SLS (Selective Laser Sintering) powder can indeed be reused, but its reusability depends on several factors, including the type of material, the degradation of the powder during the sintering process, and the specific requirements of the application. Typically, SLS powder is mixed with fresh powder in a controlled ratio to maintain the quality of the printed parts. However, repeated reuse can lead to changes in the powder's properties, such as particle size distribution and flowability, which may affect the final product's quality. Proper sieving and blending of used powder with new powder are essential to ensure consistent performance.
Key Points Explained:
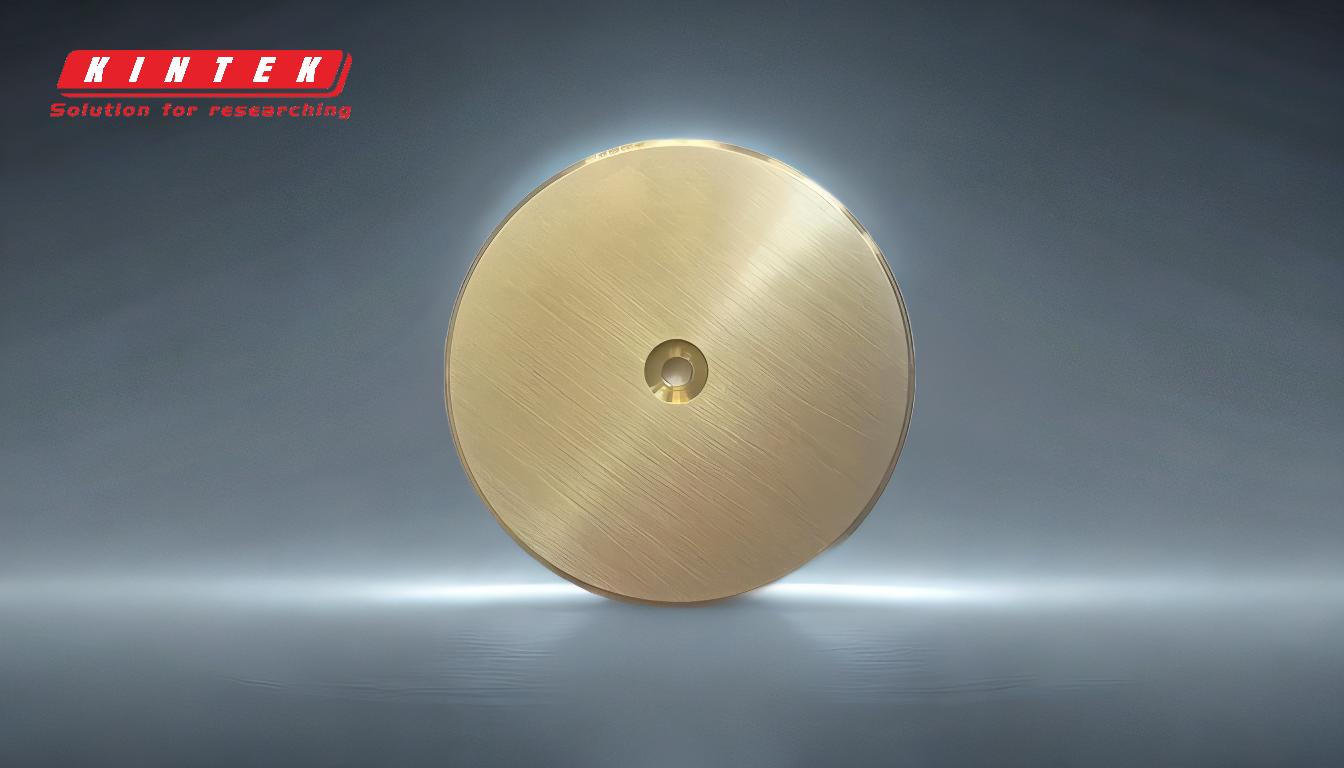
-
Reusability of SLS Powder:
- SLS powder can be reused multiple times, but its reusability is not infinite. The powder undergoes thermal and mechanical stress during the sintering process, which can alter its properties over time.
- The reusability of the powder depends on the material. For example, nylon-based powders (like PA12) are commonly reused, while other materials may have more limited reusability.
-
Degradation of Powder Properties:
- Particle Size Distribution: Repeated sintering can cause the powder particles to fuse or agglomerate, leading to changes in particle size distribution. This can affect the flowability and packing density of the powder.
- Flowability: As the powder is reused, its flowability may decrease, which can impact the uniformity of the powder bed and the quality of the printed parts.
- Thermal Degradation: The powder is exposed to high temperatures during the sintering process, which can cause thermal degradation, especially in polymers. This degradation can lead to changes in the mechanical properties of the final parts.
-
Mixing Used Powder with Fresh Powder:
- To mitigate the effects of powder degradation, used powder is typically mixed with fresh powder in a controlled ratio. This helps maintain the overall quality of the powder and ensures consistent performance.
- The ratio of used to fresh powder can vary depending on the material and the specific application. For example, a common practice is to mix 50% used powder with 50% fresh powder.
-
Sieving and Blending:
- Before reuse, the used powder is often sieved to remove any agglomerated particles or contaminants. This helps restore the powder's flowability and ensures a consistent particle size distribution.
- Blending the sieved powder with fresh powder is essential to achieve a homogeneous mixture, which is critical for producing high-quality parts.
-
Impact on Final Product Quality:
- The reuse of SLS powder can affect the mechanical properties, surface finish, and dimensional accuracy of the printed parts. For applications requiring high precision or specific mechanical properties, it may be necessary to limit the number of times the powder is reused.
- Regular testing of the powder's properties and the quality of the printed parts is essential to ensure that the reused powder meets the required standards.
-
Environmental and Economic Considerations:
- Reusing SLS powder can significantly reduce material waste and lower the overall cost of the printing process. This is particularly important in industries where material costs are high.
- However, the balance between cost savings and maintaining part quality must be carefully managed. Over-reusing powder can lead to increased scrap rates and reduced part performance, which may offset the initial cost savings.
In summary, while SLS powder can be reused, its reusability is influenced by material properties, degradation during the sintering process, and the specific requirements of the application. Proper sieving, blending, and monitoring of powder properties are essential to ensure that reused powder maintains the quality and performance needed for high-quality 3D printed parts.
Summary Table:
Key Factor | Details |
---|---|
Reusability | SLS powder can be reused multiple times, but not infinitely. |
Material Dependency | Nylon-based powders (e.g., PA12) are commonly reused; others may vary. |
Degradation Effects | Particle size, flowability, and thermal properties degrade over time. |
Mixing Ratio | Typically, 50% used powder mixed with 50% fresh powder for consistency. |
Sieving & Blending | Essential to remove agglomerates and ensure uniform particle distribution. |
Impact on Part Quality | Reused powder can affect mechanical properties, surface finish, and accuracy. |
Environmental Benefits | Reduces material waste and lowers printing costs. |
Optimize your 3D printing process with expert guidance—contact us today to learn more!