
-
How to Determine the Optimal Speed
-
Empirical Testing:
- Conducting small-scale experiments to observe mixing efficiency and adjust speed accordingly.
-
Theoretical Calculations:
- Using formulas and models to estimate the required speed based on fluid dynamics and reactor geometry.
-
Manufacturer Recommendations:
- Consulting equipment specifications and guidelines provided by agitator manufacturers.
-
Empirical Testing:
-
Impact of Incorrect Speed Selection
-
Too Low:
- Inadequate mixing, leading to poor reaction rates, uneven temperature distribution, or settling of solids.
-
Too High:
- Excessive power consumption, mechanical wear, and potential damage to the agitator or reactor.
-
Too Low:
-
Advanced Considerations
-
Variable Speed Drives:
- Modern reactors often use variable speed drives to adjust agitator speed dynamically based on process requirements.
-
Computational Fluid Dynamics (CFD):
- Advanced simulations can predict flow patterns and optimize agitator speed for specific applications.
-
Variable Speed Drives:
By understanding these key points, equipment and consumable purchasers can make informed decisions about reactor agitators, ensuring optimal performance and longevity of the equipment.
Summary Table:
Factor | Description |
---|---|
Material Properties | Viscosity and density influence speed requirements. |
Reactor Design | Size and shape affect flow patterns and speed selection. |
Agitator Type | Propeller, turbine, or paddle designs have specific speed ranges. |
Process Requirements | Desired outcomes (e.g., blending, dispersion) dictate speed. |
Typical Speed Ranges | Low (10-50 RPM), Medium (50-500 RPM), High (500-3000 RPM). |
Optimal Speed Methods | Empirical testing, theoretical calculations, and manufacturer recommendations. |
Need help selecting the right reactor agitator speed? Contact our experts today for tailored solutions!