Water Purification Equipment
Ultrapure Water Machine
Ultrapure water machines employ a multi-stage purification process to achieve exceptionally high levels of water purity. This process begins with pretreatment, where large particulate matter and sediments are removed through filtration and sedimentation. Following this, reverse osmosis technology is utilized to eliminate dissolved salts, ions, and smaller particles by applying pressure to force water through a semi-permeable membrane.
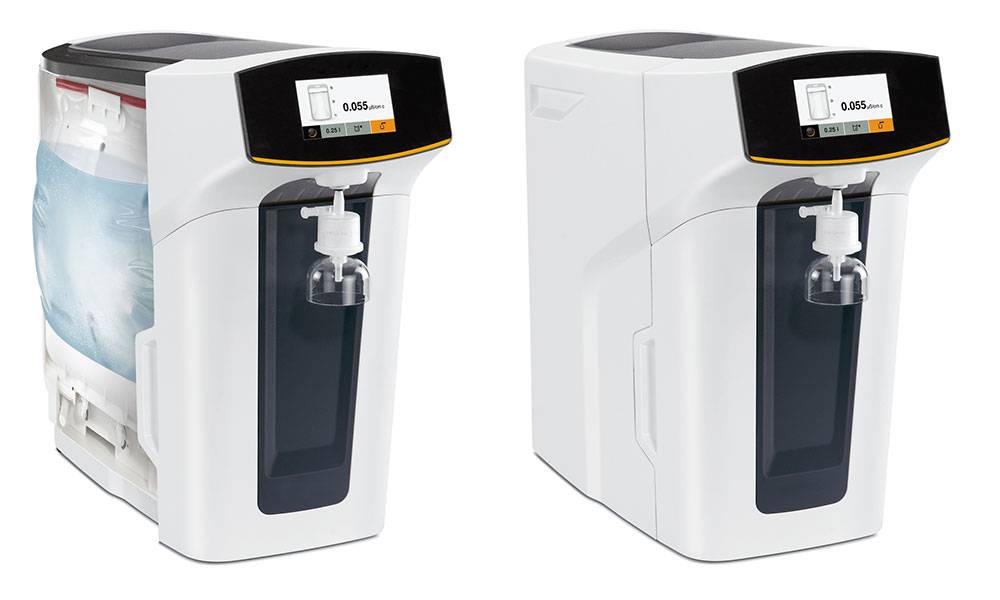
Subsequently, ultrapurification treatment is conducted to further refine the water by removing any remaining impurities, including colloidal substances, gases, and organic matter that are not dissociated. This stage often involves the use of advanced filtration media and ultraviolet (UV) sterilization to ensure the water meets stringent purity standards.
Finally, post-treatment methods are applied to stabilize the water quality and ensure it remains ultrapure through storage and distribution. This can include the addition of stabilizers or the use of holding tanks with minimal exposure to air and contaminants.
The result is water with conductivity levels approaching zero, free from virtually all conductive media, colloids, gases, and organic substances. This level of purity is essential for applications in laboratories, pharmaceuticals, and electronics manufacturing, where even trace amounts of impurities can significantly impact experimental outcomes or product quality.
Distilled Water Device
Distilled water devices are indispensable tools in various sectors such as pharmaceuticals, laboratory preparations, and other specialized departments. These devices operate on a fundamental scientific principle: when a liquid is heated, it vaporizes, and upon cooling, this vapor condenses back into a liquid state. This process effectively removes impurities, resulting in distilled water that is significantly purer than its tap water counterpart.
