Sputtering targets are essential components in the thin-film deposition process, used in industries such as semiconductors, optics, and solar cells. The manufacturing of sputtering targets involves advanced techniques to ensure high purity, fine grain structure, and precise dimensions. The process depends on the material properties and intended application, with methods like hot-pressing, cold-pressing, sintering, and vacuum melting being commonly employed. Silicon sputtering targets, for example, can be produced using electroplating, sputtering, or vapor deposition. The final product is a solid slab of pure metals, alloys, or compounds, designed to emit atoms when bombarded by argon ions in a vacuum chamber, forming a thin film on a substrate.
Key Points Explained:
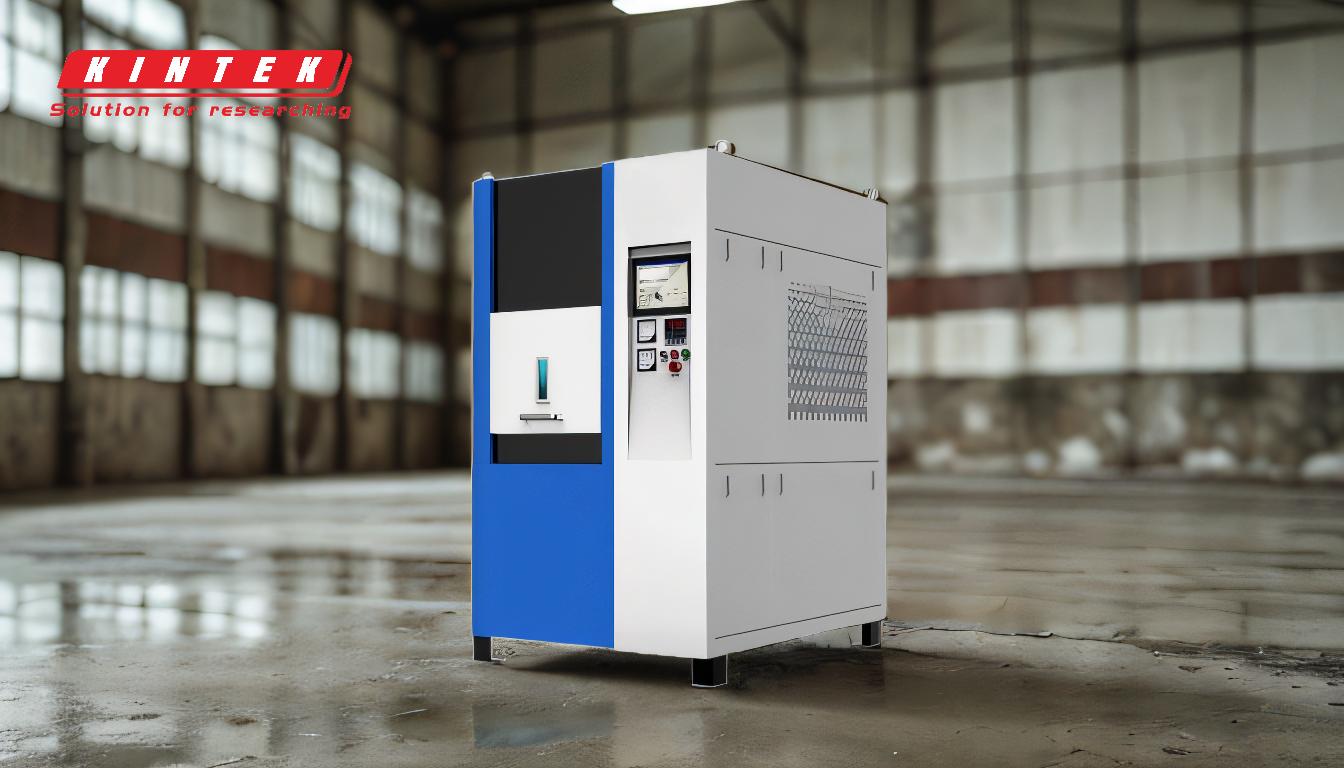
-
Understanding Sputtering Targets:
- Sputtering targets are solid slabs made of materials like pure metals, alloys, or compounds (e.g., oxides, nitrides).
- They are used in thin-film deposition processes, where atoms are ejected from the target material and deposited onto a substrate.
-
Key Manufacturing Processes:
-
Classical and Vacuum Hot-Pressing:
- This method involves heating the material under high pressure to form a dense, uniform structure. It is suitable for materials that require high purity and fine grain size.
-
Cold-Pressing and Sintering:
- The material is pressed into the desired shape at room temperature and then sintered at high temperatures to achieve bonding and densification. This method is cost-effective and suitable for a wide range of materials.
-
Vacuum Melting and Casting:
- The material is melted in a vacuum to prevent contamination and then cast into the desired shape. This process is ideal for materials that require high purity and uniform composition.
-
Classical and Vacuum Hot-Pressing:
-
Material-Specific Manufacturing:
-
Silicon Sputtering Targets:
- Silicon targets can be manufactured using electroplating, sputtering, or vapor deposition. These methods ensure high purity and precise control over the material properties, which are critical for applications in the semiconductor industry.
-
Silicon Sputtering Targets:
-
Importance of Material Properties:
- The choice of manufacturing method depends on the material's properties, such as melting point, density, and grain structure.
- For example, materials with high melting points may require vacuum melting, while materials that are sensitive to contamination may benefit from vacuum hot-pressing.
-
Advanced Manufacturing Techniques:
- Advanced methods are employed to produce sputtering targets with very fine grain structures, which are essential for achieving high-quality thin films.
- These techniques allow for the production of targets in nearly any shape or size, catering to specific application requirements.
-
Role of Sputtering in Thin-Film Deposition:
- In the sputtering process, argon plasma is ignited in a vacuum chamber, and argon ions are accelerated towards the negatively charged target (cathode).
- The high-energy argon ions bombard the target, causing atoms to be ejected and deposited onto a substrate, forming a thin film.
-
Applications of Sputtering Targets:
- Sputtering targets are used in various industries, including:
- Semiconductors: For creating thin films in integrated circuits and microelectronics.
- Optics: For producing reflective and anti-reflective coatings.
- Solar Cells: For depositing thin films in photovoltaic devices.
- Sputtering targets are used in various industries, including:
-
Quality Control and Testing:
- The manufacturing process includes rigorous quality control measures to ensure the sputtering targets meet the required specifications.
- Testing methods may include density measurement, grain size analysis, and purity checks to ensure the targets perform reliably in the sputtering process.
By understanding these key points, a purchaser can make informed decisions about the type of sputtering target needed for their specific application, considering factors like material properties, manufacturing methods, and end-use requirements.
Summary Table:
Aspect | Details |
---|---|
Definition | Solid slabs of pure metals, alloys, or compounds used in thin-film deposition. |
Key Processes | Hot-pressing, cold-pressing, sintering, vacuum melting, electroplating. |
Material-Specific | Silicon targets: electroplating, sputtering, vapor deposition. |
Applications | Semiconductors, optics, solar cells. |
Quality Control | Density measurement, grain size analysis, purity checks. |
Discover the right sputtering target for your needs—contact our experts today!