Choosing the right agitator for a reactor involves understanding the specific requirements of the process, such as the type of reaction, operating conditions, and material compatibility. Key factors include the reactor's size, operating pressure, temperature range, and the nature of the materials being processed. The agitator must ensure efficient mixing, heat transfer, and uniformity while being compatible with the reactor's design and materials. Below is a detailed breakdown of the key considerations when selecting an agitator for a reactor.
Key Points Explained:
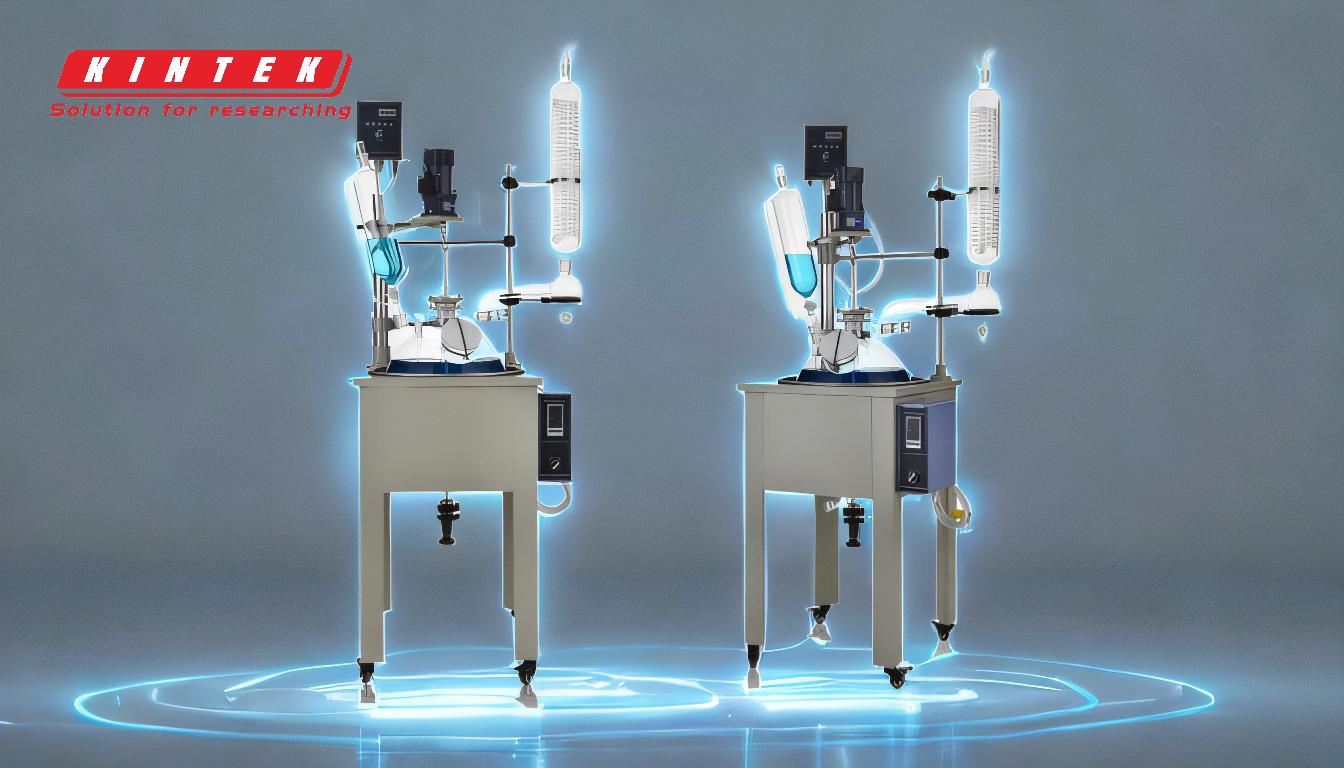
-
Understand the Process Requirements:
- Type of Reaction: The nature of the reaction (e.g., polymerization, hydrocracking, or simple mixing) determines the type of agitator needed. For example, high-shear agitators are suitable for emulsification, while gentle mixing may suffice for simple blending.