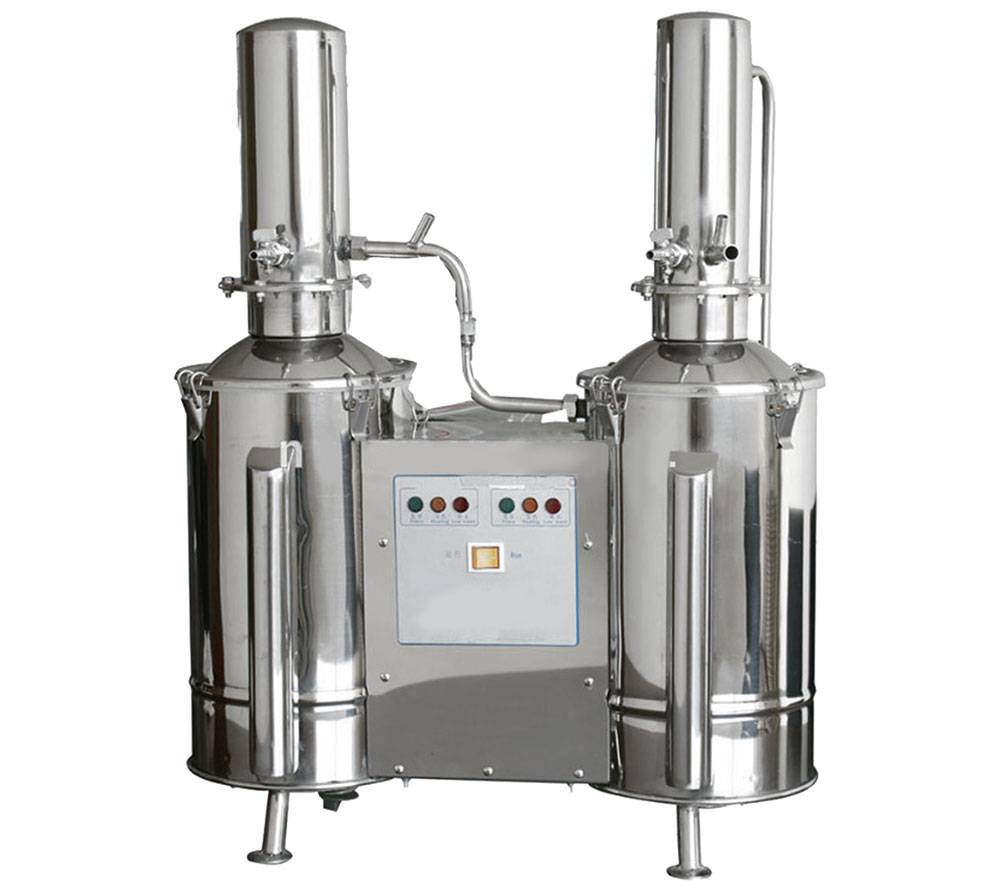
In the pharmaceutical industry, the purity of distilled water is crucial for ensuring the safety and efficacy of medications. Similarly, in laboratories, distilled water is essential for accurate and reliable scientific experiments, where even trace amounts of contaminants can skew results. The distillation process not only eliminates particulate matter but also removes dissolved gases and organic compounds, making it a preferred method for obtaining high-purity water.
The versatility of distilled water devices extends beyond just water purification. They are also used in applications where controlled humidity and temperature are critical, such as in the storage of sensitive biological samples or in the calibration of laboratory equipment. The ability to produce consistently high-quality distilled water makes these devices an invaluable asset in maintaining the integrity of various scientific and industrial processes.
Solvent Evaporation Equipment
Rotary Evaporator
A rotary evaporator, often abbreviated as rotavap, is a crucial piece of laboratory equipment designed for the efficient removal of solvents from samples through a process known as "evaporation under reduced pressure." This method leverages the principles of vacuum distillation to lower the boiling point of the solvent, making it possible to distill volatile solvents at temperatures significantly below their normal boiling points.
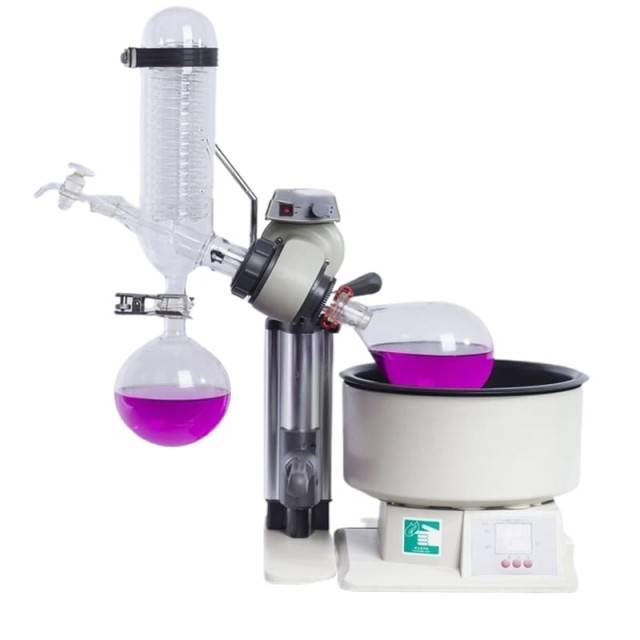
The rotary evaporator system typically includes several key components: a motor that drives the rotation of the distillation flask, a heating bath that provides the necessary thermal energy to the flask, a condenser that cools and condenses the solvent vapors, and a vacuum pump that creates the reduced pressure environment. The distillation flask, usually a round-bottom design, is filled to approximately 50% of its capacity with the solvent-containing sample.
