Reactors in the pharmaceutical industry are specialized vessels designed to facilitate chemical reactions and bioprocesses under controlled conditions. They are essential for the production of active pharmaceutical ingredients (APIs), biopharmaceuticals, and other complex molecules. Glass reactors are commonly used for drug synthesis, providing a controlled environment to optimize reaction conditions, yields, and product purity. High-pressure reactors, on the other hand, are employed to accelerate multi-step reactions, enabling precise kinetic control and reducing drug development timelines. Reactors are versatile, with applications ranging from cell culture and fermentation to distillation, crystallization, and extraction. Their design and material composition vary depending on the specific process requirements, ensuring efficiency, safety, and scalability in pharmaceutical manufacturing.
Key Points Explained:
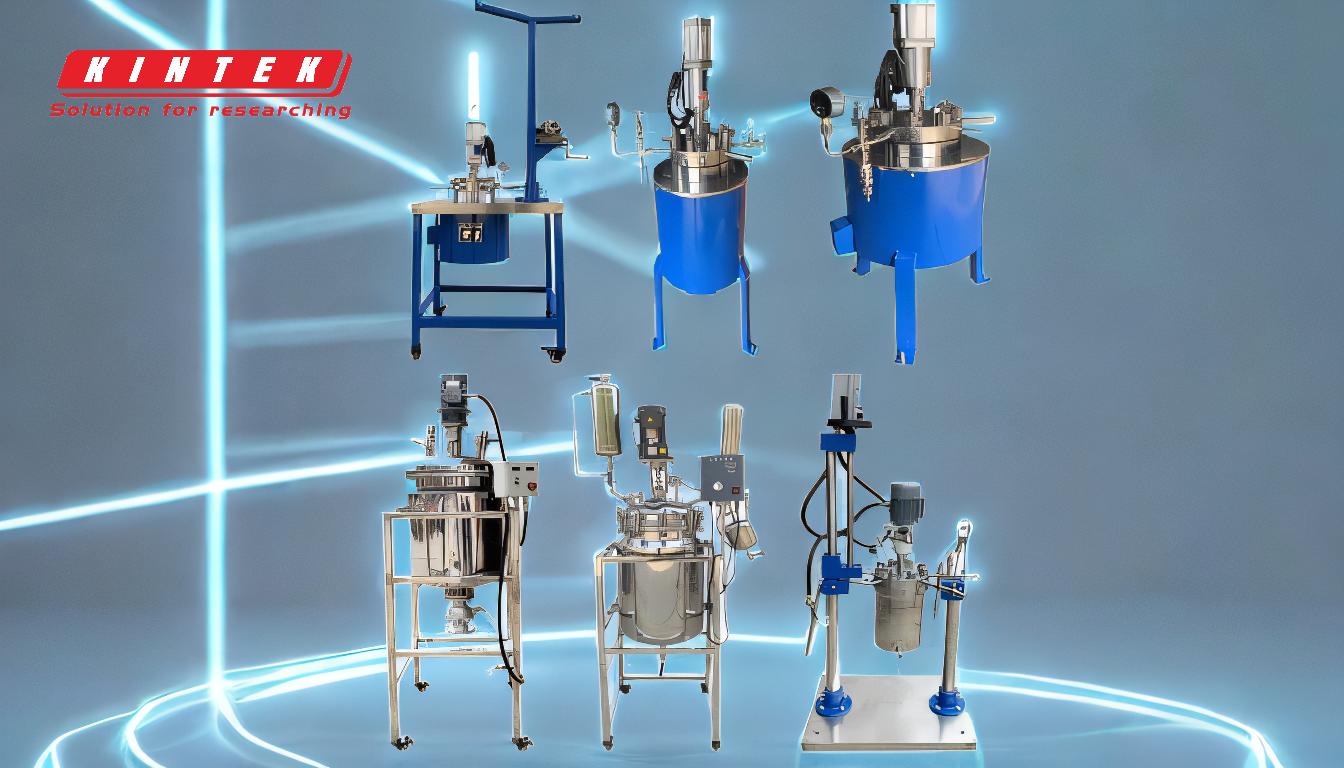
-
Purpose of Reactors in the Pharmaceutical Industry:
- Reactors are critical for facilitating chemical reactions and bioprocesses in a controlled environment.
- They are used in the production of APIs, biopharmaceuticals (e.g., monoclonal antibodies, recombinant proteins, and therapeutic enzymes), and other complex molecules.
- Reactors enable optimization of reaction conditions, yields, and product purity, ensuring high-quality pharmaceutical products.
-
Types of Reactors:
-
Glass Reactors:
- Commonly used for drug synthesis and biopharmaceutical production.
- Provide a transparent, corrosion-resistant environment for monitoring reactions.
- Ideal for processes requiring precise control over temperature, pressure, and mixing.
-
High-Pressure Reactors:
- Used to accelerate multi-step reactions, reducing drug development timelines.
- Enable precise kinetic control, which is essential for complex molecule synthesis.
- Suitable for processes requiring elevated pressure and temperature conditions.
-
Glass Reactors:
-
Applications of Reactors:
-
Drug Synthesis:
- Reactors are used to produce APIs, ensuring consistent quality and scalability.
-
Bioprocessing:
- Used for cell culture, fermentation, and downstream processing in biopharmaceutical production.
-
Other Processes:
- Reactors are also employed in distillation, crystallization, extraction, and reprocessing.
-
Drug Synthesis:
-
Design and Material Considerations:
- Reactors are designed to meet specific process requirements, including temperature, pressure, and chemical compatibility.
- Materials such as glass, stainless steel, and specialized alloys are chosen based on the chemical properties of the reactants and products.
- Configurations vary, including batch, continuous, and semi-batch reactors, to suit different production needs.
-
Advantages of Using Reactors:
-
Controlled Environment:
- Reactors provide precise control over reaction parameters, ensuring optimal conditions for chemical and biological processes.
-
Scalability:
- Reactors can be scaled up from laboratory to industrial production, maintaining consistency and efficiency.
-
Safety:
- Designed to handle hazardous reactions safely, minimizing risks to operators and the environment.
-
Efficiency:
- High-pressure reactors, in particular, reduce reaction times, accelerating drug development and manufacturing.
-
Controlled Environment:
-
Role in Pharmaceutical Manufacturing:
- Reactors are indispensable in modern pharmaceutical manufacturing, enabling the production of high-quality drugs and biologics.
- They support innovation by allowing researchers to explore new reaction pathways and optimize existing processes.
- Their versatility makes them suitable for a wide range of applications, from small-scale R&D to large-scale production.
By understanding the functionality, types, and applications of reactors, pharmaceutical manufacturers can select the appropriate reactor design and configuration to meet their specific needs, ensuring efficient and safe production of pharmaceuticals.
Summary Table:
Aspect | Details |
---|---|
Purpose | Facilitate chemical reactions and bioprocesses for API and biopharmaceutical production. |
Types | Glass reactors (drug synthesis) and high-pressure reactors (accelerated reactions). |
Applications | Drug synthesis, bioprocessing (cell culture, fermentation), distillation, crystallization, extraction. |
Design Considerations | Materials (glass, stainless steel, alloys), configurations (batch, continuous, semi-batch). |
Advantages | Controlled environment, scalability, safety, and efficiency in drug development. |
Role in Manufacturing | Enable high-quality drug production, support innovation, and ensure process optimization. |
Ready to optimize your pharmaceutical production with the right reactor? Contact us today to learn more!