- Flow Rate and Mixing Intensity: The required flow rate and mixing intensity influence the agitator's design. High-viscosity fluids may require specialized agitators like helical or anchor types, while low-viscosity fluids can use propeller or turbine agitators.
-
Operating Conditions:
- Temperature and Pressure: The agitator must withstand the reactor's operating temperature and pressure. For high-temperature processes, materials like stainless steel or specialized alloys are preferred. High-pressure reactors may require robust seals and thicker agitator shafts.
- Corrosion Resistance: The agitator material must be compatible with the reactants. For corrosive chemicals, materials like titanium, nickel, or glass-lined steel are ideal.
-
Reactor Size and Volume:
- Vessel Capacity: The agitator's size and power should match the reactor's volume. Larger reactors require more powerful agitators to ensure uniform mixing.
- Agitator-to-Vessel Ratio: The agitator's diameter relative to the reactor's diameter (D/T ratio) is critical for effective mixing. A higher D/T ratio is suitable for high-viscosity fluids, while a lower ratio works for low-viscosity fluids.
-
Agitator Design and Type:
- Propeller Agitators: Ideal for low-viscosity fluids and applications requiring axial flow.
- Turbine Agitators: Suitable for medium-viscosity fluids and applications requiring radial flow.
- Anchor and Helical Agitators: Best for high-viscosity fluids, ensuring thorough mixing and heat transfer.
- High-Shear Agitators: Used for emulsification, dispersion, and particle size reduction.
-
Mixing Efficiency and Heat Transfer:
- Uniformity: The agitator must ensure even distribution of reactants and heat to prevent hot spots or incomplete reactions.
- Heat Transfer: For exothermic or endothermic reactions, the agitator should facilitate efficient heat transfer. Jacketed reactors with appropriate agitators are often used for precise temperature control.
-
Safety and Compliance:
- Sealing Mechanisms: Ensure the agitator has proper sealing to prevent leaks, especially in high-pressure or hazardous environments.
- Explosion-Proof Design: For reactions involving volatile substances, explosion-proof agitators with ATEX certification may be required.
-
Data Collection and Automation:
- Monitoring Systems: Modern agitators often come with sensors for real-time monitoring of parameters like torque, speed, and temperature.
- Automation: Automated agitators with programmable controls can enhance process consistency and reduce manual intervention.
-
Cost and Maintenance:
- Initial Investment: Balance the cost of the agitator with its performance and durability. High-quality agitators may have a higher upfront cost but lower long-term maintenance expenses.
- Ease of Maintenance: Choose agitators with accessible components and minimal downtime for maintenance.
-
Consultation with Experts:
- Manufacturer Input: Consult with reactor and agitator manufacturers to ensure compatibility and optimal performance.
- Custom Solutions: For specialized processes, custom-designed agitators may be necessary.
By carefully evaluating these factors, you can select an agitator that ensures efficient, safe, and reliable operation of your reactor, tailored to your specific process requirements.
Summary Table:
Key Factor | Considerations |
---|---|
Process Requirements | Type of reaction, flow rate, mixing intensity, and viscosity of materials. |
Operating Conditions | Temperature, pressure, and corrosion resistance of agitator materials. |
Reactor Size and Volume | Vessel capacity and agitator-to-vessel ratio for effective mixing. |
Agitator Design and Type | Propeller, turbine, anchor, helical, or high-shear agitators based on application. |
Mixing Efficiency | Uniformity and heat transfer for consistent reactions. |
Safety and Compliance | Sealing mechanisms and explosion-proof designs for hazardous environments. |
Data Collection | Sensors and automation for real-time monitoring and control. |
Cost and Maintenance | Initial investment, durability, and ease of maintenance. |
Expert Consultation | Manufacturer input and custom solutions for specialized processes. |
Ready to optimize your reactor's performance? Contact our experts today for tailored agitator solutions!