A vacuum is essential in evaporators to facilitate efficient and controlled evaporation processes. It serves multiple purposes, including lowering the boiling point of solvents, protecting heat-sensitive materials, preventing contamination, and enabling precise control over the evaporation rate. By creating a low-pressure environment, vacuum evaporation allows for gentle distillation, reduces the risk of sample degradation, and ensures the integrity of the process. Additionally, vacuum systems are critical for handling high-boiling solvents and achieving consistent results in applications like rotary evaporation and thin-film deposition. Overall, vacuum technology enhances the efficiency, safety, and quality of evaporation processes.
Key Points Explained:
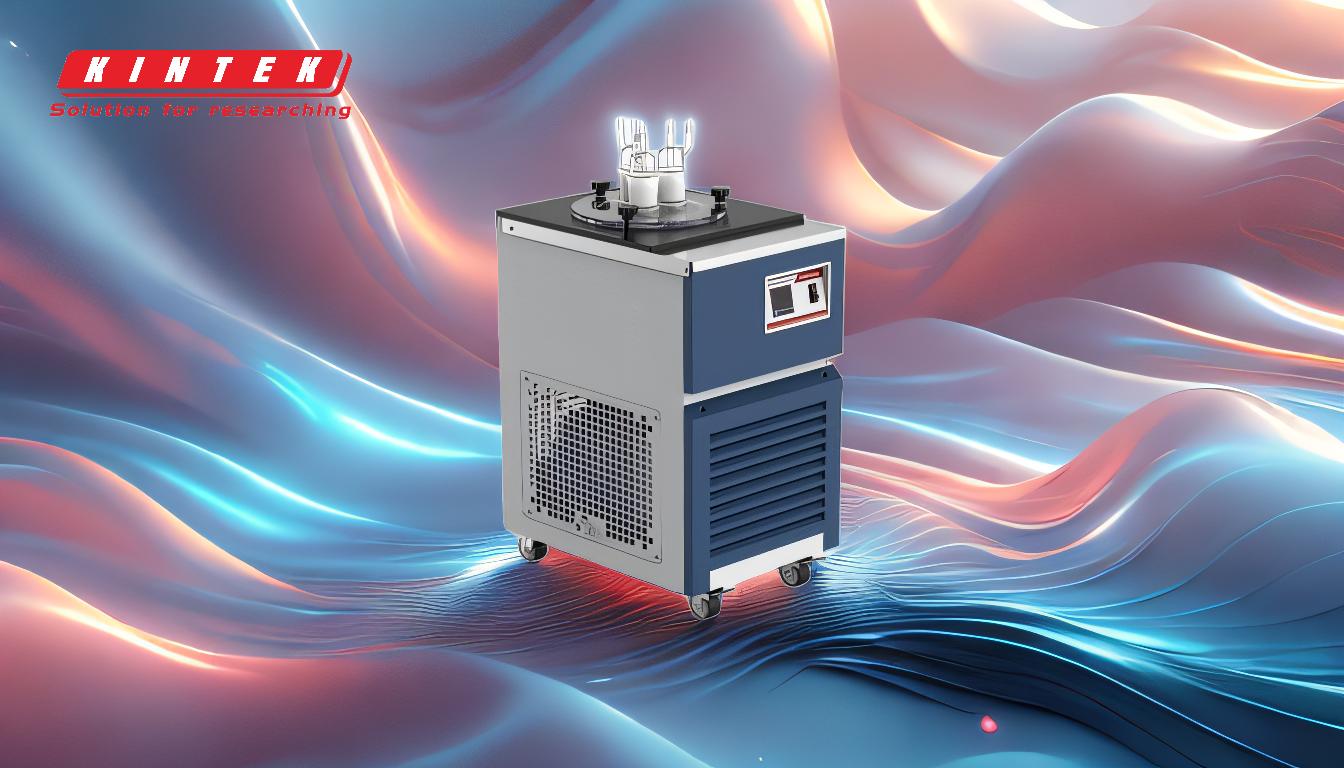
-
Lowering the Boiling Point of Solvents
- A vacuum reduces the pressure inside the evaporator, which lowers the boiling point of the solvent.
