The sputtering yield is a critical parameter in sputter deposition processes, representing the average number of atoms ejected from a target material per incident ion. It is influenced by several factors, including the energy and mass of the bombarding ions, the angle of incidence, the mass of the target atoms, and the binding energy of the target material. Additionally, for crystalline materials, the orientation of the crystal axes relative to the surface plays a role. Understanding these factors is essential for optimizing sputtering processes, as the yield directly impacts the deposition rate and the quality of the deposited film.
Key Points Explained:
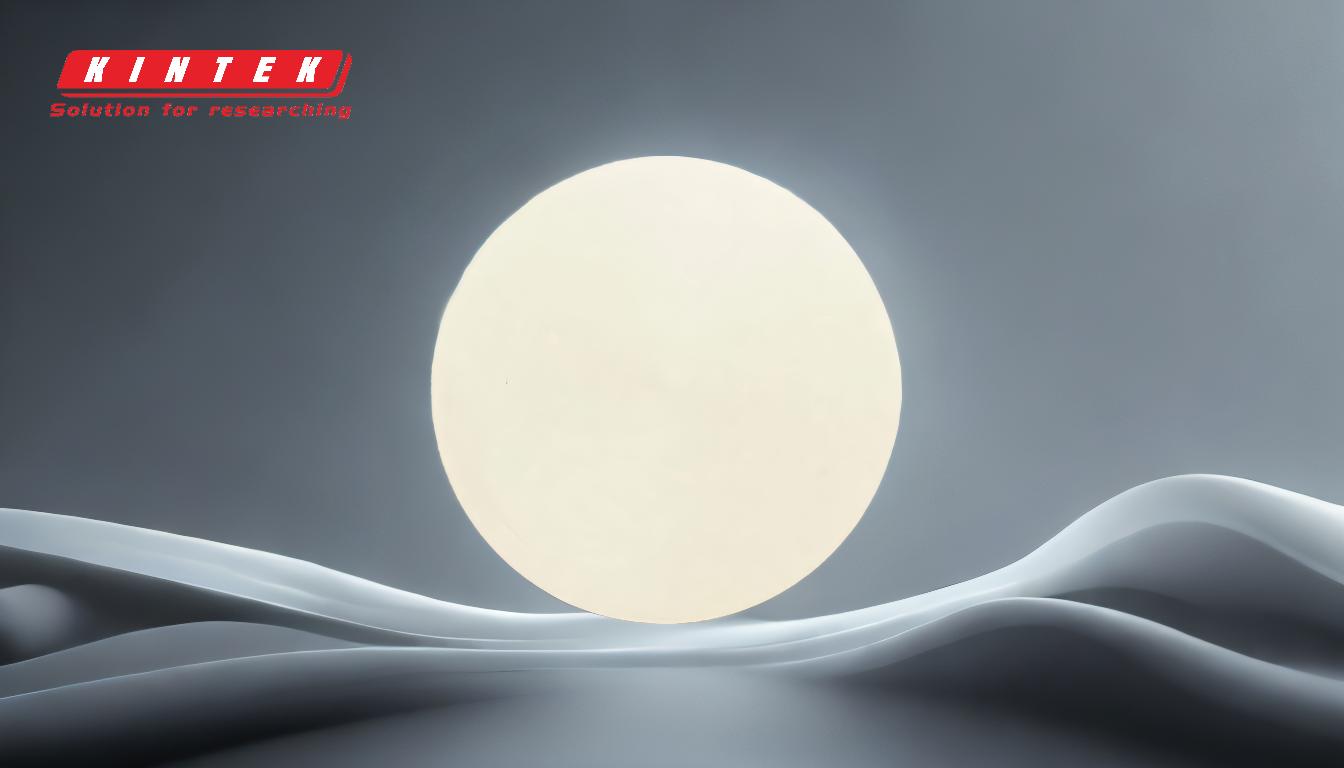
-
Definition of Sputtering Yield:
- The sputtering yield is defined as the average number of atoms ejected from the surface of a target material per incident ion. This metric is crucial in sputter deposition processes as it directly affects the deposition rate and efficiency of the process.
-
Factors Influencing Sputtering Yield:
- Energy of Incident Ions: The sputtering yield increases with the energy of the incident ions, typically in the range of 10 to 5000 eV. Higher energy ions transfer more energy to the target atoms, leading to more effective ejection.
- Mass of Incident Ions and Target Atoms: Heavier ions and target atoms generally result in higher sputtering yields due to more effective momentum transfer during collisions.
- Angle of Incidence: The angle at which ions collide with the target surface affects the yield. Off-normal angles can increase the yield by enhancing the momentum transfer to surface atoms.
- Binding Energy of Target Atoms: The strength of the bonds between atoms in the target material influences the yield. Higher binding energies require more energy to eject atoms, potentially reducing the yield.
- Crystal Structure and Orientation: For crystalline materials, the orientation of the crystal axes relative to the surface can affect the yield due to differences in atomic packing and binding energies along different crystallographic directions.
-
Practical Implications:
- Deposition Rate: A higher sputtering yield leads to a higher deposition rate, which is beneficial for increasing throughput in manufacturing processes.
- Film Quality: The energy and angle of incidence can influence the kinetic energy and direction of emitted particles, affecting the uniformity and quality of the deposited film.
- Process Optimization: Understanding the factors that influence sputtering yield allows for the optimization of sputtering conditions (e.g., ion energy, angle of incidence) to achieve desired deposition rates and film properties.
-
Additional Considerations:
- Chamber Pressure: The pressure within the sputtering chamber can influence the yield by affecting the mean free path of the ions and the coverage of the substrate.
- Power Source: The type of power source (DC or RF) used in the sputtering process can affect the yield and compatibility with different materials, as well as the overall cost of the process.
- Surface Mobility: The excess energy of metal ions can increase surface mobility during deposition, impacting the microstructure and quality of the deposited film.
In summary, the sputtering yield is a complex parameter influenced by multiple factors, each of which must be carefully considered to optimize the sputtering process for specific applications. By understanding and controlling these factors, it is possible to achieve efficient and high-quality thin film deposition.
Summary Table:
Factor | Impact on Sputtering Yield |
---|---|
Energy of Incident Ions | Higher energy increases yield by transferring more energy to target atoms. |
Mass of Ions & Target | Heavier ions and target atoms enhance yield due to effective momentum transfer. |
Angle of Incidence | Off-normal angles can increase yield by improving momentum transfer to surface atoms. |
Binding Energy | Higher binding energy may reduce yield as more energy is needed to eject atoms. |
Crystal Orientation | Crystal axis orientation affects yield due to differences in atomic packing and binding energy. |
Chamber Pressure | Influences yield by affecting ion mean free path and substrate coverage. |
Power Source | DC or RF power sources affect yield, material compatibility, and process cost. |
Surface Mobility | Excess energy increases surface mobility, impacting film microstructure and quality. |
Optimize your sputtering process for superior thin film deposition—contact our experts today!