Hot isostatic pressing (HIP) is a material processing method that applies high temperatures (ranging from several hundreds to 2000°C) and isostatic pressure (ranging from several tens to 200 MPa or higher) simultaneously to compress materials. The pressure is applied uniformly in all directions using a gas, typically argon, as the pressure medium. The process is used to densify materials, eliminate defects, and improve mechanical properties. The pressure range for HIP typically falls between 15,000 psi (100 MPa) and 45,000 psi (310 MPa), depending on the material and application. This method is widely used in industries such as aerospace, automotive, and medical devices to produce high-performance components with minimal porosity and enhanced structural integrity.
Key Points Explained:
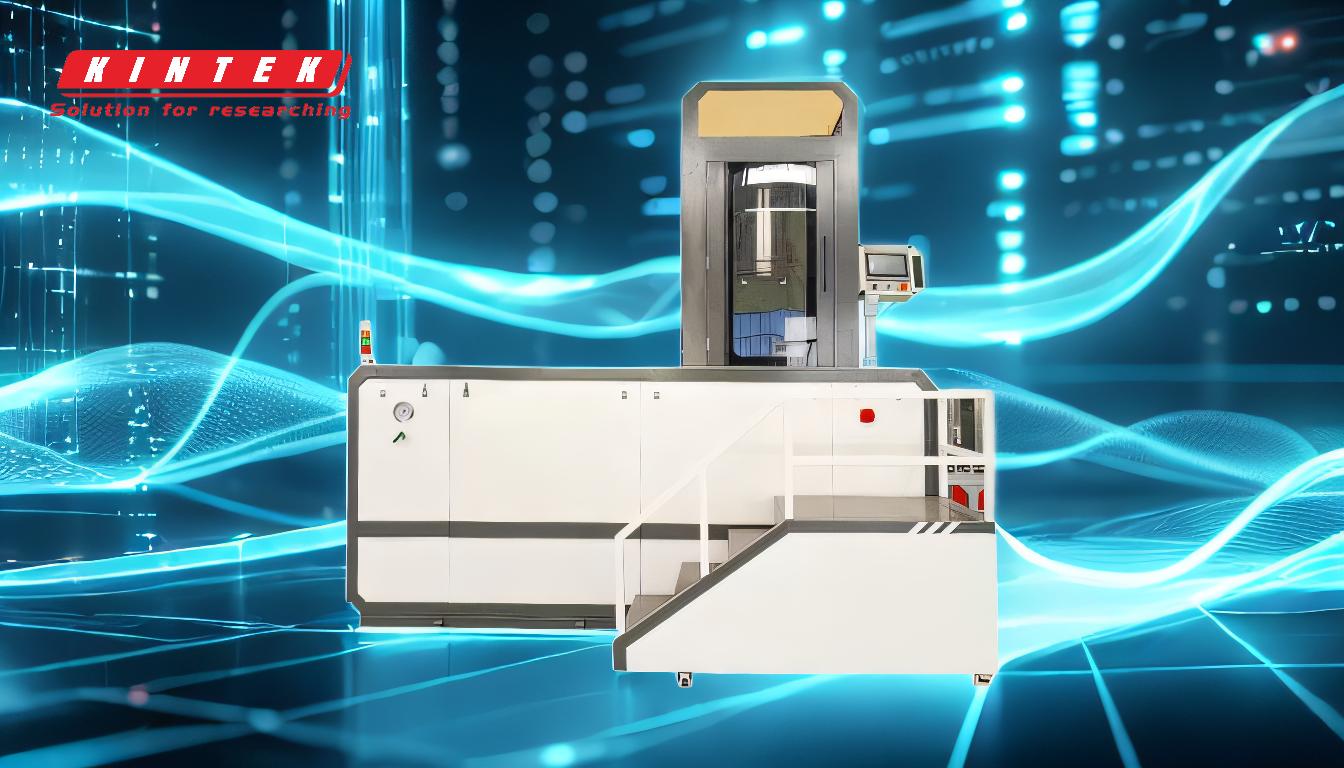
-
Definition of Hot Isostatic Pressing (HIP):
- HIP is a material processing technique that combines high temperature and high isostatic pressure to densify materials.
- The process involves applying uniform pressure in all directions using a gas medium, typically argon, to eliminate voids and defects in the material.
-
Pressure Range in HIP:
- The typical pressure range for HIP is between 15,000 psi (100 MPa) and 45,000 psi (310 MPa).
- This range can vary depending on the material being processed and the desired outcome, such as densification or sintering.
-
Temperature Range in HIP:
- The temperature during HIP can range from several hundred degrees Celsius to 2000°C.
- High temperatures are necessary to facilitate mechanisms like plastic deformation, creep, and diffusion, which contribute to densification.
-
Pressure Medium:
- Argon is the most commonly used pressure medium in HIP due to its inert properties and ability to maintain uniform pressure distribution.
-
Mechanisms of Densification:
- Plastic Deformation: Initial application of pressure causes voids in the material to collapse.
- Creep and Diffusion: These mechanisms further densify the material by eliminating pores and creating a defect-free structure.
-
Applications of HIP:
- HIP is used in industries such as aerospace, automotive, and medical devices to produce high-performance components.
- It is particularly useful for materials that require high strength, minimal porosity, and enhanced mechanical properties.
-
Equipment and Control:
- HIP equipment comes in various sizes and configurations, with chambers that can be loaded from the top or bottom.
- The process is controlled by computers, which program the equipment to achieve precise temperature, pressure, and time settings.
-
Benefits of HIP:
- Uniform Pressure Application: HIP applies equal pressure in all directions, ensuring consistent densification without altering the shape of the component.
- Defect Elimination: The process effectively removes pores and defects, resulting in materials with superior mechanical properties.
-
Comparison with Warm Isostatic Pressing:
- Warm isostatic pressing typically operates at lower temperatures and pressures compared to HIP.
- The pressure in warm isostatic pressing is around 300 MPa, which is higher than the typical HIP range but still within the capabilities of some HIP systems.
-
Material-Specific Requirements:
- The pressure and temperature settings in HIP are tailored to the specific material being processed.
- For example, certain high-performance alloys or ceramics may require pressures at the upper end of the range (up to 45,000 psi or 310 MPa) to achieve optimal densification.
By understanding these key points, equipment and consumable purchasers can make informed decisions about the specifications and capabilities of HIP systems required for their specific applications. The ability to control pressure and temperature precisely is crucial for achieving the desired material properties and ensuring the success of the HIP process.
Summary Table:
Key Aspect | Details |
---|---|
Pressure Range | 15,000 psi (100 MPa) to 45,000 psi (310 MPa) |
Temperature Range | Several hundred °C to 2000°C |
Pressure Medium | Argon (inert gas) |
Densification Mechanisms | Plastic deformation, creep, and diffusion |
Applications | Aerospace, automotive, medical devices |
Benefits | Uniform pressure, defect elimination, enhanced mechanical properties |
Ready to optimize your material processing? Contact us today to learn more about HIP systems!