The sputtering process in metals is a physical vapor deposition (PVD) technique used to deposit thin, functional coatings onto substrates. It involves bombarding a target material (usually a metal) with high-energy ions, causing atoms to be ejected from the target surface. These ejected atoms are then deposited onto a substrate, forming a thin, uniform coating. The process occurs in a vacuum chamber, often using argon gas to create a plasma. Sputtering is widely used in industries such as semiconductor manufacturing, optics, and microscopy due to its ability to create precise, durable, and high-quality coatings on complex surfaces.
Key Points Explained:
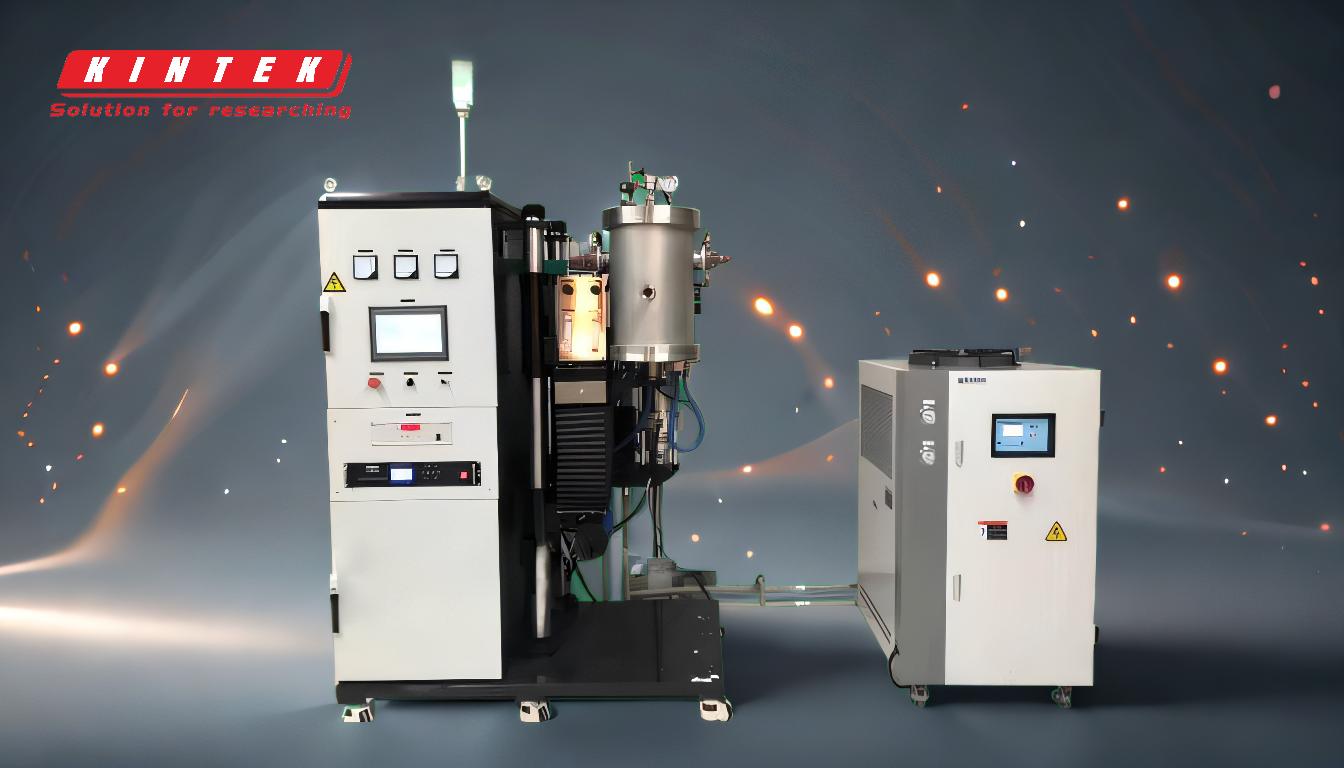
-
Definition and Purpose of Sputtering:
- Sputtering is a physical vapor deposition (PVD) process used to deposit thin, functional coatings onto substrates.
- It is widely used in industries like semiconductor manufacturing, optics, and microscopy for creating precise and durable coatings.
-
The Sputtering Mechanism:
- The process involves bombarding a target material (typically a metal) with high-energy ions, usually argon ions.
- This bombardment causes atoms to be ejected from the target surface through a momentum transfer process.
- The ejected atoms travel through the vacuum chamber and deposit onto the substrate, forming a thin, uniform coating.
-
Components Involved:
- Target Material: The material to be deposited, often a metal, is bonded or clamped to a cathode.
- Substrate: The surface onto which the ejected atoms are deposited.
- Vacuum Chamber: The environment where the sputtering process takes place, ensuring minimal contamination.
- Argon Gas: Used to create a plasma, which ionizes and bombards the target material.
-
Role of Plasma and Ion Bombardment:
- A glow discharge is formed between the cathode (target) and anode (substrate) using argon gas.
- Free electrons collide with argon atoms, converting them into positively charged ions.
- These ions bombard the target material, causing atoms to be ejected and deposited onto the substrate.
-
Applications of Sputtering:
- Semiconductor Manufacturing: Used for depositing thin films in integrated circuit processing.
- Optics: Applied in creating anti-reflective or high-emissivity coatings on glass.
- Microscopy: Used to coat specimens with conductive thin metal films for scanning electron microscopy (SEM).
- Cutting Tools: Enhances durability and performance through protective coatings.
- CD/DVD Manufacturing: Used for creating reflective layers.
-
Advantages of Sputtering:
- Uniform Coatings: Produces even and consistent coatings on complex, three-dimensional surfaces.
- Low-Temperature Process: Suitable for heat-sensitive materials like biological samples.
- Strong Atomic Bonds: Forms durable and permanent coatings at an atomic level.
- Versatility: Can deposit a wide range of materials, including metals, alloys, and compounds.
-
Challenges and Considerations:
- Heat Management: The process generates heat, requiring specialized chilling systems to maintain stability.
- Cost and Complexity: Requires specialized equipment and controlled environments, making it more expensive than some other coating methods.
- Material Limitations: Not all materials are suitable for sputtering, and the process may require specific target materials.
-
Comparison with Other Coating Techniques:
- Sputtering differs from evaporation-based PVD techniques, as it relies on momentum transfer rather than thermal energy.
- It offers better control over film thickness and uniformity compared to chemical vapor deposition (CVD).
By understanding these key points, one can appreciate the precision, versatility, and industrial significance of the sputtering process in metals. Its ability to create high-quality, durable coatings makes it a cornerstone of modern manufacturing and technology.
Summary Table:
Aspect | Details |
---|---|
Definition | Physical vapor deposition (PVD) technique for thin, functional coatings. |
Mechanism | Bombards target material with high-energy ions, ejecting atoms for coating. |
Key Components | Target material, substrate, vacuum chamber, argon gas. |
Applications | Semiconductors, optics, microscopy, cutting tools, CD/DVD manufacturing. |
Advantages | Uniform coatings, low-temperature process, strong atomic bonds, versatility. |
Challenges | Heat management, cost, material limitations. |
Interested in learning more about sputtering for your applications? Contact our experts today!