The carrier gas used for aluminum (Al) deposition in a sputtering system is typically argon (Ar). Argon is an inert gas, which means it does not react with the target material (in this case, aluminum) or the substrate. Its atomic weight is close to that of aluminum, making it efficient for momentum transfer during the sputtering process. This ensures that aluminum atoms are effectively ejected from the target and deposited onto the substrate. While other inert gases like neon, krypton, or xenon can be used depending on the target material's atomic weight, argon is the most commonly used gas for aluminum deposition due to its balance of cost, availability, and effectiveness.
Key Points Explained:
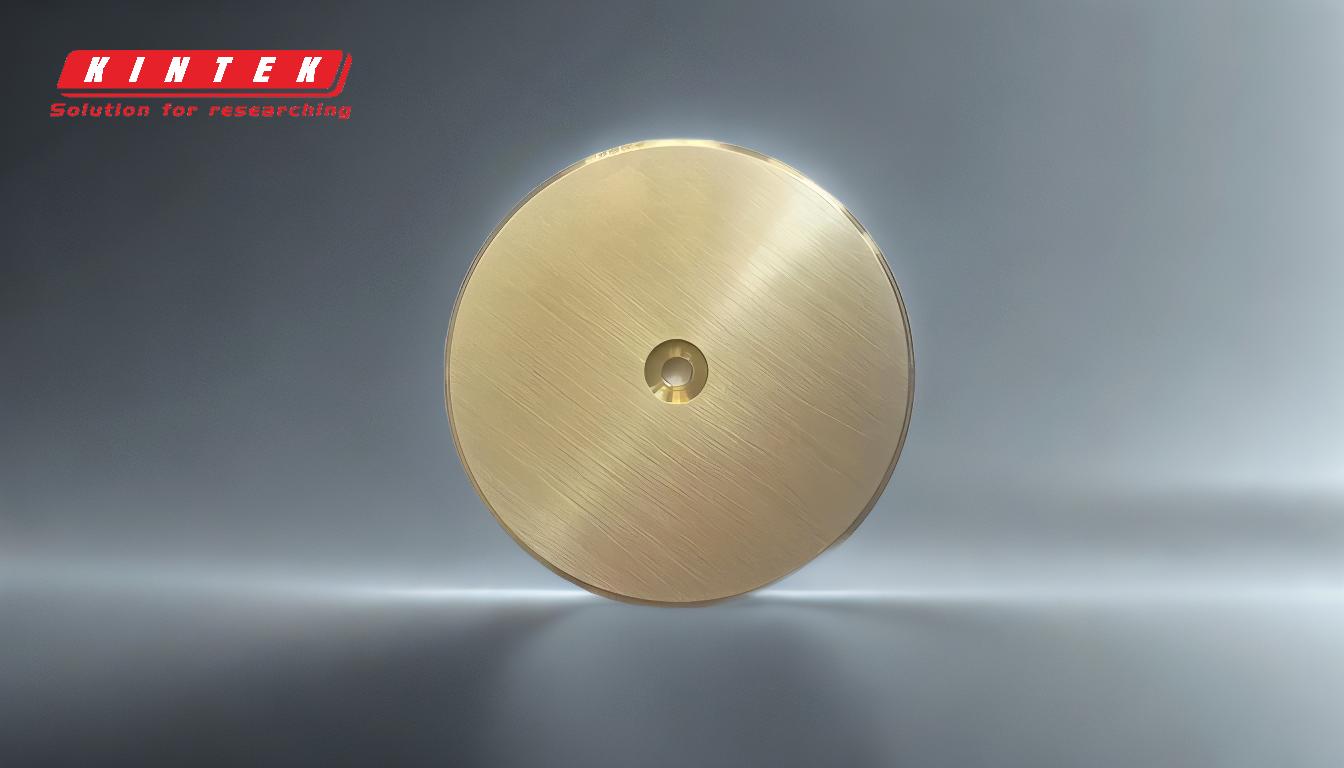
-
Argon as the Primary Carrier Gas:
- Argon is the most commonly used gas for aluminum deposition in sputtering systems.
- It is an inert gas, meaning it does not chemically react with the aluminum target or the substrate, ensuring a clean deposition process.
-
Efficient Momentum Transfer:
- The atomic weight of argon (40 amu) is close to that of aluminum (27 amu), making it ideal for efficient momentum transfer during sputtering.
- This ensures that aluminum atoms are effectively ejected from the target and deposited onto the substrate.
-
Inert Gas Properties:
- Inert gases like argon are preferred in sputtering because they do not interfere with the chemical composition of the target material or the deposited film.
- This is particularly important for aluminum deposition, where maintaining the purity of the deposited layer is critical.
-
Comparison with Other Inert Gases:
- Neon, krypton, and xenon are also inert gases used in sputtering, but their selection depends on the atomic weight of the target material.
- Neon is used for lighter elements, while krypton and xenon are used for heavier elements. For aluminum, argon is the most suitable choice.
-
Reactive Gases:
- While reactive gases like oxygen or nitrogen are used in reactive sputtering to deposit compounds (e.g., oxides or nitrides), they are not suitable for pure aluminum deposition.
- For aluminum deposition, the focus is on maintaining the metal's purity, which is best achieved using inert gases like argon.
-
Cost and Availability:
- Argon is widely available and relatively inexpensive compared to other inert gases like krypton or xenon.
- This makes it a practical choice for industrial and research applications involving aluminum deposition.
By using argon as the carrier gas, the sputtering process ensures high-quality aluminum deposition with minimal contamination, making it the go-to choice for this application.
Summary Table:
Aspect | Details |
---|---|
Primary Carrier Gas | Argon (Ar) is the most commonly used gas for aluminum deposition. |
Inert Gas Properties | Argon does not react with aluminum or the substrate, ensuring clean deposition. |
Momentum Transfer | Argon's atomic weight (40 amu) is close to aluminum (27 amu), enabling efficient sputtering. |
Alternative Gases | Neon, krypton, or xenon can be used but are less common for aluminum. |
Reactive Gases | Oxygen or nitrogen are unsuitable for pure aluminum deposition. |
Cost & Availability | Argon is cost-effective and widely available, making it ideal for industrial use. |
Need expert advice on sputtering systems? Contact us today to learn more about aluminum deposition!