Yes, aluminium can be deposited through sputtering. Sputtering is a physical vapor deposition (PVD) technique that involves ejecting atoms from a solid target material (in this case, aluminium) onto a substrate. This process is widely used for depositing thin films of various materials, including metals like aluminium, due to its ability to produce high-quality, uniform, and adherent coatings. Sputtering is particularly advantageous for materials with high melting points, and it allows for precise control over the deposition process, making it suitable for applications requiring thin, durable, and well-adhered aluminium films.
Key Points Explained:
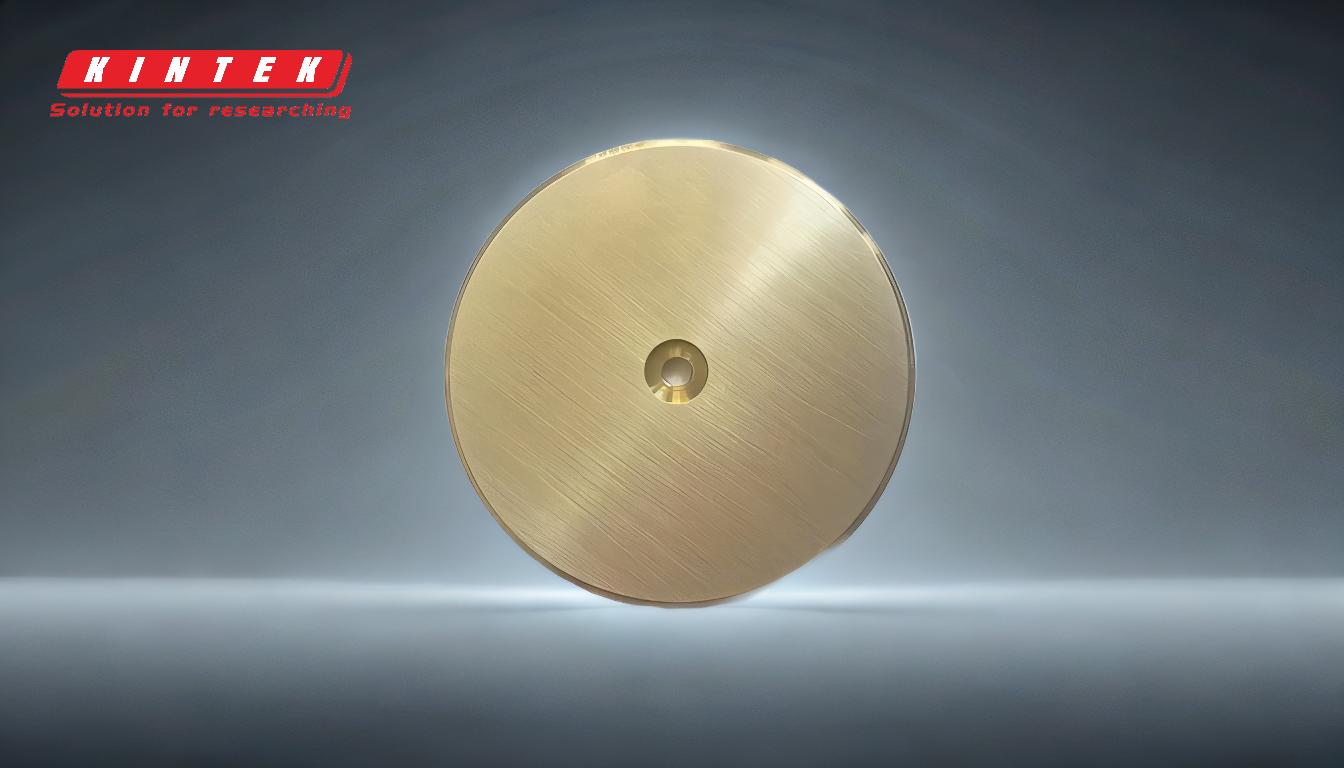
-
Sputtering Process Overview:
- Sputtering is a PVD technique where a target material (aluminium) is bombarded with high-energy ions, causing atoms to be ejected and deposited onto a substrate.
- This process is driven by the generation of plasma between the target and the substrate, which differentiates it from other PVD methods like thermal evaporation.
-
Advantages of Sputtering for Aluminium Deposition:
- High Melting Point Compatibility: Sputtering can deposit materials with very high melting points, such as aluminium, which are difficult to evaporate using thermal methods.
- Better Adhesion: Sputter-ejected atoms have higher kinetic energy compared to evaporated materials, resulting in stronger adhesion to the substrate.
- Uniform and Dense Films: Sputtering produces more uniform films with higher packing densities, even at lower temperatures.
- Precision and Control: The process allows for atomic-level precision, making it ideal for applications requiring thin, consistent coatings.
-
Comparison with Other Deposition Methods:
- Versatility: Sputtering works well with a broader range of materials, including alloys and mixtures, compared to methods like thermal evaporation.
- Environmental and Maintenance Benefits: Sputtering is maintenance-free, compatible with reactive gases, and can be performed in ultrahigh vacuum conditions, making it more environmentally friendly than chemical processes like electroplating.
-
Applications of Aluminium Sputtering:
- Optical and Electronic Coatings: Aluminium films deposited via sputtering are used in optical coatings, semiconductor devices, and reflective surfaces.
- Durable and Hard Coatings: The process produces harder and more durable coatings compared to traditional methods like electroplating.
- Advanced Processes: Sputtering supports advanced techniques like epitaxial growth, enabling the creation of high-performance materials for specialized applications.
-
Process Automation and Reproducibility:
- Sputtering is easier to automate and control compared to methods like electron beam evaporation, ensuring consistent and reproducible results.
- This makes it suitable for industrial-scale production where uniformity and reliability are critical.
In summary, sputtering is a highly effective method for depositing aluminium thin films, offering superior adhesion, uniformity, and durability compared to other techniques. Its compatibility with high-melting-point materials, precision control, and environmental advantages make it a preferred choice for a wide range of applications in optics, electronics, and materials science.
Summary Table:
Key Aspect | Details |
---|---|
Process | Physical vapor deposition (PVD) technique using high-energy ions. |
Advantages | High melting point compatibility, better adhesion, uniform films, precision. |
Applications | Optical coatings, semiconductor devices, durable hard coatings. |
Environmental Benefits | Maintenance-free, eco-friendly, and compatible with reactive gases. |
Automation | Easy to automate for consistent, reproducible results. |
Ready to enhance your thin film deposition process? Contact our experts today to learn more about sputtering solutions!