When the system is in operation, the flask is rotated at speeds ranging from 150 to 200 revolutions per minute (rpm). This rotation creates a thin film of the solution on the inner surface of the flask, significantly increasing the surface area available for evaporation. Simultaneously, the water bath is heated to a temperature between 30-40°C, while the condenser is chilled to a temperature range of -10°C to 0°C using a recirculating chiller.
The application of a controlled vacuum further enhances the efficiency of the process by lowering the boiling point of the solvent. For instance, in the case of ethanol, setting the vacuum appropriately can achieve an ethanol vapor temperature of 15-20°C. As the solvent evaporates, it passes through the condenser where it cools and condenses, eventually collecting in a separate receiving flask. This meticulous control over temperature and pressure ensures that the solvent removal process is both efficient and reproducible.
In summary, the rotary evaporator is a sophisticated tool that combines rotation, heat, and vacuum to facilitate the continuous and controlled distillation of volatile solvents, making it indispensable in various laboratory applications.
Parallel Evaporator
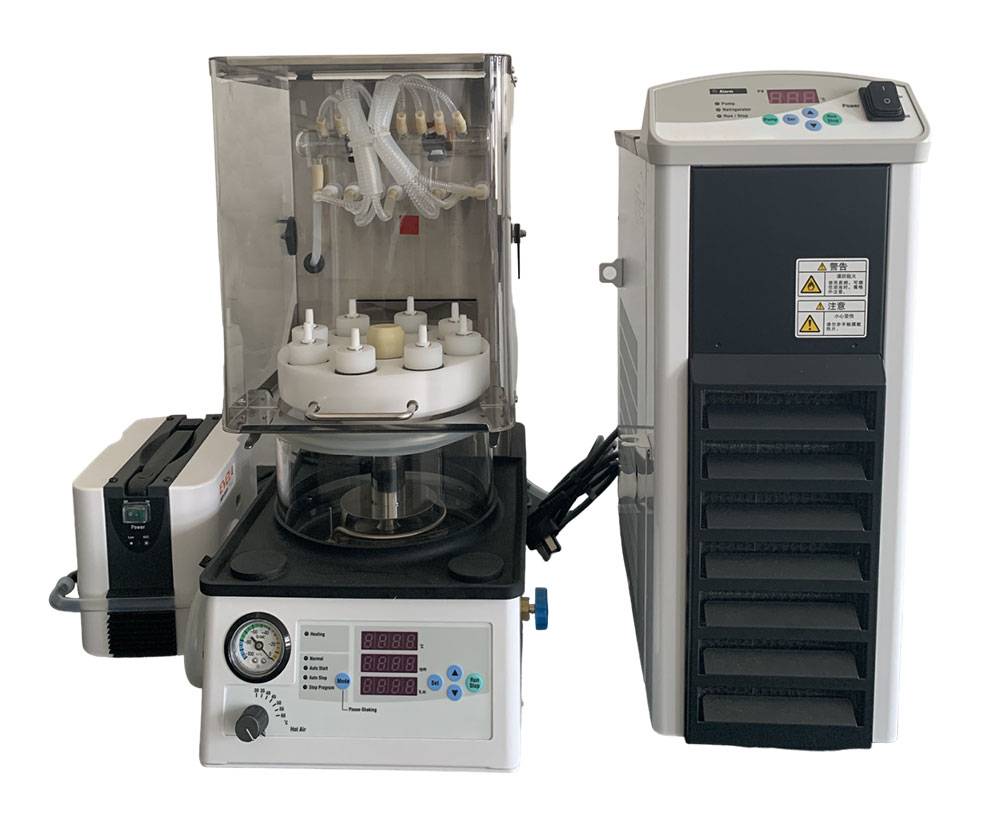
The parallel evaporator is a sophisticated instrument designed to expedite the evaporation process for multiple samples simultaneously, making it particularly adept at handling solvents with high boiling points. This efficiency is achieved through the creation of a vortex within each sample tube, which significantly increases the surface area exposed to the evaporation process. This swirling motion, coupled with the application of vacuum, enhances the rate of vaporization, thereby accelerating the overall process.