- This allows evaporation to occur at lower temperatures, protecting heat-sensitive materials from degradation.
- For example, high-boiling solvents like DMSO can be evaporated at modest temperatures under vacuum, which would otherwise require excessive heat.
-
Protecting Heat-Sensitive Materials
- Many substances, such as biological samples or thermolabile compounds, are sensitive to high temperatures.
- Vacuum evaporation enables gentle distillation, minimizing the risk of thermal damage.
- This is particularly important in applications like rotary evaporation, where precise control over temperature and pressure is critical.
-
Preventing Contamination
- A vacuum removes background gases and other vapors that are not from the desired source material.
- This ensures that evaporated particles travel directly to the deposition target without interacting with contaminants.
- Contamination can lead to reduced vapor reaching the substrate, uneven deposition, and difficulty in controlling the thickness of the substrate.
-
Enhancing Process Control
- Vacuum systems allow for precise control of pressure, which directly influences the evaporation rate.
- By adjusting the vacuum level, operators can achieve the desired evaporation rate without raising the bath temperature excessively.
- This results in controlled and even evaporation, improving the separation of solvents from products.
-
Increasing Efficiency and Reducing Process Time
- Vacuum evaporation can significantly increase the evaporation rate compared to atmospheric pressure conditions.
- This reduces the overall process time, making it more efficient for industrial and laboratory applications.
- For example, vacuum evaporation is used to concentrate solutions and reduce the volume of wastewater in industrial processes.
-
Handling High-Boiling Solvents
- High-boiling solvents, such as DMSO, require significant energy to evaporate under normal conditions.
- A vacuum lowers the boiling point, enabling these solvents to evaporate at lower temperatures.
- This makes vacuum pumps a critical component in applications involving high-boiling solvents.
-
Applications in Thin-Film Deposition
- In processes like physical vapor deposition (PVD), a vacuum ensures that evaporated particles travel directly to the substrate without interference from background gases.
- This results in high-quality thin films with controlled thickness and minimal contamination.
-
Gentle Separation of Mixtures
- Vacuum evaporation is ideal for separating mixtures with different boiling points, especially when dealing with heat-sensitive substances.
- The ability to evaporate components at lower temperatures ensures that each substance is separated without thermal degradation.
-
Energy Efficiency
- By lowering the boiling point, vacuum evaporation reduces the energy required to achieve evaporation.
- This makes the process more energy-efficient compared to traditional evaporation methods that rely solely on heat.
-
Versatility in Industrial and Laboratory Settings
- Vacuum evaporation is widely used in industries for wastewater treatment, concentration of solutions, and solvent recovery.
- In laboratories, it is essential for processes like rotary evaporation, where precise control over temperature and pressure is necessary.
In summary, the use of a vacuum in evaporators is indispensable for achieving efficient, controlled, and contamination-free evaporation processes. It enables the handling of heat-sensitive materials, reduces energy consumption, and ensures high-quality results in both industrial and laboratory applications.
Summary Table:
Key Benefit | Description |
---|---|
Lower Boiling Points | Reduces pressure to evaporate solvents at lower temperatures, protecting materials. |
Protects Heat-Sensitive Materials | Enables gentle distillation, minimizing thermal damage to sensitive substances. |
Prevents Contamination | Removes background gases, ensuring pure evaporation and deposition. |
Enhances Process Control | Allows precise control of pressure for consistent evaporation rates. |
Increases Efficiency | Speeds up evaporation, reducing process time and energy consumption. |
Handles High-Boiling Solvents | Lowers boiling points, making evaporation of high-boiling solvents efficient. |
Energy Efficiency | Reduces energy requirements compared to traditional evaporation methods. |
Versatile Applications | Used in industries and labs for solvent recovery, wastewater treatment, and more. |
Learn how vacuum evaporators can optimize your processes—contact our experts today!