Feature | Description |
---|---|
Sample Capacity | Supports a variety of test tube racks, accommodating from 4 to 96 positions. |
Volume Range | Capable of handling single samples ranging from 0.5 to 500ml. |
Vacuum Enhancement | Utilizes vacuum pumps to reduce pressure, further boosting evaporation rates. |
Temperature Control | Incorporates heaters to increase sample temperature, aiding in faster evaporation. |
Cold Trap | Essential for collecting solvent gases, preventing sample loss and cross-contamination. |
While the vortex effect is highly effective in promoting rapid evaporation, it does have limitations. The g-force generated by the vortex is insufficient to prevent bumping, a phenomenon where liquid samples froth and spill out of their containers. This can lead to potential sample loss and cross-contamination, issues that are more effectively managed by centrifugal evaporation methods.
Advanced parallel evaporators mitigate these risks by integrating vacuum pumps and heaters, which not only reduce pressure but also elevate temperatures, further accelerating the evaporation process. Additionally, the inclusion of a cold trap ensures that solvent gases are efficiently collected, thereby minimizing sample loss and contamination. This multi-faceted approach makes parallel evaporators a versatile and efficient choice for laboratories dealing with a wide range of solvent samples.
Molecular Distillation
Molecular distillation is a specialized form of vacuum distillation that operates at extremely low pressures, typically below 0.01 torr (1.3 Pa). This method is characterized by the free molecular flow regime, where the mean free path of vapor molecules exceeds the distance between the evaporation surface and the condensation surface. In this regime, the gaseous phase exerts negligible pressure on the substance being evaporated, meaning the rate of evaporation is independent of pressure.
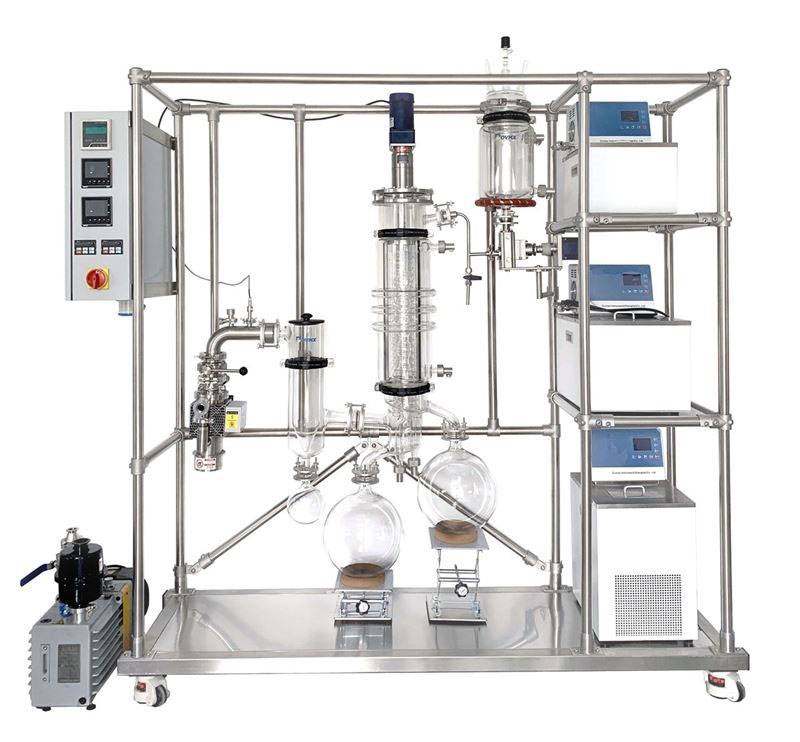
Unlike traditional distillation methods, molecular distillation relies on molecular dynamics rather than fluid dynamics due to the breakdown of continuum assumptions. This process necessitates a short path between the hot and cold surfaces, often achieved by positioning a hot plate, coated with a thin film of the feed, adjacent to a cold plate with a clear line of sight in between. The short path ensures efficient transfer of molecules from the evaporation surface to the condensation surface, enhancing the separation efficiency.
Molecular distillation is particularly valuable for the purification of thermally sensitive and complex molecules, such as vitamins and polyunsaturated fatty acids. Industries that benefit from this technique include those involved in the production of high-purity oils. The process involves brief exposure of the distillate liquid to high temperatures under high vacuum (approximately 10⁻⁴ mmHg) in a distillation column, with a minimal distance of around 2 cm between the evaporator and the condenser. This configuration ensures that the separation is based on the differing evaporation rates of components within the liquid mixture, facilitating effective separation and purification.
Sample Concentration and Purification
Nitrogen Blowing Instrument
Shanghai Bingyue's water bath nitrogen concentrator, an innovative piece of equipment, combines purge and capture technology with precise temperature control. This instrument is designed to facilitate rapid and controlled concentration of sample solutions by utilizing inert gases like nitrogen. The device effectively blows nitrogen gas directly onto the sample surface, ensuring a swift and oxygen-free concentration process.
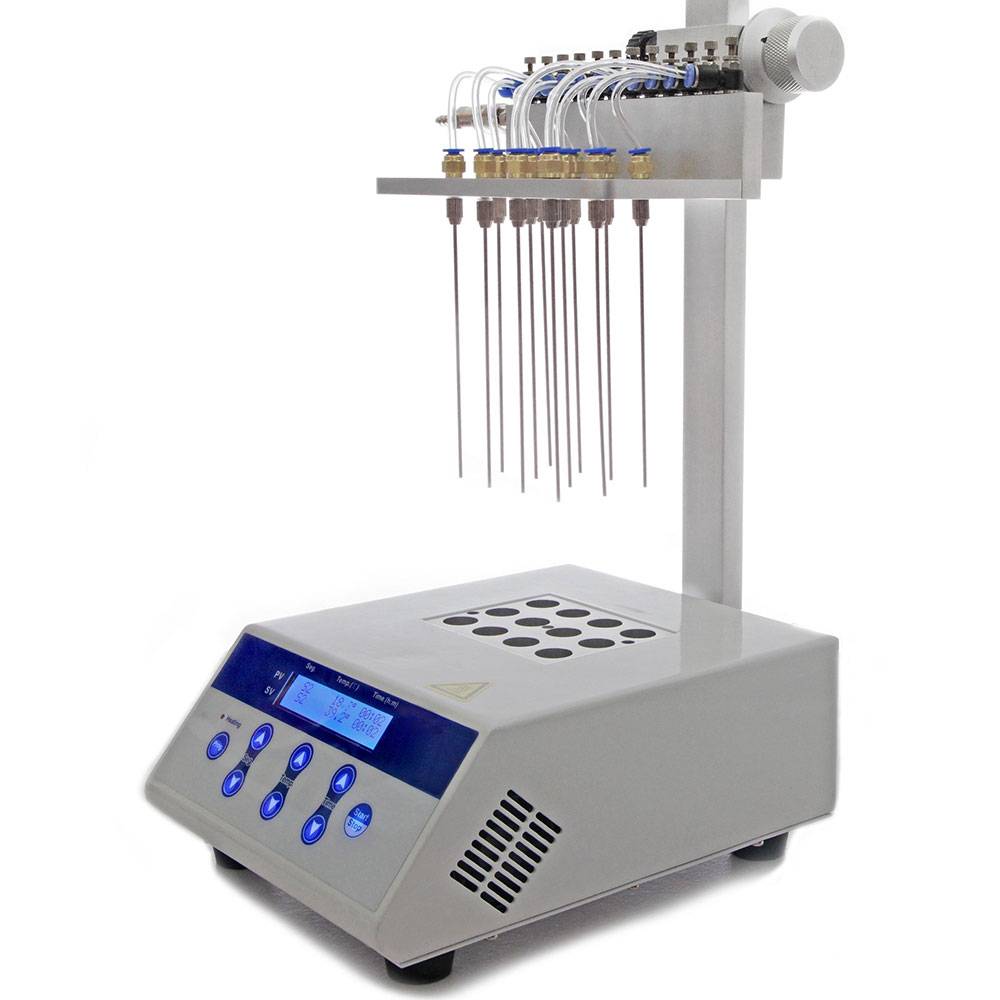
Key features of the nitrogen blowing instrument include:
- Purge and Capture Technology: This technology enables the efficient removal of oxygen from the sample environment, ensuring a controlled and rapid concentration process.
- Temperature Control: The instrument allows for simultaneous heating of the sample, enhancing the efficiency of the concentration process.
- Inert Gas Application: By using nitrogen, an inert gas, the instrument minimizes the risk of sample contamination and oxidation.
This equipment is particularly valuable in laboratory settings where rapid and precise sample concentration is essential, offering a reliable solution for achieving high-quality analytical results.
Vacuum Centrifugal Concentrator
The Carbon Ring Intelligent Manufacturing Integrated Intelligent Vacuum Centrifuge Concentrator is a sophisticated piece of equipment that leverages advanced technology to enhance its operational efficiency and intelligence. One of its key features is the integration of an intelligent chip, which significantly improves the sensitivity and control capabilities of the device. This intelligent chip allows for more precise and adaptive control, making the concentrator a highly reliable tool in various laboratory settings.
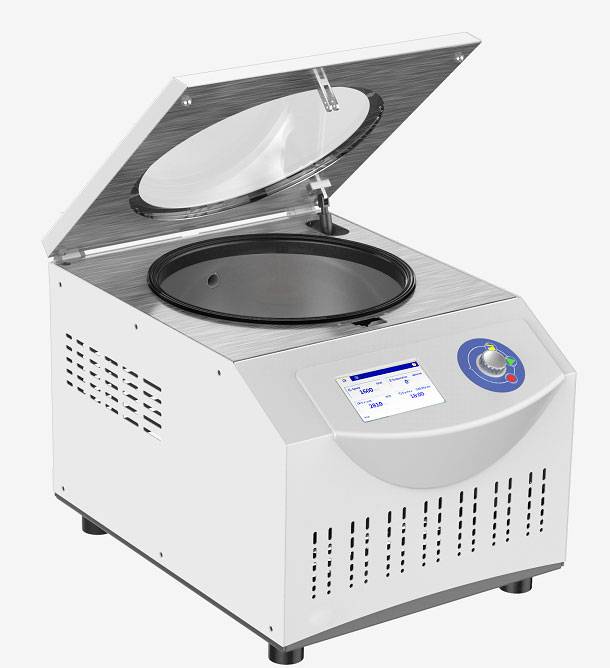
In addition to its intelligent control system, the vacuum centrifugal concentrator employs a maintenance-free centrifugal structure that utilizes magnetic transmission torque. This design not only ensures durability but also simplifies the operational process, as it eliminates the need for frequent maintenance. The microprocessor-based control system further enhances the device's functionality, enabling fully automatic operation that reduces the need for manual intervention.
To achieve effective sample concentration, the vacuum centrifugal concentrator is often paired with additional components such as a chiller and a vacuum pump. The vacuum pump plays a crucial role by reducing the pressure within the centrifuge chamber, thereby lowering the boiling point of the sample's solvent. This process, known as centrifugal evaporation, involves spinning the centrifuge chamber to create a pressure gradient within the solvent. This gradient allows the samples to evaporate from the top down, preventing common issues like solvent bumping.
As the solvent evaporates, it is directed to a solvent condenser where it is collected, leaving behind the concentrated sample. This method ensures that the concentration process is efficient and controlled, making it an ideal solution for laboratories that require precise and rapid sample preparation.
Gel Purification System
The Gel Purification System operates on the principle of gel permeation chromatography (GPC), a technique that segregates and collects complex samples based on molecular volume. This method is particularly effective in eliminating macromolecular matrices and small molecular interferences present in the sample. By doing so, it significantly enhances the sensitivity and accuracy of subsequent analytical procedures.
Moreover, this system not only refines the sample but also contributes to the longevity of analytical instruments. By reducing the accumulation of contaminants, it minimizes wear and tear, thereby extending the operational lifespan of these critical laboratory tools. This dual benefit underscores the importance of the Gel Purification System in maintaining high-quality analytical outcomes and ensuring the durability of laboratory equipment.
Waste Treatment Systems
Waste Gas Treatment
Waste gas treatment in laboratories is a critical process to ensure environmental safety and compliance with regulatory standards. Several methods are employed to effectively manage and mitigate the impact of hazardous gases.
One common approach is the water film dust removal + activated carbon adsorption method. This technique involves passing the waste gas through a water film to remove particulate matter, followed by adsorption onto activated carbon to capture volatile organic compounds (VOCs) and other harmful gases. The water film acts as a preliminary filter, while the activated carbon provides a high surface area for adsorption, ensuring thorough purification.
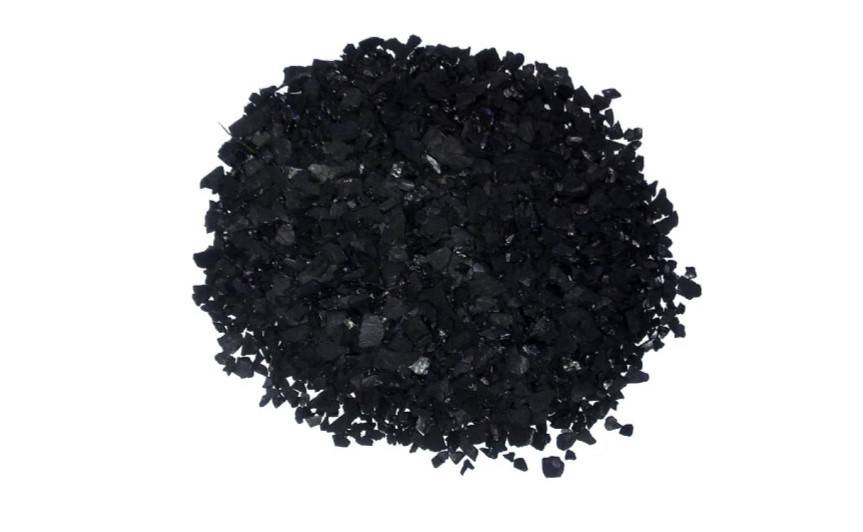
Another method is the dry filtration dust removal + activated carbon adsorption method. In this process, the waste gas is first subjected to dry filtration to remove solid particles. The filtered gas then passes through an activated carbon bed, where it is purified by adsorption. This method is particularly effective for gases with high particulate content and is often used in conjunction with other purification steps.
A more advanced technique is the activated carbon adsorption + catalytic combustion method. Here, the waste gas is initially adsorbed onto activated carbon, similar to the previous methods. However, the adsorbed compounds are then subjected to catalytic combustion, where they are oxidized into less harmful substances such as carbon dioxide and water. This method offers a higher degree of purification and is suitable for treating gases with complex chemical compositions.
Each of these methods has its own advantages and is selected based on the specific characteristics of the waste gas, including its composition, volume, and potential hazards. By employing these techniques, laboratories can effectively manage their waste gas emissions, ensuring a safer working environment and minimizing environmental impact.
Wastewater Treatment
Wastewater treatment is a multifaceted process that requires meticulous consideration and analysis, primarily driven by the variability in water quality and the presence of diverse chemicals. The complexity of this process is further compounded by the environmental implications of the residues and chemicals that are often generated post-filtration.
One of the primary challenges in wastewater treatment is the heterogeneity of the contaminants. Water sources can vary significantly in their composition, influenced by industrial discharges, agricultural runoff, and domestic waste. This variability necessitates a flexible treatment approach that can adapt to different chemical compositions and concentrations. For instance, industrial effluents may contain heavy metals, organic solvents, and other hazardous substances, each requiring specialized treatment methods.
Moreover, the by-products of wastewater treatment can themselves pose environmental risks. Advanced treatment processes, such as chemical precipitation or membrane filtration, often yield residues that are rich in concentrated contaminants. These residues must be managed carefully to prevent secondary pollution. For example, the sludge produced from biological treatment processes can contain pathogens and heavy metals, necessitating further treatment or secure disposal methods.
In summary, wastewater treatment is not merely about purifying water but also about managing the entire lifecycle of contaminants, from their initial removal to the safe disposal of treatment residues. This holistic approach ensures that the environmental impact is minimized, and public health is protected.
CONTACT US FOR A FREE CONSULTATION
KINTEK LAB SOLUTION's products and services have been recognized by customers around the world. Our staff will be happy to assist with any inquiry you might have. Contact us for a free consultation and talk to a product specialist to find the most suitable solution for your application needs!